Dialed In
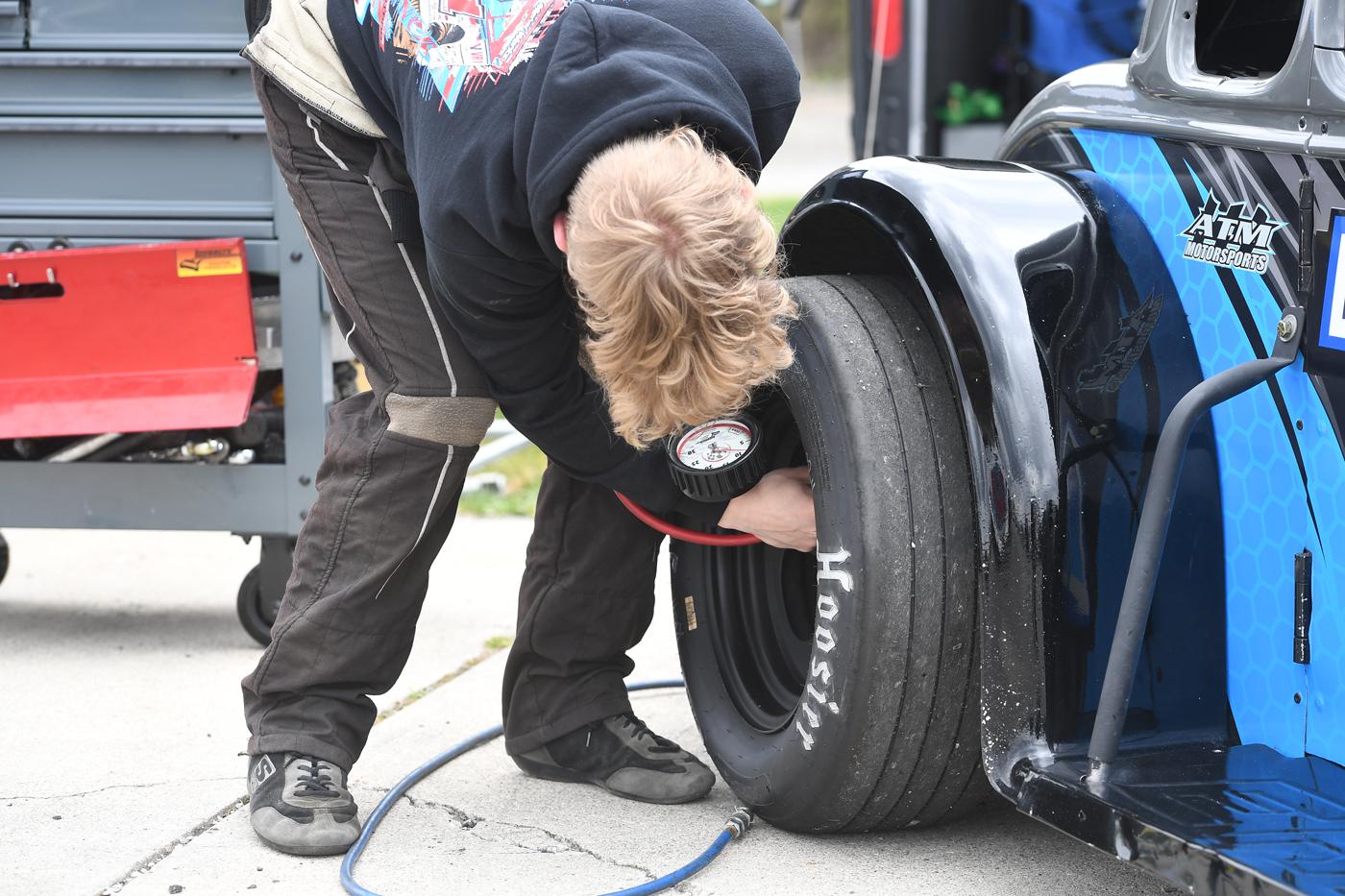
Advances in measurement and testing procedures are helping to deliver consistent, repeatable results on track.
As various series tighten rulesets to address rising costs across a range of motorsports disciplines, chassis setup has become a crucial element of competitive race programs. While the benefits of a well-sorted setup have been understood for some time now, in recent years it has become much more difficult to overcome any potential shortcomings with an additional dose of horsepower or a clever aero tweak. As a result, many teams are taking an increasingly sophisticated approach to the setup process, and they’re utilizing equipment that can provide a level of accuracy that was unheard of not so long ago.
