Rods of Destiny
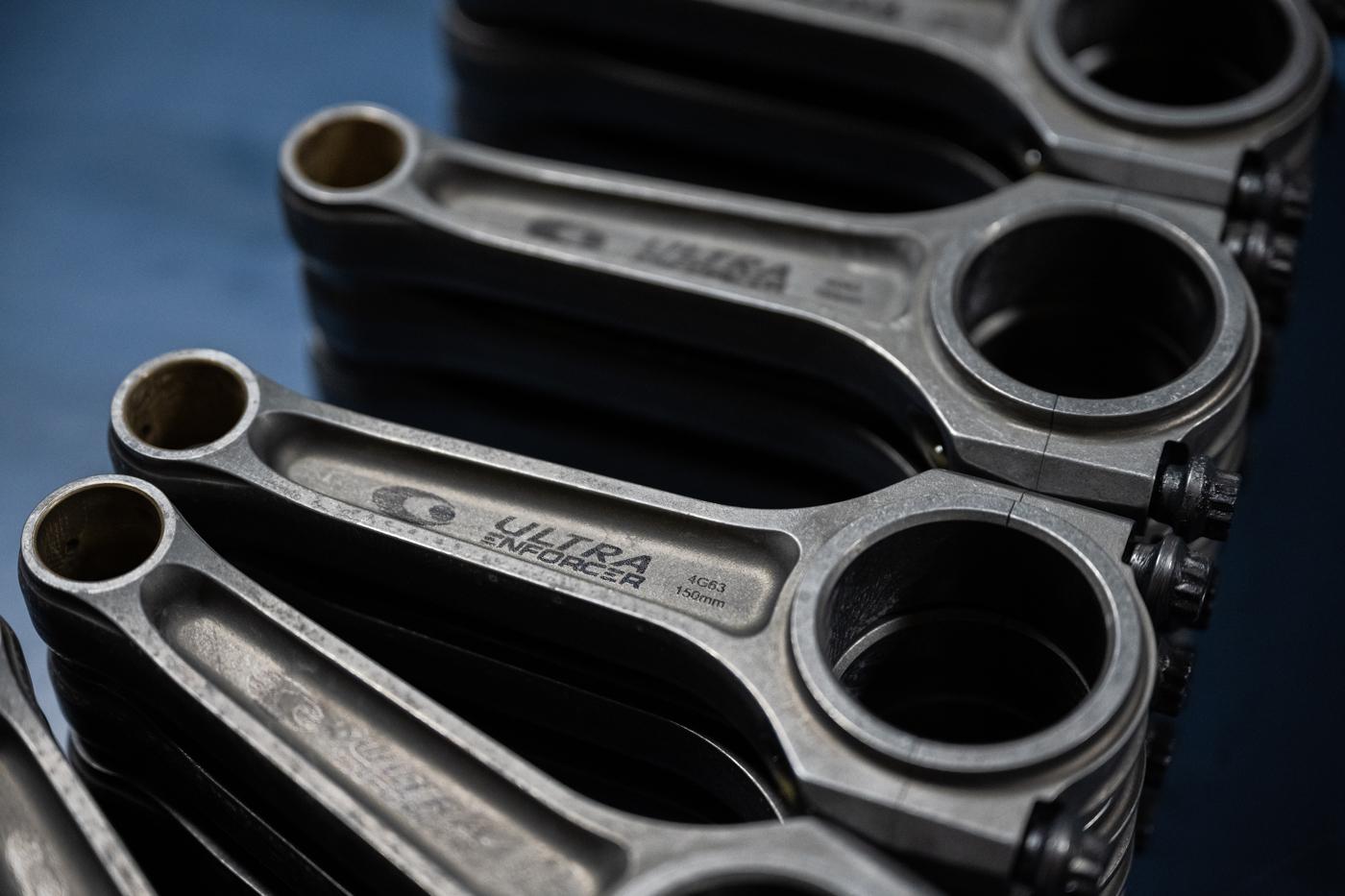
With the exception of unexpected raw material price hikes and occasional supply glitches, the domestic connecting rod market is quite stable in terms of product innovation and design—but there may be a quiet revolution looming in the shadows.
