When Too Much Is Never Enough
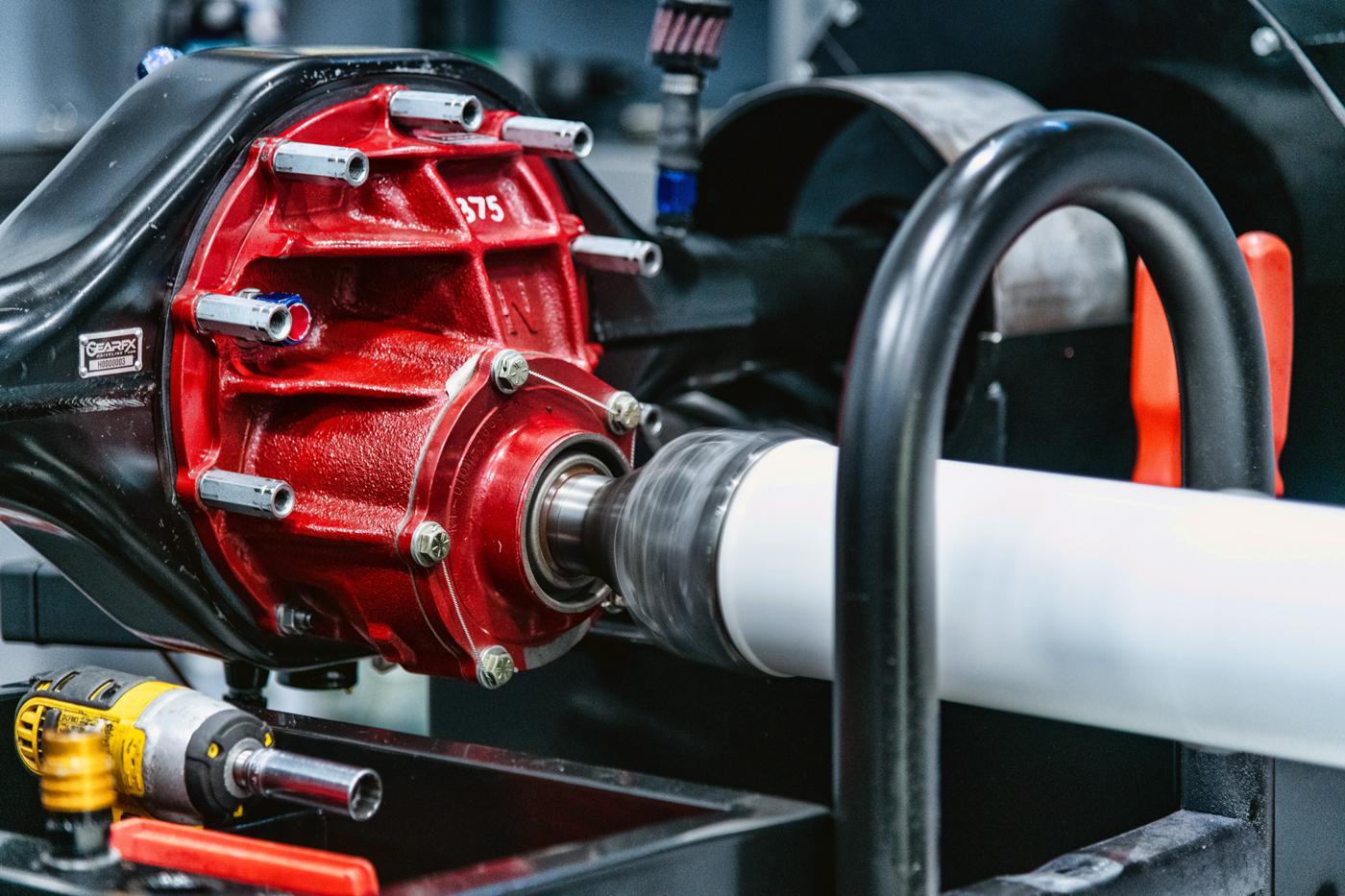
Driveshaft manufacturers are taking a strategic approach to design in order to deliver lightweight components that are both reliable and cost-effective.
As four-digit horsepower becomes the norm both at the race track and on the street, driveshafts are being put to the test like never before. With racers constantly upping the ante to find a competitive edge, driveshafts are playing an increasingly critical role in teams’ success; unlike many other components in a race car, failure here is at best a DNF, and at worst, a serious safety risk.