“With the digital caster camber gauges we’re using, the margin of error is down to less than a tenth of a percent,” said Ben Baker of Longacre Racing Products, Boonville, Indiana. “When you compare that to the analog-style needle gauges, the accuracy really comes down to whoever is reading the gauge. The gauge itself might be very accurate, but it’s open to interpretation by the person who is looking at the measurements. There are some chassis height gauges out there measuring within ten thousandths of an inch. In the pavement world, that kind of accuracy is really critical.”
And detailed accuracy required in other industries, such as aviation and the US military, is benefiting motorsports, according to Carter Gerlach of Intercomp Racing in Medina, Minnesota, which is an ISO9001:2015 Certified US manufacturer and offers weighing and measurement products for all three industries and more. “We take that level of precision from our other markets and float it into our racing market products,” he said, noting that Intercomp RFX Wireless Scales are used exclusively by all NASCAR divisions including ARCA for tech inspections, “which is really indicative of the accuracy and the precision of the product.”
Tech-Driven Precision
While the exactness of today’s chassis setup equipment is allowing racers to take a more scientific approach to their tuning strategies, Steve Arpin of Longhorn Chassis in China Grove, North Carolina, pointed out that chassis manufacturing quality can have a profound effect on the end result.
“It really starts on the jigs,” Arpin said. “Teams in every motorsport discipline have always had their ‘special’ cars. I remember that during one of Kevin Harvick’s best years in the Cup series, he had this one specific car that he put aside for the Chase. You’d assume that if anyone would have the budgets to have identical cars produced, it would be teams in the Cup series, yet they still had these certain cars that worked better than the rest of them. That led us to wonder why. What are the differences that make one car stand out among the others? It starts with the materials, the tubing wall thicknesses, and how it’s all put together. You have to think about the chassis itself as a spring because it flexes out on the race track. That means that the consistency and repeatability you’re looking for in a chassis setup starts at that level.”
The importance of quality is reinforced by Steve Watt at Maxwell Industries in Ventura, California, who said that inconsistent parts manufacturing can make it difficult to hone in on the right settings. “With torsion arms, for instance, the manufacturer can make a difference. When some of the titanium ones first came out, we tested them and discovered that they were a softer rate than the aluminum ones. That kind of thing can really impact how you’re setting up the car, and it can kind of take you off of the ‘system’ of settings that you know you like.”
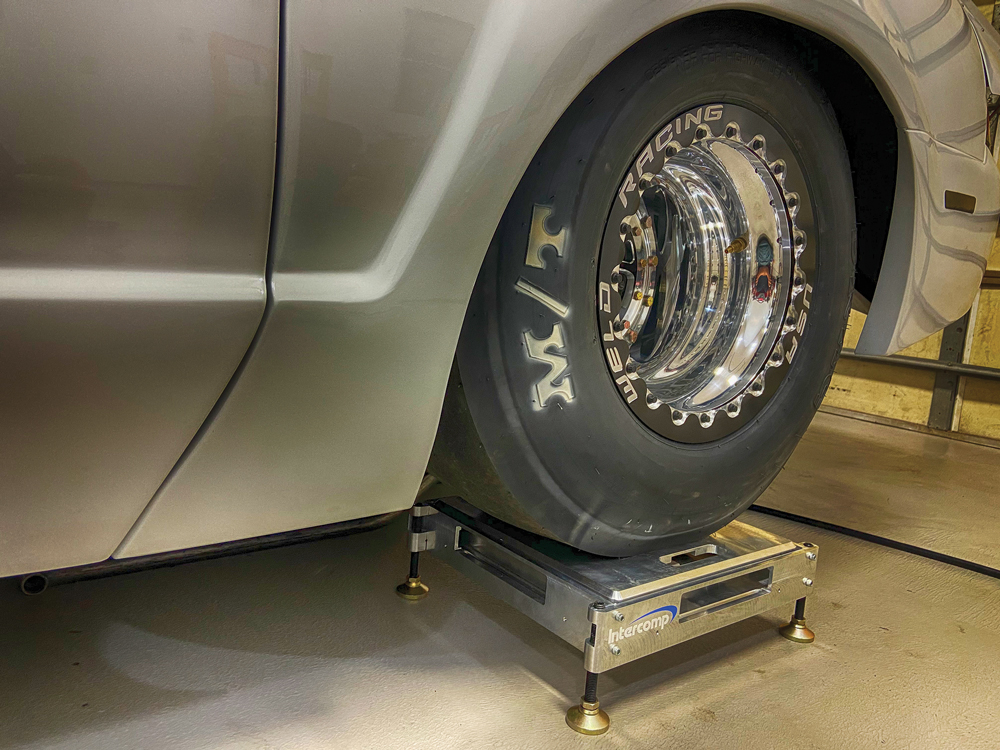
Moving beyond the importance of a solid foundation, Keith Berner of Accu-Force Shock Dynos in Millersburg, Ohio, said that the accessibility of advanced chassis equipment is bringing a level of exactness to grassroots and sportsman racers that simply wasn’t available in the past. “We’re at the point where regional and local competitors are using lasers to get measurements down to the thousandth. We used to use tape measures to do everything, and now we’re using things like micrometers and linear potentiometers that can tell you exactly where you’re at. When I first started building spring smashers, I thought that if we went to a tenth of inch, or maybe even a hundredth, that would be plenty accurate. But once we started using them, we realized that we had to go to the thousandth. Part of it comes down to the level of competition we’re seeing today. If you don’t do it, you’re not going to keep up with the guy who is.”
