BALANCING PRIORITIES
While budget-priced performance connecting rods are common throughout the industry, many motorsports manufacturers are now focusing on high-horsepower or endurance applications that require additional strength and versatility.
In what universe would connecting rod manufacturers concede that their products could be used as some de facto rev-limiting device?
Well, that’s the justification a leading manufacturer was told when one of his engine builders questioned a Midwest sanctioning body as to why I-beam connecting rods were required in the engines for a certain class. The engine builder suggested H-beam rods were more readily available and easier on the pocketbook.
“Everyone knows that you cannot turn an I-beam as high an rpm as you can an H-beam, so this will limit what people do with their engines,” reportedly was the sanctioning body’s response. The engine builder quickly reminded the official that a 7,200-rpm chip was already required in the ignition box.
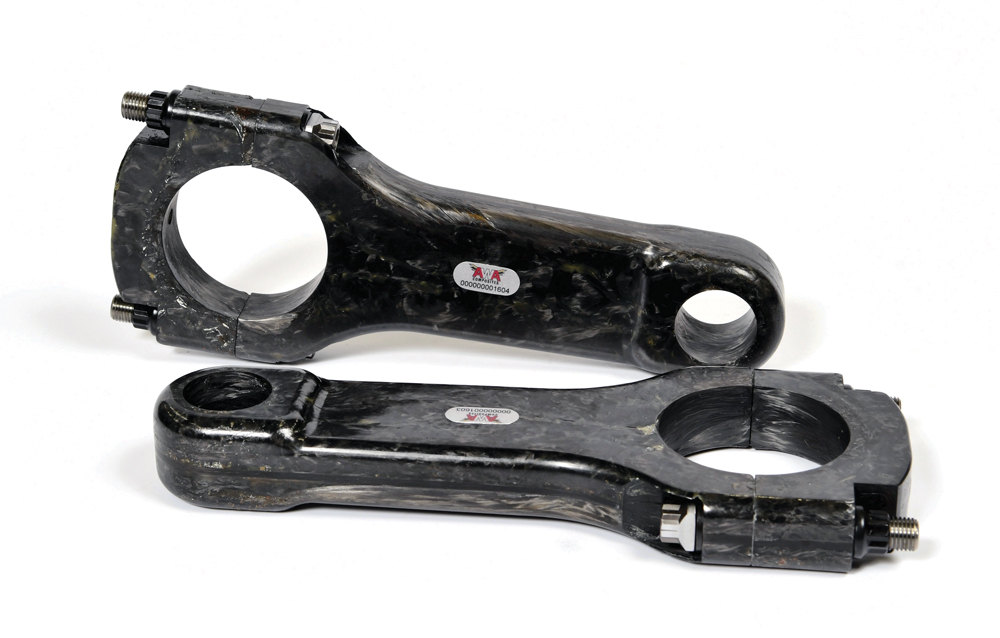
“I just shake my head sometimes when these guys come out with rules that they intend to save everybody money, when all it does is end up costing people more money,” said Tom Molnar of Molnar Technologies, Kentwood, Michigan.
Making this rule even more absurd is the realization that leading connecting-rod manufacturers are at the top of their game right now—and I-beam vs. H-beam is no longer a contentious and divisive feud between racers or manufacturers. There is a wide variety of models available to cover power levels for all racing venues. Behind significant computer and lab investments from their R&D efforts, companies have accurate data and simulation intelligence to supplement years of their own experience and customer feedback in building the proper connecting rod for specific racing applications—regardless of the preferred design. Balancing the priorities between strength, weight, and cost remains the critical challenge for the aftermarket.
“Engine builders are not looking for an anvil with two holes,” observed Gabriel Casella of Saenz Performance in Miami, Florida.
MARKET MOVERS
In addition to the current vitality among manufacturers, the connecting rod market may soon witness the working arrival of a disruptive technology that was first previewed at the PRI Trade Show two years ago. That’s when AWA Composites of Rolling Hills Estates, California, introduced its Sheet Matrix Composite, a fiber-woven composite with a proprietary weaving technique. Designed for Top Fuel engines, this connecting rod is half the weight of a conventional aluminum rod, yet is projected by company engineers to last an entire season instead of just 12 to 15 races. It has gone through a few changes since its debut.
“Now, by reason of our new design, we are in the final stages of getting some conclusive figures on those,” said Bryan Gill. “We have gone through alcohol testing. We have gone through Spintron testing. We have done forms of post-testing and material FEA. Now we are in engine testing.”
