Separating Fact from Fiction
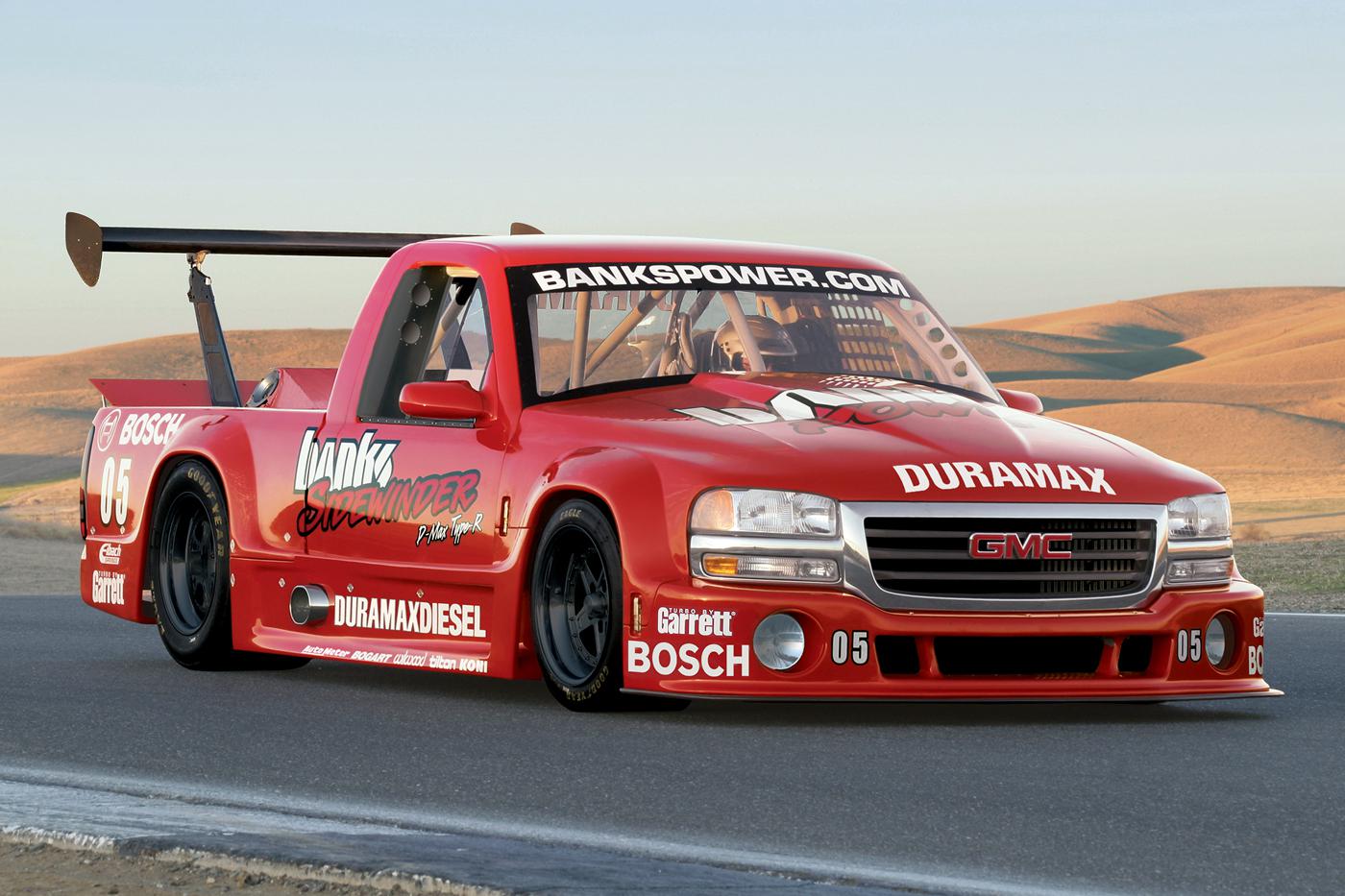
Thanks to advances in areas like engine management controllers and fuel delivery, today’s diesel setups don’t need to operate like smoke stacks on wheels in order to make big power.
Diesel technology has been fighting a long, uphill battle to establish its place in the realm of high performance. While diesel’s inherent benefits in commercial and heavy-duty applications have been well understood for some time, these oil-burning powerplants have largely been overshadowed by their gasoline counterparts in hot rodding and racing circles due to their narrower operating range, comparatively limited aftermarket support, and, to a tangible degree, public perception.
