Tech Update: Deconstructing Crankshaft Balancing
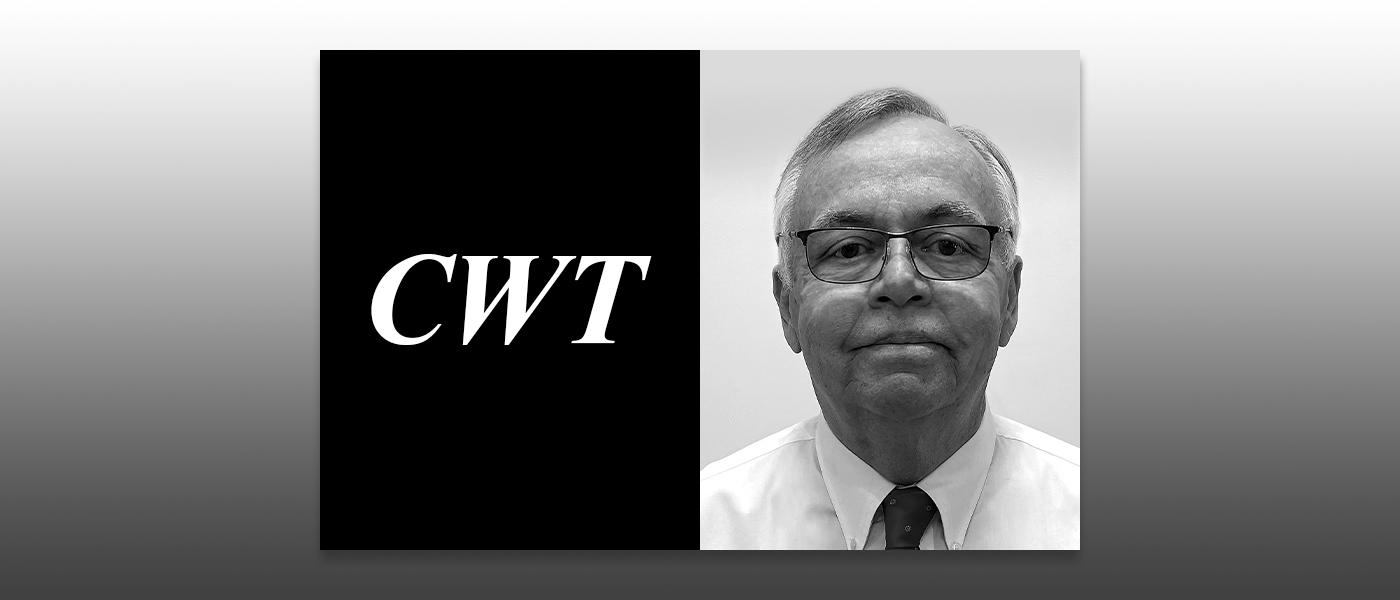
How this critical, but often-misunderstood process helps eliminate the harmful forces that can prevent your engine from freely transmitting the power it creates.
The practice of balancing rotating assemblies is one of the most misunderstood dynamics within the engine building community. Just look at social media forums, which are filled with misguided or “voodoo” information on the subject.
So let’s start at the top: The main reason for balancing rotating assemblies is to eliminate damaging and parasitic forces that cause erratic mechanical activity that in turn robs the engine of its ability to freely transmit its generated power. Most people overlook the fact that all engines from the first stage of manufacturing go through some process of balancing. When the crankshaft and all related components are manufactured, they must be shaped and weighed to meet a target weight specification.
As such, the crankshaft is designed with counterweights that offset the reciprocating and rotating forces generated via the combustion cycling, which causes the assembly to rotate. While this is generally known and understood, what we need to make clear is that the engines we used just a few decades ago were running at a relatively low rpm band as compared to the engines we’re currently getting from the OEMs. Notice that I am talking here about “grocery getter” vehicles, not high-performance machines.