AWA is adapting this new composite to an OEM application as well as other race-engine components. The company expects to display pushrods, pistons, and wrist pins at this year’s PRI Show in December. But don’t hope for entry-level models or budget pricing.
“We wanted to show proof of concept of being able to master the tremendous cylinder pressures that are created by a nitromethane engine. Once we’re able to master that cylinder pressure requirement, everything else falls by the wayside to that,” Gill added. “We understand that composites are usually, in the grand scheme of things in the automotive industry, always on the premium end of anything. So, we are at the end of the ultra-premium market, and we do not really intend to offer what we call a budget composite rod.”
If AWA’s rod can last an entire season, then there will be an argument for saving money. “Cost versus benefit, I think that we are one of the better choices out there,” claimed Gill.
Auto Verdi in Soderbarke, Sweden, is another manufacturer that specializes in high-end connecting rods by focusing on NHRA Pro Stock, and officials don’t foresee expanding the line to other racing disciplines, unless a business case can be made.
“Everything is custom made. We work straight to the customer’s requirements,” explained Stefan Verdi, noting that most of the rods are an H-beam design. “We work with a couple of different materials. The up-level material is for Pro Stock. They’re looking for durability and rods that can withstand 80 to 100 runs.”
Auto Verdi does stock a small inventory for popular Saab and Audi applications, but other than Pro Stock the customer base is limited to a few diesel and land speed engines. Even though Auto Verdi has close ties with NASCAR and circle track engine builders via its oil-pump products, those markets are not candidates for connecting rods.
“That would entail a considerable machining investment,” said Verdi. “If we start producing and then they quit on us, we will have a problem.”
Most manufacturers offer a range of connecting rods to suit different applications and horsepower levels. But even some of those companies are rethinking their budget series.
“We’re going to be discontinuing our Sportsman line,” said Shane Pulido of Crower Cams, San Diego, California. “Either today’s customer wants a really good rod, or they’ll go offshore—and we can’t compete with those in a budget line. Everything we offer is made in the US with US steel.”
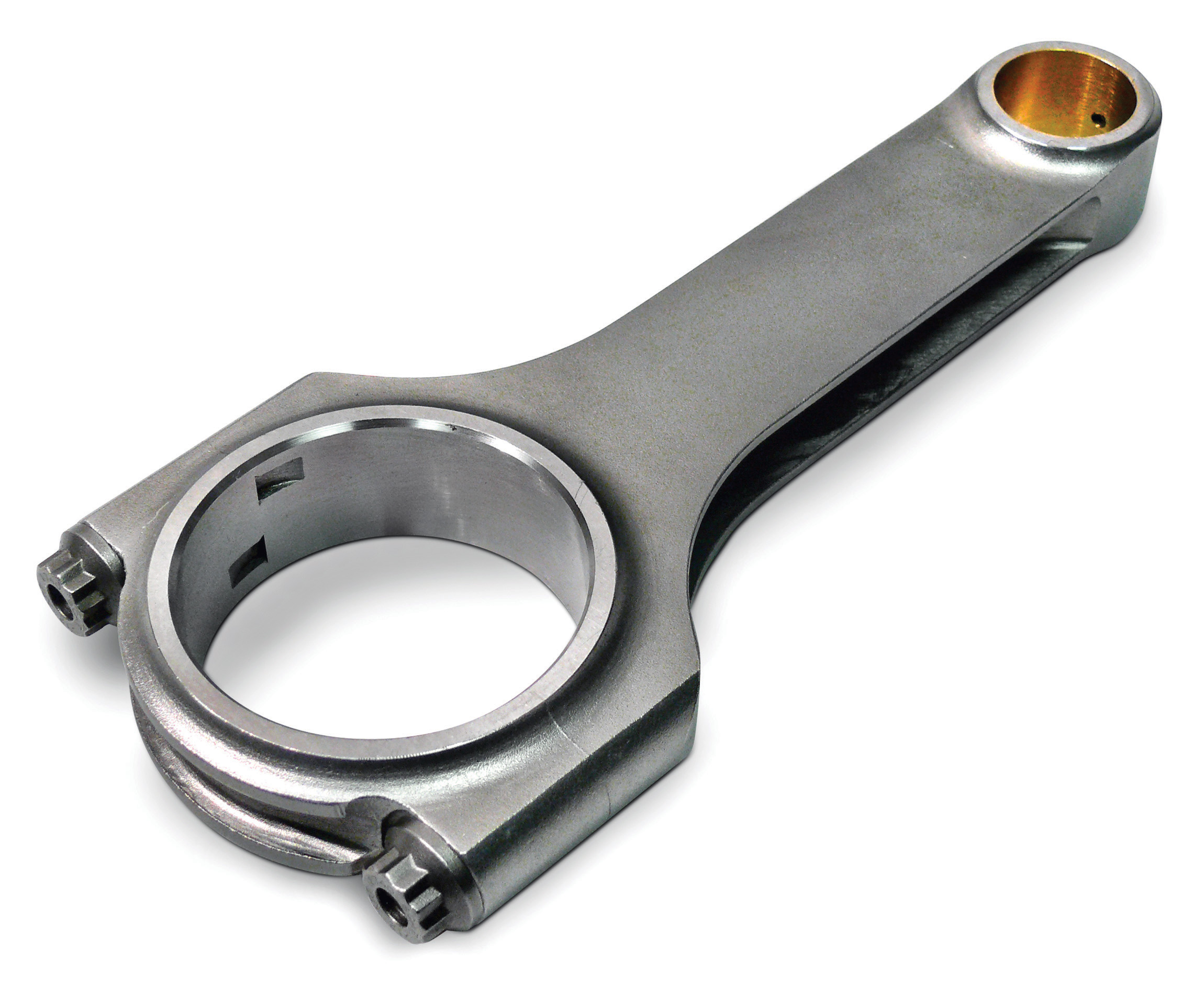