Compare a sampling of today’s performance-driven connecting rods with a similar cross-section of rods from 10 years ago and there may not be much difference to the untrained eye. Machining will be more precise, critical dimensions more accurate, finishes more impeccable, and certainly the fasteners will be much more robust.
However, to paraphrase Gertrude Stein, “a rod is a rod is a rod.” Not much has really changed in design or materials for the majority of popular motorsports applications. Sanctioning body rules often limit innovation by mandating a specific design or imposing minimum weights to reduce the temptation to try uber-expensive materials. So it’s safe to say that there’s a slow news cycle around the connecting rod industry right now.
“There really hasn’t been much that has changed in the rod biz,” admitted Tom Molnar of Molnar Technologies, Kentwood, Michigan, who has been involved in designing and manufacturing connecting rods for more than 40 years. “Costs are going up, cost of materials, labor, overhead. Our customer base has grown. People are finding us through word of mouth.”
“I really wish I had something to tell you on that particular avenue, but I don’t,” concurred Danny Cerny of Scat Crankshafts, Redondo Beach, California.
“At this point, Howards has no new rods in the pipeline. We continue to stay committed to grassroots racing and entry-level racers,” added Kirk Peters of Howards Cams & Racing Components, Oshkosh, Wisconsin, who added a stunning bit of gossip to the conversation. “As for 3D printing of parts, I’ve heard rumors that high-end engine builders have played with the idea, but there are no pictures to substantiate the rumors.”
Well, we have some pictures, but the innovative rods are not meant for IMSA or NASCAR or even Pro Stock. Instead, those “anadiaplasi” titanium rods (see sidebar on page 100) are designed for an exotic hypercar V10 engine expected to produce more than 3,000 horsepower for the street.
Such a design trend is unlikely to spread to mainstream racing markets. The technology is still in its relative infancy and quite expensive. Instead, connecting rod manufacturers are focused on improving production efficiency, keeping orders filled, and helping customers select and install the correct rod. New or upgraded products will be introduced as power levels continue to increase or new applications are introduced to the market.
Future Planning
“There has been a tremendous increase in ‘typical’ power output, and with that comes increased power-handling capabilities for connecting rods,” explained Alan Davis of Eagle Specialty Products, Southaven, Mississippi, noting that the company has been using its current third-generation design for some 20 years. “Eagle’s much anticipated 4th Generation design (4D) will become available this fall in time for the 2024 racing season.”
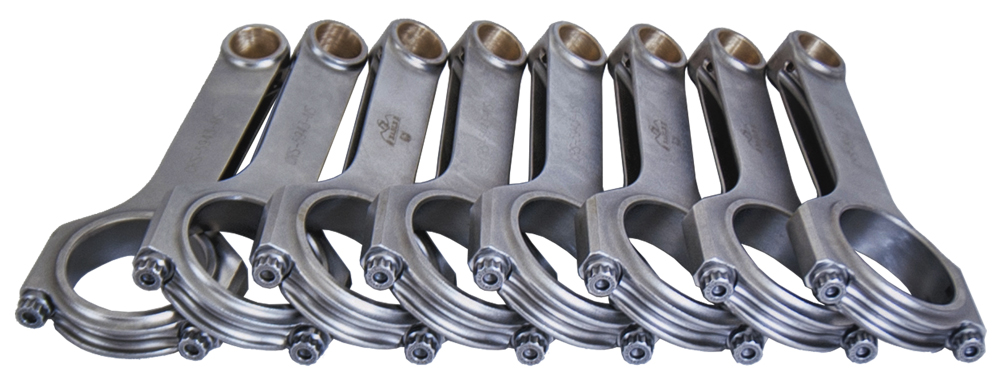
This redesign will feature thicker webbing in the beam to improve tensile and compressive strength.
“But the big improvement is realized around the big end of the rod,” Davis continued. “Several improvements have been made to strengthen the big end and make the bore more rigid to further prevent distortion under high load.”
The rods will be fully CNC machined from Eagle’s exclusive two-piece forging of a proprietary steel alloy. ARP 2000 bolts will be standard, and ARP’s Custom Age 625+ bolts may be an option. Initial applications will be Chevy small block, LS, Chevy big block, Ford 302 and 351W, along with popular Honda, Subaru, and Toyota engines.