Now, let me provide some information that hopefully will get your attention: In the 1990s, OEMs such as GM, Ford, and Chrysler produced engines that would generally accept a balancing tolerance of 2.0 ounce-inch. So what does that mean? Essentially, the 2.0 ounce-inch tolerance means that a typical crankshaft that has a total diameter of 6.0 inches will have 18.95 grams of unbalance weight residually embedded at the outer edge of the counterweights. When the engine is running at 1,000 rpm (just above idle), the embedded weight will cause the rotating crank assembly to generate a “centripetal unbalance force” of 3.56 pounds. As we increase the rpm to 2,000, the unbalance force increases to 14.24 pounds; at 4,000 rpm, it is now 56.96 pounds; and 8,000 rpm will generate 227.84 pounds of force.
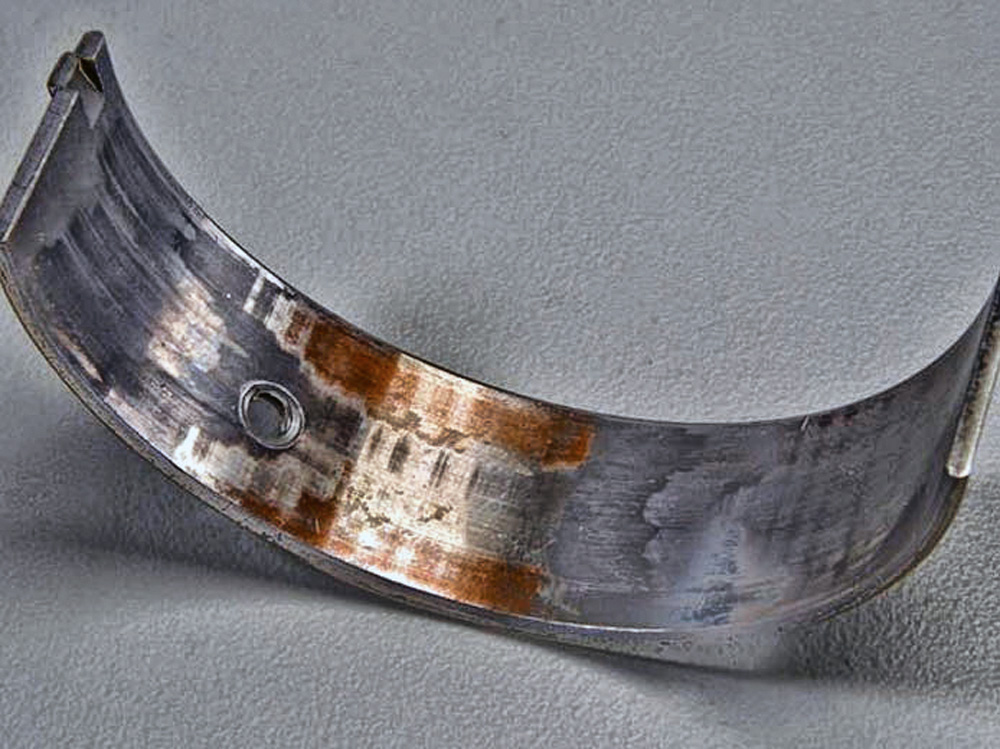
It is important to understand that even though the unbalance force can increase from 3.56 pounds all the way up to 227.84 pounds at 8,000 rpm, the actual embedded weight of 18.95 grams is still the same. Only by increasing the rpm do we increase the generated unbalance force. Simply put, as you increase rpm, the generated centripetal force of the offending unbalance mass is increased exponentially.
At this point you may be saying that because we rarely operate the engine at 4,000 rpm, the 56-plus pounds of force is not a big deal. Well, let me point out that if you had a 56-pound hammer and you dropped it on, say, the hood of your car, you would notice an unwelcome dent. Now let’s imagine that the hood of your car is an engine bearing. This bearing is receiving a pounding load of that 56.96-pound hammer at a rate of over 66 times per second at 4,000 rpm; and at 8,000 rpm, this hammer now weighs 227.84 pounds and is cycling at 133-plus times per second.
It is critical to understand that the damage created at the higher rpm is not recoverable by simply reducing rpm.
For the grocery-getter, you’re probably more interested in fuel efficiency. But for the high-performance engines you should be more concerned with the durability and stability of your engine components. And, you must acknowledge that parasitic drag is stealing horsepower.