Crower has long focused on I-beam designs from billet steel, and one of its most popular lines is a tapered RBT (radial beam technology) Maxi-Light that removes excess material from non-critical stress areas. For popular applications, this rod is offered in a variety of weight and bolt configurations to suit the rpm, horsepower level, type of racing, and whether boost is involved. For example, in a small block Chevy the lightest Series 1 rod weighs 495 grams and comes with a 3/8 bolt for horsepower levels up to 550 on the drag strip. The Series 5 rod weighs 645 grams, comes with a 7/16-inch bolt, and is built for 1,000-plus engines at the strip.
“For Series 6, we design those just for horsepower, rpm, and how much boost are running,” said Pulido, adding that the engineers evaluate the stroke, piston weight and piston speed at various crankshaft angles. “We can see the force at those points and rpm, and then we overbuild the rod by a long shot—because everybody wants to put it on the ragged edge and go for broke.”
Crower also has tips for inspecting rods between teardowns. “Looking at the bushing end to see if it’s squished out on the bottom from detonation. Also, your bearing’s going to tell everything, as far as how it’s wearing. If it’s wearing on the top end, then you have a detonation issue. If it’s wearing on the other end, you’re over-revving it,” said Pulido.
Catering directly to the customers’ specific needs is a common theme among manufacturers. K1 Technologies in Mentor, Ohio, focuses on H-beam designs. Instead of offering good-better-best choices, K1 tries to match the rod to the engine requirements.
“For certain applications, like small block Chevrolet, you have a lot of circle track people looking for a lightweight option,” explained Mike Skeen. “Whereas more of the drag race community is looking for a standard weight or a heavy-duty H-beam. The hardware stays consistently the same—it’s all ARP2000.”
Providing a package deal motivates Scat Enterprises in Redondo Beach, California, to offer a variety of connecting rod models. “The reason we have so many different rods is because we have the crankshafts to match them,” said Tom Lieb. “For instance, you’ve got a cast crank, and there’s no reason to buy an expensive H-beam rod. It’s just overkill on the pocketbook, but also the application.”
Scat’s strategy is to match up the crank, rods, pistons, rings, and bearings, then balance the unit so it’s ready for assembly. “We’ve gone step by step by step to match the application to the pocketbook. That’s about as simple as it gets,” added Lieb.
Again, Scat works with customers to determine the appropriate package. Street-rod and Super Stock dirt track engines might both dyno out at 500 peak horsepower, but the stress and durability requirements are quite different—and therefore the engine is set up differently.
