Racing's Heavy Act
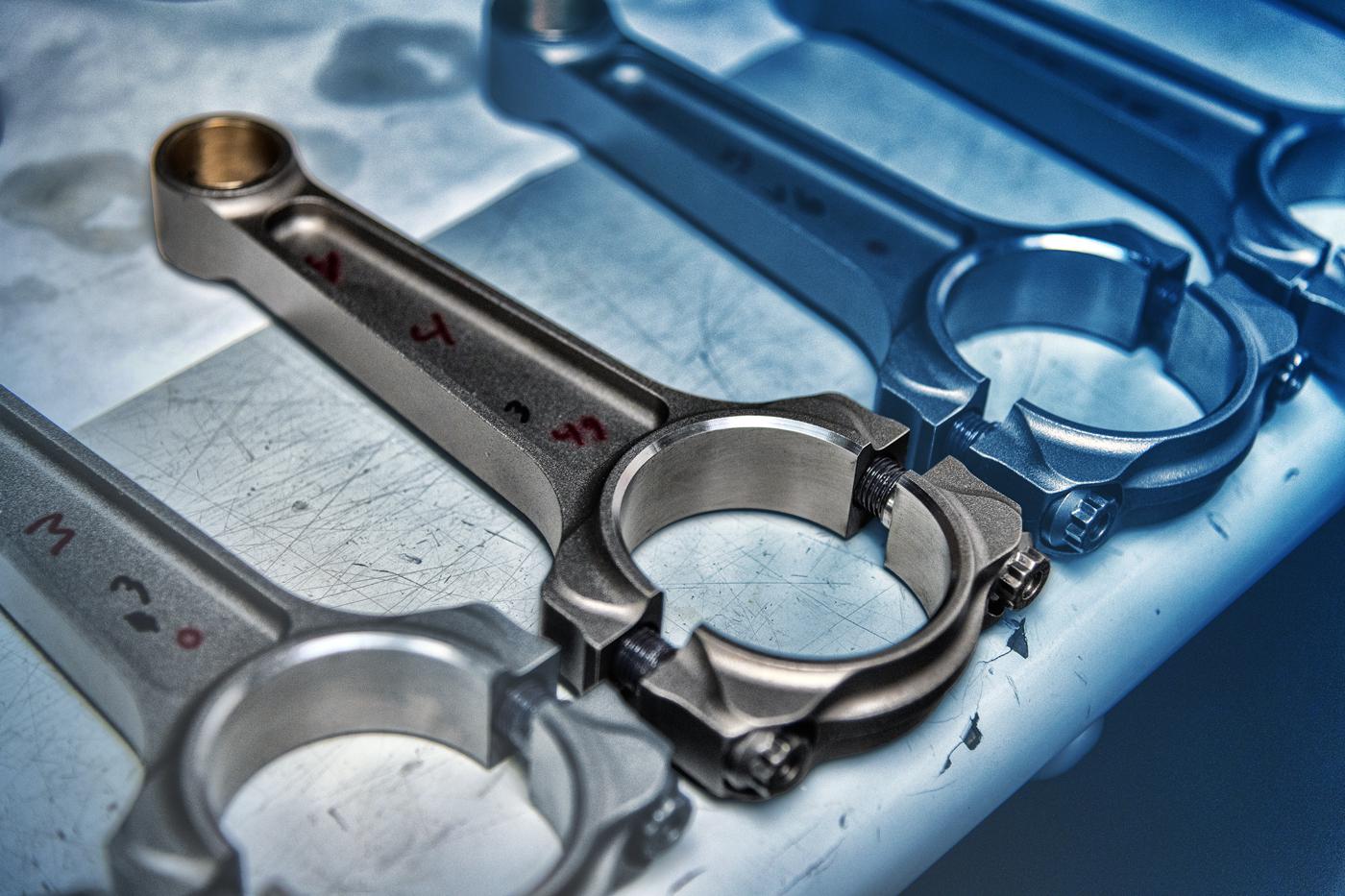
Connecting rods are gaining weight and getting stronger to accommodate race engine builders bent on cranking up the boost.
If there’s a common mistake that engine builders make when selecting connecting rods, it’s probably that they don’t listen to their connecting rod supplier.
“But you have to know your supplier,” advised Tom Lieb of Scat Crankshafts, Redondo Beach, California. “There are people who sell parts, and there are people who make parts.”
