FAILURE IS NOT AN OPTION
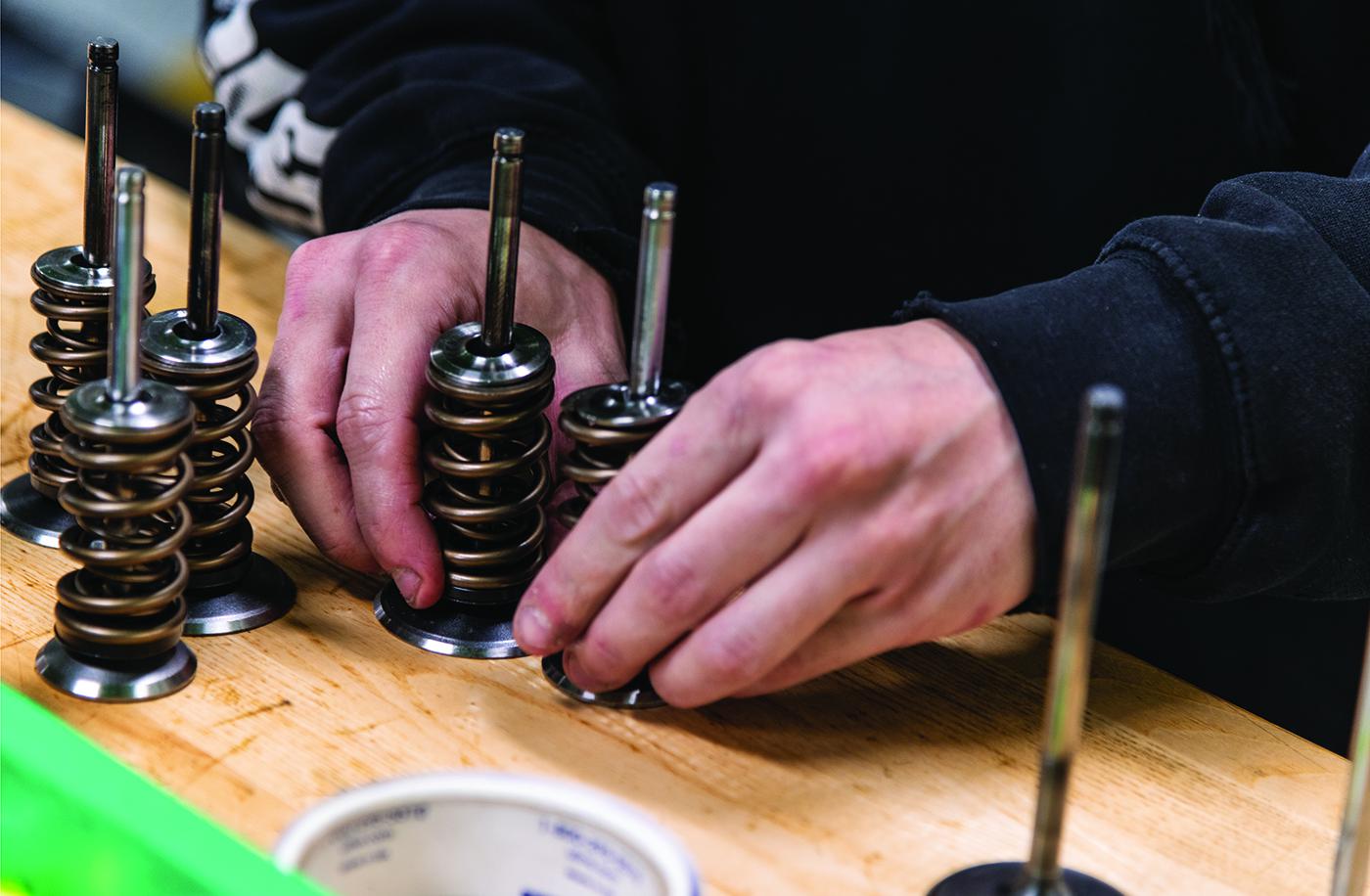
Though valvetrain parts probably break down more often than any other engine component, when subject to constant testing and improvement they are responsible for huge power gains.
A Stock Eliminator drag racer wanted answers. Though he had run a full season without any valvetrain failure, and even won the class championship, he was annoyed at the wear on all the exhaust valves. Each had a noticeable “trench” dug into the tip.
“He had been concerned about it for some time and was going to contact the manufacturer to investigate the hardness and quality control to see if they could solve the issue,” recalled Billy Godbold of COMP Cams, Memphis, Tennessee.
Instead, the racer sent block, heads, and valvetrain to Ben Strader at EFI University in Lake Havasu City, Arizona, for testing on the shop’s Spintron machine. About two minutes into the first run the first of many questions was answered.
