Surface Warfare
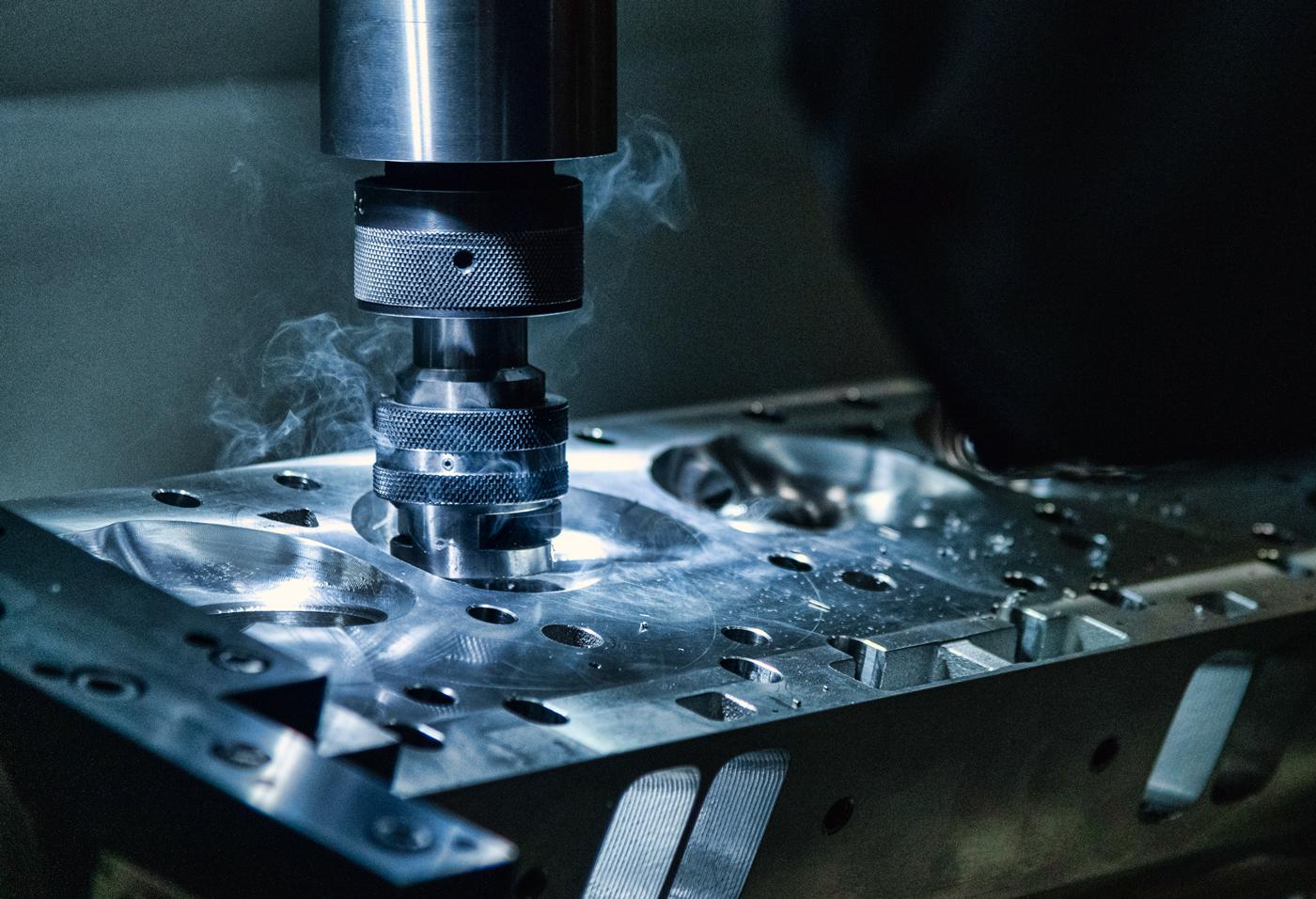
Engine builders want more automation in their shop machines to help counter labor shortages, and they’re keeping a close eye on surface finishes.
