Positive Reinforcements
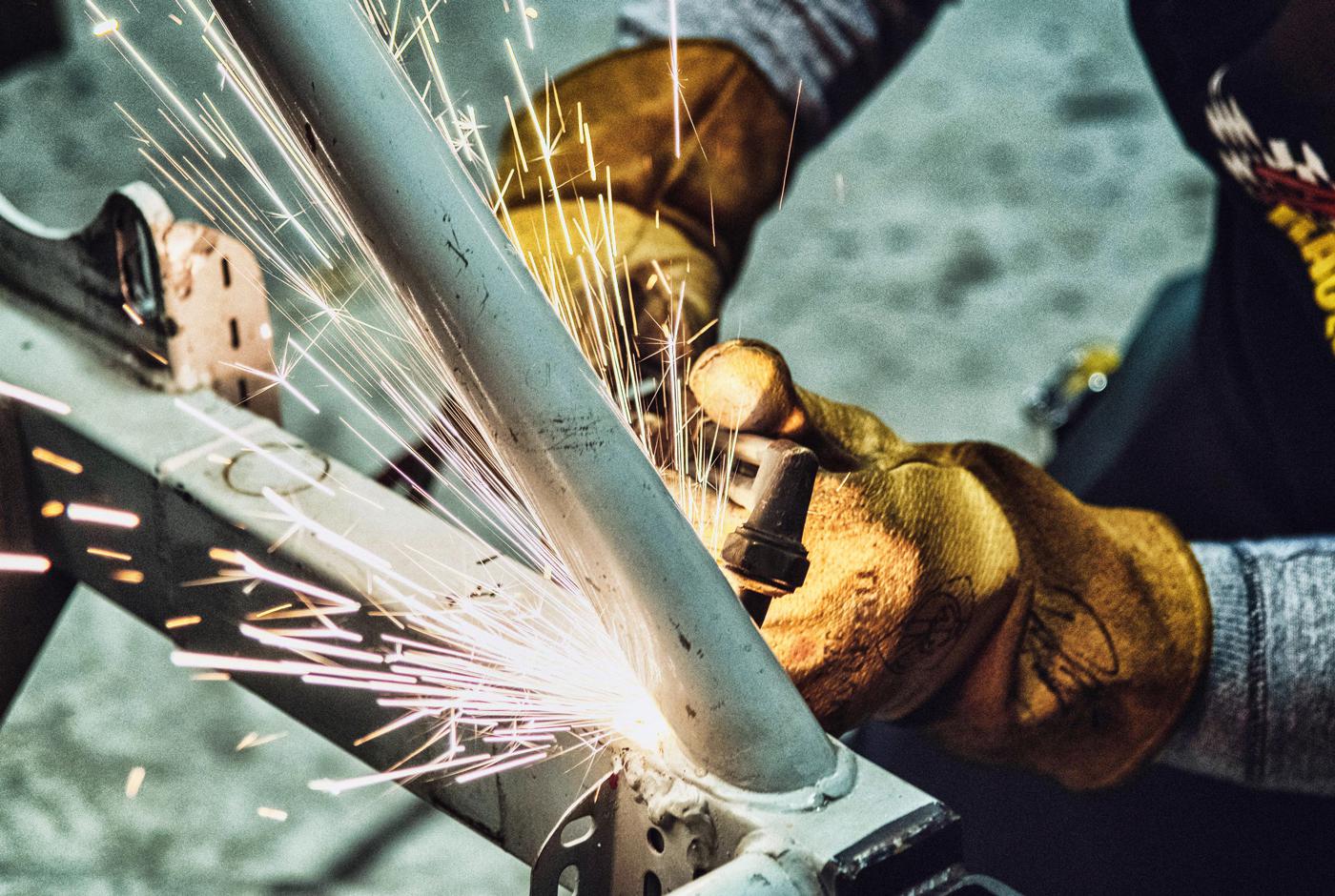
Armed with specialized building techniques, modern digital tools, and advanced materials, today’s fabricators are building stronger, safer and more effective chassis than ever before.