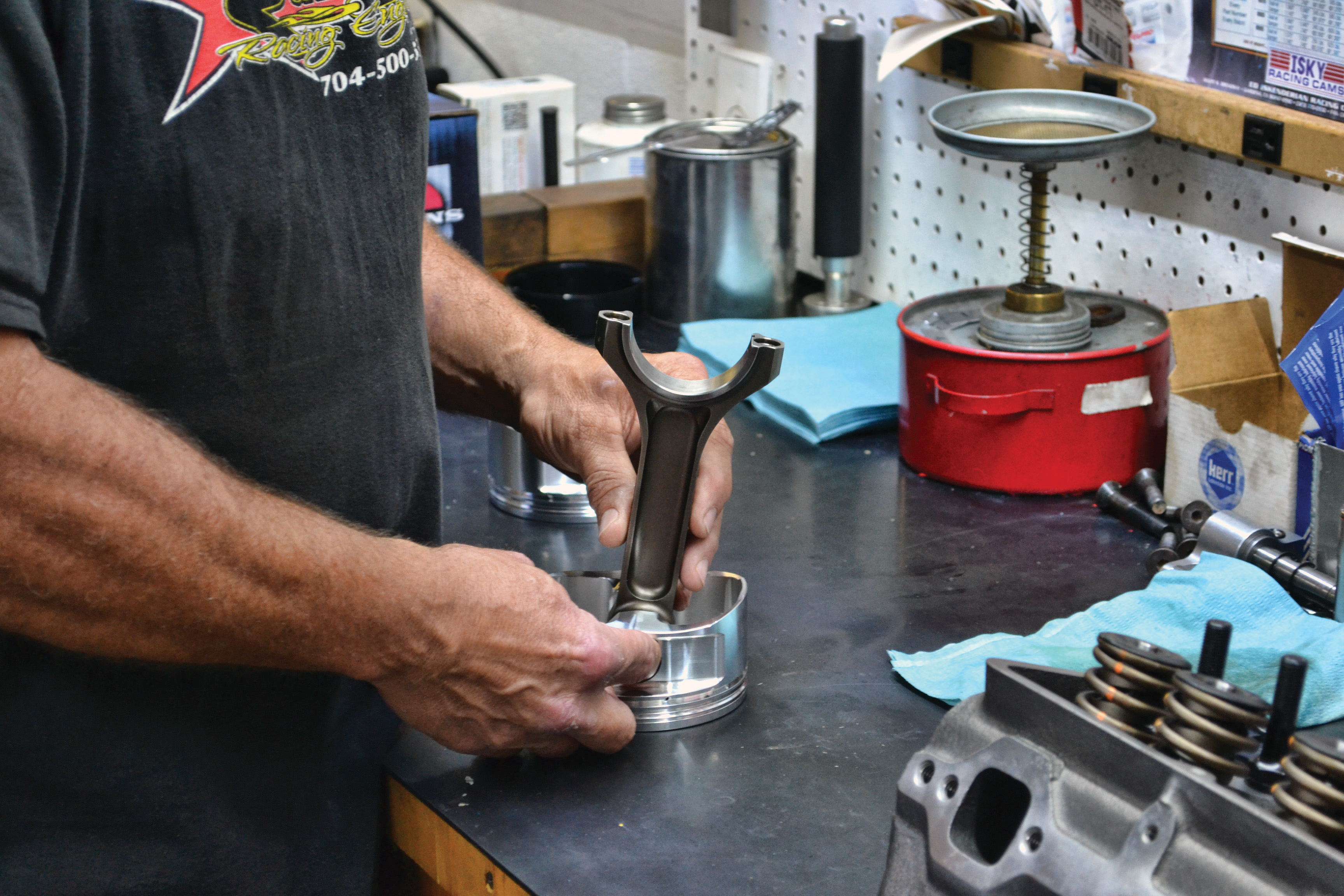
“You look at piston speed, which is based on the stroke,” said Lieb. “That will break a rod, and it has nothing to do with horsepower. Yes, we do have to do things with horsepower in mind, but it’s more piston speed, weight of the components, and the rpm you’re running.”
One of Scat’s premium rods is the Ultra HP Stroker, where the design game plan moved mass where it was needed to improve strength, then pockets were cut where strength wasn’t needed to lighten the overall weight.
“If you look at an I-beam, there’s no material there. But on an H-beam, because of the way we machine the rib, the cutter has a radius and leaves a triangular cavity in that section,” explained Lieb. “It has absolutely no effect on the rod’s strength.”
As racers educate themselves more in the deep technology of the sport, offering the customer a choice of steel materials provides another selling point. The most popular alloys are 4340, 4330 and 300M—although few companies will work with all three, and some partner with suppliers to develop a proprietary alloy.
“A lot depends on the application, and depending if it’s off the shelf,” said Julio Conception of Saenz Performance. “The 4340 tends to be a little bit heavier than 300M. Let’s say you want 1,200 horsepower—a 4340 rod would be a heavier rod than a 300M rod capable of holding 1,200 horsepower, but the 300M would be more expensive.”
Saenz offers both I- and H-beam, but focuses on I-beam in its Performance Series, while the budget-minded S-series is all H-beam. Most of the applications cover import engines, yet the company is expanding into the domestic market.