“Outside of diesel’s competition origins in sled pulling and tractor pulling, there’s been a handful of teams over the years who were brazen enough to put one in a drag car, and for a long time these were kind of rat rod-style builds that were basically put together because they told us we couldn’t do it,” explained Jared Alderson of Kill Devil Diesel in Poplar Branch, North Carolina. “That essentially relegated these builds to sort of ‘side show’ status—a novelty kind of thing. It was like, ‘Hey guys, watch the smokey truck go down the track and then we’ll get back to real racing.’”
That perception wasn’t aided by the popularization of diesel street trucks being tuned to “roll coal” so that their exhaust systems would belch out massive plumes of thick, dark smoke. “Rolling coal produces incredible amounts of smoke and soot that blocks out the sun,” explained Gale Banks of Banks Power, Azusa, California. “That’s horsepower that you can see, but not feel or use. It’s wasted fuel. That never really struck me as a manly thing to do. I’d rather be out there setting records.”
Nick Priegnitz of Calibrated Power in Woodstock, Illinois, said that while emissions-compliant vehicles currently comprise a niche of the diesel motorsports segment, there’s been a larger shift toward a cleaner approach. “There are a growing number of events in the country that currently have a clean diesel category—classes that mandate factory-style emissions controls. But in general, the attitude in the industry now is to use as little smoke as possible to make the power you need to make. It’s kind of the unspoken tuner’s rule now. It used to be a ‘more smoke is better’ mentality, but that has changed.”
Combatting Misconceptions
It’s no secret that efficiency is key to extracting all the performance potential of a given setup. As diesel tuning has become more sophisticated over recent years, improved efficiency has helped to push diesel performance to new heights.
“Look at what the Firepunk guys and people like Ryan Milliken are doing today,” Alderson said. “Some of these guys are now nipping at the heels of the fastest gas cars in the world. It has reached a point where diesel is a viable option for folks who are serious about being competitive.”
Thanks to these strides in diesel technology, segment-leading diesel setups are operating virtually smoke-free.
“I think there’s this general misunderstanding that if it’s not smoking a lot, the power isn’t there,” observed Brian Jelich of JeliBuilt Performance, Moyock, North Carolina. “But it’s actually the other way around. When it’s clean, you know that thing is making power. You look at Derek Rose or Ryan Milliken—their setups are making more than 3,000 hp and they’re running clean. There’s not even a haze coming out of the exhaust.”
Alderson said that those who roll coal at the track these days typically do so for the sake of the visual spectacle, but there are drawbacks that go beyond any environmental concerns. “At the track there’s a showmanship element to it, but ultimately, we’d rather just burn all that fuel. One thing we see a lot from gas guys who are coming into the diesel world is this concern about running too lean and blowing the motor up. But in the diesel world, it’s really quite the opposite: Lean is actually what we want. The smoke might look cool, but it’s not efficient, and it’s not good for the engine.”
He also told us that recent efficiency improvements have come in part due to teams and builders looking for ways to improve durability. “We obviously want to go as fast as we can while keeping parts alive,” Alderson continued. “Running cleaner is better for the engine. You’re not sooting the oil, and you’re not dealing with fuel wash on the rings as much. So, to some degree, running cleaner is really a byproduct of trying to get these combinations to live.”
Priegnitz said that modern rich-running setups also quickly run into the law of diminishing returns from a performance standpoint. “A diesel typically makes its best power around an air/fuel ratio of 15:1, and the line for ‘clean’ is somewhere around 16.5:1 or so, if you’re using a well-designed piston and injector. In the past, folks would run down to in the 12:1 or 13:1 range mainly just because they could, and engine controls weren’t great at keeping the engine out of that space during transient operation, like during turbo spool-up, for instance. But the engine controls we’re using today are light years ahead of what folks were using not so long ago, and there’s really no reason to leave the engine with an excess of fuel like that anymore. A sooty truck is just performing under its potential.”
Changing The Game
Banks said that OE-backed development of technologies like Bosch’s common-rail injection system have also played an important role in improving diesel engine efficiency across the board, but maintaining that efficiency when launching off the line is perhaps the biggest challenge facing tuners.
“Say you’re at sustained wide-open throttle, like at Bonneville,” Banks explained. “In that situation the turbocharger is at full song, so all you’ve really got to have is a good match of parts. But coming out of the hole is a different story. Because the turbocharging usually lags behind the fuel—you’ve got to have exhaust energy to spool it up and get the air to come to the party—people put a huge shot of fuel in to minimize that lag. But it isn’t always turbo lag that’s the problem. It can sometimes be air system lag. And that comes down to understanding the volume of air that you’re compressing, and how long it takes to get to the intake valves.
