Conversion Factor
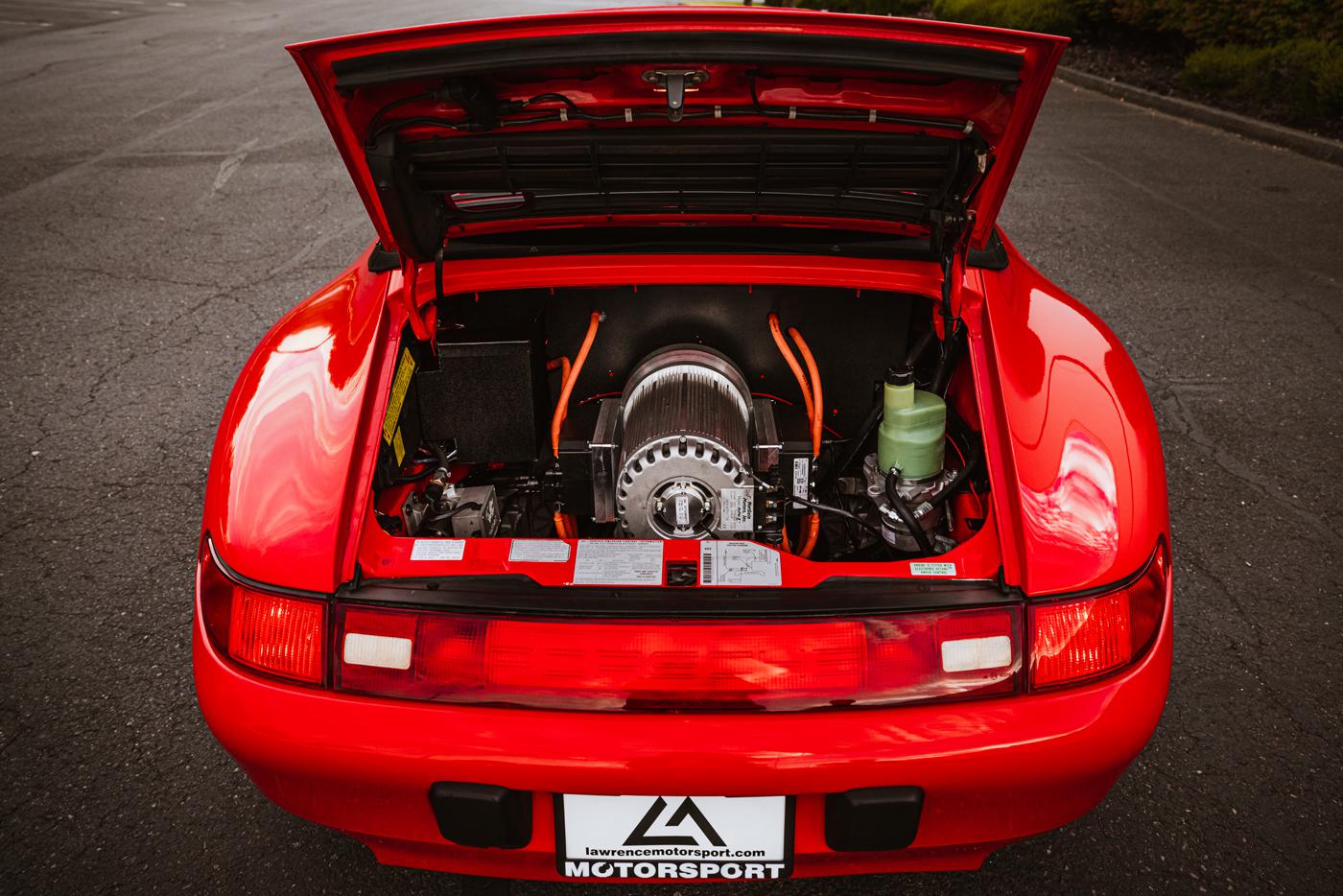
As electrification sees greater adoption on the street and on the race track, interest in ICE to EV changeovers continues to grow. Although the technology still has its limitations, the advantages it offers in certain racing disciplines are undeniable, and it’s only going to get better from here.
