Tailor Made
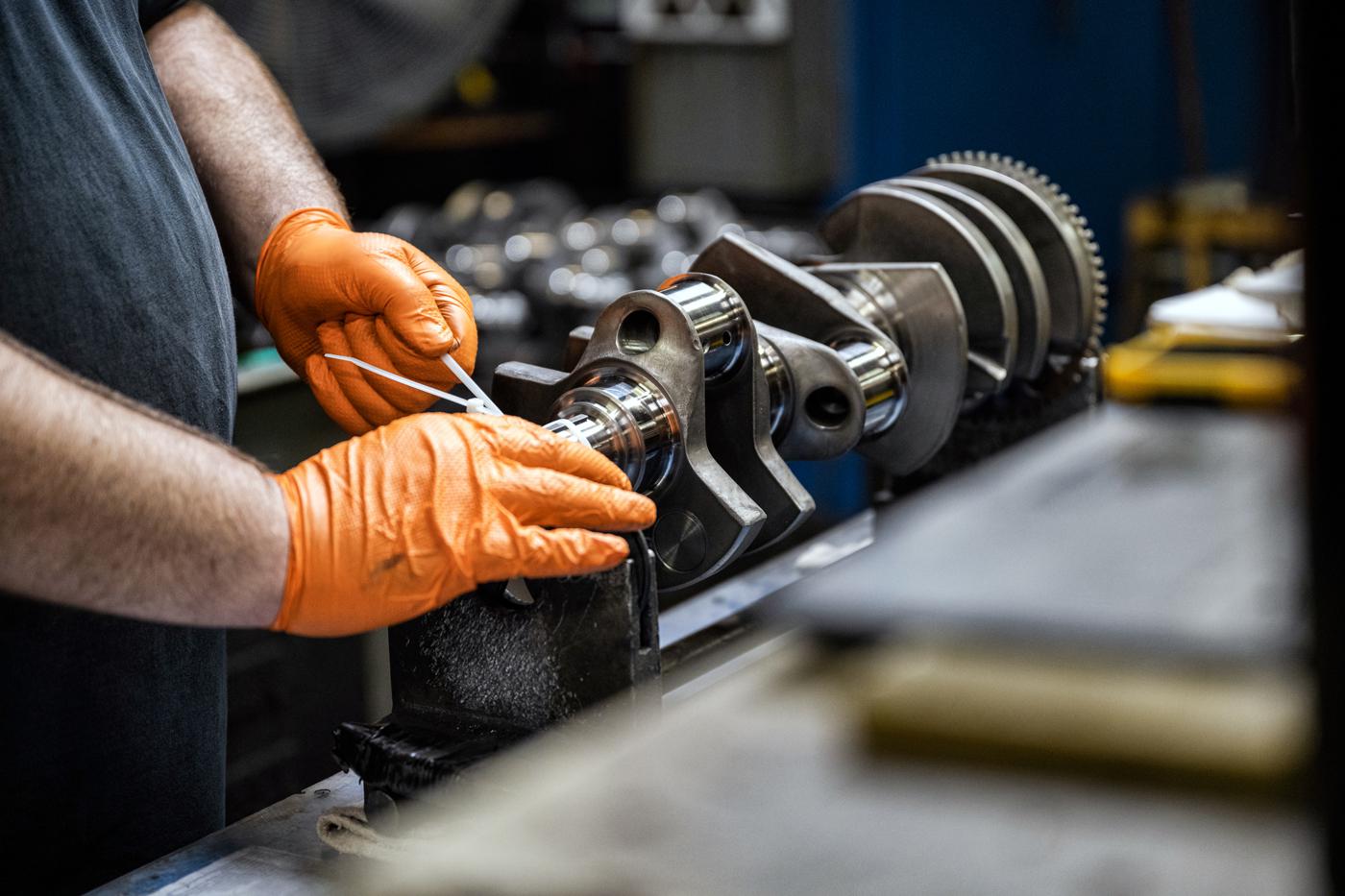
Manufacturers continue to report strong demand for one-off crankshafts across various applications, even as the lines between custom and off-the-shelf grow blurrier by the day.
Crankshaft manufacturers offer a wide variety of counterweight designs, strokes, weight options and journal sizes for popular racing platforms. So many, in fact, that it begs the question: What is a custom crankshaft these days?
“Generally speaking, it’s because a racer is trying to build something special or something different,” said Tom Molnar of Molnar Technologies, Kentwood, Michigan.