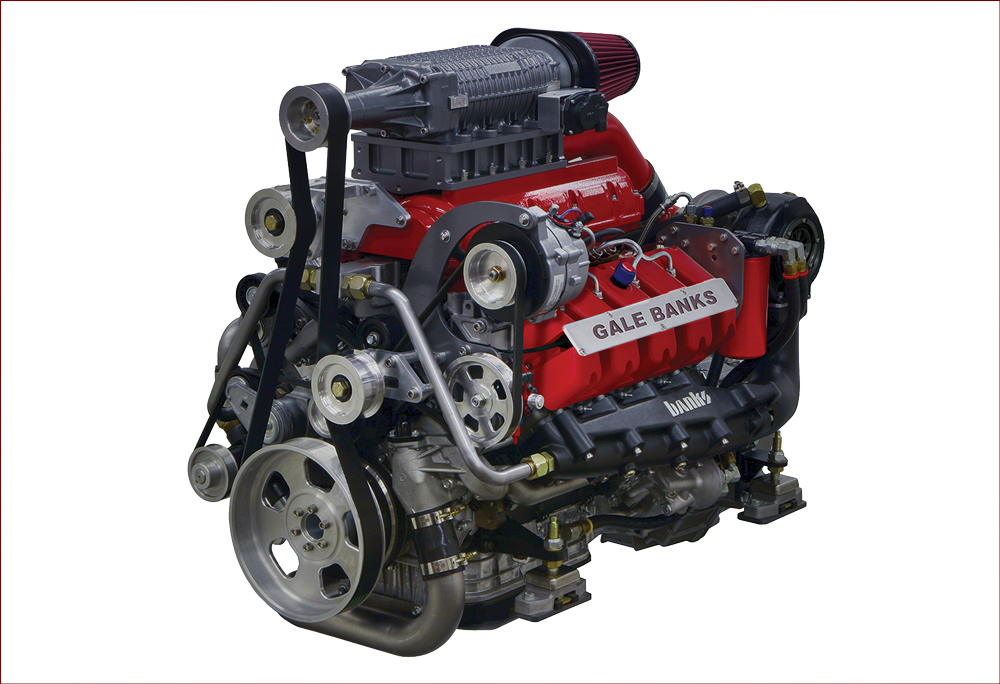
“You also have to consider where you open the intake valves and where you close them,” he continued. “On the exhaust side, you want to blow down the cylinder and get all the pressure out of there by bottom dead center, if possible. You don’t want to open the exhaust valves too early, but you want it to be early enough to let the energy out and kick the turbine in the ass. So you do the most you can with camshafts, turbine housing, and turbine wheel specifications, and that’s also where variable valve timing comes in. There’s a wonderful sweet spot to be found that really helps the turbine response.”
Jelich pointed out that advancements in tuning have made finding that sweet spot a much easier task. “The tuning methods have evolved quite a bit over the past five to 10 years, and now we have standalone systems available that take it to the next level. You can tune directly to an air/fuel ratio. That’s a big deal because the goal is to keep your EGTs low, and the more you lean it out, the lower the EGTs are. We try to shoot for about 30:1, and at that point there’s no visible exhaust coming out of the pipe. It’s actually cleaner than a lot of the gas vehicles that are going down the drag strip. And it’s making really good power without creating a lot of heat in the engine, so it’s putting the heads, pistons, and other components through less abuse.”