With automakers continuing to pour billions of dollars into the development and manufacture of electric vehicle platforms, public interest in EV technology continues to grow in turn. The tech’s increased visibility has also brought increasing awareness to EV conversions, a fledgling industry that has greatly benefited from those OEM-backed development efforts. Once a niche populated by a small group of tech-savvy DIY hot rodders, EV conversions are becoming more sophisticated and capable by the day, and they’re convincing an increasing number of competitors to ditch ICE powertrains in their mothballed race cars for electric motivation.
As EVs become a greater presence in brand portfolios and top-tier models continue to tout increasingly impressive performance figures, the inherent benefits of the technology are becoming more widely understood as well. Yet EVs remain a topic of heated debate in the realm of motorsport. While it’ll likely be some time before we see a grid powered solely by electricity at the 24 Hours of Le Mans, it’s important to note that there are formats where the tech is ready for prime time right now. Perhaps even more important, there’s plenty of evidence that indicates that the early adopters of today could become the front-runners of tomorrow.
“We can’t put our head in the sand and just ignore this,” explained Lawson Mollica of AEM EV, Hawthorne, California. “The public certainly isn’t—the Ford F-150 Lightning and Hummer EV are sold out for their introductory years, and dozens of new electrified models with performance intent are coming over the next few years. I think we kind of have to look at this like the early LS swap market. It really wasn’t that easy to do early on, and you had to solve a lot of problems along the way. But over time, the market matured and the problems were solved. That’s how we see the progression of this segment going as well.”
Although the majority of the focus in the ICE to EV conversion market is currently aimed at street applications, more and more teams are starting to take notice of what the tech is capable of.
“I think you have to approach this from the requirements of the discipline,” said Michael Bream of EV West, San Marcos, California. “There are situations where an electric isn’t going to stand up against its gasoline counterpart right now. But you also have to consider the fact that the record at Pikes Peak is currently held by an electric vehicle.”
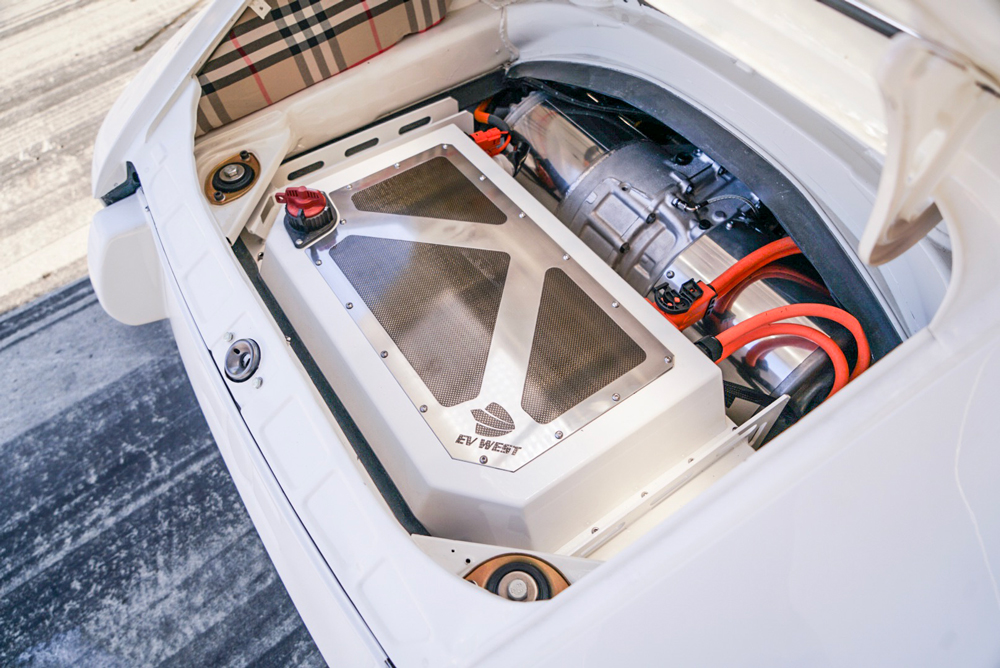
Targeted Advantages
While the earliest EV conversions were about technical curiosity and experimentation more than anything else, Mavrick Knoles of Legacy EV in Tempe, Arizona, told us that performance is the biggest driver in today’s market.