“We’re constantly in a state of development,” said Lee Mejia of The Driveshaft Shop, Salisbury, North Carolina. “From both the custom side and the OEM-style replacement side, we are regularly faced with challenges that require good solutions—some of the stuff that worked a few years ago doesn’t work so well now.”
Whether we’re talking about a street/strip drag car or a tube chassis circle track racer, the demands from competitors are the same—high strength, low weight, and affordability. But with tire and suspension technology rapidly evolving alongside the rise in engine output, accomplishing those goals is often easier said than done. And for many, the approach comes down to the specific needs of a given application.
The Modern Arms Race
“There’s a new kind of race car out there,” said Jesse Powell of G-Force Engineering, Wichita, Kansas. “Nobody is building 1969 Camaros to go race in NHRA Super Stock today. But if you go to any NMCA race, you’ll see about 150 late-model vehicles there to run the quarter-mile. These are the new race cars—it’s not the Fox-body Mustang that was bought for five grand that had $70,000 invested in it to make it competitive. It’s the new car that was bought for $70,000 and had five grand invested in it.”
Powell cited late-model Dodge Challengers and Chargers, Ford Mustangs, and Chevrolet Camaros as the main drivers of current demand. While all are capable of producing serious horsepower with fairly minimal changes from their showroom stock spec, these vehicles are often equipped with two-piece driveshafts from the factory in order to minimize noise and vibration from the driveline—designs that meet the strength requirements of an unmodified car and not much else.
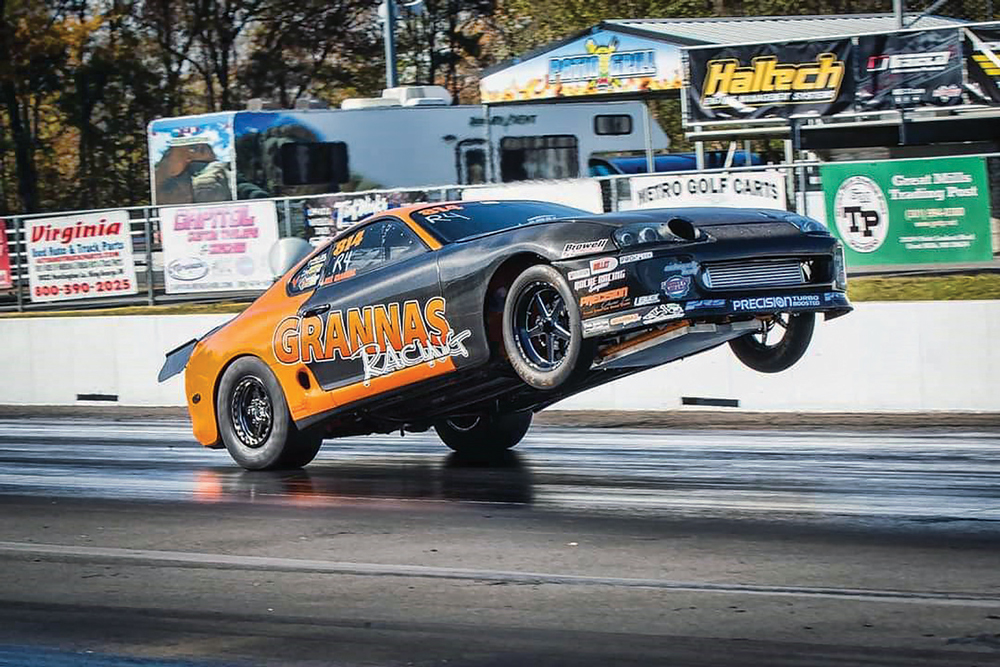
“The demand is pretty simple to understand—we’re dealing with a lot of horsepower and a lot of weight,” he said. “The cars are heavy and their horsepower potential is almost unlimited. A Hellcat makes 700 horsepower from the factory, but for about $2,000 in modifications you can make more than a thousand. The driveshafts that the OEs are designing are fine for the power that these cars make in stock form, but that’s basically it. The minute you start adding horsepower, you start breaking parts.”
Since many of these cars serve double-duty as race cars and street machines, the priorities for these driveshaft designs differ from traditional high-horsepower motorsports applications. “I think you can quickly reach a point of diminishing returns with light weighing,” Powell said. “The guy with the 4,500-pound Demon isn’t worried about adding two pounds to the driveline—he wants to support more power. There is a threshold that you reach where you start to lose more capability than the advantages you gain from keeping the weight down. You obviously want to do the best you can to keep the part light by using materials like aluminum and carbon fiber, but if the part breaks, you need to move to hardened steel, and that might be a few pounds more. At a certain point, if you want more horsepower you need to make sacrifices elsewhere.”
