A New Twist In Crankshaft Development
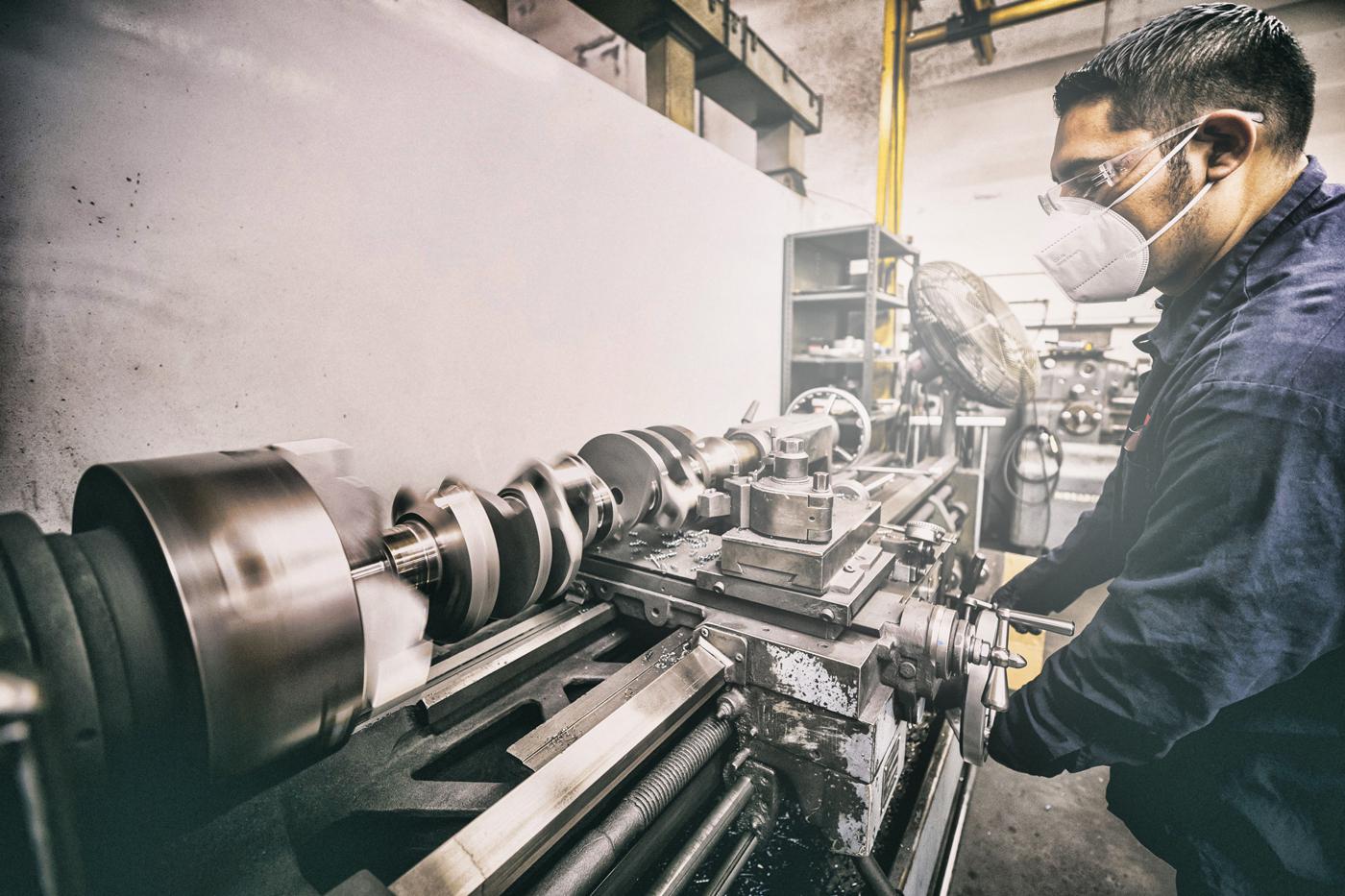
Innovative designs and new applications are keeping manufacturers busy as engine builders and outrageous boost levels demand more of the product.
Crankshaft design is becoming more inclusive.
“Everybody wants something a little different,” observed Nick Boes of Shaftech, Fostoria, Ohio. “Got a customer with a drag boat. It has a big block Ford crank with Hemi rod journals and a Chevrolet snout. We’re getting more and more cranks like that where it’s a conglomeration of a little bit of everything. Everybody wants their own little spin to make it a unique piece. But we can’t stock stuff like that because we’d never get rid of the next one.”