“We’ve heard countless stories about people being hesitant about the technology and then going for their first spin in a Tesla in Ludicrous Mode. I think that EVs feel like the future for many folks, and they want to embrace the next wave of technology. We’ve spent so much time perfecting the gas engine, and now we’re kind of starting fresh with EVs. A lot of people are saying to themselves, ‘Okay, now how can I further optimize the performance of this?’ That’s where people start to get really excited.”
The current limitations of the technology may keep battery-powered vehicles out of endurance racing and other motorsports disciplines that require long periods of sustained output for the foreseeable future, but EVs can shine in other competitive disciplines right now. “You don’t need a massive battery and tons of cooling to do formats like drag racing and autocross,” said Adam Roe of Zero Labs, Gardena, California. “There are EVs out there with 14 kWh batteries and a thousand horsepower. There’s a lot of things that you get from an EV powertrain that you can’t replicate with a gas vehicle, and the main one is efficiency. You have 85% or more of the energy in an electric vehicle being converted to usable power, whereas you might see 15% with an internal combustion engine. Although gasoline has great energy density, a lot of it is lost to noise and heat.”
Bream also cited another potential advantage of EVs that may not be obvious at first glance. “A race, for all intents and purposes, is a moving auto show. If you want people to look at your car and the sponsors that are on it, electric is currently the best choice for that,” he explained. “I think what’s driving this current trend of ICE to EV conversions is an overall excitement around electrification. So if you’re trying to get a million views on your video, there’s so much interest in electric that you’re going to have a better chance of getting that kind of attention with an EV build.”
Getting Race-Ready
Today’s street-car EV conversions often showcase the ‘wow factor’ of instant torque delivery and scratch the itch of general curiosity about the technology. That allows those conversions to focus on drivability and achieving an agreeable combination of range, performance, and cost. But as in the ICE world, EVs built for racing tend to balance priorities differently.
“Torque management is key,” said Mollica. “Electric motors provide prodigious amounts of torque. And while that sounds really cool from a performance standpoint, it doesn’t equate to fast on the track if you can’t make it stick. That’s where we really focus our efforts—the software that allows you to manage that.”
AEM EV’s VCUs, or vehicle control units, essentially serve as a bridge between the EVs’ various powertrain systems. Integrating everything together into one interface makes tuning much more straightforward than it has been in the past. “You have a lot of different systems that aren’t really talking to each other, and that’s where the VCU is a game-changer,” Mollica said. “For instance, our battery management system monitors the batteries and does all of the features that a battery management system should do, but it’s programmed through our VCUs. The same goes for our power distribution units. So not only is the VCU controlling what’s going out based on the data it’s bringing in, but it’s also seeing everything that’s coming across the bus. It can do passive balancing, it can tell you if you have a bad cell, it can tell you what your temperatures are, and on and on. So if you give it the beans, the VCU can, for instance, take that information and determine if it needs to de-rate the power output to prevent you from damaging something.”