It starts as just a pile of tubes. Bit by bit, expert fabricators piece it into a spidery jungle-gym-like sculpture. The driver is wrapped in a cocoon of heavy metal hoops. The pieces are tied together into a cohesive whole, and a race car takes shape.
At this point races are already won or lost. That’s how important a chassis is.
At a glance, chassis fabrication for most race cars might look like it hasn’t changed much in recent years. But a number of subtle, incremental developments have come along to make race car chassis safer and stronger, while at the same time more economical and less time-consuming to build.
To learn about these changes, we talked to leading experts in the fields of fabrication, materials, and welding. Their insights provide valuable lessons on what it takes to get the ideal race car chassis.
Different Bars for Different Cars
When it comes to chassis design and fabrication, the needs of different forms of motorsports vary widely. Whether its drag, dirt track, or drifting, every type of racing creates different stresses and potential dangers that chassis fabricators have to take into consideration. Crashes in rally competition, for example, are completely different from practically any other type of motorsports.
“A unique aspect of rally is that we have a very high potential for point loading our cars,” said Ryan Thompson of Thompson Racing Fabrication, Cedar, Michigan. “That means you can hit a tree at 100 miles an hour, and all the energy that your car had carried with it is really focused in that 8- to 24-inch area of the tree. That puts a tremendous amount of energy in that one small spot.”
In contrast, road racing has its own unique mayhem when things go wrong, explained Tony Colicchio at TC Design in Campbell, California. “In road racing, we’re generally hitting big tire walls, which rip stuff. So our problem is that if you hit a tire wall head on, it likes to move wheels into your foot area. The other thing we see are big side-to-side impacts—a whole car hitting you in the door bars.”
Given these complex, dynamic forces acting on a chassis, it might seem prudent to simply err on the side of more bracing, adding extra bars wherever forces could possibly act. But this can build too much weight into a car, and often rules don’t permit it. So fabricators have to carefully consider node placement, the location where tubes meet each other on a chassis.
“A lot of the lower classes in SCCA and NASA have rules that say you can’t add too much bracing or structure within their minimum standard of cage,” said Colicchio. “They’re trying to keep the cost down. So we’ll look at where we are going with the tubing nodes, to improve safety.”
Worth noting is that while many race car chassis are full, purpose-built, tube-frame designs, many forms of motorsports don’t allow such comprehensive structures. This is particularly true in entry-level classes. In such cases, fabricators typically try to reinforce the structure as much as possible to improve handling and crashworthiness.
“In some classes, if it’s allowed, we do seam welding on the car,” said Colicchio. “A lot of the seams of the unibody would be stitch-welded every inch or so just for extra stiffness on the chassis itself, and then the roll cage would be added to that. Then we try to do as many things as possible with the stock mounting points. If we can go to a mounting point that’s safe, like the rear shock tower, that helps make the whole chassis stiffer.”
Digital Discoveries
To handle the complex needs of building modern race car chassis, shops are increasingly relying on highly specialized digital tools. These allow fabricators to design more effective chassis and assemble them with greater precision, less waste, and fewer mistakes.
CAD software has long been a part of high-volume shops, especially production chassis manufacturers, because of the ease in which digital designs can be integrated into an ongoing fabrication line. Now, thanks to lower cost software, it increasingly makes sense for smaller shops and even for do-it-yourselfers. One of the handiest types of CAD programs for chassis builders is tube-bending software.
