Tech Update: Indivisible: Pumps And Dyno Performance
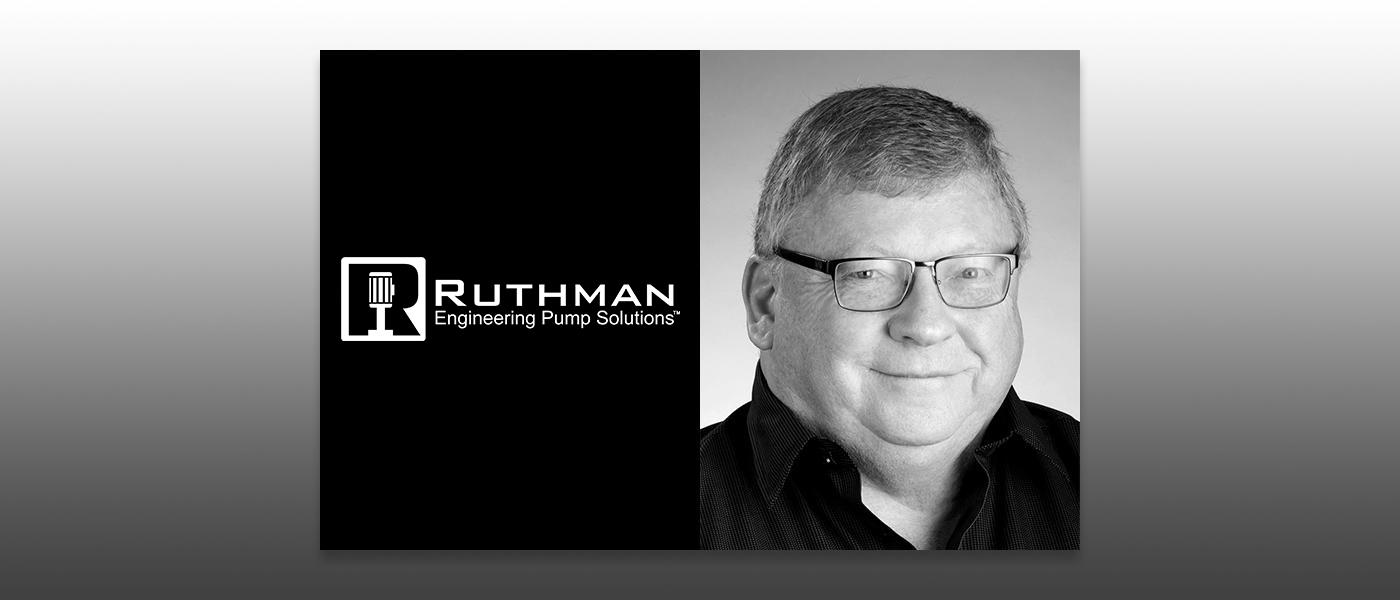
Proper sizing, configuration, and curvature are critical to maximizing the potential and longevity of your water brake engine or chassis dynamometer.
Dynamometer testing provides critical data that allows you to fine-tune your driveline for optimum performance. However, the ability to achieve the highest level of performance from your race vehicle is only as good as the dyno system and its components.
Some of the most important components of a water brake dyno system are its pumps. Properly specifying the right intake and return pumps will allow you to reliably test over a wide horsepower range, with long service life and minimal maintenance downtime.
In a water brake system, water flow, proportional to the load under test, creates the resistance to the engine. The dyno’s intake pump creates a controlled water flow through the inlet manifold, which is then directed to the center of the rotor in each absorption section. This water is then propelled by centrifugal force to the outer dynamometer body, accelerating into pockets on the stationary stator plates, where the water then decelerates.
The power generated by this pattern of acceleration and deceleration is absorbed by the dynamometer to determine engine torque. The water, now heated by this transfer of energy, is then discharged and pumped back into the top of the storage tank, away from the system intake.
Pump Sizing/Selection
Properly sizing the dyno system’s pumps is the first step in ensuring efficient, reliable performance and long service life. Poor pump selection can result in wasted energy on the system, and increased wear and tear on the pump.
A general rule of thumb for sizing the intake pump is that 10 gallons per minute (gpm) of capacity is needed for every 100 horsepower that will be under test. So, if you will routinely be testing 800-hp engines, you will want to specify a pump with a capacity of at least 80 gpm. Operating pressure (expressed as psi) is determined by the dyno system manufacturer and is generally in the 65–70 psi range.