Racers’ need for more rod strength is also driving Callies of Fostoria, Ohio, to expand a popular line to include more applications. “We’ve had a line for small block Chevy and LS called the Compstar Xtreme,” explained Brook Piper. “We’re now expanding that into big block Chevy and Gen III Mopar. It’s for the guys running up to 1,800 hp, so it’s going to be a good rod for probably 60% of the market like the average bracket guy and street/strip. They’ll retail for around $1,250 per set.”
Callies basically put its Compstar H-beam rod on steroids to create the Compstar Xtreme. Engineers added some weight by thickening the web and added an H11 tool-steel fastener. Overall, Callies calls the rod an “H-I” design.
“It’s kind of a hybrid between an H- and I-beam,” said Piper. “It’s made from 4340 steel, and we’ll start with 6.385, 6.535, and 6.700 lengths for the big block Chevy. For the Gen III Hemi we’ll have a 6.125, which is popular for strokers. We’ll also expand the LS with a 6.350 rod for the tall-deck guys.”
Over at Crower Cams & Equipment in San Diego, California, material costs make for challenging times, but there are bright spots. “We’re holding our own right now. Our titanium rods are big movers, but it’s really hard to compete with material costs,” said Peter Harris, noting that titanium has doubled in price in recent years and costs for heat-treating have also increased significantly. “People can’t always justify spending $800, $900, or $1,000 per rod. But everyone wants a light rod that doesn’t break at high horsepower.”
A new material and new applications are making headlines at CP-Carrillo in Irvine, California. The company is now offering rods for the Nissan VR30DDTT, and expanding into powersports is also a priority as rods are now available for the Aprilia RS 660 twin, Arctic Cat Z1 Turbo, Can Am X3, and Suzuki GSXR1300 Hayabusa (extreme duty).
“We’re also working on a Ford Godzilla rod for high-horsepower applications,” said Richard Batchelor. “We have been offering our new high-strength steel called C107. This material is approximately 22% stronger than our standard material, and we can make rods 10–15% lighter while maintaining the same strength. With this material we have been making some Porsche rods for a few of our high-end customers that are actually lighter than the factory titanium rods.”
With such a wide variety of connecting-rod styles, weights, and materials available to racers, it’s more important than ever to make the right decision when building a competitive engine—especially if more horsepower is in the plans.
“The biggest thing with selection is to buy a rod that you can build off of for years to come,” stressed Piper. “If a big block Chevy guy calls in and says he’s going to do a little bit of nitrous, we all know that eventually leads to a whole lot of nitrous. So choose your rod that will fit your need but allow for growth, because we all have this addiction to go faster. We all know how quick and easy it is to put on a turbo or a ProCharger. I always impress upon our guys here to ask about plans for the future so we can get the customer the best bang for the buck.”
Avoiding Distractions
Most experienced engine builders have already narrowed down their preferences for every type of engine and will order accordingly. However, there remain some misconceptions that can sidetrack even the best builders. One such distraction is the question of rod balance; that is, every rod in a set must be balanced equally and perfectly. That precision isn’t always possible because of wear on machine tools during a single run.