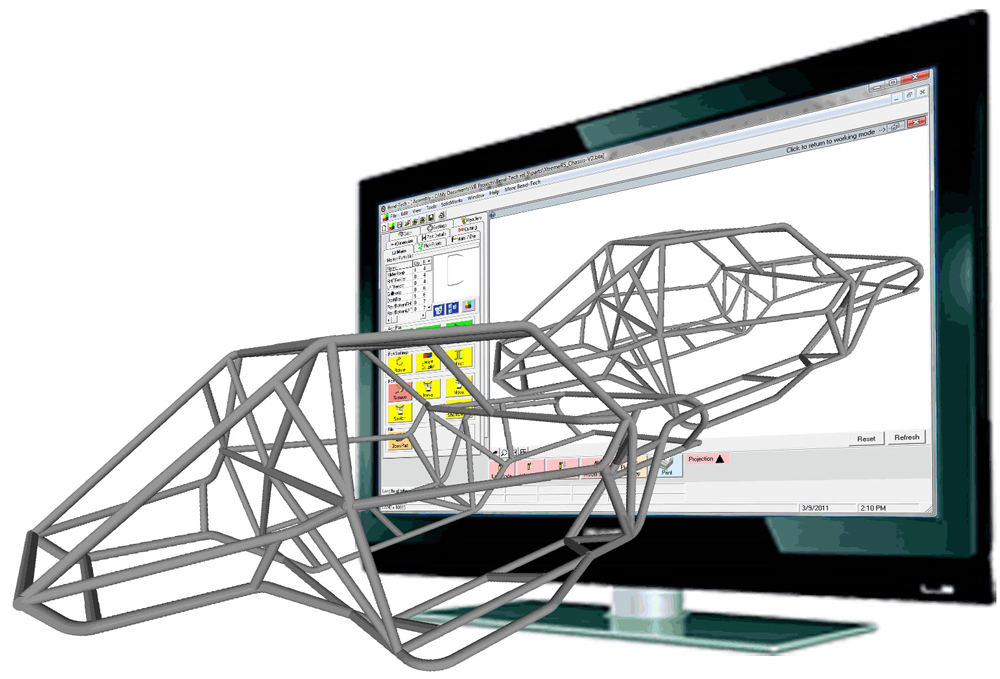
“With that software, you can lay out your entire frame and then print out a build sheet on how to make each part, and it’ll spit out a materials list,” said Carter Vos of Trick Tools, Pella, Iowa. “You know how much material to order, and it can really simplify the tube-bending process. One of the most popular for us is Bend-Tech Pro, which sells for around $300. You don’t have to know CAD to understand how to use this program. Most of our users are productive the first time they ever use it.”
Some chassis fabrication shops are taking the CAD revolution to the next level by incorporating 3D scanning to precisely image the cabin of cars and design roll cages and other structures. “I really think that’s where the high end of this industry is going,” said Colicchio. “Late last year we purchased a brand-new FaroArm that does blue laser 3D scanning, and then also probe scanning as well. It’s extremely accurate. From there, we have plug-ins that will bring that information and data set into SolidWorks.”
“Most of my cages are for the same 10 cars over and over,” added Colicchio. “So if I spend the time scanning them and getting the design to where I want it, it makes us more efficient and much more consistent. I’ve got a part that’s laser cut and CNC bent, and it will always fit in the same spot. Once we have that file, we can change things like door bars really easily.”
Hot Metal Mastery
For chassis builders, there are basically two types of welding, MIG and TIG. MIG welding is one of the fastest, easiest forms of welding. It utilizes a gun with filler wire automatically fed from its tip. Although it still requires proper training and technique, MIG welding is largely a matter of pushing a button and keeping the gun moving.
TIG welding, in contrast, is one of the hardest forms of welding. It uses a stationary electrode for the arc, which demands precise, steady hand positioning while welding. The amperage is varied continuously with a foot pedal by the operator, who manually adds filler rod to the molten metal pool. Tremendous coordination is required.