That’s a given: Leading engine builders will work directly with a well-respected manufacturer to ensure that the correct rod is helping anchor the rotating assembly. Most rod manufacturers offer a range of different designs and lengths, while others focus on specific markets or applications. The bottom line is that manufacturers can offer a wealth of practical knowledge.
“When a supplier tells you to torque a bolt to a specific number or use a specific clearance, they’re coming from a position of experience,” noted Lieb.
Meeting Power Demands
In the past, the search for a winning combination often led engine builders to use lighter connecting rods as new materials and manufacturing methods improved the rod’s overall strength. A lighter rotating assembly will accelerate quicker, which may be the slight advantage that a drag racer or dirt track racer needs. That conventional wisdom is being challenged today by rod companies that are concerned about the tremendous power levels generated when engines are boosted and tuned to the ragged edge.
“Rod weight is important, as it affects the reciprocating forces in the engine,” explained Matt Polena of K1 Technologies, Mentor, Ohio. “Many people think a lighter rod is better because it means faster throttle response and acceleration. But the rod needs to be strong enough to withstand the horsepower and tension forces the engine can generate. Weight is just one characteristic to consider when making your connecting rod choice.”
Pushing the engine’s envelope is also pushing up the weight of connecting rods. Just ask Kenny Duttweiler, who has built all the record-setting engines for the Poteet & Main Bonneville streamliner Speed Demon. These engines run wide-open throttle for five miles with boost pressures up to 50 psi.
“Any form of detonation would bend the rods,” recalled Duttweiler. “It doesn’t take a lot to spike the cylinder pressures. We probably started with a 680-gram rod and ended up with around 880 grams. Now our big block rods weigh 930, and I’m having Chrysler rods made that are over 1,000 grams.”
Teams can chase gremlins all over the engine trying to find the cause of detonation. One year, using the 388-cubic-inch engine, the Speed Demon team made a pass with an ultra-safe 11 degrees total timing. On the return run they bent a rod.
“At what point did we fix the problem and at what point did something else occur?” asked Duttweiler, who thinks some form of spark scatter or intrusion into the cam/crank signals interfered with the precise timing maps needed for a perfect run. “You might get a couple hits on the spark that’s off a few degrees, and that would bend the rod.”
Regardless, Duttweiler worked with two rod companies over the years, and the advice kept recommending heavier and stouter rods.
“I told him off-the-shelf rods simply won’t work,” said Stefan Verdi of Auto Verdi, Söderbärke, Sweden—the company currently working with Duttweiler. “You need something more like a diesel rod, so I came up with a rod that was very heavy. We do a lot of rods for diesel engines. Those rods need to be very fat, and then they work perfect.”
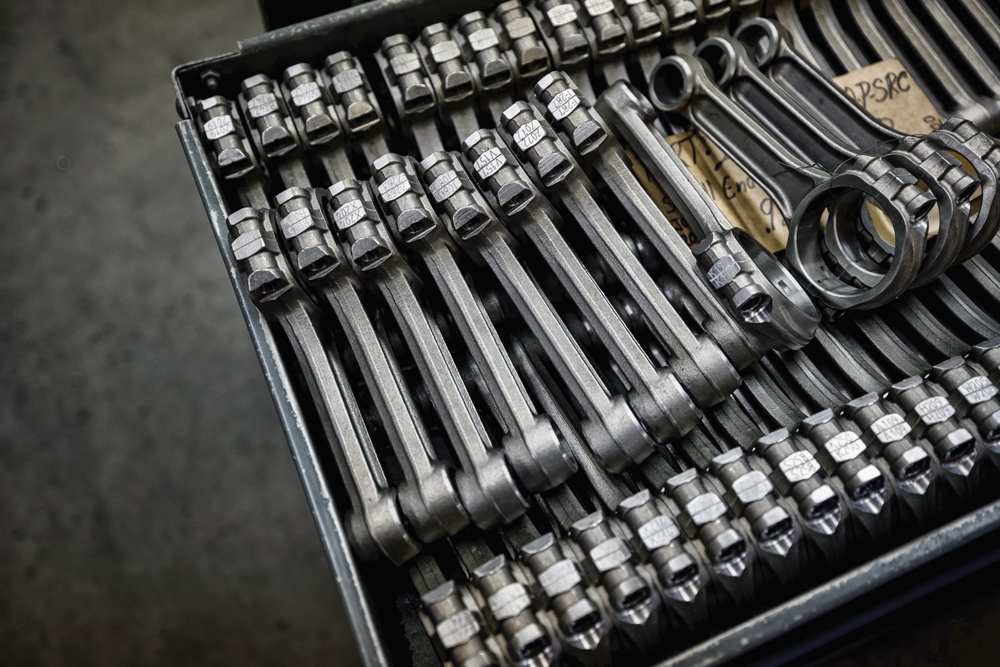
Sophisticated tuning has certainly upped the power game, especially at the drag strip where power adders are the norm.