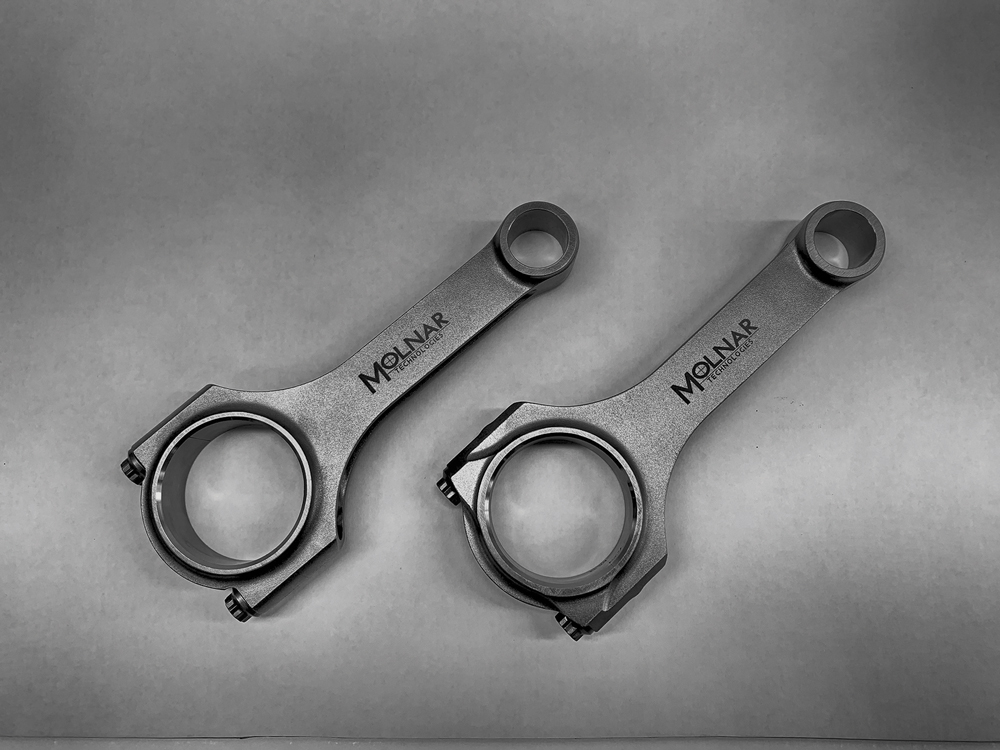
“Say there’s a run of 96 rods. The first rod will be the lightest and the last will be heaviest,” said Roger Friedman of Dyer’s Top Rods, Forrest, Illinois. “You’re always going to have a little variation, maybe one or two or three grams. But some engine builders are so critical that they want perfect. Well, how do you measure the oil on the rod when it’s spinning around?”
The real problem isn’t a difference of a couple of grams in a rod or two, it’s when the engine builder tries to correct the problem. “They take metal off the wrong places, usually with a belt sander, and they weaken the rod,” explained Friedman. “Every engine builder is different, but we see some hack jobs, especially with stroker crankshafts and the rods are cut for the camshaft. We actually put the rods in a fixture with the bolts properly torqued, and we’ll mill it with a CNC machine. Then we deburr all the edges and polish it. We’re trying to give this rod every chance to survive.”
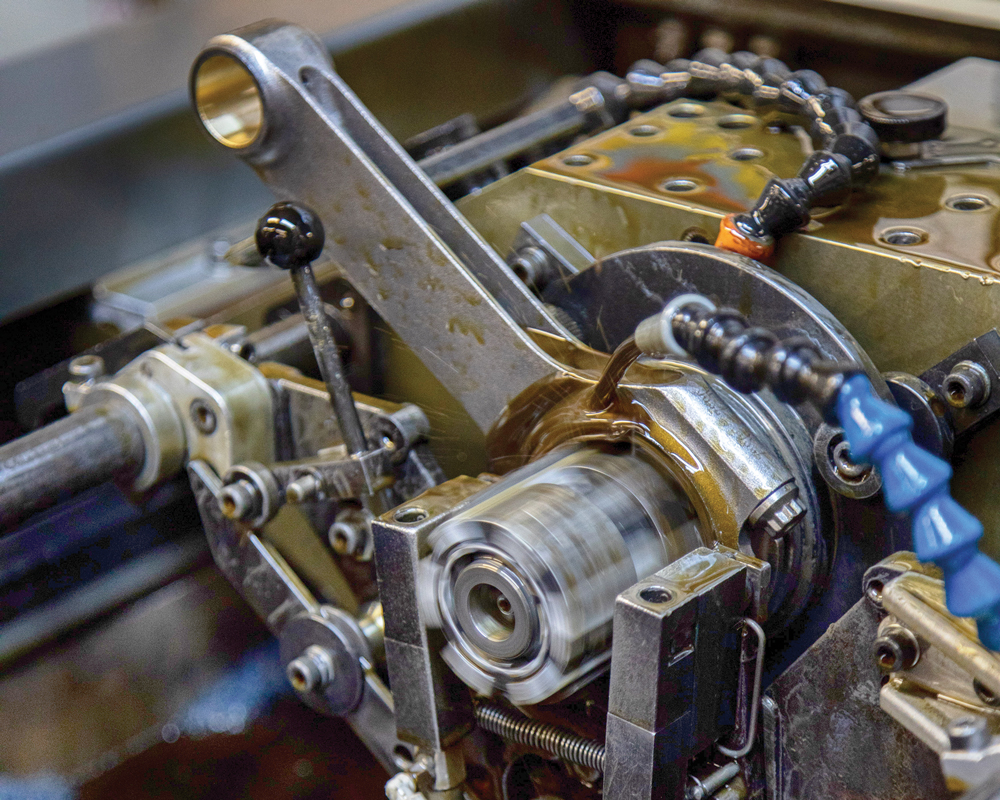