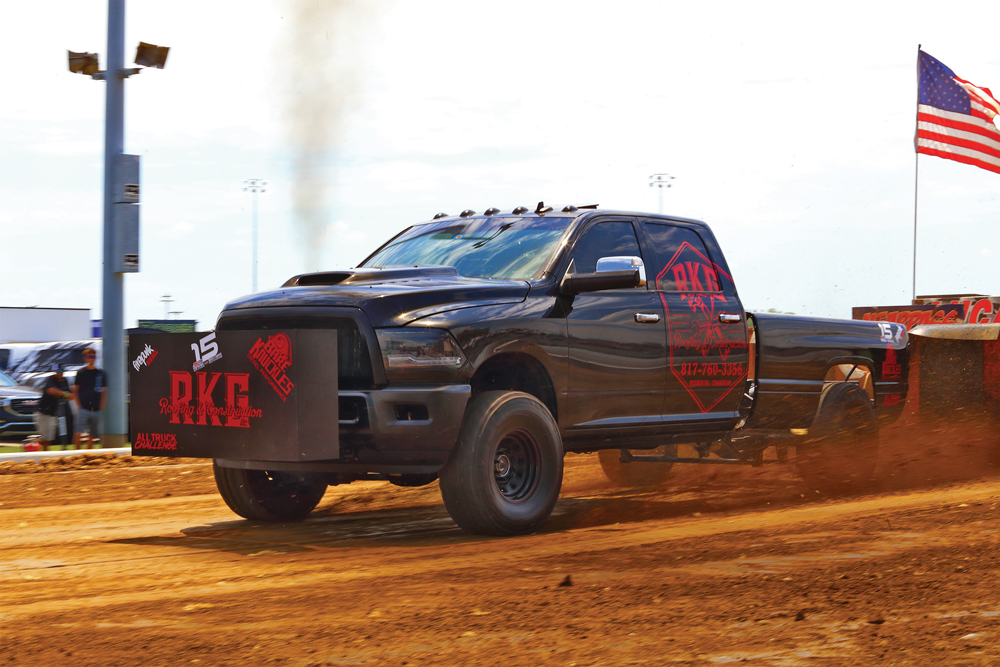
Tuning to an air/fuel ratio is possible without a standalone, but the capabilities of these systems can yield better, more consistent results. “For example, there isn’t a standalone system available for my 7.3-liter Power Stroke because the injectors use very high voltage and there’s nothing that supports it,” Jelich pointed out. “With that it’s just about adjusting the fuel quantity and pairing it up with a nitrous system to balance everything out and keep the AFR where we want it. Monitoring EGTs can be helpful with that, too. When you’re at 18:1, for instance, you’re making a lot of heat, and EGTs are probably at more than 2,000 degrees. When you start to lean it out with a lot of nitrous, you can bring that down to 1,400 or 1,500 degrees. But with a MoTeC system, or some of the Bosch stuff, those adjustments are basically automated because the systems can self-adjust.”
The situation is aided by stronger aftermarket support in other areas as well, Priegnitz said. “We have a broad spectrum of available turbochargers now, and that’s made a big difference. Ten or 15 years ago, it was common to see a turbo thrown on a truck that was just grossly oversized for the application simply because the options were limited. Now we’re able to match parts much more precisely to the desired output and use-case of the vehicle, and that has helped improve that transient engine response, which inherently makes them run cleaner.”
This more dialed-in approach also offers the added benefit of improved parts longevity. “When the engine is running more efficiently, you’re not washing the cylinder walls, burning piston rings as badly, you’re not killing turbos, and you’re not putting valves and seats through as much abuse,” explained Alderson. “That’s another huge advantage.”
Building Momentum
Regardless of the trajectory that the emissions-compliant diesel racing takes down the road, ongoing development in the high-performance diesel realm is expected to continue to improve efficiency in the coming years.
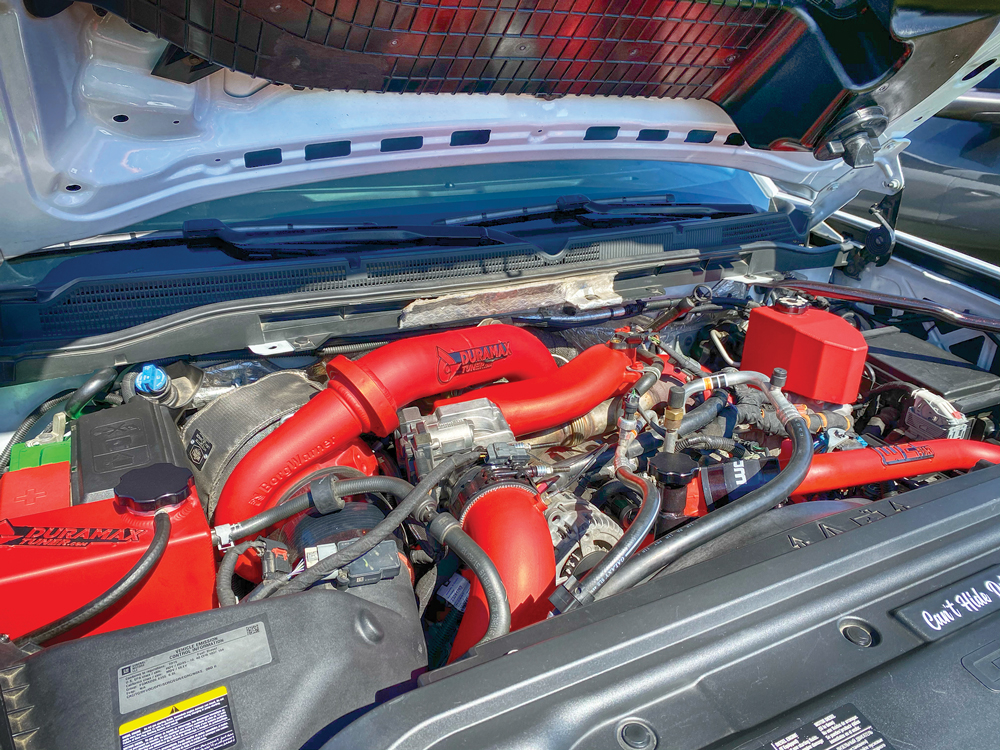
“The real key here is having enough oxygen in-cylinder to burn all of the fuel in-cylinder,” Banks said. “We’re still at a point where a lot of folks still haven’t maximized the efficiency of their charge-air cooling systems. They don’t flow enough coolant, or they might have insufficient airflow; there’s still a lot of mistakes being made in this area, especially when it comes to sizing. That’s an important consideration because, in a really serious race engine, the charge-air cooling system has a huge impact on horsepower. What you need is an instrument across the charge-air cooler that measures pressure in, pressure out, temperature in, and temperature out to ensure that you’re getting the lowest pressure drop, and the highest temperature that you can get. We’re in the process of developing that type of an instrument right now.”