“We’re always making stronger rods. We try to steer people in that direction,” said Peter Harris of Crower Cams, San Diego, California. The company’s Maxi-Light 93 series is available in six different versions, stepping up in weight each time. “For road racing guys, you always want to keep them in a stronger rod even though they want a lighter one. And you still have to get them into a 7/16-inch rod bolt because that racing is so hard on the rod bolts.”
Even Crower’s top-of-the-line series 6 model has a few different versions to handle power adders. “We’re always making the beam stronger and making the big end stay round,” added Harris. “Our Maxi-Light series is a radial beam design, which means it’s all continuous radiuses. There are no straight areas for stress concentration.”
While strength is a priority, the best rod design that can achieve that toughness continues to be debated. It’s one of the hottest arguments within the industry, and it’s one of those where there really isn’t a clear-cut winner.
“We’ll preach all day long for a big power adder that an I-beam is stronger than an H-beam. But at the end of the day, everyone argues both ways,” said Brook Piper of Callies, Fostoria, Ohio, which recently introduced its Enforcer series. “It’s a heavier, stouter rod that can take power adders. If you are not making 1,000 horsepower, you’re nobody these days. And everybody’s using some kind of power adder.”
Weight vs. Durability
Over at Dyer’s Top Rods in Forrest, Illinois, only H-beam rods constructed from 300m steel are produced—so the priority is on selecting the best weight and size for the application.
“We’ll ask how much horsepower, peak rpm, piston and pin weight—get all the usual information,” said Roger Friedman. “Then I can determine how heavy or light a rod and whether it needs a 3/8-inch or a 7/16-inch bolt.
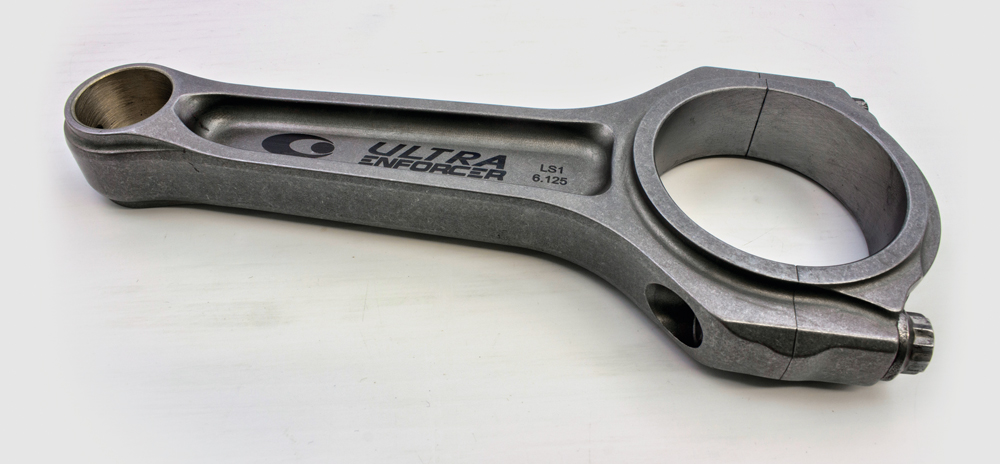
“What has changed is the LS engine,” continued Friedman. “It seems that if you’re talking 600 to 800 horsepower you can get away with any rod. If you had 600 to 800 horsepower in a regular small block Chevy, you don’t normally get by with any rod. I really don’t have an answer; it just seems that the LS is more of what I call a ‘happy’ engine.”
Friedman and others also have intense discussions with customers over rod weight.
“The best engine builders will question themselves, but their clientele sometimes dictates what they will build,” said Friedman. “Racers complain they want lighter and lighter rods, which do accelerate faster. There’s probably 1% of all the dirt drivers that can tell the difference between a light or heavy rod in an engine.”
Even when titanium rods are allowed, Friedman suggests that it would be difficult to tell the difference from the driver’s seat. “They’ve got these cars glued to the track and they’re on the throttle all the way,” he added. “A titanium rod may weigh 500 grams and our rod in the same application could be 620. Maybe in a small bullring a driver could feel the acceleration difference. But on an average track where they’re on the floor all the way, how’s that guy going to tell what the rotating assembly is doing to him?”