“The most frequently asked question we get is about cam clearance,” agreed Cerny. “A lot of people don’t know about the different base circles of the camshafts. They try to use a standard cam and throw an H-beam in there with a stroker crankshaft. We recommend they run with our stroker clearance rods. That way you don’t worry about getting out a die grinder or spending another $700 on a small base-circle camshaft.”
Installation Tips
Although connecting rods appear quite simple, there is a correct way to install them. To help the DIY engine builder, Scat machines the rod with different-sized chamfers on each side.
“We’ve taken the guesswork out of it,” said Cerny. “On the big end of our rod, one side of it has a very large chamfer where the bearing would sit. The other side has a very small chamfer. Obviously, for us, the large chamfer is what’s going to go toward the counterweight or the throw where the radius is on the rod journal. The small chamfer is where the two rods will face each other.”
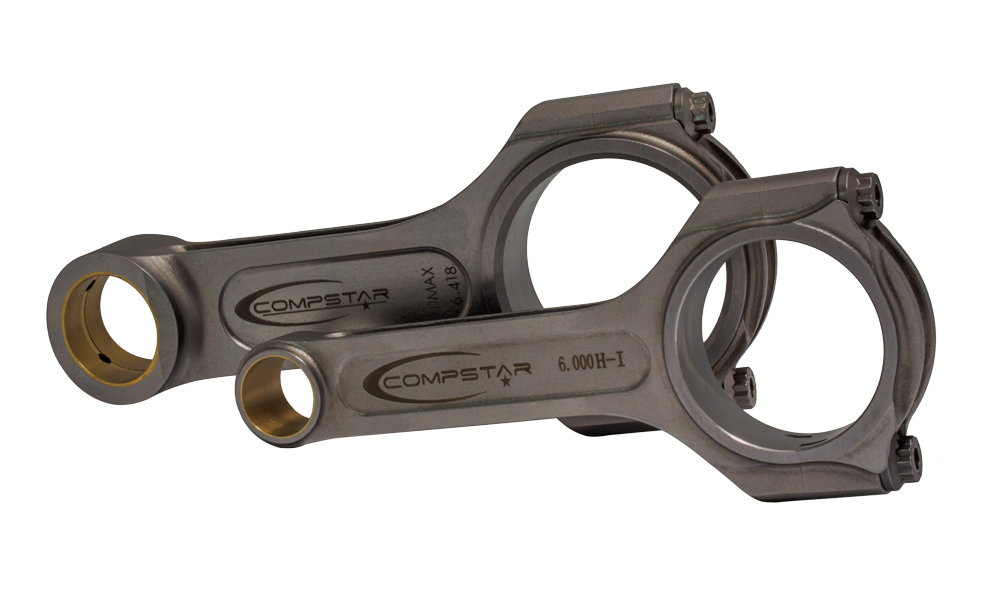
The correct installation also addresses rod offset. Some engines are designed so that the cylinder-bore centerline is slightly offset from the rod-bearing radial centerline. That difference is corrected by offsetting the rod slightly so that the little end is centered on the wrist pin.