Gerlach cited Intercomp’s variable speed shock dynamometers, which feature a 40-inch mast height to rate a wide variety of shocks, with either a 3-hp or 8-hp motor, and simulates travel velocities of up to 55 inches per second to gather data for all markets.
To complement a race car suspension program, Intercomp also offers its traditional spring rater for testing springs alone, or its coil rating option, Gerlach explained, which allows testing of the entire coilover assembly without disassembling the shock and spring.
He acknowledged that Intercomp is “not a shock company, but we’re a shock testing company. Really, far and away, I would say shocks have changed in the cars and in the market the most in the past five years. That is a continual moving target and something that is really not slowing down. Racers and the teams are putting a lot more emphasis on their shock programs and accuracy with the testing and validating their shock program with our shock dynos and spring raters.”
As series continue to crack down on the gray areas of their respective rulesets, this level of exactness has become a necessity for those who want to extract all of the performance potential from their car without running into trouble at tech inspection. “As far as measuring suspension travel goes, things have changed quite a bit in the last eight years or so,” said Dave Dunlap of Basic Racing Enterprises in Asheboro, North Carolina. “With how close we’re running the cars to the ground now, it’s not really good enough to get it in the ballpark with a tape measure. We’re now getting to within an eighth of an inch to the ground without hitting it, and that’s thanks to things like the setup plates that companies like Wehrs and DRP Performance are producing. Today we can get a really clear picture of what’s going on with the suspension, and before we were just sort of guessing.”
Building A Baseline
Chassis setups require a holistic approach in order to be truly effective, but generally speaking, there is a hierarchy to the process. For Baker, that starts at the front end of the race car.
“You have to have the front end right or nothing else will work. If you don’t have the camber, caster, toe, and the bump steer set where it should be, it doesn’t matter what you’re doing in terms of weight distribution, or what your load numbers are—it’s just not going to work. So that’s the number-one thing in my mind. The next priority for me is the scaling process, and getting the corner weights where you want them. From there, it’s the load numbers.”
While it’s important to establish a reliable combination of static settings, today’s competitive chassis setups are largely based on how the car will behave on the race track. To get a better understanding of how that differs from those static settings, teams are using setup equipment that can replicate the forces that are applied to the car at race pace.
“We don’t drive around the race track with the car ever at ride height—the only time it’s at that height is when it’s sitting in the pits,” said Arpin. “When we’re scaling the cars, we’re setting the percentages to make sure the car has proper weight distribution, and to make sure it’s heavy enough to pass tech inspection at the end of the race. Everything else is done ‘in posture,’ whether that’s with load sticks or spring smashers. That allows you to replicate the attitude of the car when it’s going around the race track, so all of the setup adjustments really happen there.”
Berner told us that understanding the car’s dynamic position with the data provided by this equipment helps to deliver the consistent, repeatable performance that teams are striving for. “Spring smashers have been a game changer because they let us look at things that we weren’t able to see before, and pull-down rigs have benefited racing in much the same way. Over the years, these products have gotten more and more refined and have taken everything that much further. Our spring smasher goes down to the thousandths because we need that level of precision. What we found was that 10 thousandths on a heavier spring might be 20 or 30 pounds of difference. In today’s world, that matters.”