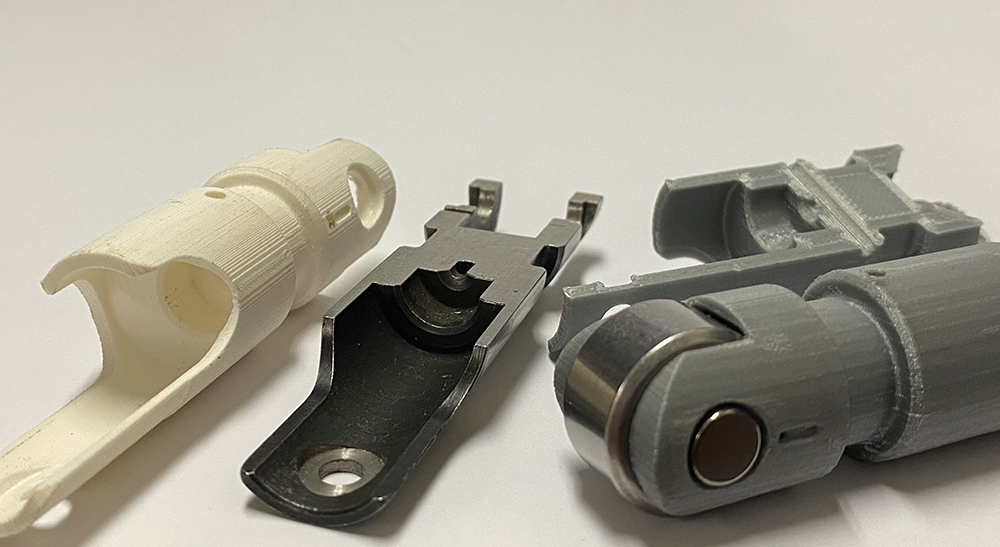
“We could all visually see the issue,” said Godbold. “The valve was so severely out of control and was likely jack-hammering the rocker on the valve stem.”
“Yes, we could clearly see the loft was uncontrolled and bouncing on the nose of the camshaft lobe,” added Strader.
A larger, stiffer valve spring would generally be the prescription, but this was Stock Eliminator. Cylinder heads can’t be modified to accept any spring larger than stock. And the camshaft lobe design was also a possible source of the problem.
“There are strict rules to limit total valve lift, which causes racers to want as much area as possible on the nose—think ‘square lobes.’ This is incredibly challenging because the acceleration rates near peak lift—that is, when the lifter transitions from the ramp to the nose of the lobe—can get to be very high. And that makes controlling loft nearly impossible for the springs,” explained Strader.
COMP Cams and Strader have a long history that has cataloged numerous lobe profiles that, when combined with the correct valve spring or other valvetrain changes, will solve most problems.
“Occasionally, when we can’t get just what we want, we ask for Billy to take a swing at a new lobe design,” said Strader. “In this case, Billy came up with a design that gave us a gentle opening ramp with a very aggressive velocity at the .200-inch lift points. It had a lot of area under the curve, but would not have as much speed near the nose so that we could prevent it from lofting out of control.”
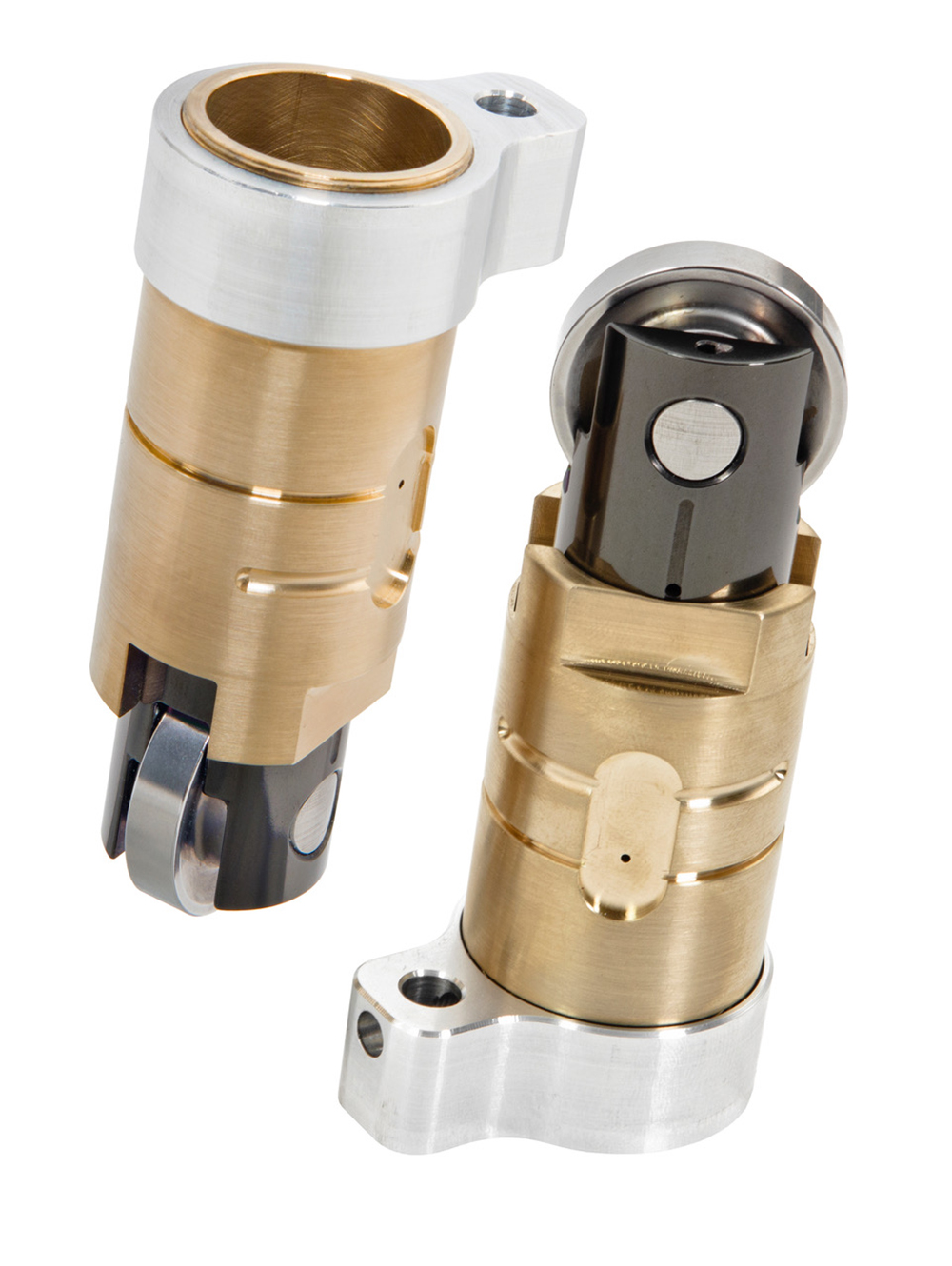
The next step was testing four spring combinations and pushrod setups.
“We then settled on a terrific package that had great reliability and made more power than when they arrived,” added Strader. “This total system approach works really well for us and pairs well to our relationship with Billy and COMP, as we can provide independent testing to look for new ways to solve valvetrain problems.”
Probably nowhere in a pushrod V8 engine built for racing has there been more problems and failures than with the valvetrain. From the lifter to the valve, it’s a delicate linear arrangement that can be compromised by mass, harmonics, and geometry—not to mention cylinder pressure. For a while, engine builders simply made more power than the valvetrain could withstand.
“Cam manufacturers have come to the realization that we can’t destroy the valvetrain to make horsepower,” said John Partridge of Bullet Racing Cams, Olive Branch, Mississippi. “It used to be that the more aggressive you got, the more power you’d make. But there’s a limit if the valvetrain is going to live.”