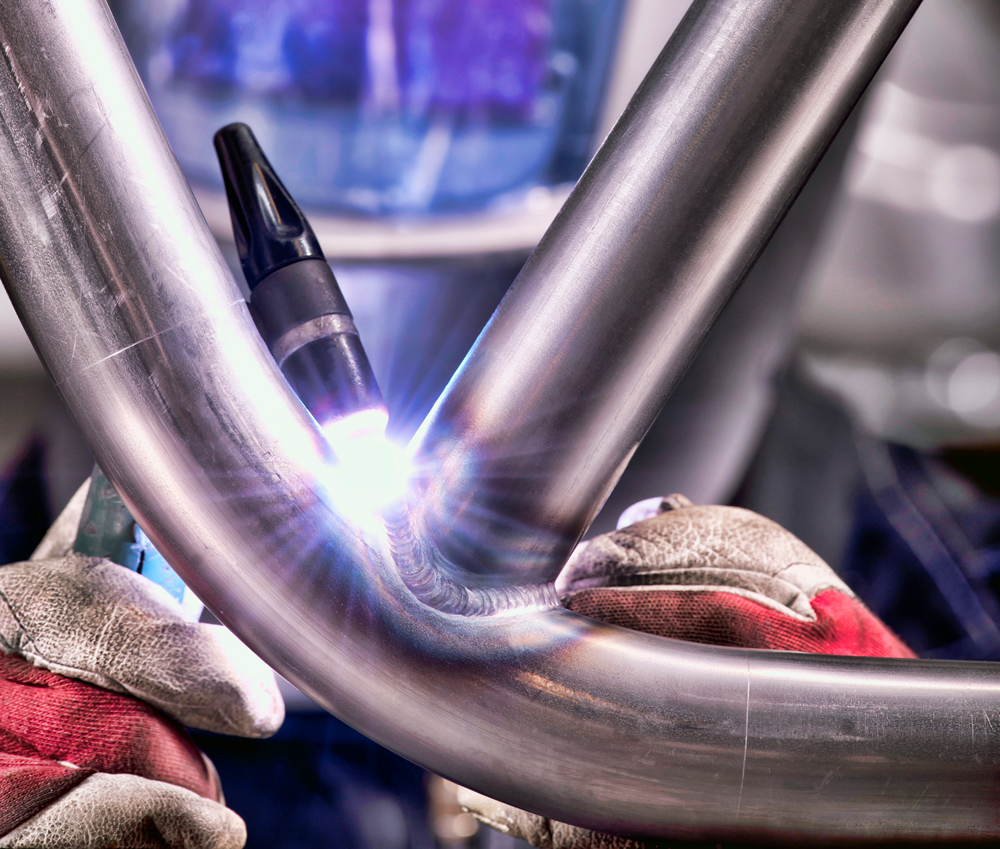
Because of this, MIG welding is usually much faster than TIG welding, making MIG a natural choice for companies that mass produce standardized chassis designs. But there’s also an aesthetic factor to be considered. Even in the hands of the very best welder, the look of MIG welds can’t match the flat, tight, rhythmic looping of an expertly done TIG weld.
For some situations, there’s no choice. The material dictates the type of welding. “If it’s 4130 chromoly tubing it has to be TIG welded, per NHRA rules,” noted Lon Damon from Lincoln Electric, Cleveland, Ohio.
All these things said, both types of welding can produce equally strong welds when done properly. And so, different shops often prefer one over the other for their own unique reasons. Some fabricators switch back and forth to optimize costs for customers. “We do mainly MIG welding, and then on the higher-end projects we do TIG welding,” said Colicchio. “It’s strictly for cost. There’s no strength difference given the materials we’re using. With MIG welding, customers can spend their money on our engineering and fabrication rather than having the prettiest weld.”
The Devil in the Details
With so many subtle nuances and variations in different race car types, specialization is vital to getting an effective chassis. The best chassis fabrication shops usually serve just one form of racing and often work with the same handful of basic car designs. This enables them to obsess over the details that separate the safest, winningest cars from the less desirable ones.