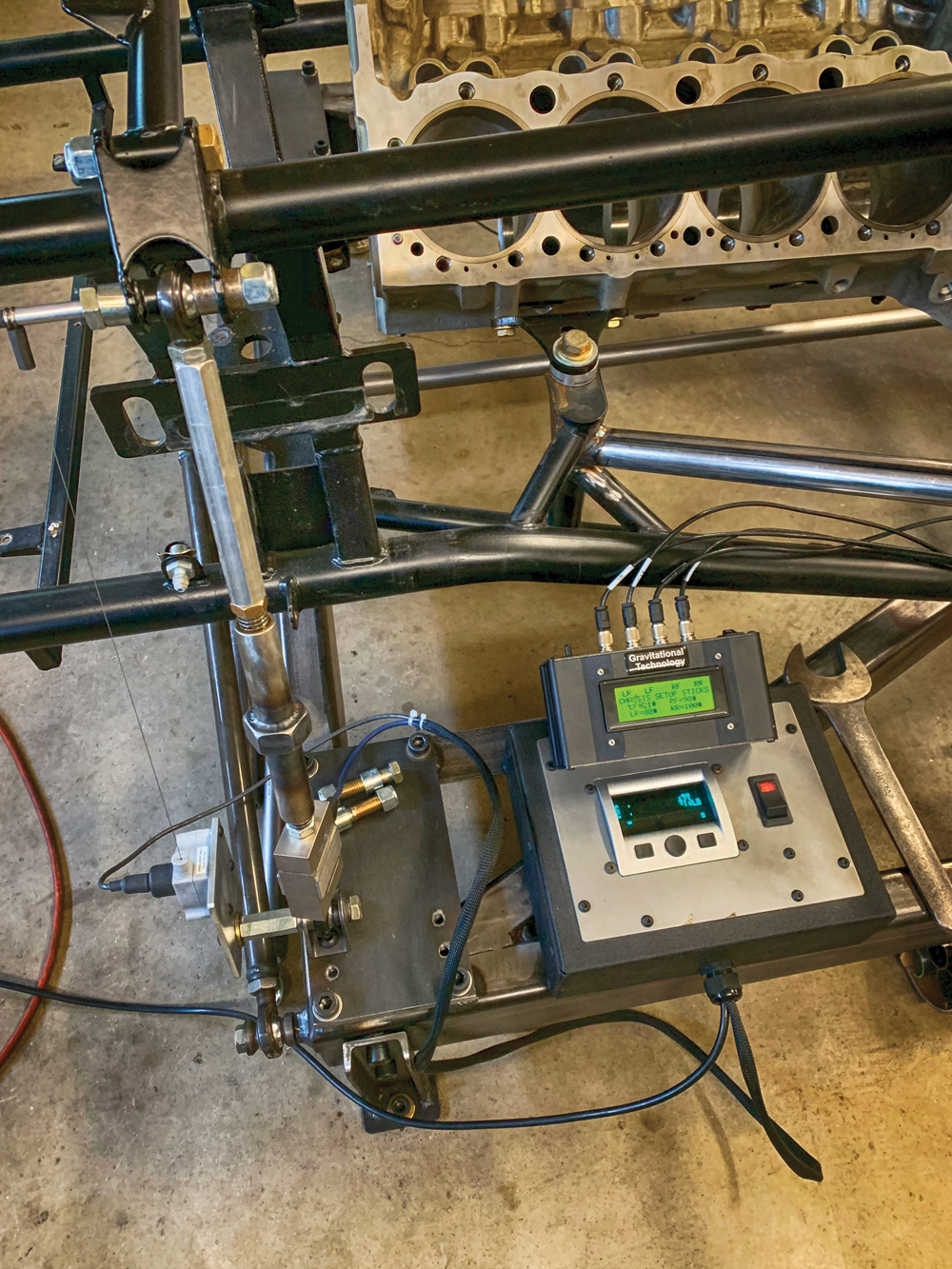
Although one incremental change here or there might not have a profound effect on a given car’s lap time, this level of accuracy can be used to improve a number of different aspects of a chassis setup. Enough small changes in the mix can add up to something that has a meaningful impact on race day.
“The top-running teams have a deep understanding of every single point on their cars,” Arpin said. “Improving one detail on the car might get you a hundredth of a second, and that might be considered a negligible benefit on its own. But if you stack up 20 different improvements that each get you a hundredth of a second, that can make a very big difference. Two-tenths of a second can be the gap between the national-level teams and the Saturday night racer.”