Powell noted that driveshaft designs for modern performance vehicles are limited by tight production car packaging, so engineers look for specific aspects of the design to pinpoint where meaningful improvements can be made. “We’re trying to defy physics. Right now a lot of what we do is aluminum, and we’ve gotten incrementally better with it by working with our partners like Sonnax to find the shortcomings, adding material where it’s needed, going to a thicker wall tube, reworking the bonding process—those types of things.”
He said he feels like they’ve reached a pinnacle of what they can do right now from a materials standpoint, so the current strategy is mainly focused on making the parts more robust as a system rather than making the driveshafts themselves stronger. “That means putting together the right bushing package, making sure we’re not binding up the U-joints, or putting the driveshaft into some sort of undesirable angle that can excite the driveshaft or compromise its integrity. For instance, we developed a new set of dual-stage bushings that provide OE-drivability at idle and while cruising, where the bushing material has a softer durometer. But it also has a harder durometer material that comes into play as you start to load the driveline that holds it firm so the pinion can’t move so much.”
The Balancing Act
While weight might not be a big issue for street/strip applications, it takes on greater importance for those running in series with purpose-built race cars, where the application necessitates different design priorities.
“You usually don’t have as many constraints to contend with here,” said Mejia. “Obviously we work with our manufacturers to make sure the tubing of our carbon fiber and aluminum driveshafts is of the best quality, but there are also innovations that are helping to support the driveshaft, effectively making it stronger. For instance, from our axle technology we’ve developed what’s basically a stub-mount system that uses a 300M chromoly stub shaft that connects the CV to either an aluminum or a carbon fiber driveshaft.”
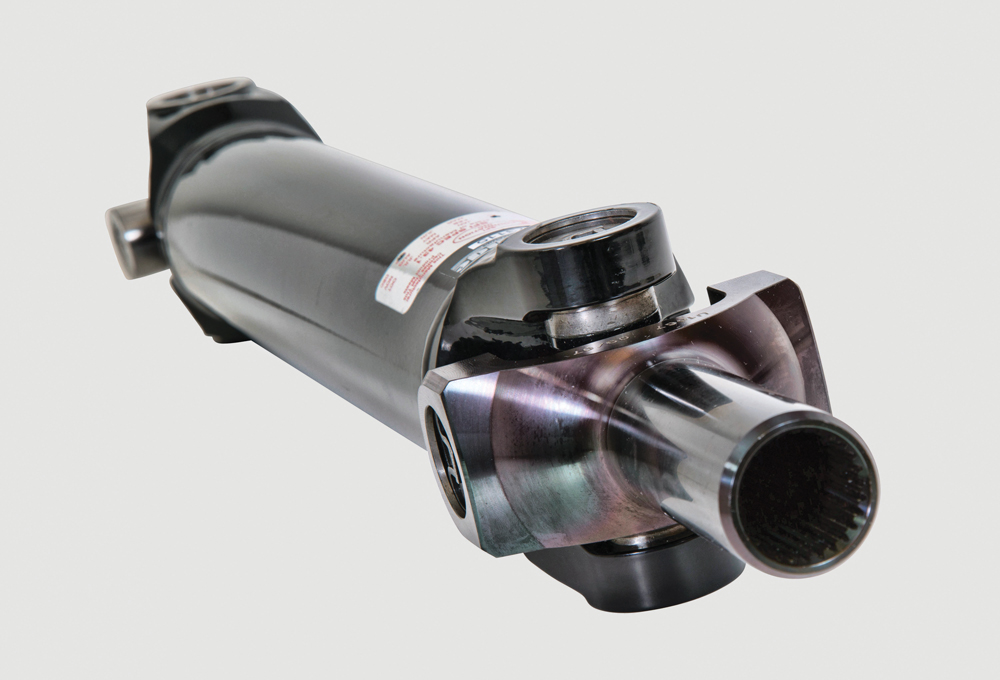
He added that it’s important to consider how the vehicle is going to be used in order to spec out an effective setup. “If a driveshaft is properly selected for the application, we tend to see very low rates of failure. They typically happen because something is being used in situations it wasn’t designed for. The criteria that we usually go by includes the weight of the car, horsepower range, the kind of racing they’re going to be doing, and the kind of tire they’re going to be running. We also verify any possible diameter restrictions—in some cases we can only do a chromoly tube or something like that because of the amount of space that we have to work with.”