“We have probably two families of cars we work on, with BMW being our biggest one,” said Colicchio. “Mazda is the next, because of its support of club racing. So we’re very efficient at those builds. That gives us a competitive advantage. Customers don’t have to do the R&D.”
On the flipside, chassis builders who aren’t familiar with a particular type of car or racing series often saddle customers with subpar workmanship, dangerous design compromises, or cars that won’t pass tech. “We see the biggest problems from shops that come from a different form of motorsports,” said Colicchio. “I’ve seen beautifully TIG-welded cages come to me, but the safety for a road race car, and the hits that we’re going to see, just weren’t addressed.”
Great Expectations
For all the importance that individual shops play in building safe, competitive race car chassis, the process of chassis fabrication all stems from racers’ demands and expectations. Unfortunately, those can be surprisingly low, according to our sources. “There are a lot of people who don’t see a rollcage as a safety device,” said Thompson. “Their motivation is, ‘How cheaply can I get through tech? This is just an obstacle I need to overcome.’ They’re probably not going to end up in our shop.”
Much of the difference between subpar chassis designs and effective ones comes down to the details, which in many cases aren’t immediately obvious. “Sometimes the proper load path isn’t the easiest path to construct,” said Thompson. “Compound joints are very difficult to assemble, where you have four, five, six, seven tubes all hitting in one node. If you’re looking for a price point, you start spreading those pieces out. That’s a lot faster, a lot easier to put together. But we’re willing to do the extra work because we want that best quality product possible.”
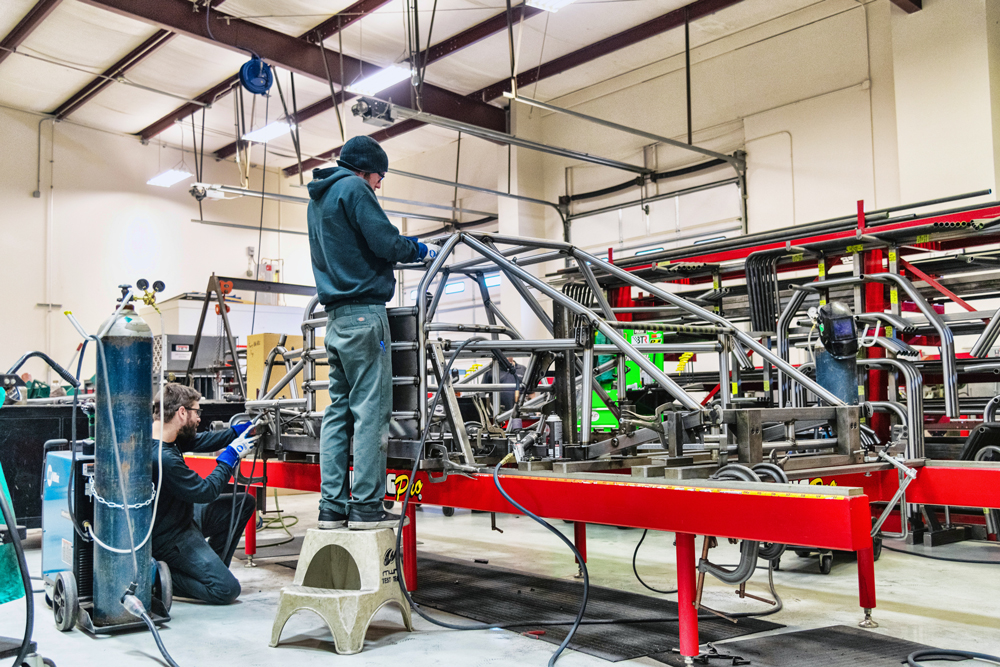
Unfortunately, there are some fabricators who simply haven’t mastered the basics of their craft. “I still see bad welds,” said Damon. “I’ve seen some stuff that kind of raises your eyebrows. But I don’t see as much as I did years ago. Now it’s mostly the backyard guy who does a chassis for someone or an update on a professionally built chassis—they added some bars and stuff.”