“Let’s say you go from 650 grams down to 600 grams,” added Tom Molnar of Molnar Technologies, Kentwood, Michigan. “How much difference does that 50 grams make when you’re trying to move a 3,000-pound car? You go too light and you’ll have a catastrophic failure. We’re moving people into stronger parts.”
Molnar has developed the Power Adder Plus series to keep up with power demands. “Everyone wants to spray or turbo their motors,” he said. “We’re adding more material in critical areas. We’d been running our regular rods with pretty good luck. But when I see what some of these guys are doing, I better have a stronger piece.”
When designing these new rods, Molnar relied on science and engineering but also “40-plus years of just doing it.” He said FEA is a great tool, but he has seen improper data used, followed by unsound results.
“There’s more to it than just what a computer tells you,” he said.
“The strength of the rod is in the metal,” confirmed Lieb. “It goes without saying about the quality of the metal and heat-treatment. But the amount of metal is the strength. Look at NASCAR. They run a relatively heavy rod because of the rpm they run.”
Plus, there are design tricks manufacturers can use. Scat will drill a hole near the big end of the rod in its Ultra Lite stroker H-beam series. “Now we’re able to put more material in the beam,” said Lieb. “The weight of the piston during overlap is tremendous. When it is coming up with both valves open, it’s ready to go through the cylinder head. That’s the material that holds the piston when it changes direction.”
There are limits to dealing with a steel rod, however.
“We try to steer guys to their application, and if they have a power adder, we try to put in the heaviest rod we can,” said Piper. “But once you get to a certain point you have to look to an aluminum rod.”
Aluminum connecting rods take up a lot of real estate, but they are easier to manufacture and, of course, they are lighter than steel. A big block Chevy rod may be 200 grams lighter than a comparable steel rod. Most are machined out of billet alloy, so there’s flexibility in the design. Perhaps the most useful property of the alloy rod is that it acts like a shock absorber in high-boost and high-cylinder-pressure applications like Top Fuel, Pro Mod, and even truck and tractor pulling. Not all of the tremendous pounding the piston takes under detonation or misfiring is transferred to the crankshaft, mains, and bearings. The downside, however, is that an aluminum rod won’t offer the same cycle life as a steel rod, so it’s used mostly in applications where there is consistent maintenance and replacement. Yet, there are always exceptions.
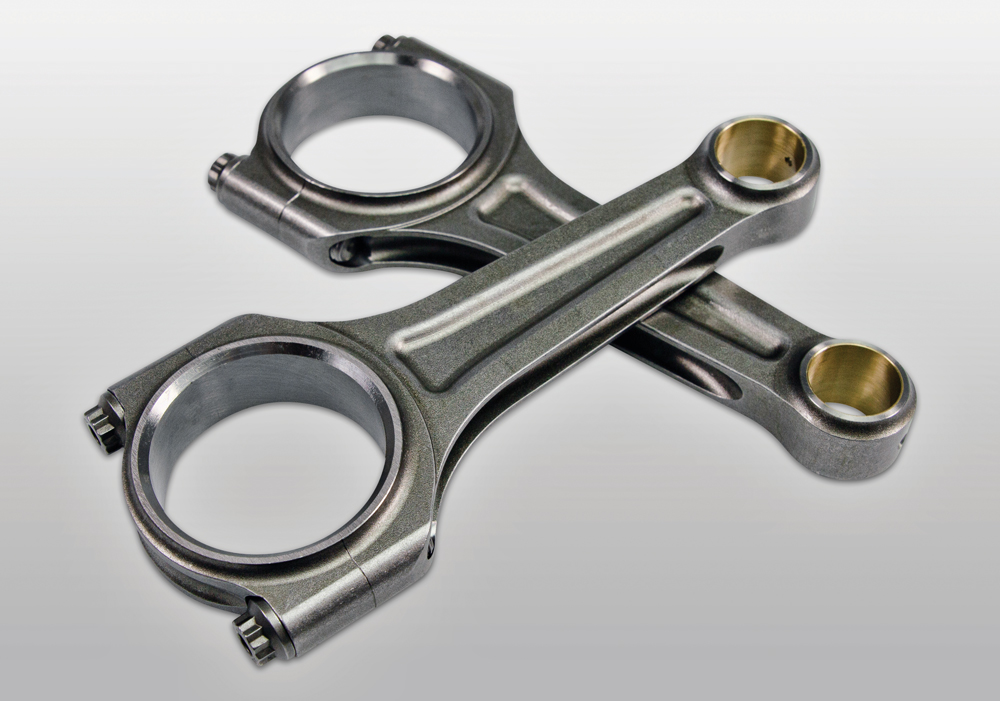
“We’re seeing more people use them for street use,” said Anthony Giannone of MGP Connecting Rods, Colorado Springs, Colorado. “These are high-horsepower, Drag Week-style or street-strip engines making 2,000 horsepower.”