Boes doesn’t manufacture crankshafts, but rather he repairs, modifies and applies finishes, so he sees the wide variety of crankshafts now peppering the market, especially because those selective racers may not be able to get a duplicate crankshaft for some time.
“They’re all moving to one-off parts. When a guy hurts something like that and wants to order a crank now, they may say 16 weeks, but he’d be lucky if that’s when he actually got it,” said Boes.
Like most other sectors in the racing industry, crankshaft manufacturers stayed busy during the pandemic and often struggled with the same problematic issues of labor and parts shortages.
“Just getting trucks,” added Matt Polena of K1 Technologies, Mentor, Ohio. “There’s a lack of shipping trucks to get stuff from Point A to B.”
“I was talking to a customer who had 32 motors on the floor and couldn’t get enough parts to finish even one of them,” agreed John Partridge of Bullet Cams, Olive Branch, Mississippi.
Hottest Trends
Despite some setbacks, new products are rolling out of the shops as more applications become popular or the crank manufacturers expand their catalogs.
“Howards did release both LS and big block Chevy billet cranks in our Reaper Series just before the pandemic shut everything down,” noted Kirk Peters of Howards Cams, Oshkosh, Wisconsin. “We feel those two consumer markets had and currently have the biggest potential for market growth. Also, LS is the wave of the future and Howards plans on meeting those challenges with a better engineered product, such as machine center counterweight clearances so our cranks can be used in both stock and aftermarket blocks. The addition of center counterweights on both the LS and BBC cranks has increased the longevity of larger stroke crankshafts.”
Center-counterweight or eight-counterweight crankshafts are certainly one of the hottest topics in the industry right now.
One of the hottest trends this year is the eight-counterweight or center-counterweight design.
“We’re coming out with a new eight-counterweight billet LS crankshaft,” said Tom Molnar of Molnar Technologies, Kentwood, Michigan.
“We are offering more center-counterweighted crankshafts than ever before. The first to roll out are Chevy big block with LS following,” echoed Alan Davis of Eagle Specialty Products, Southaven, Mississippi. Conventional design cranks will also be on the forefront of company efforts, he said. “We are putting a lot of effort into developing a specific crankshaft for use in the RaceSaver sprint car series. We want to offer more than just a modified version of an off-the-shelf crankshaft. We want to not only reduce costs, but also improve performance and durability while staying within the RaceSaver rules.”
Debate over choosing between a six- or eight-counterweight V8 crankshaft seems to focus on weight versus unwanted vibration.
“Center counterweights are implemented to reduce crankshaft flexing at extreme power and rpm levels,” explained Davis. “This will also increase durability and fatigue strength. Racers are making more power than ever.”
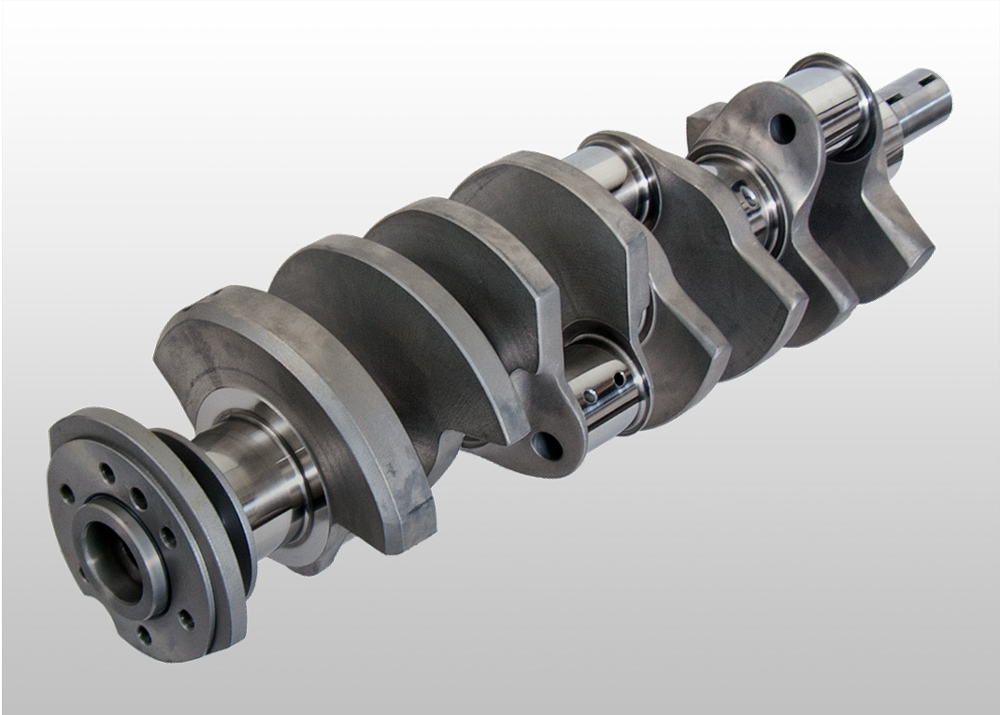
“A lot of people do not like the extra weight,” countered Molnar, noting there are specific markets that truly need full counterweight designs. “The longer the stroke, the more there is a need for eight counterweights. Shorter strokes do not need them as badly.”