While steel isn’t the lightest option available, it does provide some peace of mind in terms of outright strength. “We focus on strength,” said JC Cascio of Strange Engineering, Morton Grove, Illinois. “Accordingly, all of our driveshafts are manufactured with heat-treated seamless 4130 chromoly material with 4130 chromoly weld ends, which provides the strongest option. Both our 3-inch and 3.5-inch diameter tubes come with 0.083-inch wall thickness and are straightened to have less than .008-inch of total runout.”
For others who’re looking to get the strength they need with the minimal amount of weight penalty required to do so, other materials can provide a more targeted solution. “We do a lot with 4130 chromoly, but this is where carbon fiber really shines,” said Mike Bennett of Dynamic Drivelines, Des Moines, Iowa. “It’s super light and it’s very strong relative to its weight. Cost usually ends up being the main factor when choosing between the two.”
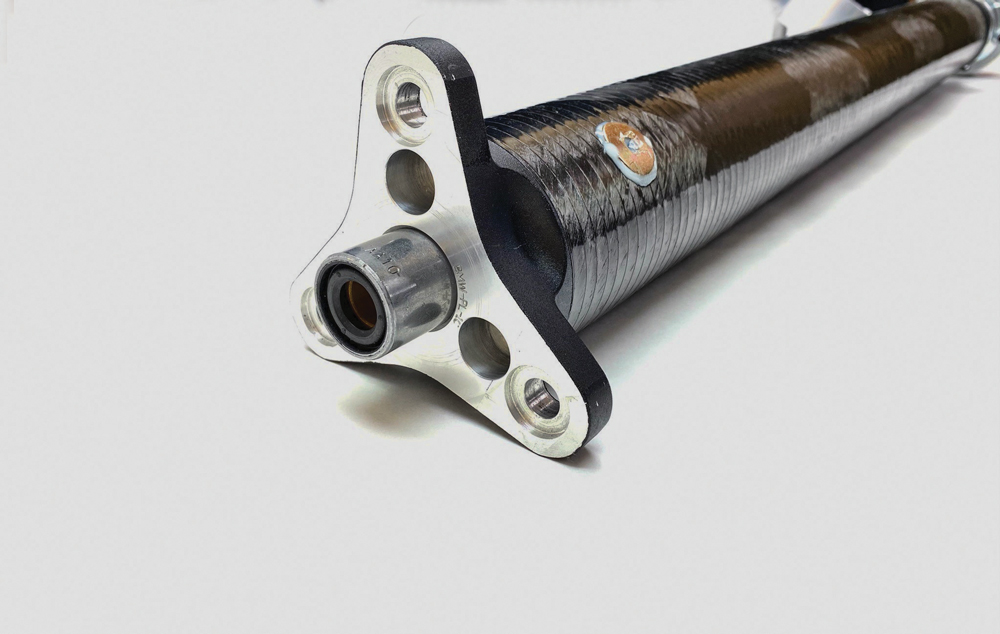
Aluminum also offers a lightweight alternative to carbon fiber that’s more budget-friendly, but it’s ultimately not as strong. To address this, engineers at Diversified Machine in Lancaster, Pennsylvania, identify where material can be added to provide meaningful improvements in overall strength, and where it can be removed without compromise.
“We can increase the OD—if we go bigger with the OD, we gain that strength, and we can still put a big hole through the center in order to provide a lighter product than the competition,” said Diversified Machine’s Dave Ely. “And maybe there’s a spot where we had a 0.030-inch radius previously—if we can get that to a 0.060 or a 0.090 radius, that will make a difference. Any time you’re able to put more radius in and make your transition points smoother, you’re going to gain longevity. At this point, it’s as much about the machining practices as it is about the materials.”
The Next Big Thing
With all signs pointing toward continued increases in horsepower, grip, and weight in the future, driveshaft manufacturers have no time to rest on their laurels. “As with all race components, driveshafts will evolve as the weight and horsepower dictate,” said Cascio. “And to that end, we’re always doing research, development, and testing to improve the capability of our driveshafts and expand our line.”
And by most accounts, that future is likely going to include an increasing shift toward carbon fiber driveshafts, despite the headwinds the material initially faced in this type of application. “I think they originally got a bad rap from the early years of sub-standard manufacturing,” Mejia said.