“A custom crankshaft, technically, could be any crankshaft that’s different from stock,” added Kirk Peters of Howards Cams, Oshkosh, Wisconsin. “More and more crankshaft companies have made the custom add-ons part of their product line.”

“If you’re looking for something that isn’t in the catalog, then it automatically becomes a custom crankshaft,” noted Tom Lieb of Scat Crankshafts, Redondo Beach, California.
“Our crank offerings haven’t changed much over the last three to five years with the exception of adding a couple of LS billet offerings,” said Michael Tokarchik of Manley Performance Products, Lakewood, New Jersey. “Throughout our crank program, our designs don’t typically evolve beyond what we launch.”
But an off-the-shelf billet crankshaft?
Who would have predicted that for the shopping scenario entering the 21st century when ‘billet’ was synonymous with ‘exotic custom,’ and high-quality forgings were still hard to come by outside of factory performance vehicles.
“In the ‘old days’ when nothing aftermarket was common, the only option was billet,” explained Alan Davis of Eagle Specialty Products, Southaven, Mississippi. “Nobody could justify the initial cost of a forging. You saw it first with pistons and cams. Everything high-performance was billet, hence the reputation.”
Led by a racing community that quickly accepted new OEM engine platforms, and then overcame its aversion to EFI and boost, the aftermarket industry grew as fast as horsepower levels at the track. Companies selling rotating assembly parts started investing in forge tooling and offering extra crankshaft features such as unique counterweight designs and extra machining to reduce weight.
Strong Demand
Even though racers have so many options off the shelf or out of the catalog today, there continues to be a strong demand for custom crankshafts. Callies Performance Products has no fewer than six different lines of forged and billet crankshafts in its catalog, and yet the custom orders come in at the rate of two per business day—and that’s just for an aging 67-year-old engine platform.
“You’ll probably fall over, but last year alone for the old-school small block Chevy, we produced 546 different custom cranks,” said Brook Piper of the Fostoria, Ohio-based company. “And I would say 99% were mainly for a custom stroke.”
Rules drive much of the demand for a custom-stroke crankshaft. There may be a cubic-inch limit, and the engine builder finds a way to expand the bore on a cylinder block—thereby requiring a unique stroke to fit within the displacement rules.
Sometimes the need arises from a completely new engine. Callies recently worked with a major racing outfit that was building a new engine platform to compete in a high-profile series.
“They had a general architecture in mind, and then we put our scent on it,” said Piper. “The race shop did an FEA analysis on the model that we proposed. When it came back to us, we did some more tweaking. It went back and forth at least twice.
“You can tweak the pin arms, the width of the counterweights, elements like that,” continued Piper. “Cranks fail in the pin arms from torsional loads. I’m sure they had the cylinder pressures and loads it will see at rpm, and they can simulate the entire crankshaft operation.”
Truly Staggering
The research behind some of today’s custom crankshafts can be truly staggering. Austria-based Pankl manufactures racing and OEM performance-engine components and is a sister company to CP-Carrillo in the US. Pankl has worked with NASCAR, Pro Stock, and Formula 1 teams in designing and manufacturing crankshafts, and the development process always starts on a desktop.
“We first provide basic data sheets that need to be filled out,” explained Christoph Wachmann, adding physical space constraints are needed along with cylinder pressure, operating rpm, maximum torque, piston and rod weights and, most important, the type of racing.
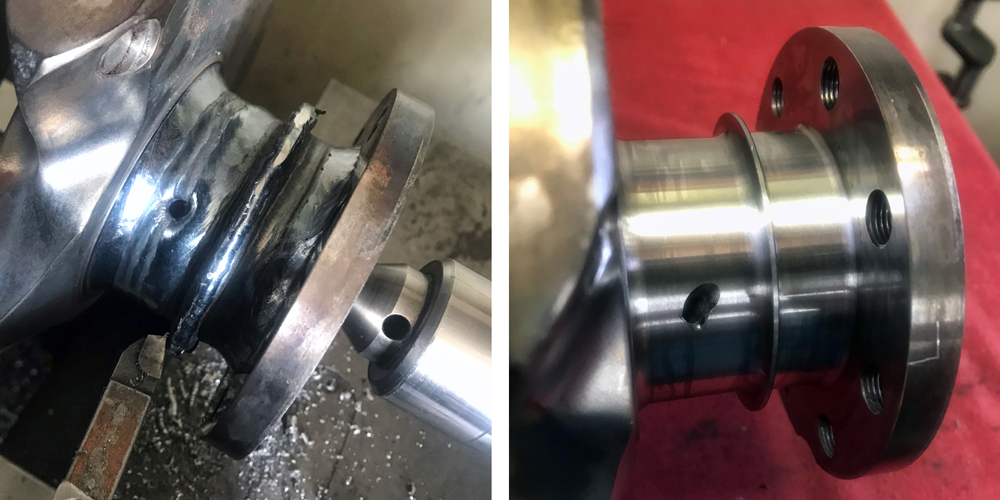
“The next step is to define the development targets. Is the focus on friction or being as light as possible?” continued Wachmann. “If you make it very light, it could flex more and end up being a higher friction crankshaft.”