Molnar pointed out that “counterweights will not necessarily improve performance but will improve longevity. You have forces pulling on all the rod pins. You need a counterweight opposite of those forces to reduce the bending. This is not about balancing, it is about reducing bending.”
Engineers at Lunati in Olive Branch, Mississippi, agree with the benefits of the eight-counterweight design but have plans for an added twist. “The demand for an eight-counterweight is coming from hardcore racers,” said Will Vance. “It’s the same scenario we went through with the big block Chevy. Everyone figured out six counterweights were fine in a street application, but if you’re making any real power you can get too much crank whip. Now we’re seeing 450-cubic-inch LS engines turning over 7,500 rpm. Crank whip can be an issue with them.”
To help separate its crankshaft from the competition, Lunati plans to leverage its proprietary Black Magic finishing technology currently used on the company’s premium line of LS camshafts. The in-house coating adds hardness and smooths out the surface while leaving a unique black chrome appearance on the metal.
“The coating really improves the RA factor,” added Vance. “It fills in any imperfections left after machining. We’re looking at doing the same finish with crankshafts. It won’t make any more power, but it can improve longevity on the bearing ride area. If we can get this eight-counterweight crank going, it will probably be introduced with a play on the Black Magic brand.”
Another hot market for manufacturers is big diesel engines used for tractor pulling. Callies, which is based in Fostoria, Ohio, has released a billet crank designed for the International DT466 engine after a couple local racers brought in an aftermarket crank for a checkup. Engineers made a few design changes to strengthen Callies’ billet offering and are now talking with the racers to see if additional stroke is desired. This project opens up additional possibilities in a market in which the crankshafts can weigh up to 250 pounds.
“John Deere is probably one that we’ll do very soon,” revealed Brook Piper. “We’re going to go after the big cranks in the tractor market.”
On a more conventional note, Callies is developing a billet crank specifically for a billet block machined by Bullet Race Engineering in Australia that’s patterned after the Nissan RB30 platform.
“They’re targeting the Toyota 2JZ market down there,” added Piper.
Dirt late models running 4.500-inch-bore-center cylinder blocks make up another hot segment within the crank industry.
“We’re making a lot of crankshafts for those,” explained Peter Harris of Crower Cams, San Diego, California. “Those late models are very hard on parts. The harmonics going on in those engines can be really bad. We’ve had to make the cranks stronger.”
On the OEM side, new fuel economy and emissions standards are driving the development at Tier 1 supplier Pankl, which is based in Austria but also has operations in the US.
“Our customers have started to work on higher efficiency combustion engines, such as VCR [variable compression ratio] and opposed-piston concepts, which require a special crankshaft design,” said Christoph Wachmann.
New Directions
Much of the crankshaft industry has settled into a comfortable pace. Each manufacturer has its favorite steel, and while there may be different schools of thought on heat-treating, cranks are more durable than ever. Engine builders often have standard orders and don’t deviate from their favorite weights or journal sizes. They’ve experimented in the past but now know what works. and they’re happy with the results.
That doesn’t mean that risks can’t be taken. One of the livelier directions in the market is the flat-plane crankshaft. Other than Formula 1, flat-plane crankshafts have been tested but not well accepted into other racing venues. Among the reasons given was that engine builders were tired of chasing dampers around the dyno room because flat-plane cranks can be notorious for vibration issues.