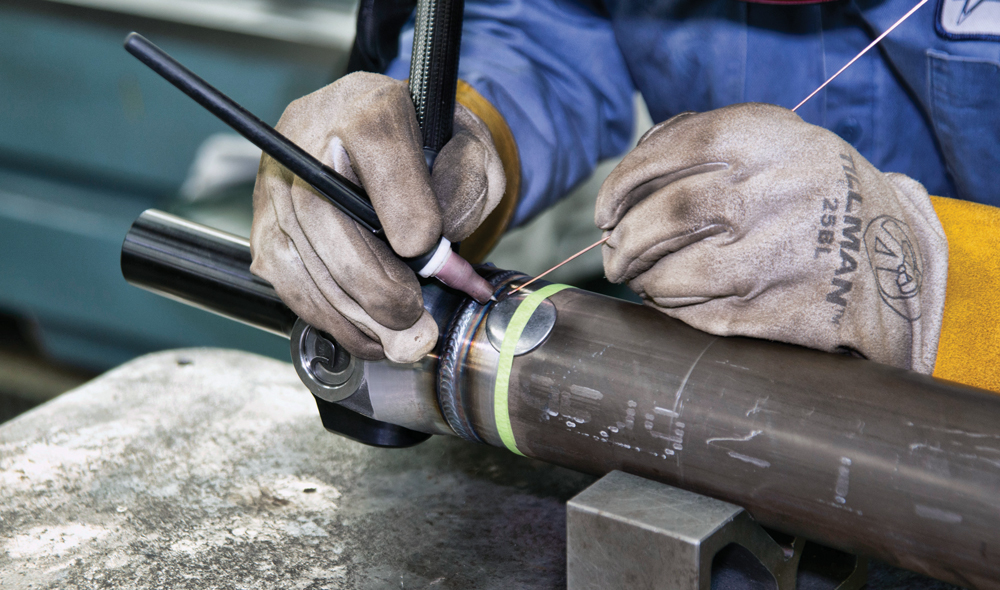
That sentiment is backed by Ely, who noted that circle track sanctioning bodies were soured on carbon fiber early not only because of potential cost increases, but reliability issues. “Twenty years ago, some companies came out with carbon fiber stuff and it didn’t really work very well. So right away the sanctioning bodies wanted to do away with this thing they saw as an unnecessary complication—just do away with them before everybody gets them.”
But as Powell pointed out, those processes and the resulting quality of carbon fiber parts have come a long way in the past few decades. “I think that’s where the drivetrain world is going—we’re just waiting for everything else to catch up with the technology. We know that carbon is where it needs to go in order to do this right in our segment.”
Bennett also agreed that carbon fiber is the material of choice for the road ahead. “Carbon is probably going to be the focus—right now it’s about getting the costs down. The way it’s made is more labor intensive, but the industry is definitely working toward ways to improve the pricing.”
And while certain classes and series are still hesitant to bring carbon fiber driveshafts into the fold, the tide is turning. “As carbon fiber driveshafts have improved as a whole and more people understand the benefits there, they have become much more widely accepted,” said Mejia. “The times that we run into problems running carbon today are mostly in series or classes where stock-style or spec components are a requirement because of the format.”
Beyond the performance and reliability advantages that today’s carbon fiber offers, the safety benefits are indisputable. “We do a lot of these for Pro Mods and things like that—big horsepower drag cars,” he added. “And a big factor for that is how safe it is. If a carbon shaft fails, it doesn’t have the potential to come into the car. It opens up like a broom stick and basically disintegrates.”