“Every customer is different, so we like to get in the conversation to know their application. Not only do we ask what you’re doing now, but how much horsepower are you looking to make in the future,” said Conception, who added that drag racers make up the better part of the company’s customer base, although midget racers using four-cylinder engines are a growing market. “Our first domestic rod is a 6.125-inch LS, and now we came out with the Ford 4.6-inch in the Performance series.”
Earning a strong reputation with dirt track engine builders has helped Dyer’s Top Rods in Forrest, Illinois, categorize its line of connecting rods to suit very specific engine-builder needs. “We also make rods for the off-road and LS markets,” said Roger Friedman. “And then we have Australian accounts for their sprint cars. We only make connecting rods.”
The product lineup is basically broken down by weight into different levels or series. For example, the H-series is the heaviest, while the XL-series is extra light—but there’s also ultra light and super light series. The rods are mostly standard H-beam or a tapered beam.
“After 20 years, we pretty much know what our customers are asking for. The range of lengths and weights is determined by the horsepower, rpm levels, and piston weight,” said Friedman.
Off-the-shelf rods are not fitted with hardware until all the customer requirements are noted. Then the big end can be finish-honed, as needed.
“We don’t have a lot of cookie-cutter stuff on the shelf,” added Friedman, noting that all Dyer’s rods are constructed from 300M steel. “It’s expensive material, but I believe it’s one of the strongest materials out there when the heat-treat is correct.”
Dyer’s originally machined its rods out of billet but finds the new forgings stronger. “A forging will give you grain structure around the big and little ends,” said Friedman.
Molnar Technologies offers a variety of rod weights and lengths for popular applications, mostly in H-beam and constructed from 4340 steel alloy. For the small block Chevy, there’s a standard rod, mid-weight, and light-weight.
“Then we have our PWR ADR and PWR ADR Plus rods,” said Molnar. “The Plus rods are for the extreme guys—the spray and boosted engines when they start getting into the 35- and 40-pound boost ranges. We use proprietary ARP2000 bolts for everything.”
Molnar also manufactures a lightweight I-beam rod for circle track SBC engines and NHRA-approved Stock replacements.
“We take everything on an individual basis. We do not rate by horsepower because, quite honestly, nobody ever broke a connecting rod or a crankshaft due to horsepower,” said Molnar. “Horsepower does not break rods.”
Rod manufacturers are sometimes limited by rules—and not the farcical type that think a rod design is by nature a rev limiter. There are often weight restrictions, and certainly some organizations have outlawed exotic materials. The minimum weights required by some sanctioning bodies are intended to keep costs down. Still, lighter isn’t always better.
“It depends on the application. There are some lightweight rods that should not be in certain applications. Our lightweight late-model rods are made for a small four-barrel or a two-barrel application. You would not want to run that rod in a 410 sprint car. Everybody wants everything light, light, light, but there are limits,” said Molnar. “Five-hundred-gram rods are just not going to live in some of those applications, which is why we do not put horsepower ratings on them. We try and take each into each engine build on an individual basis, and try and help people get the right parts for their application.”
On the other side of the fence, Engine Pro in Wheat Ridge, Colorado, manufactures its line of rods from one-piece forgings that are initially produced offshore. “Then we finish machine them in Kansas City,” said Jesse Jones. “I like the idea of a single-piece forging, because it’s the same material, same circumstances for both pieces.”
All of the Engine Pro connecting rods are H-beam style forged from 4340 alloy. The customer has a choice between three ARP fasteners: 8740 chromoly, ARP 2000, or L19. Engine Pro suggests maximum horsepower levels based on the fastener selection, ranging from 700 up to 1,500 depending on the application.
Engine Pro also offers a lightened version of the H-beam for LS engines with ARP 2000 as standard bolts. Final weight comes in at 615 grams.
“Our goal was to make it the same weight as the OEM to replace the powdered metal rods,” added Jones. “Essentially, it’s the same construction as all the other H-beam rods, but thinned out in some areas where we can get away with it.”
Eagle Specialty Products in Southaven, Mississippi, offers products for a wide variety of applications for a diverse range of end users.
“Our rod lineup covers any form of grassroots and semi-professional racing,” said Alan Davis. “The only limitations would be custom or unique applications. Our strength is in our large-scale production. This drives the price down—not shortcuts in quality or material.
The entry-level SIR rod is forged from 5140 steel and designed for rebuilds, although some racers will use them in claimer applications. Next step up is the FSI I-beam made from 4340 steel followed by the top-of-the-line CRS 4340 H-beam rod. Both rods have bolt options.