Despite the challenges, there is still interest. Ford developed a flat-plane crankshaft for its 5.2-liter Voodoo engine found in the Mustang GT350 and GT350R programs.
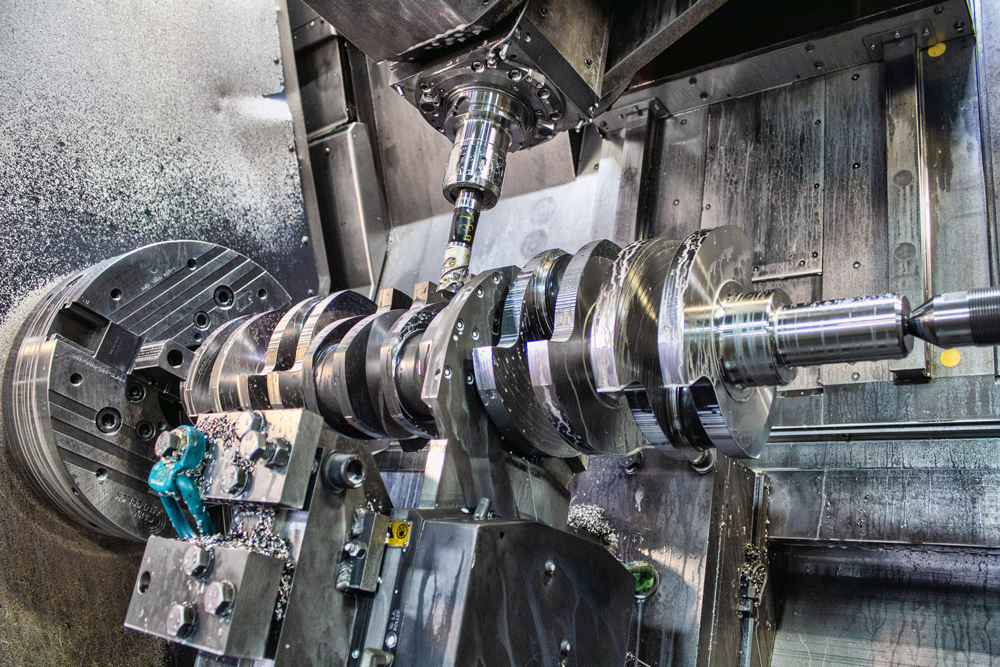
“We are making more billet flat-plane crankshafts,” said Tom Lieb of Scat Crankshafts in Redondo Beach, California. “We’re making them for engines other than the Ford. Engine builders are finally getting onto the fact of what the flat-plane crank is all about. And the flat-plane crank is about using the exhaust system for tuning.”
Lieb said there are misconceptions about equal-length headers when using a conventional 90-degree crankshaft in a V8 engine. But with a 180-degree crank, equal-length headers will take advantage of the exhaust dynamics created as the cylinders fire 180 degree apart.
“You can adjust the length of the header, but to all four at the same time, and now you can use the exhaust to tune the intake,” suggested Lieb, adding that Ford worked out many of the vibration issues by using an up-down-up-down configuration for the rod-pin locations instead of an up-down-down-up configuration often used in other flat-plane applications.
“That changed the balance of the firing order from side to side,” added Lieb. “This way it goes front-to-back, front-to-back to even the load across the crank and cuts the vibration.”
The debate continues, however.
“There are things that happen in a flat-plane crank that cannot be fixed,” warned Molnar. “You cannot fix some of the forces even though the crank is balanced correctly. Those engines shake. They might get some better performance, like in a Formula 1 car. But they basically tell the drivers, ‘If you don’t like the way the steering wheel vibrates, we’ll find somebody else.’”
No doubt that engine builders are demanding more of their crankshafts. Boes said the data acquisition on one of his customer’s tractor-pulling engines revealed the turbo boost peaked at 425 pounds during one pull.
“That’s a staggering number, when you think about it,” he said. “We’ve gotten a lot more requests to repair cranks. I think it’s twofold. Costs keep going up, so repairing becomes more feasible. Also, availability is getting to be a problem.”
“Big turbo, real high-horsepower drag racing applications seem to be the wave of the future,” noted Harris. “Outlaw and no-prep racing. Some of those guys are making two-, three- and four-thousand horsepower. Trying to keep a crankshaft in there while it’s trying to get pushed out the bottom of the block is pretty tough.”