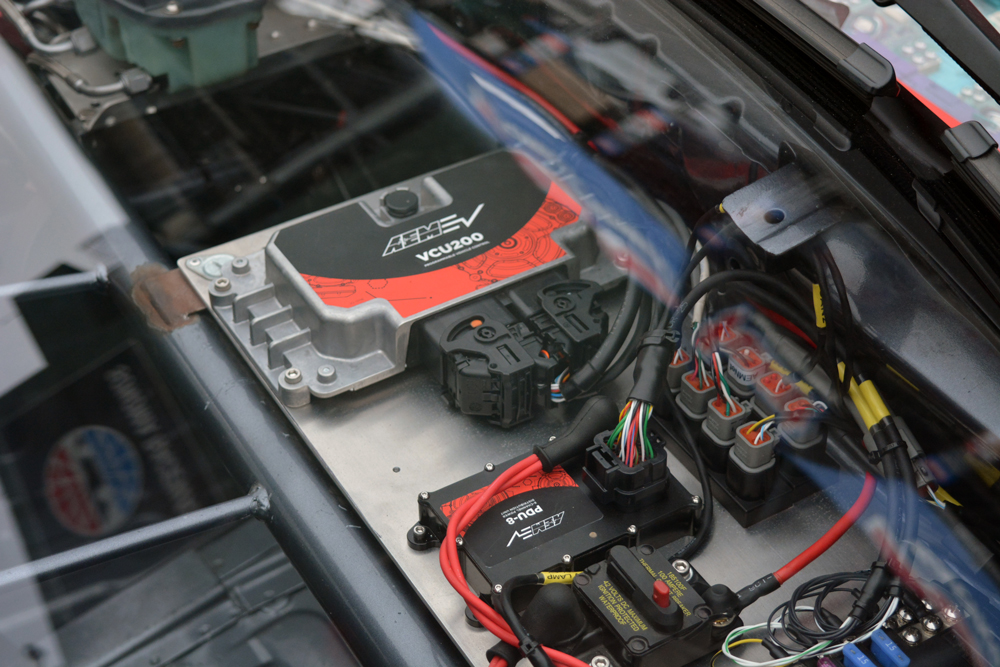
As with internal combustion powertrains, excess heat is the enemy of EV performance, and managing it still remains a challenge today. “The problem isn’t the size of the radiator, or the water pump, or the fan,” said Bream. “We know how to dissipate heat. The problem is that the current drive components that people are using weren’t engineered to wick the heat out of them at those higher power levels. You could have the best cooling device in the world on a Tesla motor, but if you run that motor hard for about two to three minutes, you’re going to start going into thermal cutback. The internal water passages and the surface area aren’t big enough to dissipate heat like that.”
Bream noted that with his team’s Bonneville EV land speed car, they pre-chill the motor with ice for 20 minutes before every run to maximize its potential. For racing that requires sustained power output for long amounts of time, he suggests that over-engineering the powertrain and dialing it back is likely the best solution for the time being.
“Inherently, I think the engineering has to take an approach that maximizes getting heat out of the internals in these components, and racing just isn’t a big enough niche yet,” he explained. “The systems that are doing these high continuous loads are commercial systems that you’d find in things like electric buses. So they exist, but you’re not going to use a bus motor in a race car because it weighs a thousand pounds or something like that. If you wanted to build an EV race car for a road racing application right now, the recipe is to get an extremely lightweight car that’s very aerodynamic, put in an electric motor that’s rated for, say, four times as much power as you need, and dial the output back electronically so it doesn’t have to work as hard. That’s the only way to do this type of performance continuously right now.”
Meanwhile, others continue to look for ways to adapt more traditional cooling systems to these powertrains to help mitigate heat issues. Roe noted that while the batteries are the main concern, there are other components that need to be taken into account as well. “Thermal management needs to be focused on your inverter and the motor, too. We use two radiators on our vehicles, and we have two connected systems for cooling so those systems can focus on different jobs. I’ve seen layouts where people have the batteries, the motors, and the inverter all on the same circuit, and the problem with that is that your cooling reservoir will just cook because in that setup you are going from hot, to hotter, to hottest. In order to maximize efficiency you need as short of a run as possible and cycle it as much as possible. And it’s a good idea to have a backup pump in the system—pumping capability is not something you want to suddenly be without,” he said.
Knoles also pointed out that the cooling requirements of powertrain components can differ. “You need to know what the operating specs are for the battery you’re using,” he said. “It’s something that tends to get overlooked in the industry, and some chemistries are much stouter than others. Some batteries run at peak efficiency at 120 degrees Fahrenheit, so the cooling system might not have to work as hard as you’re expecting to keep those batteries where they want to be. Meanwhile, with the inverter you’re converting DC current to AC current, so the more power you’re sending to the motor, the hotter that inverter is going to get. Those differing system demands typically need to be regulated independently.”