This has prompted some fabricators to call for standards that would apply to all chassis builders. “In Europe, there are shops that are FIA certified,” said Colicchio. “They’ve gone through steps to prove that their welding is up to spec, that their joint building is up to spec, and so on. In the US, we don’t have that for the most part. It’s really just up to the sanctioning body to tech whatever it is at that point. And as you know, whether that car passes or not can vary wildly depending on who techs it.”
In general, the sources we spoke to noted that customers are getting more savvy about the importance of a good chassis and what it takes to get one. “I see a trend that people are getting better educated,” noted Colicchio. “We’re seeing people willing to spend the extra money. And they’re starting to realize that it takes time as well. A fabricator you can just hire next week maybe isn’t one you want. If a fabricator isn’t busy, there’s probably a reason why he’s not.”
Ultimately, the quality, safety, and success of a race car chassis comes largely down to the competence and commitment of the shop that builds it. It’s a matter of pride and peace of mind for many fabricators. “I have this mantra: Every roll cage we build should be the very best cage we’ve ever built,” said Thompson. “I’m very aware that people are relying their lives on what we build. I want to sleep well at night.”
Steel with Appeal
–
Except for those in a relatively small handful of top motorsports series, race car chassis are still usually fabricated from welded tubular steel, as they have been for decades. For that, there are two common choices of material: mild steel or chromoly. Both have advantages in terms of weight, working methods, and safety in specific applications.
Chromoly is an alloy steel that gets its name from chromium and molybdenum, two of its main alloying elements. This type of steel is often referred to as 4130, its American Iron and Steel Institute designation.
Developed in the early 20th century, chromoly was readily adopted by the aviation industry for its light weight and high strength. Today, 4130 chromoly is widely used in race cars for many of the same reasons. However, the choice often comes down to tradeoffs between weight and crashworthiness. Chromoly is lighter, but it tends to be more rigid. Mild steel, by contrast, is heavier, but it yields more in a crash before breaking, thereby absorbing more energy.
For this reason, the choice of one over the other is often dictated by sanctioning bodies. Rules typically specify welding methods as well. Mild steel can be readily welded using MIG or TIG, but 4130 tubing usually has to be TIG welded. Its thinner walls require more precise heat control.
Along with these tried-and-true materials, new advanced high-strength steels are gaining popularity among fabricators. One that’s getting considerable attention lately is Docol R8, made by Swedish company SSAB and marketed in the US by A.E.D. Motorsport Products in Indianapolis, Indiana. “We use a lot of Docol R8 tubing,” said Ryan Thompson of Thompson Racing Fabrication in Cedar, Michigan. “It was made for motorsports. With it, we can use thinner, lighter material that allows us to put in a few more tubes without adding extra weight.”