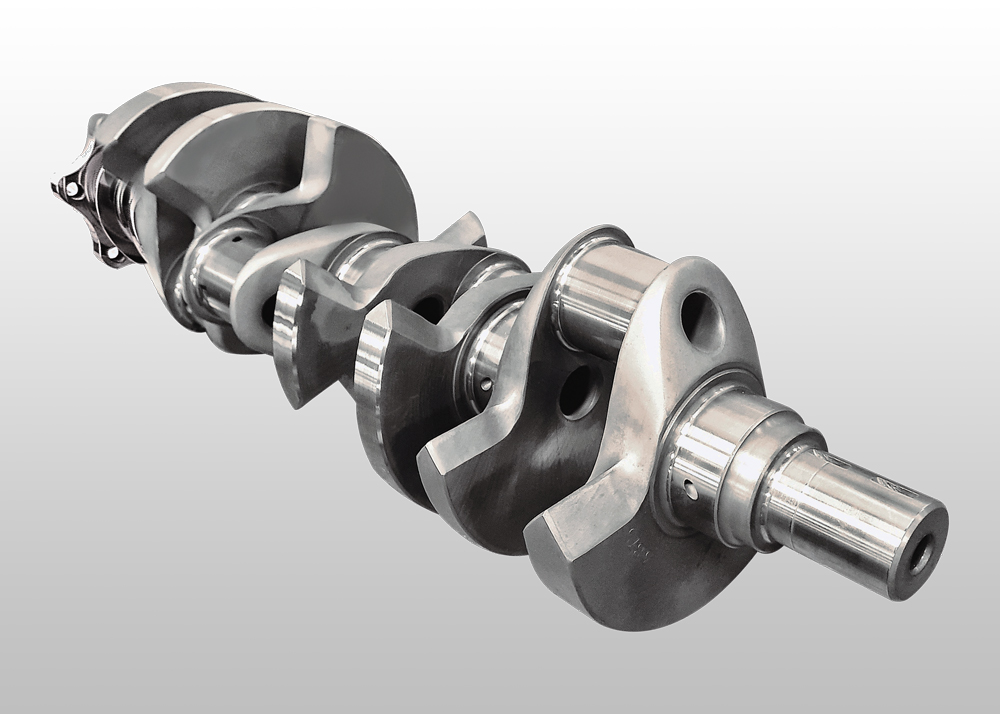
Increasing crankshaft strength often revives the billet versus forging debate.
“There’s a place for both,” said Peters. “If there’s not a forging available, building a crankshaft from a solid round piece of material is the best way. It all comes to building a billet crankshaft when nothing else is available.”
“There really is no debate, only a misinterpretation of design intent and manufacturing viability,” affirmed Davis. “A forged part will be stronger than a billet part if there are no other differences dimensionally, material, or otherwise. I do think it is interesting that the automotive industry is the only industry that seems confused about this. Go anywhere else in any machinery-related industry and it’s not even a topic anyone talks about. Why don’t we have billet hand tools, for instance?
“I think this all started because way back in the day, all anyone ever had were OE parts, and aftermarket forgings were not yet cost-effective,” continued Davis. “Yet, a high-end racing crank would always be a billet one. OE forgings were only slightly better because the materials used were still not very strong compared to chromoly steels. I think the lofty reputation has just persisted through the years.”
What’s Next
Looking ahead, some crank suppliers are updating their manufacturing facilities and others are following advanced technologies, such as 3D printing. Callies and its sister company Energy Manufacturing will be bringing three new WFL multi-operation machines online in the near future.
“We’re working diligently on adding capacity and flexibility through machining technology,” said Piper. “One of the WFLs is a monster. It could also do a 40-inch diameter by 20-foot-long crankshaft. That gives us the capacity for longer applications.”