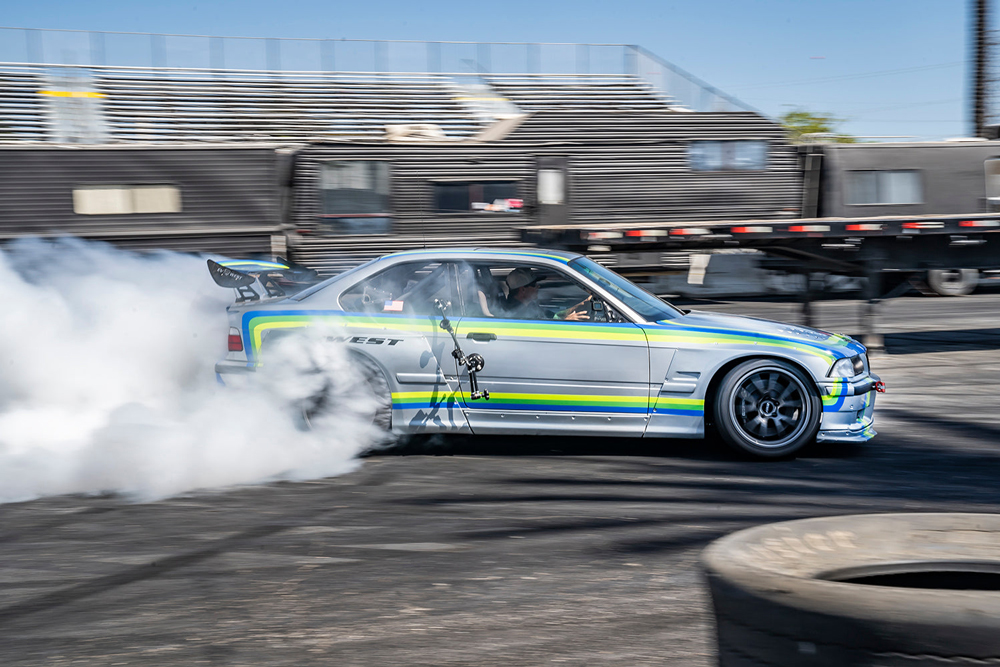
The specifics of EV race car safety components are usually going to be dictated by the rule set of the sanctioning body a racer is competing with, but expect a kill switch to be part of the mix regardless. “You basically need isolation management; your high-voltage battery needs to remain isolated from the metal in your 12-volt chassis system,” said Bream. “You see this in Formula 1 and Formula E—you have a component that looks for voltage isolation within the chassis, and that system will give you a visual cue, like a bright green or bright red light, which indicates whether or not the high-voltage system is still properly isolated after an incident. In terms of controlling that kind of thing, it’s a hundred times easier to turn off electricity than it is to shut down a fuel line or to stop a liquid that’s not containable. An inertia switch can turn off a fuel pump, but you still have all the fuel in the lines that can drain out. An EV’s version of that inertia switch is called a contactor, and it’s an electromechanical device, so it literally operates at the speed of light.”
Cost Benefits
EV conversions can cost anywhere from about $40,000 in parts and labor for a basic powertrain swap to well into six-figure territory for a bespoke solution that’s designed for hardcore competition. While that’s a sizable chunk of change to initially drop, there are cost benefits to be had once the job is completed.
“There’s a bigger up-front investment with EV development, but as with an electric vehicle on the street, the operating costs go way down,” said Mollica. “You don’t have multiple fluids to change, multiple gear sets to service, and all of these different types of things that can break. It’s also easier on the braking system. As long as you’re not destroying components, the biggest concern is the batteries at that point. If you maintain them properly, they’re going to last quite a while.”
Looking into the future, Bream posits that the racers who choose to adopt this technology while it’s still in its infancy will likely have an advantage in the long term. “You have to be cognizant of current events,” he said. “The winds are starting to shift, and a lot of businesses that are interested in sponsorships are becoming more aware of the footprint. I don’t think it’s a stretch to say that some of these large companies that are throwing around sizable amounts of money want to align themselves with future technologies, cleaner technologies. Because they’re the ones that are going to survive.”
SOURCES
AEM EV
aemev.com
EV West
evwest.com
Legacy EV
legacyev.com
Zero Labs
zerolabs.com