A basic computational model analysis with FEA and balancing schemes is performed followed by a 3D model. From there, the customer could order a crank, or the computer could start working overtime.
“There are a lot of budget-dependent options on simulation. This could include choice of materials, dynamic calculations where we would need a model of the crankcase. We can take into account the full interaction between the rotating crank with rods and pistons,” added Wachmann.
The basic development calculation runs around $10,000, and just the simulation and modeling can easily top $100,000 when oil-film analysis and other computations are required.
“An important point for crankshafts is oil flow and lubrication,” said Wachmann (see sidebar on page 98). “You have all kinds of possibilities in passage angles, bore diameter, chamfers. Combine this with inertia analysis, oil pressures and rotation of the system. We’re trying to design the oil system to avoid things like cavitation.”
Exotic Alloys
Most custom crankshafts are machined from billet bar stock because the cost of producing forging dies for a single application is prohibitive. For one customer, however, Pankl was able to use the automaker’s forging dies from a similar engine to manufacture a custom crank that was part of that factory’s supercar production program.
“We forged the cranks with our own material, then applied our process for induction hardening and filet rolling,” said Wachmann.
An advantage noted by some competitors is that Pankl has access to exotic steel alloys made in Europe. Wachmann said it’s a steel that will accept extremely deep nitride hardening.
“Deep nitride for us is up to a millimeter or 1,000 micrometers,” said Wachmann. “Usual nitride depths can be 100 to 300 micrometers. A NASCAR crankshaft may go up to 500 micrometers. These steels have a different chemical composition that allows a deeper nitride. To get a one-millimeter depth, the crank stays in the nitriding furnace for 200 hours.”
Steel quality is one of the most confusing, if not mysterious, metal properties that weigh on engine builders’ minds. Most performance forgings are made from 4340 steel. To some, that alloy can mean different formulas are in play.
“I don’t believe all 4340 steels are the same,” said Dave Olsen of Mile High Crankshafts, Denver, Colorado.
Olsen doesn’t manufacture crankshafts, but he sees a wide range of models that are in for repair or customizing.
“You can call it 4340 because it has whatever window of ingredients in it, but that window might be pretty big,” he said. “I’m not a metallurgist, but it just seems that the domestic cranks are a better grade of steel.”
Popular Request
Echoing what Piper mentioned earlier about stroke length being the driving force in custom cranks, Olsen said modifying the stroke on a crankshaft is one of his most popular requests. For example, NHRA Stock and Super Stock classes allow a plus or minus .015-inch variation on the published stroke for a particular engine.
“So, we’ll add around .013-inch to be safe. It’s not really for bigger displacement. It gives the guys a little more compression because they’re limited on combustion chamber size and the pistons they can run,” said Olsen. “And then there are the Pro Stock guys. They’re always changing their combination. A little less stroke because their bore is getting big enough and they can’t make the 500-cubic-inch limit.”
Mile High Crankshafts can also change the journal size. “We do that because basically the crank manufacturers are so buried with orders that they don’t have time to do some of these jobs,” added Olsen.
Fluctuating workforce numbers have prompted some crank companies to limit custom orders because of the extra manhours, and experienced specialists who grind crankshafts are retiring with no replacements in sight.
“It’s a labor issue,” said Peter Harris of Crower Cams & Equipment Co., San Diego, California. “To tell you the truth, we do still make custom stuff, but I’m shying away from it. The amount of time that’s involved and what I can get for them kind of make it cost prohibitive.”
Lunati, which is based in Olive Branch, Mississippi, does not accept custom orders but has a mild customizing program for high-performance cranks in its catalog.
“Our forgings and heat-treat process ensure we have a crank that will handle about all you want to throw at it,” said Will Vance. “As far as custom work, we do offer undercutting the throws for rod length accommodation, as well as offer a ‘blower series’ where we enlarge the flexplate holes as well as the crank-snout bolt. We also add an additional keyway.”