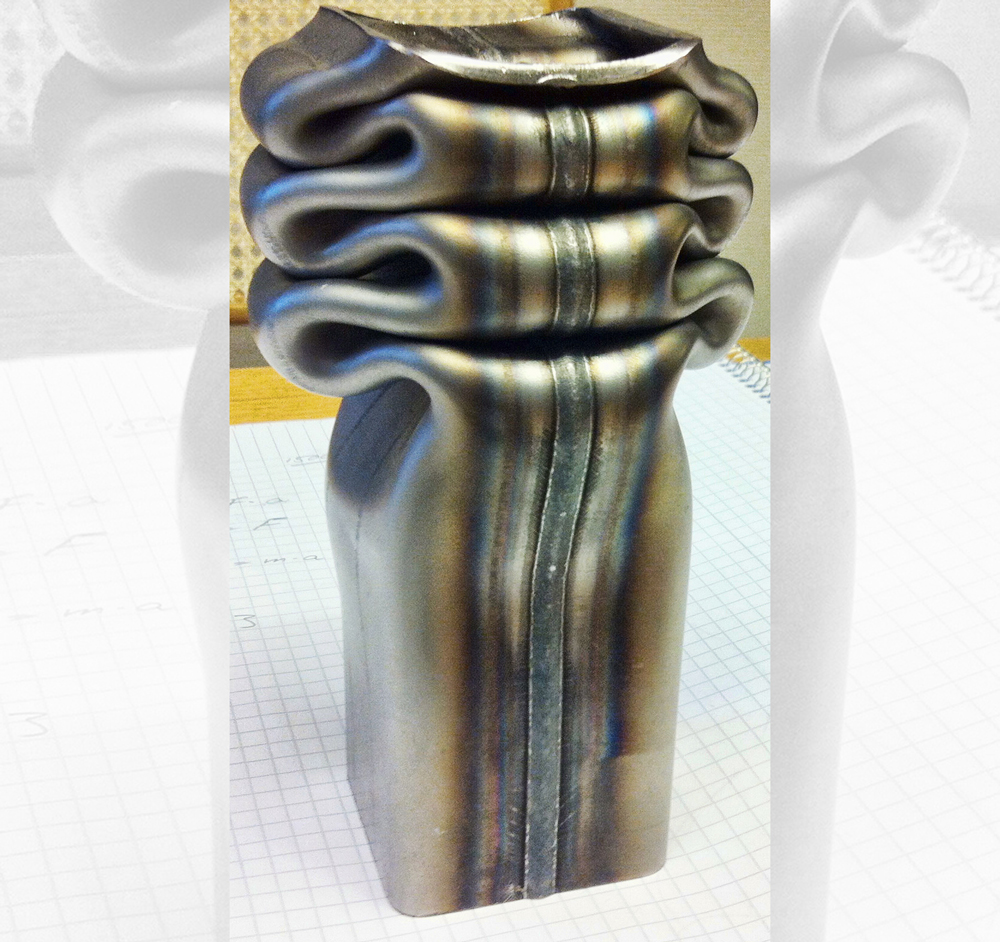
Docol R8 is said to blend the best characteristics of mild steel and chromoly. “Docol is stronger than 4130 by 10% or 15%,” said Al Lowe at A.E.D. “But it’s made with chemical and metallurgical properties that are much more like a mild steel. Because it’s a mild steel, we don’t see the deviation in the heat-affected zone that you do with a heavily alloyed product, so the chemistry and the mechanical properties stay much more consistent. That generally leads to a better fabricated car with less tension, less stress. It gives us a better joint for defamation and impact.”
Some of Docol R8’s advantages come from the method used to form it into tubing. “Chromoly is an extruded type of product, and Docol is rolled from flat product into a tube,” said Bruce Wilkinson of SSAB. “So the consistency and the flatness, the gauge control and the overall dimensions are stronger. The fatigue behavior is much better, much more consistent.”
Along with this advantage, Docol R8 is said to have much of the same compressibility as mild steel. “I’ll use stock cars as an example,” said Lowe. “In the event of a collision, a heavy right front impact transfers a lot of energy to the left rear. Docol steel absorbs that energy. You don’t find the structural failures in other areas of the car that are common with a 4130-built car.”
According to Lowe, Docol can be worked with the same methods as traditional steels, including MIG and TIG welding. It can also be welded to dissimilar metals such as 4130 and stainless steel. He also noted that most sanctioning bodies allow Docol R8 for chassis fabrication, and they typically specify the same wall thicknesses for it as they do for 4130. —David Bellm
SOURCES
–
A.E.D. Motorsport Products
aedmotorsport.com
Lincoln Electric
lincolnelectric.com
SSAB
ssab.us
Strong Hand Tools
stronghandtools.com
TC Design
tcdesignfab.com
Thompson Racing Fabrication
thompsonracingfabrication.com
Trick Tools
trick-tools.com