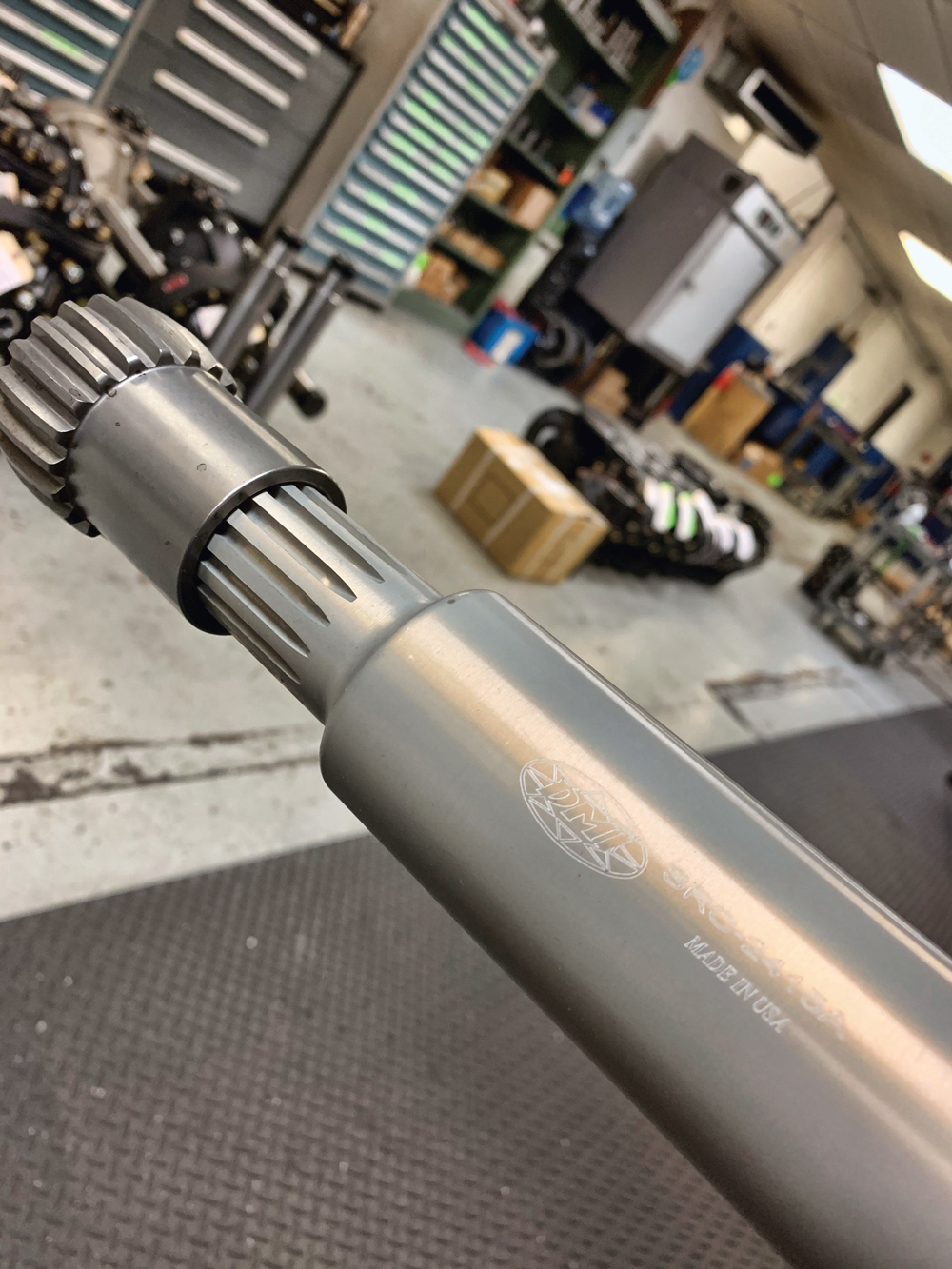
And because of that behavior, it’s also less liable to really beat up the vehicle in the event of a failure. “Generally, if a carbon fiber driveshaft fails, it splinters and shreds,” Powell explained. “So you usually have a lot less damage to the vehicle than you do with aluminum or steel. And in situations where you might not have a safety loop, carbon fiber is probably the least likely to cause the car to catapult because of how it breaks up.”
Although carbon fiber is seeing wider use among OEMs these days as well, Powell noted that it’s still largely relegated to specialty vehicles. “Stuff like AMGs, the new Mustang Shelby GT500 has a carbon fiber driveshaft—there’s a few of them out there. But they’re on premium vehicles, and I think it’s going to continue that way for a while because it still brings a premium price. Until we see that come into the same price realm as steel or aluminum, I don’t think you’re going to see carbon as the everyday OE material of choice. And that’s OK because it leaves room for us in the aftermarket.”
SOURCES
–
Buzze Racing
buzzeracing.com
Coleman Racing Products
colemanracing.com
Diversified Machine, Inc. (DMI)
diversifiedracing.com
Dynamic Drivelines
dynamicdrivelines.com
G-Force Engineering
gforce1320.com
Strange Engineering
strangeengineering.net
The Driveshaft Shop
driveshaftshop.com
VAC Motorsports
vacmotorsports.com