“The only secondary service we offer is balancing, which is surprisingly popular with our engine builder customers as of late,” said Manley’s Tokarchik, echoing that recurring theme of tight labor, especially for skilled machinists. “This is likely due to staffing issues on their end. They can still enjoy a nice profit while their employees can focus on other things.”
“We offer some additional machining on finished products, like undercutting the counterweights,” added Davis. “Also, a round sprint-car rear flange and a second keyway for blower applications.”
Billet More Common
As demonstrated, off-the-shelf billet crankshafts are becoming more common because it’s still cheaper than making forging dies to produce just a dozen or so for a rare application. Molnar recently designed a billet eight-counterweight crankshaft for a vintage AMC block because the forging dies are no longer available. Just tooling up a typical forging die would cost upwards of $100,000 to $120,000. A crank manufacturer would need to sell 200-plus crankshafts just to recover the initial investment.
Molnar designs his billet crankshafts in the US but has them machined offshore, however, that factory requires a minimum order. “I got enough guys together to make a run of it,” said Molnar, adding that once there were commitments for the minimum order, word spread and he was able to double the number. He also added a couple extra to the order in case there was a quality issue with one to have an example in stock. “I wouldn’t necessarily call these custom cranks, they’re more of a limited run.”
The average turnaround time for a custom crank when raw materials and labor conditions are favorable is 10 to 12 weeks. That’s after all the data review and consultations, which don’t always end in a custom order. Some engine builders have radical ideas that prompt the manufacturer to shy away when there’s conflict over the predicted structural integrity.
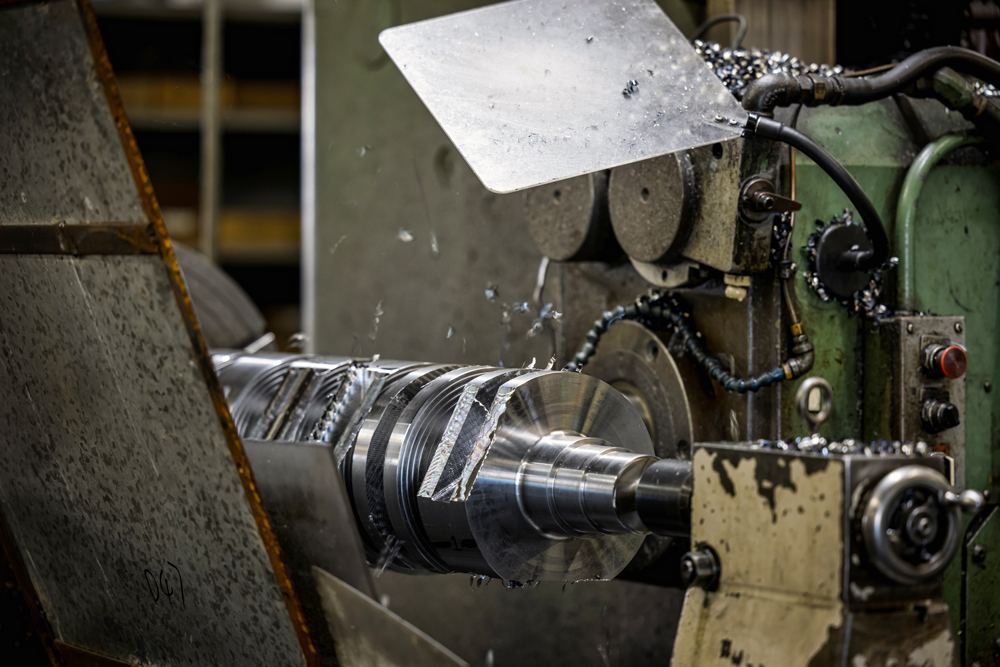
“The strength of the crankshaft is between the top of the radius on the main to the bottom of the radius on the throw,” explained Lieb. “That cross-section is what holds the crank together. As you increase stroke and/or decrease the rod journal or main journal diameter, that cross-section changes. If the guy has a 4-inch-stroke crank for a small block Chevy and wants to run a Honda rod journal and an early 283 main size, I mean, there’s less than my pinky finger worth of material holding it together.
“We’d talk and say, ‘Hey, I’m flattered that you want to keep our employees working by making a crankshaft for you, but you’re going to be really pissed when it breaks. So we’d rather not,” added Lieb.