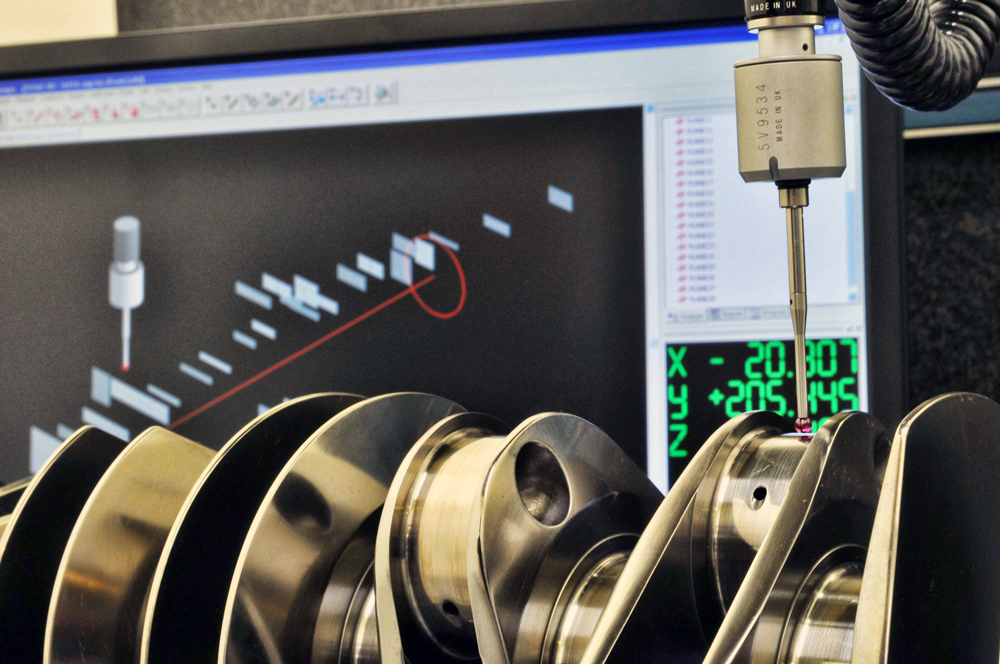
“Additive manufacturing is already possible, but costs are high,” said Wachmann. “The advantages will be lower weight with best stiffness and lubrication systems.”
Market consolidation will be a factor in future development plans. K1 recently released a crankshaft for the Gen III Hemi, and sister company Dart Machinery is developing a Hemi block.
“In conjunction with our other brands we have been working on Gen III Hemi parts to complement the Dart block,” said Polena, noting that matched rotating assemblies with K1 crank and rods and Wiseco pistons are productive for engine builders. “We have a couple of K1 rotating assemblies just for the LS platform, but we’ve been working on other applications, making sure all the fitments are right. It does take a lot of the guesswork out compared to trying to put together the parts individually from different brands.”
Ford’s Godzilla platform is also drawing attention at K1; otherwise, the ongoing directive is quality control.
“We’re looking at keeping tighter tolerances on the crankshaft than what we’re currently using,” added Polena. “We don’t have a crank yet for Godzilla, but we do have rods and have made some custom pistons.”
On the custom side, Bullet continues to modify forgings to make them legal for Super Stock racing. One of the key adjustments is adding .015-inch stroke, which is legal under NHRA rules.
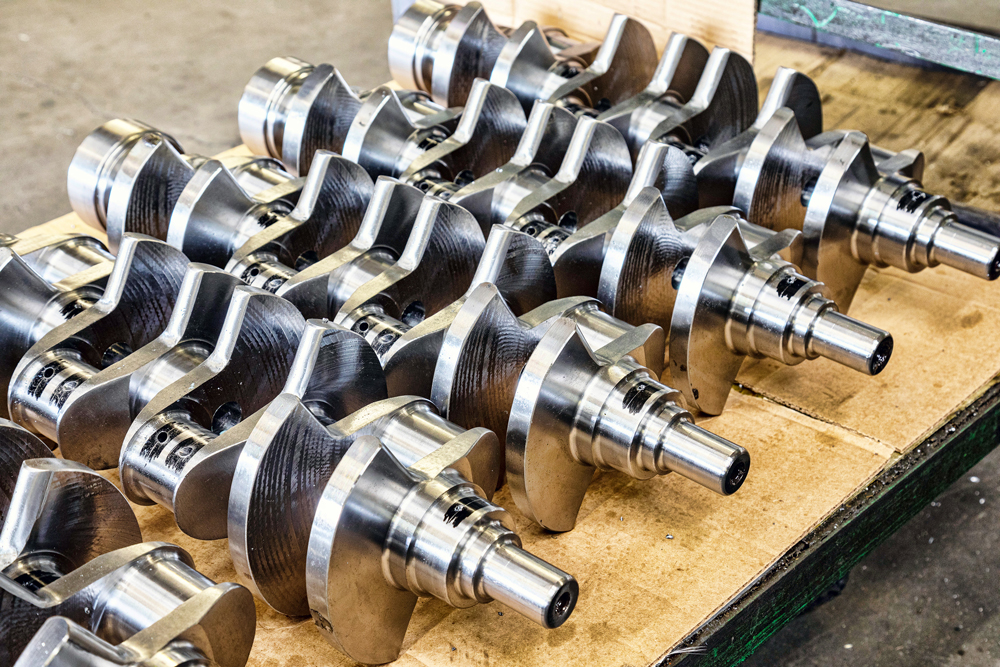
“Normally we put in only .013-inch to give the customer some cushion,” said Partridge. “Then we make them as light as we can within the rules, which means the counterweights cannot be undercut. You can’t knife edge them, either, but we roll the leading edges over. And we can run any bearing diameter. It’s usually a 283 Chevy for the mains and a Honda for the rods, but we can do any size they want. When we get through with them, they usually weigh around 40 to 42 pounds.”