For the most part, suppliers of engine-building machinery weathered the pandemic surprisingly well. Sales were consistent, even with staffs working from home, and there were minimal disruptions in production due to COVID-19 absences. All segments of the market kept pace with previous years, including racing and industrial, which gave manufacturers enough breathing room to continue R&D projects and upgrade or develop new equipment.
Evidence of those efforts will be showcased on Machinery Row at the 2021 PRI Show in Indianapolis on December 9–11. There remain a few veils of secrecy this far out from the Show; however, hints of exciting introductions have been shared.
“There will be an all-new B4250 engine block machine, which has an all new frame with a bigger spindle,” said John Cowher of Centroid, Howard, Pennsylvania. “Also, our big machine, the A560XL, will be an all-new machinery frame to debut this year.”
“We’ve got some new product introductions coming up later this fall,” confirmed Bob Davis of Sunnen, St. Louis, Missouri, who added that new graphics and a revised logo will adorn the company’s products. “We are a couple years away from our 100th anniversary, so we decided it was time to freshen things up a little bit. And by the Show, we’ll have e-commerce available to our customers on the website.”
“We’ll have a nice lineup of machines,” added David Bianchi of Rottler, Kent, Washington. “We’ll also have a surprise and a few tricks up our sleeve.”
Growing Sales
One begs to fully explain the relatively steady bottom line and even an occasional sales record for the machine industry during the past 18 months. There is certainly noticeable consolidation and shrinking of the engine rebuilding market for both commercial and racing operations. Those surviving shops are picking up the slack and staying very busy, and that includes buying equipment to fulfill needs that previously had been sourced out.
“I had the busiest year-and-a-half ever. Everybody is busy. People are wanting to do their own stuff,” noted Russ Tierney of RT Sales, Highland, Michigan. “Lately, it may take a month or better to get parts back because every shop is overwhelmed. So guys are buying their own machines so they can control the quality.”
“I’ve worked for the company since 1979, so speaking with some history behind me, I can say we had the best year we’ve ever had,” agreed Jeff Murchison of Hopper Equipment & Supply, Upland, California. “I really think that in all categories where there’s general engine building and performance, there’s more money being spent, whether that’s fixing up old cars or racing hot rods.”
Another segment that’s keeping engine shops very busy is the diesel market. Most racers have diesel trucks to tow their vehicle to the track, and performance diesel work is also on the upswing.
“We’ve done very well,” said Tammy Baker of Joe Baker Equipment Sales, Cincinnati, Ohio. “A lot of diesel work has picked up. The race shops just keep doing what they do.”
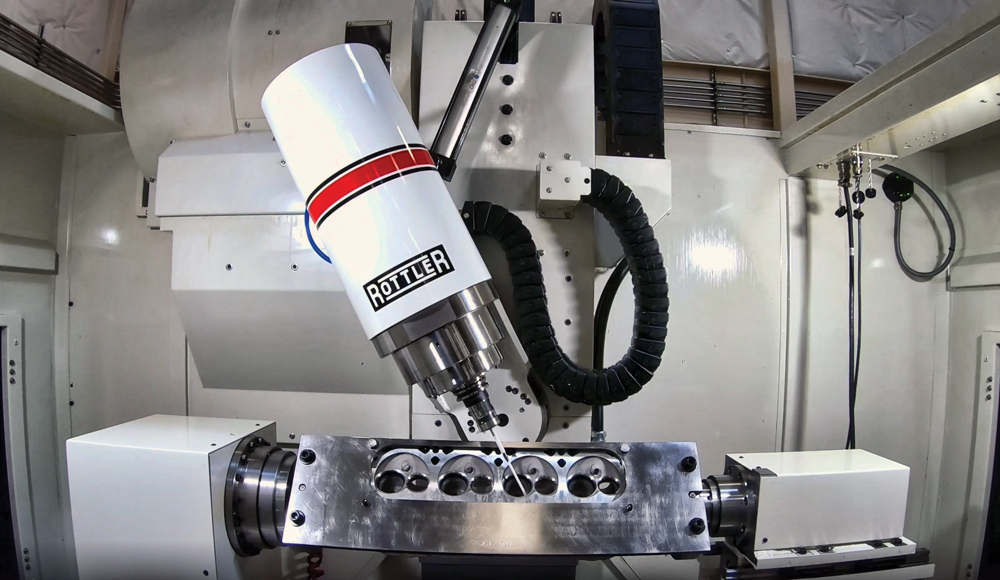
Reviewing some of the jobs performed by leading engine shops, Centroid has noticed an uptick in modifying OEM superchargers and how that equipment meets the challenges of working within tight confines. “I’ve been doing a lot of programming, specifically with porting superchargers,” said the company’s Andrew Jenkins. “You can gain a lot of horsepower by porting out a stock supercharger, also intake manifolds and blower snouts. It’s very difficult to do some of those engines because of the geometry. It’s not your normal port shape. Long tooling is needed because you can’t always cut all of it from the open face of the supercharger. Sometimes you have to come at it from the back, which can mean tooling in excess of 18 inches.”