When to Choose
Now that the lines between custom and off-the-shelf are blurrier than ever, just when should an engine builder choose to order a custom crankshaft?
“Most stock crankshafts have enough safety margin built into them to handle a mild increase in power and torque. The time to upgrade to a performance or custom crankshaft will vary depending on your application. However, if you’re building an engine that will be boosted, blown, or use nitrous, you should always upgrade to a billet,” said Matt Polena of K1 Technologies, Mentor, Ohio.
“Horsepower really isn’t a factor in custom ordering a crankshaft,” noted Peters. “For example, a hobby stock dirt track racer with an unlimited budget wants to build a killer engine and custom-orders a super light crankshaft with Honda journals for his two-barrel 450-horsepower engine.”
“Horsepower doesn’t break cranks,” agreed Molnar. “Look at a Top Fuel car. They make 11,000 horsepower first time down the track on a new crank. But they also know they can get only so many passes before that crank does break due to the fatigue of bending and twisting from the high loads.”
The best advice, as always, is to talk to the manufacturer’s tech reps. They can provide critical advice along with useful do’s and don’ts when it comes to ordering crankshafts.
“We’ve had requests for crankshafts before that we could not fulfill, so we recommended the customer to a billet manufacturer,” said Davis. “Such things as unique stroke, unique application, something that had a design aspect that was necessary, and we couldn’t accommodate. It rarely has anything to do with power-handling capabilities. It is most often due to unique design aspects that were required.
“Finally,” he added, “race what you can afford to replace.”
The Straight and Narrow
It’s an oil strategy that’s been around for decades, and it still works.
“When Chevy designed the original 265-cubic-inch engine, they used the straight-shot oil system,” said Tom Lieb of Scat Crankshafts, Redondo Beach, California. “All of us crank guys over the years have tried to improve on that. Guess what? We haven’t been able to in the last, what, 70 years?”
Straight-shot oiling means there is a straight passage for the oil to flow without interruption from the crankshaft mains to the rod bearings. Over the years, refinements have been made to the angles and positions of the feed holes to better serve high-rpm applications.
“With some engine builders, placement of the oiling holes is highly important, and with others it’s no big deal,” said Kirk Peters of Howards Cams, Oshkosh, Wisconsin.
For a time in the 1980s, though, racers had a love affair with cross-drilled crankshafts. It was a high-tech-sounding term that stirred fantasies of much-improved lubrication. The original concept added supplementary oil passages through the mains in the belief that oil flow would be equalized to the bearings. Basically, users thought the bearings would get two shots of oil with each crank rotation. At high rpm, however, centrifugal forces come into play and would actually draw oil away from the rod journal oil holes.
“There isn’t enough oil pressure in the world to push that oil in at high rpm,” said Tom Molnar of Molnar Technologies, Kentwood, Michigan. “You can’t get oil to the rod bearing and then you fry them.”
“You could do an entire article on crankshaft oiling,” added Alan Davis of Eagle Specialty Products, Southaven, Mississippi. “The highly debated topic of standard vs. cross-drilled oiling is ripe with speculation, and inaccurate information is floating around. Much of which is the opinion of ‘old school’ racers and has very little, if any, engineering analysis behind it.”
Any discussion of crankshafts will almost always touch on weight. As engine builders demand lighter and lighter cranks, they also don’t want to give up strength. Cross-drilled cranks were out of the question when manufacturers offered to gun-drill the mains. But there’s also a way to lighten the crankshaft using the oil system.
“Almost all dirt late models have gone to a wide-bore or 4.500-inch bore-space cylinder block,” explained Peter Harris of Crower Cams & Equipment Co., San Diego, California. “Some are running into durability issues with how light a crankshaft they want. We combat this by putting in smaller oil holes. We used to have quarter-inch oil passages. Then 7/32nds. Now it’s eighth-inch. It doesn’t seem to be an issue for oiling, but it definitely makes the crankshaft stronger.” —Mike Magda
Sources
Callies Performance Products
callies.com
Crower Cams & Equipment Co.
crower.com
Eagle Specialty Products
eaglerod.com
Howards Cams
howardscams.com
K1 Technologies
k1technologies.com
Lunati
lunatipower.com
Manley Performance Products
manleyperformance.com
Mile High Crankshafts
milehighcranks.com
Molnar Technologies
molnartechnologies.com
Pankl
pankl.com
Scat Enterprises
scatcrankshafts.com
Shaftech
shaftech.com