He added that this level of precision in chassis setup can help identify potential handling problems before they cause problems out on the course. “If you look at the Lucas Oil series, for example, there are virtually no DNFs for the teams that finish in the top five. Being able to look at the car with that much detail gives you a better handling car, so obviously you have more control. Having more control makes it easier to avoid wrecks and not get torn up.”
Gerlach cited a continual evolution in racing chassis setup equipment as “the chassis builders and the experts in the industry that are fabricating and developing setups within the cars are asking for numbers being tested, so we need equipment to test them. Where maybe five years ago they weren’t asking for that to be tested on the cars.”
To deliver those numbers, Gerlach pointed to several of Intercomp’s products including its digital air gauge that reads out to .01 PSI with accuracy of 0.1%, 6061-T6 billet aluminum scales, precision hub scales, caster camber gauges, turn plates, shock dynos, spring testers, and RFX Wireless suspension load sticks.
Intercomp’s Microflex scale systems have four load cells per pad for enhanced capacity and ultra-low deflection, he noted, and offer the company’s highest level of accuracy, repeatability, and stability for consistent chassis setup. They are available with system capacities of up to 16,000 lbs. (7,300 kg), and are an optimal choice for teams using pull down rigs and EV manufacturers that are doing weight and balance on the heavier EV vehicles.
Suspension load sticks are one of Intercomp’s newest products. Gerlach explained that these are installed on all four corners of the race car “in the shop or in the pits, where you’re able to pull a corner of the car into motion and see how much load is applied to that corner as we’re simulating what it’s supposed to be doing on the track.” This provides a picture of the race car’s load distribution in different chassis attitudes and allows racers to select the spring rates required to get the car into the dynamic ride heights needed to carry maximum speed and momentum through a turn. Intercomp’s Load Stick allows the user to read from one to all four corners of the race car on one RFX Wireless Indicator.
Translating Data To Performance
Although the ability of today’s chassis setup equipment to accurately simulate the dynamic forces on the car is a valuable tool for teams, real-world testing is still a critical element of the process due to varying track conditions and other external factors. But rather than relying solely on driver feedback to make adjustments, Watt noted that many teams are incorporating data acquisition systems into their test sessions in order to minimize the amount of guesswork that’s required back in the garage.
“You can put a system in the car that will tell you exactly how fast and how much your shocks moved, and the speed that they moved at, and there are shock dynos available now that will actually play that track data back,” he said. “That allows you to run your shock on a dyno as if it is running five laps around the track, and that can help establish a baseline for a course.”
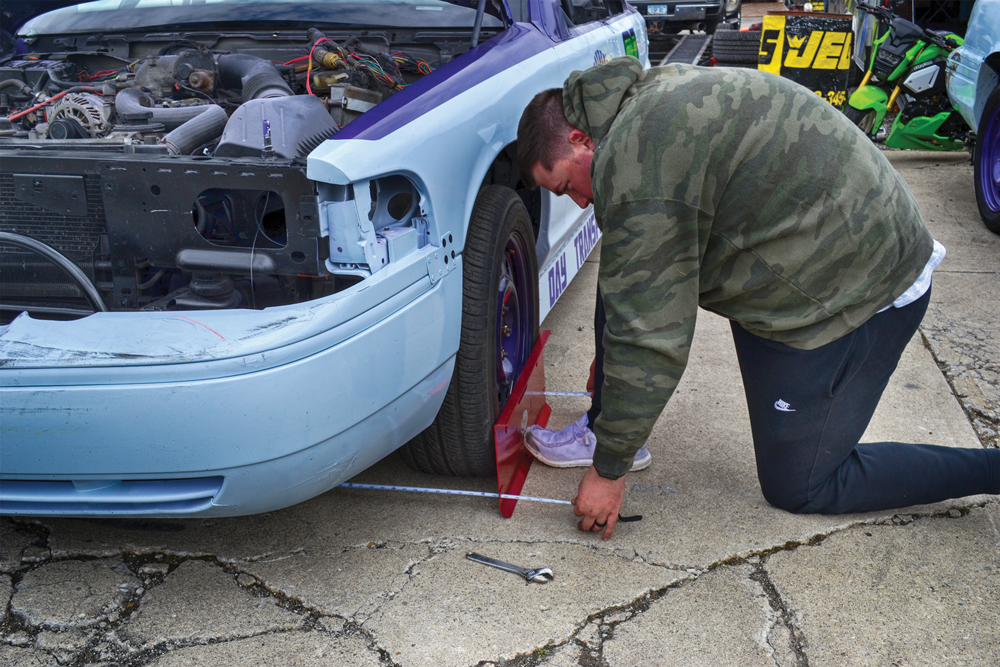
Berner said that having a precise baseline can be especially helpful for those who find they are suddenly starting from the ground floor again. “Let’s say we’ve got everything dialed in, but you get in a wreck. Instead of sort of getting everything in the ballpark of where it’s supposed to be, and not really being sure whether or not there are still problems in the car, you’ve got everything measured down to a thousandth, or a tenth of a degree, or whatever a particular measurement may be. Once you get the new parts on and set the car up that same way, it should be like the car was never wrecked.”