“The H-beam rods are forged in two pieces,” noted Davis. “The cap is forged separately from the beam. This allows the grain flow of the rod cap to follow the stress lines. This feature would be impossible if the rods are forged as one piece and separated later.”
Eagle also offers an option called “Extreme Duty” in response to high-boost applications in the sport-compact market. “Most of these engines were making more than 260 horsepower per cylinder (1040 hp total). We start with the same H-beam rod and polish the entire rod to smooth out any microscopic pits or inclusions, which are starting points for fatigue failure,” explained Davis. “We then install the ARP Custom Age 625+ bolt, which have roughly a 27% higher tensile strength. The much higher clamping load helps keep the big end bore stable under extreme conditions, hence the name ‘Extreme Duty.’ We haven’t established a power rating on these yet.”
Eagle will introduce its fourth generation connecting rod in the near future. “I can’t tell you much more than that, but just like Eagle changed the performance landscape over two decades ago with our 3D rod, the 4D rod will do it again,” said Davis.
One of the companies touting I-beam construction is Callies, although it does offer limited applications in H-beam—starting with the value-added Compstar series. It’s forged and machined offshore, then sent to the US for finishing.
“We bring them here and do all the critical dimensions in our machines,” said Brook Piper of the Fostoria, Ohio-based company. “Then we go to our Ultra lineup, where we have an H-beam, but it’s for the high-volume applications only. The H-beam is a little easier to make than the I-beam. So, we can keep some costs out of it. So, the guy on the fence that really should use a better rod, then he could get into our H-beam instead of buying something from overseas.”
Callies uses 300M steel on all the Ultra rods. It also offers an Ultra XD that is designed for additional rod-to-cam clearance with stroker crankshafts. The company’s top-of-line offering is the Enforcer series.
“The Enforcer is for monster power-adder guys, whether it’s nitrous or boosted,” said Piper. “These are our I-beams on steroids—thickened up a little bit and heavy.”
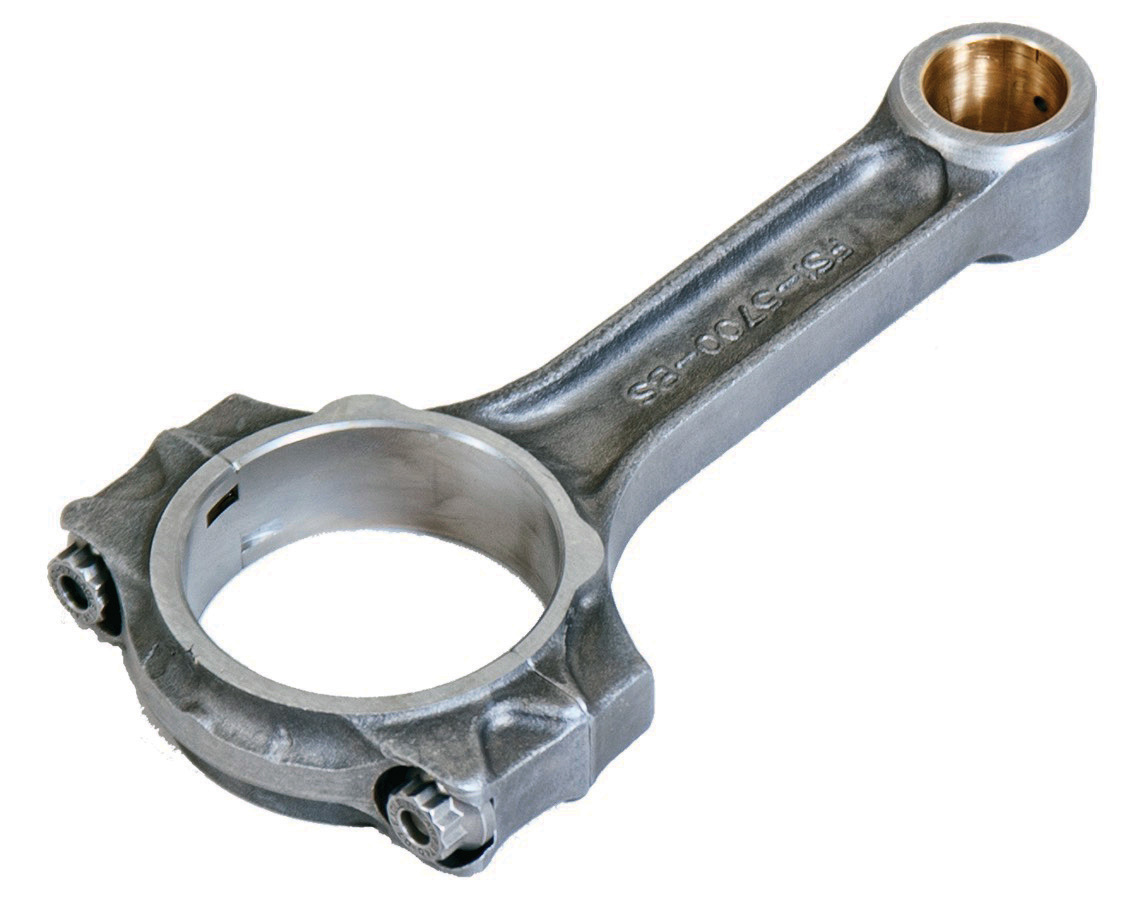
For circle track racers, Callies offers a lightweight version of the Ultra I-beam, but also caters to traditional H-beam racers. “We have been trying for years to educate them that the I-beam is stronger. But it is one of those handed-down things that they all believe in—H-beam is where you need to be in the circle track,” explained Piper. “So, we actually came up with the Ultra Dirt Series now.”