“Many times customers will use rods that are not correct for their engine, such as running an SBC rod in a small block Ford, which have different offsets,” explained Batchelor. “That moves the pin end of the rod 0.025-inch toward the pin boss instead of being centered in the piston. This is a common practice due to availability of SBC rods, and in most cases if the rod is built strong enough it will work, as long as they have additional clearance for the small end of the rod in the pin boss.”
Batchelor also had a customer experiencing unusual wear on the pin end of the face and on the opposing big-end face. He asked the engine builder to mock up all the blocks he was using and take some measurements.
“We were able to figure out that making the big-end offset to what it needed to be would have resulted in a weaker design,” said Batchelor. “Instead, we corrected the problem with non-standard offsets of both ends and changing the pin-end width slightly so that both ends of the rod could never contact the piston pin boss and the crank at the same time.”
One design element of connecting rods that often baffles customers is an oil squirter built into the rod. Users often have the misconception that pistons and cylinder walls won’t receive any oil if a squirter isn’t designed into the rod.
“First of all, a hole in the big end of the rod is a fantastic starting point for a fatigue failure crack. You don’t want that,” explained Davis. “Have you ever imagined what even 20 psi of oil pressure flowing past the rods and crank journal surfaces might look like in the bottom of an engine? Not to mention what 40, 50, or 60 psi would look like! Oil is spraying everywhere. The only way everything is not completely soaked in oil in the crankcase is if you don’t have oil in it at all. Nothing will escape this violent oil spray.”
As long as the oil system is working properly, cylinder walls, piston skirts, rings, pins, and other components will receive plenty of oil. The reason many OEM engines, especially imports, have oil squirters and other oil manipulating features is that auto manufacturers have to plan for the worst possible owner when it comes to ignoring routine maintenance, harsh driving conditions and overall misuse of the vehicle.
“It has to be idiot-proof,” concluded Davis. “In the racing and performance enthusiast industry, I guess we expect a bit more out of our customers!”
What is Anadiaplasi?
The unique connecting rod that appears to have been modeled after a twisted jungle vine was actually developed by Spyros Panopoulos Automotive (SPA) using its proprietary method of Design for Additive Manufacturing (DfAM) called “anadiaplasi.”