Something I’m often asked is whether balancing makes horsepower. The answer is no, at least not in direct form. It does, however, eliminate parasitic forces, which unleashes horsepower. These disrupting (parasitic) forces also can generate erratic mechanical disruptions, resulting in what we call “excitation” to engine components. As we know, vibration is directly linked to premature wear of the engine bearing, along with block and head machined mating surfaces—especially main bearing caps and block registers. It’s also linked to natural frequency excitation “triggering” that results in potentially disruptive harmonics associated with all moving and non-moving components (where you will witness fretting on mating surfaces).
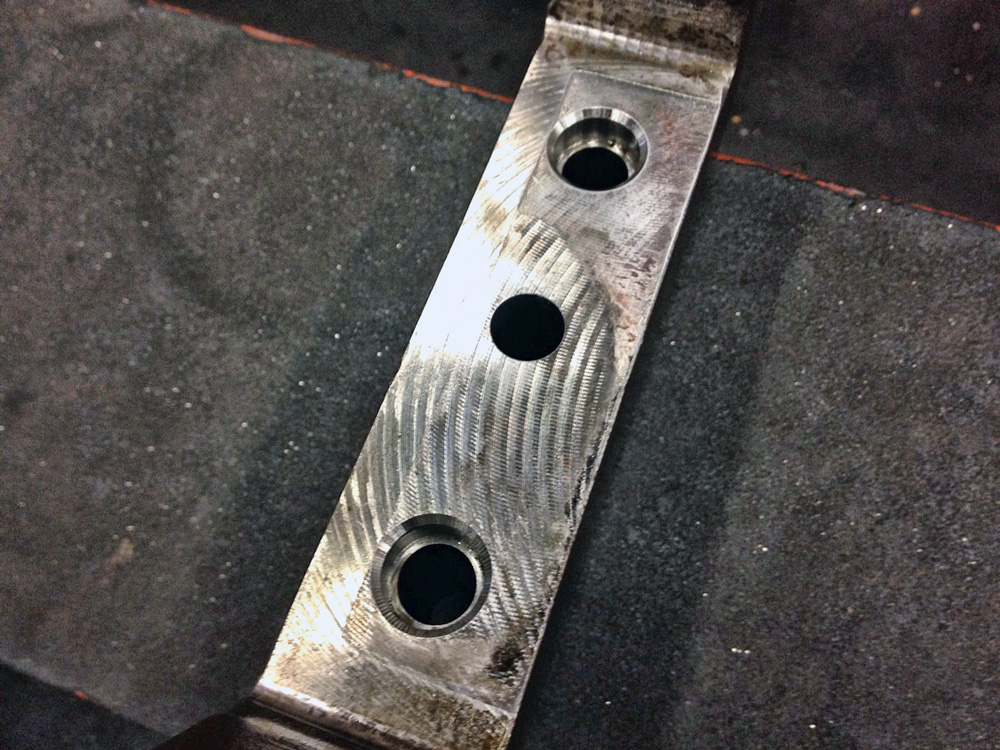
Here’s a quick example of how drivetrain components are linked and work in harmony: While driving down a smooth highway, you accidentally veer off the edge of the smooth asphalt surface. You instantly feel the shuddering of your steering wheel. The tire is bouncing, but again, you feel the disruption in your steering wheel. Now, in order for you to feel the disruption, you must understand that the initial catalyst of that disruption came via numerous interconnected components, all of which were affected before you felt the vibration.
Referring back to the engine, the out-of-balance forces generated by the unbalanced crank assembly emulates the same “disruptive excitation” induced by the rough surface of the unpaved road. But, by simply driving back onto the smooth asphalt you can eliminate the disruptive force. Unfortunately, that’s not the case with an unbalanced crank assembly. Any unbalance force retained within the crank assembly can only be corrected by disassembly and rebalanced to the correct ISO 21940 Balance Tolerance.
Randy Neal is the owner of CWT Industries in Norcross, Georgia. A 50-year veteran of the auto racing industry, Neal is widely considered a leading authority in the design and manufacture of dynamic balancing machines. Over the years he has developed proprietary software, machinery, and application knowledge that’s helped take the “voodoo” out of the balancing process.