The company has also observed a growing need to machine billet parts and modify turbochargers with all the attention that boost is getting at the track.
“The biggest thing with COVID is that people can’t get parts, so they’re looking for ways to bring matters in-house,” added Jenkins. “That’s what has brought on some of these billet projects. They want to be able to make the parts themselves so they’re not relying on other manufacturers. Also, some of our customers are porting turbocharger housings.”
With more emphasis on sealing the engine and keeping combustion pressures inside the cylinder, there’s also a need to deliver surface finishes to exact specifications. Advanced CBN (Cubic Boron Nitride) and PCD (Polycrystalline Diamond) cutting tools have allowed manufacturers to develop more sophisticated machines that can deliver exact finishes.
“Whether it’s the top of the block or inside a port, we have some neat stuff going on there,” reported Rottler’s Bianchi. “We have some new advancements, proprietary things that we’re not ready to launch. They’re about six to eight months out.”
“It’s up to the gasket manufacturer to set the standard,” noted RT Sales’ Tierney. “Just like cylinder honing. It’s not Sunnen that tells you what the finish should be. It’s the ring manufacturer. You need to have a profilometer. The old guys can run their fingernail across the finish and tell you what it is, but a profilometer gives you an exact number.”
More engine shops are transitioning to diamond honing stones to achieve the desired cylinder surface finish.
“Diamond is pretty much the way to go now,” said Davis. “It’s typically faster cutting, and it lasts longer with fewer change-overs. They’re more expensive to buy, but it all evens out because they last longer, and you’re not shutting down the machine to change stones as often. There’s more total uptime.”
Sunnen is also working with Applied Nano Surfaces, a company out of Sweden that has developed a surface solution that can be applied with a honing machine. “Instead of using stones, it uses ‘ledges’ and applies a solution to the cylinder walls,” explained Davis. “It’s not really a surface treatment, it actually changes the composition of the cylinder walls. It makes them extremely durable and reduces friction.”
Personnel Shortage
If there’s a single critical issue facing both manufacturers and users of engine machinery, it’s the shortage of qualified operators. There isn’t enough new talent entering the industry to replace the experienced machinists as they retire. Graduates of trade schools often have multiple offers from aerospace, manufacturing, and medical industries in addition to automotive. Most engine shops will train new workers, and machinery suppliers have extensive training programs to offer. The challenge is finding enthusiasts who want to learn and stay with a shop.
“Guys are buying machines to do stuff themselves so they’re in control of the quality, but it all comes back to having a guy run the machine,” said Tierney. “A lot of places would like an automated piece of equipment, but you can only automate the precision to a certain level,” which may not be up to what a performance shop would want to get.
“I would say most of my customers are struggling to find qualified help,” confirmed Darren Davis of Millennium Machinery, South Bend, Indiana, a dealer for Citizen Swiss and Miyano machines. “They’re all stealing people out of the same pool of guys. We’ve been running training programs for new operators and bringing people up the best we can. We also built a couple machines that people put robots on to try and fully automate them.
“Almost all of our machines come with a bar loader,” he added, “so they’re made to run unattended. We’re planning on bringing a Citizen Swiss CNC lathe with a bar feeder to the PRI Show. A lot of people from the last Show didn’t understand how the bar feeder was integrated into the system.”