A native of Athens, Greece, Panopoulos has been designing his own connecting rods since 1999. He soon started manufacturing other performance engine parts like billet heads, turbo compressor wheels and titanium camshafts. About five years ago, he built a 1,788 cc Mitsubishi Evo engine that pulled 2,880 horsepower at 14,100 rpm and pushed the car to a quarter-mile time of 7.704 seconds in Abu Dhabi. Additional innovations include brake and piston designs for Formula 1 and working with “super alloys” for various racing parts.
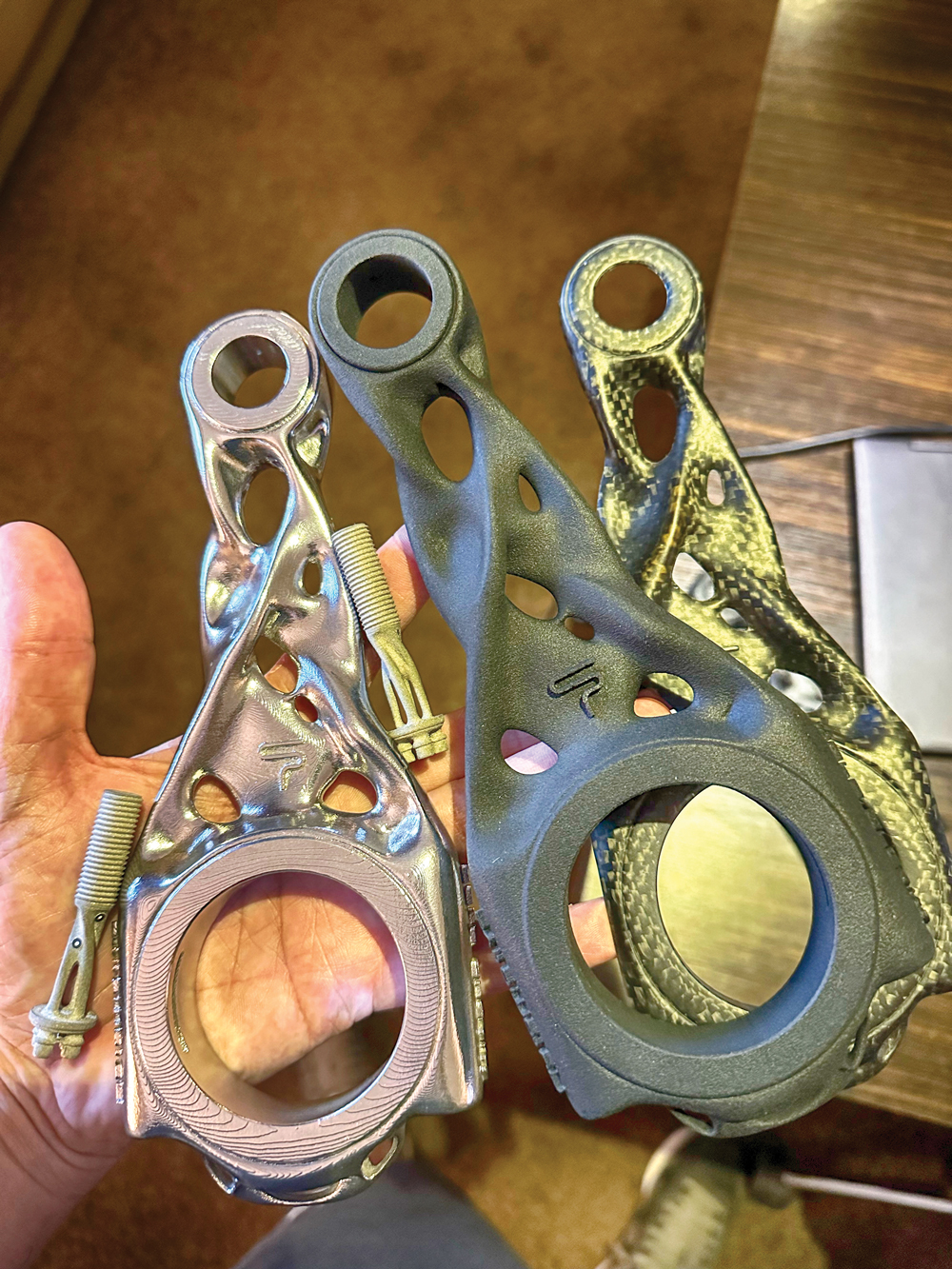
Around 2019, Panopoulos developed anadiaplasi to take advantage of advancements in high-tech 3D metal printing. In theory, the component’s shape is dictated solely by the forces acting on it. Effective designs multiply and evolve while inefficient designs die off in this AI-driven development. The end result is that material is minimized if performance isn’t supported and added where needed to improve performance.
“It’s an algorithm created in-house,” explained Panopoulos, “and based exclusively on 3D printers. The method is based on the strength and properties of materials in relation to the forces exerted on the forms.”
SPA has developed designs for different materials, including carbon, alumina, titanium, and ceramic. Different additive manufacturing methods—including XJet nanoparticle, selective laser melting (SLM), or binder jetting—are used to print the parts. Then any number of surface treatment technologies may follow, including CVD or ALD coatings, ultrasonic nanocrystal surface modification (UNSM), and shot peening.
Panopoulos has created connecting rod designs that may be used in future Formula 1 engines, but current efforts are focused on a 4.0-liter 90-degree DOHC V10 developed for the Chaos hypercar, which is made from more than 44,000 3D-printed parts. SPA will use its 3D technology to manufacture the crankshaft, camshaft, intake valves, exhaust system, and even the magnesium engine block. Twin turbos made from carbon and titanium, and fitted with ceramic compound turbine wheels, will boost the engine to a projected 3,000 hp at 12,200 rpm.
“The engine is on the test phase on the chassis dyno,” confirmed Panopoulos. “We’re testing different materials and designs. But similar parts with the same technology have been tested on the dyno and track since 2018.” —Mike Magda
SOURCES
Callies
CP-Carrillo
Crower Cams & Equipment Co.
Dyer’s Top Rods
Eagle Specialty Products
Howards Cams & Racing Components
Molnar Technologies
Scat Crankshafts
Spyros Panopoulos Automotive