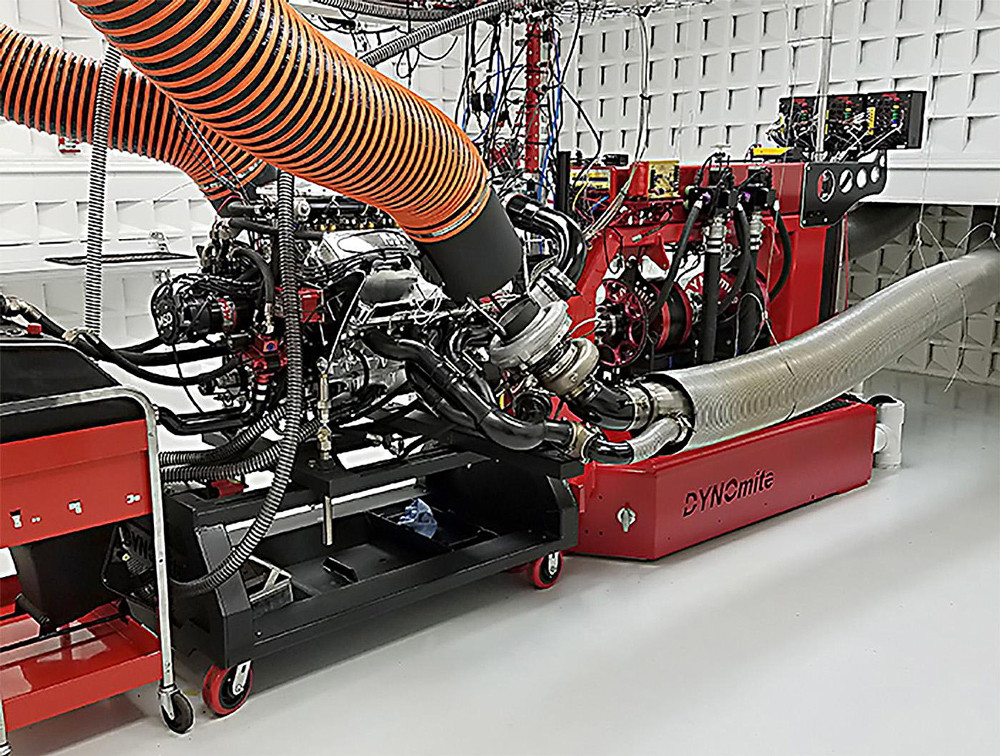
A smaller return pump is needed on the discharge side for pumping water back to the reservoir, as the flow is lower and not holding any back pressure. A below-ground well reservoir will take a smaller pump, letting gravity do the work. A larger pump may be needed on an above-ground tank, working against gravity to return the water to the top of the reservoir.
Additional parameters that factor into pump selection include voltage (single-phase or three-phase), inlet and outlet diameter, pipe size, and reservoir size.
Choose Your Configuration
Once you’ve determined the basic pump performance parameters, the next factor to consider is whether a horizontal or vertical pump will best suit your dyno setup. Horizontal pumps are the most prevalent and are best suited to installations where overall equipment footprint is not an issue. Systems with an above-ground reservoir typically use a horizontal pump.
In higher horsepower dynos, or shops where floor space is at a premium, vertical pumps can bring higher capacity with a more compact size. Vertical pumps are well suited to below-ground reservoirs, where the pump can be dropped into the tank at ground level. Vertical pumps also have the added advantage of seal-less pump design—an option that eliminates the risk of leaks and reduces overall maintenance.
Consider The Curvature
Now that you know the size and type of pump you want, you will want to consider the performance curves of your pump options. The performance curve indicates how a pump will perform with regard to pressure head and flow. In general, you should look for a more rounded pump curve, which is indicative of a pump’s ability to maintain the required pressure through variations in the flow rate.
A pump with a rounded curve is more capable of adjusting the pressure to compensate for the load on the system and is more forgiving of variations in performance. A pump with a flatter curve is less forgiving. If flow becomes restricted, the risk of wear and tear to the pump and its components is significantly increased.
Beyond pump performance, features that affect lifetime maintenance should also be considered. For dyno systems using vertical pumps, a seal-less design eliminates the mechanical seal and associated maintenance. Another feature to look for on both horizontal and vertical models is renewable sleeves and bushings. This means that routine replacement of these parts can be done in the shop, rather than sent out, minimizing dyno downtime.
Pumps are at the heart of any water brake engine or chassis dyno. With careful selection, your dyno will run smoothly, allowing you to focus on maximizing your vehicle’s performance.
Gary Smith is Regional Sales Manager for Ruthman Companies. He joined the company’s flagship Gusher Pumps brand 48 years ago, where he took on various roles before spending the next 30-plus years in sales for Gusher. In 2016, he transitioned to a wider role with Ruthman Companies, representing its full range of pumps and valves. Smith has worked with countless manufacturers and race shops to spec and install pumps for both engine and chassis dyno applications.