Meanwhile, Priegnitz looks to the expanded range of turbocharger options in the aftermarket as a means of improving both competitiveness and efficiency. But he also noted that, in the diesel realm, some of the biggest innovations being made today are occurring at the OEM level.
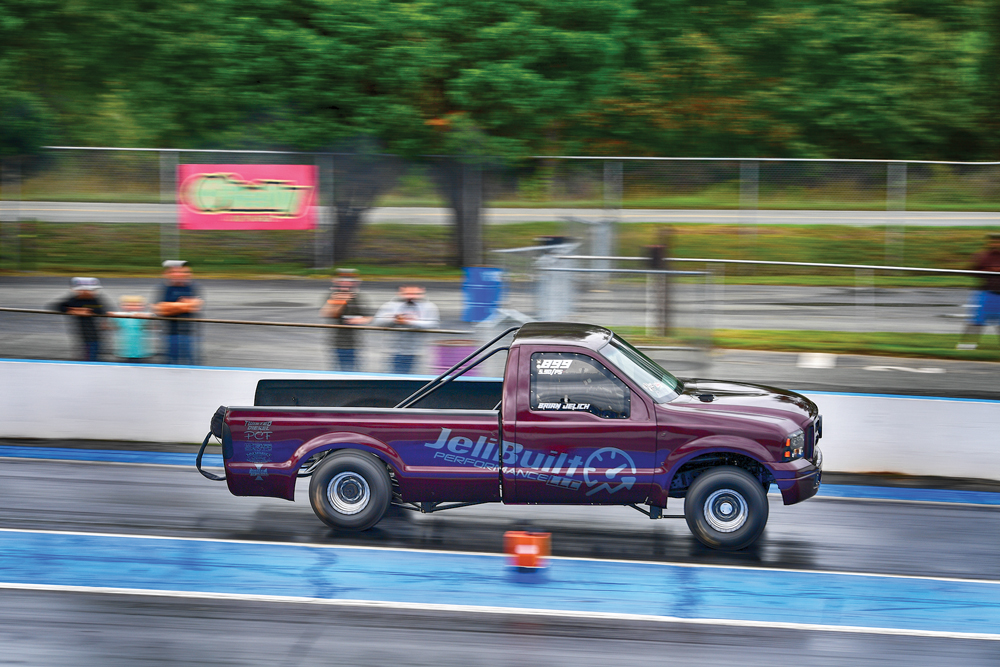
“I think the variable geometry stuff could be a neat addition to class racing. But what’s interesting is that we’re used to motorsports existing as a way to help drive innovation that will trickle down to street-driven vehicles. Right now, in the diesel racing world, I feel like the development is kind of flowing the other way: The innovations are coming from the street to the track. We keep seeing higher and higher fuel pressures from the OEMs with better pumps, better injectors, and better atomization. I think that racers will definitely benefit from that through things like more precise cylinder pressure control.”
As this segment continues to mature, Alderson expects high-performance diesel setups to become less of an anomaly in the racing world. “It’s continuing to get more and more competitive with the mainstream options. We’re breaking records every year, and not by small amounts. I think that’s going to continue to bring increased interest and support, which in turn will draw more people into the diesel industry.”
SOURCES
Banks Power
bankspower.com
Calibrated Power
duramaxtuner.com
JeliBuilt Performance
jelibuiltperformance.com
Kill Devil Diesel
killdevildiesel.com