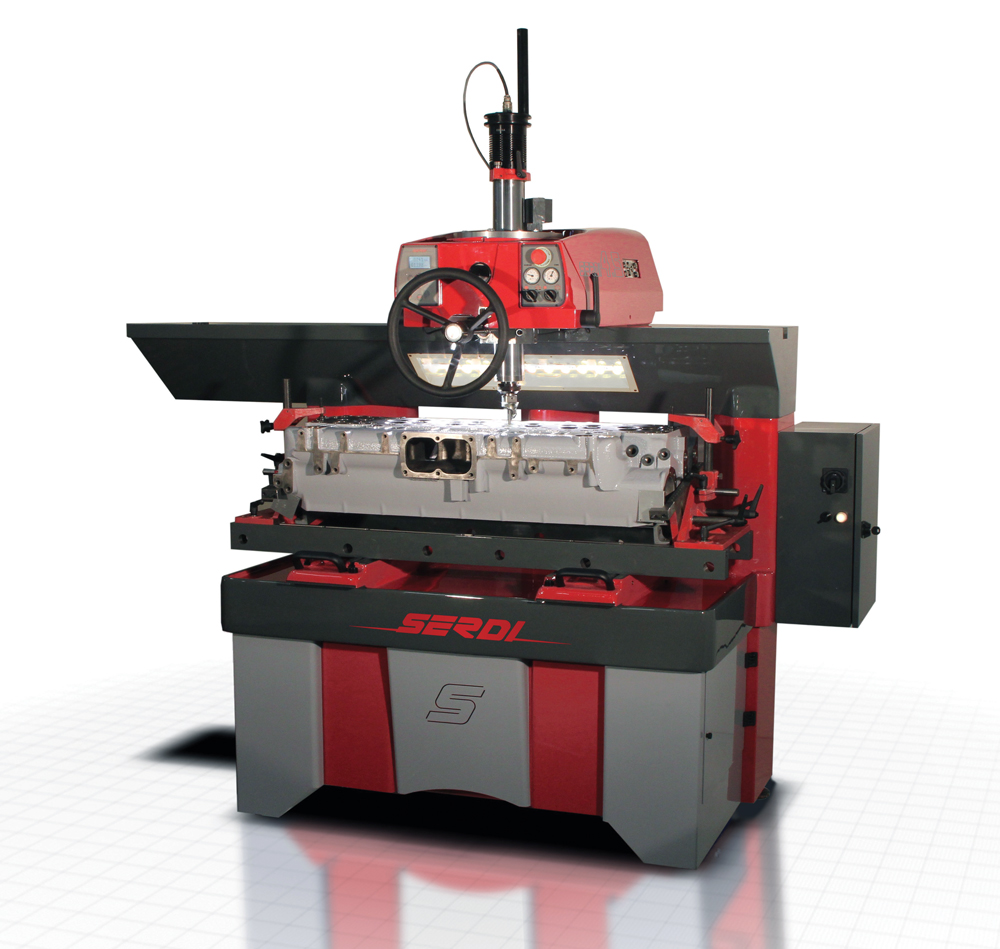
Some suppliers acknowledged that a market still exists for manual machines. “They’re a little afraid of CNC,” noted Baker. “They still like the hands-on.”
Others say more engine shops—even longtime operations—are asking for advanced computer-controlled equipment.
“I’ve got two big CNC machines going to a man who’s almost 70 years old,” Murchison said. “If I didn’t have the Rottler software, I probably would have tried to steer him away from it, unless he was going to hire someone to run it. But I’m going to train him, and I know he’ll adapt to it and make it work.”
The shift toward more automation will continue, according to industry observers, simply because of the labor shortage and the potential to increase production in large shops that grow when smaller ones close as the owners retire. Bianchi cited the difference between Rottler’s H85A and H85AX honing machines. The latter is automated, and the user can leave it unattended while all the cylinders on one bank of a V-style block are honed.
“The mix of A to AX, especially in the performance market, has significantly shifted to the AX,” said Bianchi. “It’s almost turned to where the performance guys are buying AXs, or even beyond with the AXY that can do the whole block. We’re definitely seeing more automation, also with boring machines, surfacers, and cylinder-head equipment. Our CNC porting machine sales are double from a year ago.”