The Ultra Dirt is a lightweight H-beam design for small block Chevy that is available in three lengths with Honda-sized journals or the standard 2.000-inch journal.
BEYOND H-BEAM AND I-BEAM
One way a manufacturer can help distinguish itself from the H-beam vs. I-beam debate is to come up with a new beam design. In addition to a traditional H-beam, CP-Carrillo of Irvine, California, offers an A-beam in its marketing plan. And Lunati has a new X-beam rod for the market.
“The A-beam is a lightweight I-beam style rod,” explained Richard Batchelor of CP-Carrillo. “It’s designed for lower horsepower, naturally aspirated engines. The Super A is a little beefier I-beam style designed for mild boost.”
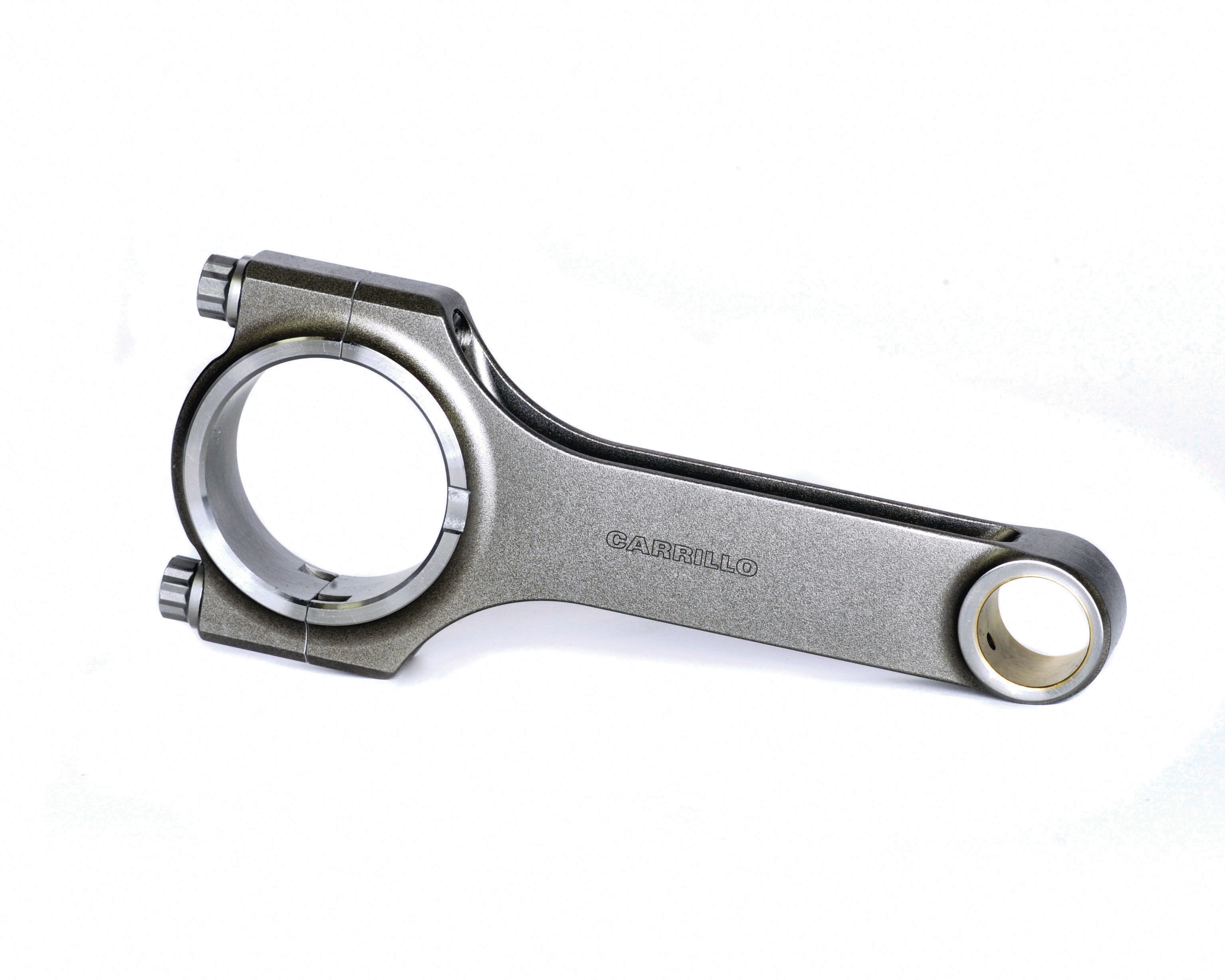
CP-Carrillo’s H-beam rods are constructed from a proprietary 4330 steel alloy, and may also be ordered in a tapered design. The company also offers a line of rods designed to meet NHRA requirements for Stock Eliminator replacement, and there’s an aluminum rod line for select applications, including drag racing.