Obtaining raw forgings is the priority at Bullet. The company first tries to find US forgings, then goes to overseas markets.
“We do all the work in-house to make them the way we want, as opposed to buying something already made and trying to reconfigure it,” added Partridge. “It’s a specialty crank, and not that many other people do it. It’s so low volume that most others don’t want to fool with it. For two of my workers, that’s basically all they do.”
Keeping up with demand will be the main priority for crankshaft suppliers, even as the racing season winds down. The winter months are always busy for engine builders, and they are understandably anxious about parts delivery.
“Some customers basically tell me, ‘Just don’t let me run out of crankshafts,’ and I’m trying to get at least 20 in the shop at all times,” noted Harris. “So, it’s good business out there.”
The Damper Question
—
To run a damper or not. Sometimes that is the quiz of the week in racing garages.
Also referred to as a harmonic balancer, dampers are designed to reduce unwanted harmonics created when the crankshaft bends and twists under heavy loads. The automotive performance aftermarket offers four types to racers: viscous, pendulum, friction and elastomer. The manufacturers of each type have their loyal customers, as there are pros and cons to each design that engine builders weigh before selecting one for a particular application.
But there are racing classes where dampers are not used, and that’s not always a good idea.
“We had an import racer who was really having a hard time with crank flex,” recalled JC Beattie Jr. of ATI Performance Products, Baltimore, Maryland, the manufacturer of elastomer-style dampers. “He was not running a damper at the time. When he went on the two-step, the car would not sit still.”
ATI suggested a damper package that worked. “Turns out the crank would flex so much that the back of the crank would bend and engage the clutch a little bit as it flexed, making the car creep forward,” explained Beattie.
The damper industry seems to always be educating the customer on their product’s benefits, including those racers who refuse to run them. They point to reduced wear on bearings and less risk of crankshaft failure, thereby reducing costs.
“Sprint cars and Formula 1—both rumored holdouts to damper integration—are currently using dampers or have used them,” said Brian LeBarron of Fluidampr, Springville, New York, manufacturer of a viscous-style damper. “Fluidampr recently had great success with a small-diameter viscous damper on a Formula 1-inspired, 1,000-hp, 10,500-rpm, 396-cubic-inch V12 OEM production engine. The engine developer enclosed the damper within the timing case and used active oil cooling to achieve zero damper maintenance. In addition to the enclosed crankshaft damper, four camshaft viscous dampers were used to diminish torsional vibration effects in the valvetrain itself.”
Sprint car engine builders have always worried about weight and packaging when trying to fit a damper in line with the water pump. Still, there are benefits.
“They are giving up horsepower, more peak rpm and the longevity of their engine and/or the components on it,” added Beattie. “If you can’t convince a racer that a few pounds will free up a lot of power, then I am not sure what will.” —Mike Magda
SOURCES
–
ATI Performance Products
atiracing.com
Bullet Racing Cams
bulletcams.com
Callies Performance Products
callies.com
Crower Cams & Equipment Co.
crower.com
Eagle Specialty Products
eaglerod.com
Fluidampr
fluidampr.com
Howards Cams
howardscams.com
K1 Technologies
k1technologies.com
Lunati
lunatipower.com
Mile High Crankshafts
milehighcranks.com
Molnar Technologies
molnartechnologies.com
Pankl Racing Systems
pankl.com/en/
Scat Enterprises
scatcrankshafts.com
Shaftech
shaftech.com