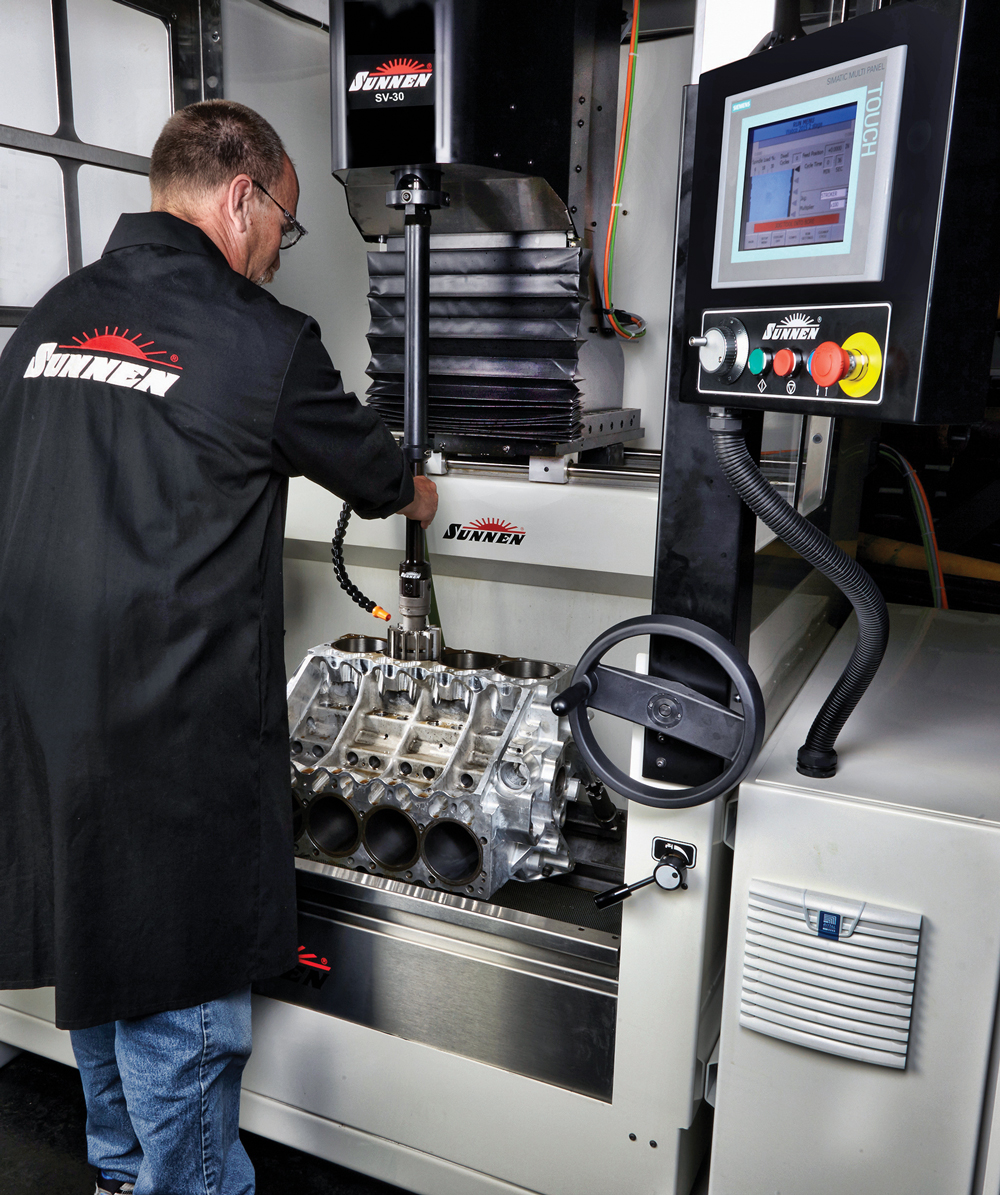
One of Centroid’s clients recently lost six employees due to a number of factors, including childcare costs and COVID issues. While automation is a concern, if not a priority, for customers, an employee remains necessary to an engine shop’s operation.