Combining real-world data with the detailed information that’s available from today’s chassis setup equipment has also ushered in components that enable teams to make changes in equally precise increments. “In some cases, we’ll put to use a packer that’s a sixteenth of an inch to make an adjustment. It’s basically a shim that’s made out of either plastic or aluminum that goes between the bump stop and the shock that changes your engagement height and puts more load on it. Sometimes a sixteenth of an inch is all you need,” said Baker.
He’s also quick to point out that while they’re an important piece of equipment in today’s setup strategies, some of the old school equipment still has its place. “There’s this huge misconception that, if you have a load machine or load stick, you don’t need scales anymore. It’s just not true—there are so many things that those load machines will not tell you that a scale can. Beyond getting percentages, there are situations where a scale will tell you if you have a bent spindle or a bent rearend. There are lots of things that the load machine will not catch.”
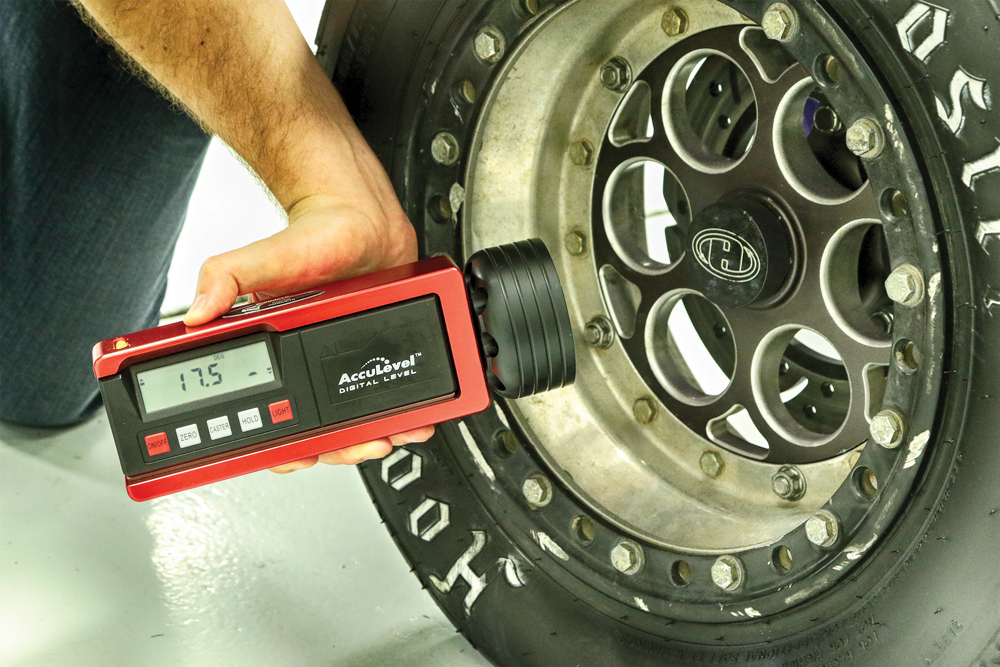
With the racing as close as it is today, there’s really no room for error. “People often wonder why their good car is getting beaten by some other guy, and most of the time it really comes down to the details,” said Berner. “There was a point in time where someone might’ve said, ‘Oh, that spindle isn’t bent that bad,’ and they’d race with it. But those attitudes have changed. Now if you even remotely think a spindle might be damaged, you have to change it or you won’t be able to keep up. The whole package has to be right.”
SOURCES
Accu-Force Shock Dynos
accuforcetesters.com
Basic Racing Enterprises
Intercomp
intercompracing.com
Longacre Racing Products
longacreracing.com
Longhorn Chassis
longhornchassis.com
Maxwell Industries
maxwellindustries.com