Finally, CP-Carrillo makes a Bullet line of rods from 4330 near-net forgings to appeal to select budget markets. “It’s an I-beam style rod,” said Batchelor. “We made an investment in a few forgings for limited applications, and that is to keep the cost down. We buy the forgings in bulk, keep our costs down, and minimize machining operations where we can to make them more of a low-cost sportsman rod.”
The Bullet series should attract circle track engine builders and select sportsman drag racers, but the Pro H-beam is still CP-Carrillo’s signature offering.
“The H-beams are typically for bigger power, our bread-and-butter rod. It’s what we’re known for and have done for decades,” said Batchelor. “Fred Carrillo actually brought the H-beam into the motorsports world. The rod stayed pretty much the same structure for many decades. In the last 10 years we’ve made some changes, improving the designs through FEA and our own knowledge.”
Some 50 percent of the company’s business is with custom orders, and working closely with the engine builders is key to producing the correct product.
“What are your goals today and for the future?” asked Batchelor. “Sure, you want to make 600 horsepower now, but in two years are you going to be happy with that? Do you want to make a thousand horsepower? Design the rod for what you want to do with it, not just what you are doing with it.”
Over at Olive Branch, Mississippi-based Lunati, the company has introduced the new X-beam for LS and LT engine families. The design strategy is to combine the benefits of both I- and H-beam rods into a unique 4340 forging that is secured with ARP 2000 bolts. The company rates these 6.125-inch long rods up to 1,700 horsepower and 9,000 rpm. A lightweight version is also available with respective ratings of 850 horsepower and 9,000 rpm.
“Even though pricing on it is cheaper than our Signature series, it is the ultimate rod to have for any extreme horsepower application, whether that’s boosted or nitrous,” said Will Vance. “These rods were extensively tested in a dyno mule making closer to 1,800 horsepower and spun up to 9,000 rpm. When pulled down for inspection they looked new. We believe we have one of the baddest rods on the market with a price that any racer in this power range can afford.”
Lunati’s rod lineup starts with the Voodoo H-beam series that is rated up to 750 horsepower, followed by the Signature I-beam series with a rating of 1,200 horsepower.
“The Signature has been our premier rod for years and still extremely strong,” said Vance.
FINAL ANALYSIS
By all accounts, connecting-rod manufacturers show a willingness to work with individual teams to meet their specific needs, and have compiled proven track records to back up their designs. There are high-end racing classes that allow titanium, but all those rods are custom ordered and expensive. Other specialty classes like Top Fuel and some land speed engines are loyal to aluminum rods; however, if composites prove worthy of the hype, then that is a narrow segment that will be disrupted in the near future.
In a final analysis, however, current connecting rod strategies appear to be benefiting motorsports with few drawbacks. Computing power, testing, and mature wisdom combine to build a solid product that is versatile and cost effective. The future can only get better, if only because experience continues to enlighten the skeptics and teach the novices.
“I have seen people try things, had things not work out, then five years later you find people trying to do the same thing again,” explained Molnar. “It keeps going around and around. As new people come on board, they try all the things that they think are going to work…. Regardless of the brand, why don’t you call the manufacturer? Why go to someone that does not have any connection to what you are doing?”
SOURCES
–