“You still need that human being to get that part into the fixture and ready to go,” advised Cowher. “If the customer can get it in the fixture and call the right program, then you’re good to go [with automation]. But you need several different classes of these operators. There’s an operator, and then there are guys who can design and manipulate ports with the software.
“What I see is the older guys retiring, and the younger guys are stepping up to the plate and buying modern CNC machines,” he added. “They want to be able to do it all, and they want to do it automatically and with precision. So, we have to up our game a little bit and start teaching them how to do CAD work to make those parts.”
Over at Sunnen, one of the strategies is to help the less experienced workers with an easier user interface. “A lot of the older workers are retiring,” said Davis. “The new people coming up may not have that hands-on experience. Our machines are made with computer controls that remove a lot of the guesswork. There used to be a lot more touch and feel involved with such things as surface finish, crosshatch angle, and things like that. There was a lot of manual intervention, like measuring the finish bore with a dial-bore gauge. Now, we can program that all into the honing machine ahead of time, and it will hit ‘stop’ right on the money every time with the exact crosshatch pattern, the exact bore size, exact surface finish you want.”
Many of the experienced workers who are retiring were also adept at fixing machines. Now some of the manufacturers are offering online diagnostics and repair instructions.
“The shop can get somebody at the factory to figure out the problem, whether it’s mechanical, electrical, or operational,” said Murchison. “It can be worked out pretty quick, and it takes a load off my back.”
One possible conflict that challenges some engine builders is the choice between a machine that is versatile and can perform multiple jobs or a dedicated machine that focuses on one task.
“In the case of Comec machines, particularly the boring mill, the competitive CNC machining centers are essentially industrial machine tools that have been optimized for the automotive market,” said Kevin Hartley of Comec, Mooresville, North Carolina. “Whereas the Comec CNC boring mill is actually designed as an automotive machine from the beginning and dedicated only to automotive operations. It’s a very simplified CNC control, so it can be sold for less than a comparable large industrial-based automotive CNC machine.”
Serdi, also in Mooresville, North Carolina, offers the S3.5 valve seat and guide machine that is popular with many automotive operations while the larger S4.5 can handle both small heads and the large diesel cylinder heads as well. Race shops, however, are drawn to the STroniK line of CNC machines.
“The STroniK allows the operator to design his own valve seat profile,” noted Hartley. “That’s important for a race shop that does a lot of development work and must be able to make modifications to the valve seat profile. Because it uses a single-point cutting tool, it engages only a small amount of material at any time, eliminating chatter on hard seat materials and improving accuracy.”
Bottom line: The automotive machine industry is eager to show off new equipment and help customers solve their labor issues, whether that’s with training or more automated equipment. Racers will benefit with new technologies that provide increased precision and productivity, regardless of a shop’s size. Just a sampling of the catalogs shows that there is a machine for every task and budget.
“And you can build with some of these machines, too,” said Murchison. “You don’t have to buy it all at once. You can add to it when the time is right.”
“Yeah, we’re coming to PRI with new equipment because I think it’s time,” concluded Bianchi. “The industry, as a whole, we’re all getting back together.”
SOURCES
–
Air Turbine Tools
airturbinetools.com
Bend-Tech
bend-tech.com
Centroid
centroidcnc.com
Comec
comecus.com
CWT Industries
cwtindustries.com
Dynapack
dynapack.com
Fytron Software
fytronsoftware.com
Giant Finishing
giantfinishing.com
Hopper Equipment & Supply
hopper-shop.com
Joe Baker Equipment Sales
joebakerequipsales.com
Lincoln Electric
lincolnelectric.com
Magido
magidousa.com
Millennium Machinery
millenniummachinery.com
Miller Electric
millerwelds.com
Pit Weld U
visitpit.com
Robins Machines
robinsmachines.com
Rottler Manufacturing
rottlermfg.com
RT Sales
rtsalesinc.com
Serdi
serdimachines.com
Shaviv USA
vargususa.com
Strong Hand Tools
stronghandtools.com
Sunnen
sunnen.com
Swift-Cut Automation USA
swift-cut.com
Ultrasonic LLC
ultrasonicllc.com