Drag Week engines must run for about 1,000 miles on the road plus a number of all-out runs on five race days at various drag strips during the class competition.
“I want to say our rods are good for a Drag Week-and-a-half on an engine that’s making 3,000 horsepower,” said Giannone. “We’re also seeing more people use them in LS engines. That’s about the only application we’re broadening the horizon with these days.”
MGP can choose between 42 different designs after considering the customer’s application and power level.
“We’re starting to get into import engines, and that can be a tough fit for an aluminum rod and still have enough cross section to make them durable enough to handle boost,” added Giannone.
In addition to weight and construction design, rod length is another fun topic that comes up often in bench-racing sessions. Some engine builders have a range of rod-length-to-stroke ratios that fall within their acceptable margins. Others set priorities like deck height, piston compression height and stroke, and then let the rod length fall where it may. While rod length is a highly debatable subject, there are success stories when making certain changes.
Alan Davis of Eagle Specialty Products in Southaven, Mississippi, recalled an engine builder specializing in offshore marine motors. One of his top products was a supercharged 540-cubic-inch big block Chevy utilizing 6.385-inch rods.
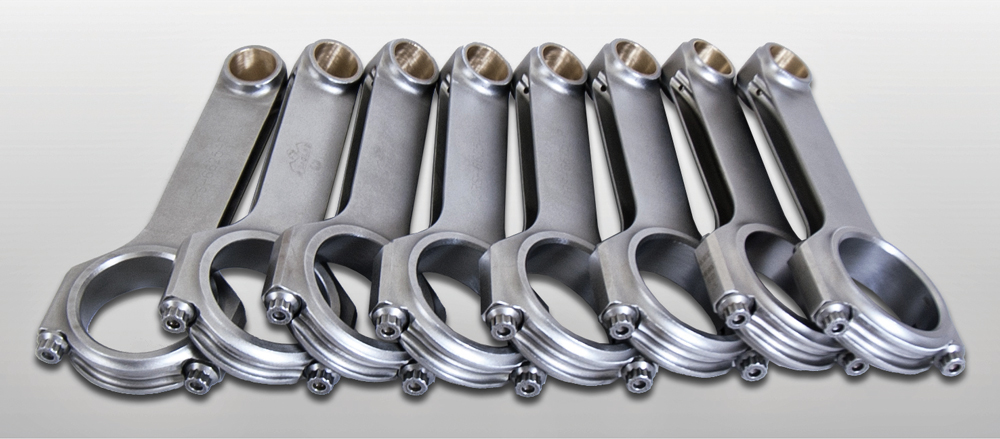
“While everything worked well, we were able to reduce piston skirt wear by putting a comparable assembly together that used a longer rod,” said Davis. “The reduction in maximum rod angle and resulting reduction in side loading helped extend the service life of the engines. It also made for a smoother running engine and it was less sensitive to timing. Engine acceleration is not important in an offshore application but reducing wear due to constant high-rpm use is.”
Eagle offers a wide variety of rod designs and often has to educate the builder on proper selection.
“Most manufacturers offer several variations of each connecting rod that each shine in different applications. Some exist to save money, some exist to provide ultimate strength, some exist to reduce weight to improve acceleration, some exist for longevity in real-world applications. There are connecting rods that are a mixture of several of these attributes, but you can’t have everything. Understanding which rod is right for your application is essential in extracting the best performance from your engine. Understand your requirements and take a realistic approach to considering the viability of each option.”
Further Improvements
The future of connecting rods isn’t exactly filled with surprises. There are suggestions that composite materials and 3D printing will be major factors, but for now those breakthroughs are still deep in development.
“There is the most benefit to gain from creative and innovative design,” predicted Will Vance of Lunati, Olive Branch, Mississippi. “Although new materials are constantly being developed, many new materials have limitations, like cost or shelf life, that are prohibitive to all but the highest end consumer.”
Vance said manufacturing improvements will lead to lower costs, but engineering design will lead to more performance advancements.
“Lunati recently developed a new X-Beam connecting rod that combines the benefits of traditional I-beam and H-beam designs,” he said. “That helps to minimize weight without sacrificing strength. We feel it offers the best strength-to-weight ratio of any rod geometry.”
As far as materials, there is no “unobtainium” that offers both significant strength and a reduction in weight. Auto Verdi plans to come out with a stronger steel in the next year or two, but there is very specific and expensive heat-treatment associated with this alloy.
“Cost is always a concern with racers, but there are teams that will pay,” said Verdi.
“This is a never-ending process, and we are always improving,” said Davis. “The market has dictated the necessity for design improvements. More power is being made now than ever before and stronger rods are being developed with this in mind. The biggest thing you will see in the future of connecting rods is diversity. Application-specific connecting rods will emerge as each market segment becomes more educated in where the advantages are to be found in their specific application.”
Center Stage
—
While most of the companies we spoke with for this report offered advice on connecting rod strength, design, length, and materials choice, one wanted to focus on a very specific oversight on the part of some engine builders.
“Some engine builders do not understand the rod offset needed to keep the pin end of the rod centered in the piston,” said Richard Batchelor of CP-Carrillo, Irvine, California.
There is a simple formula to determine the offset: rod width – cylinder back offset = the rod offset toward the crank throw. For example, on a small block Chevy, a .940-inch-wide rod minus the .880-inch-bank offset equals a +.060-inch offset.
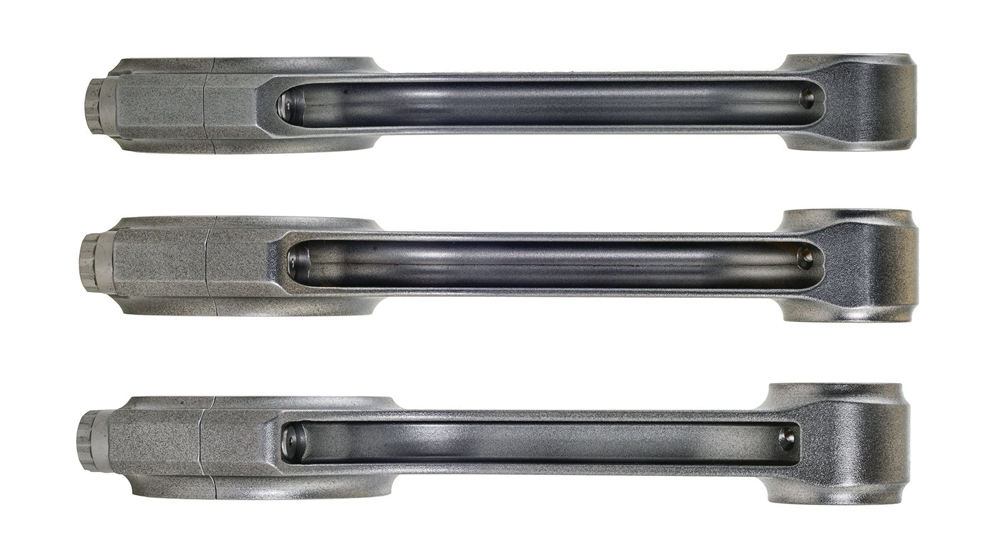
“Often we see the big-end rod width listed as on center when it should not be. Our rod order form requests that the ends be written down from center of the beam,” explained Batchelor.
The company recently had a nostalgia fuel customer with six vintage blocks that all had slightly different bank offsets. The team had constant issues with the pin end rubbing the piston and the big end of the rod rubbing on the crank cheek.
“I sent them a sample rod with a narrowed pin end and had them mock it up in each block and measure the distance to the piston pin boss on both sides. Once I had these numbers, I was able to get them a rod that was intentionally offset on the pin end in the opposite direction of the big end. This combined with an increase in big-end offset and narrowed pin end was just enough to keep it off the piston, regardless of which block they were using,” said Batchelor. “It took me some time to figure it out, but in the end, they were extremely happy to not have this problem anymore.” —Mike Magda
SOURCES
–
Auto Verdi
autoverdi.com
BoostLine
boostlineproducts.com
Callies
callies.com
CP-Carrillo
cp-carrillo.com
Crower Cams
crower.com
Duttweiler Performance
Dyer’s Top Rods
dyersrods.com
Eagle Specialty Products
eaglerod.com
Howards Cams
howardscams.com
K1 Technologies
k1technologies.com
Lunati
lunatipower.com
Manley Performance Products
manleyperformance.com
MGP Connecting Rods
mgpconnectingrods.com
Molnar Technologies
molnartechnologies.com
Scat Crankshafts
scatcrankshafts.com