Shattered lifters, bent pushrods, and broken valve springs were often dismissed as simply the cost of racing. To their credit, sanctioning bodies implemented rules that forced engine builders and suppliers to rethink their strategies. Some have instituted rpm limits to help keep the valvetrain under control. Others are imposing reliability standards. NASCAR teams used to have practice engines and two-lap grenades called qualifying motors. Then on Sunday they would install the race engine. NASCAR now requires teams to used sealed short blocks over multiple weekends. The goal is to reduce the number of engines a team can use during a season by forcing them to improve durability.
Suppliers quickly learned that by understanding the total picture of valvetrain dynamics, reliability would improve, followed by horsepower increases.
“It all started with the Spintron,” recalled Nolan Jamora of Isky Racing Cams, Gardena, California. “We bought the third one off the line. We saw some of the work Richard Childress was doing in NASCAR and applied that to drag racing.”
“You always have failures as you develop products,” added Rob Remesi of Jesel, Lakewood, New Jersey. “You discover the reasons why and make them better, whether trying different materials or different heat-treats. That’s how the lifter has evolved over the years.”
FOLLOWING THE TRENDS
Some definite trends have developed over the years. The industry acknowledges that strength and stiffness is preferred over weight savings on the lifter side of the valvetrain. That has led to massive components, such as lifters more than 1 inch in diameter and pushrods that are 3/4-inch in diameter.
“We just came out with a 3/4-inch pushrod,” said Steve Rhodey of Trend Performance, Warren, Michigan. “It’s wide open to whoever can fit that big a pushrod into the head and block.”
Trend developed the big pushrod by starting with 4130 tubing for the body and machining the tips out of nitride H13 tool steel. The key to making a stronger pushrod came in determining the radius of the tube’s inside diameter where the tip feeds into the body.
“There’s some technology in this radius,” noted Rhodey. “We’re looking at the mating radius, the type of fit, and also the heat-treatment. The pushrod comes in either long or standard clearance styles. The most popular seems to be the long clearance.”
Such a fat pushrod has become necessary in high-powered engines where open valve-spring pressures are in the 1,700-pound range and valve lifts are well north of 1.1-inch. And those numbers put considerable pressure on the lifter. Isky has been leading the movement toward a roller lifter design that uses a bushing to support the wheel axle, compared to more traditional designs that use needle bearings.
“We developed better springs [testing on the Spintron] but we kept failing the lifter,” explained Jamora. “So we came up with the bushed lifter, and that stopped the failures. Of course, that allows you to go even more aggressive on the camshaft and springs.”
Isky is now delivering the seventh version of its bushed lifter following changes in materials and design. Early designs couldn’t retain oil, then engineers discovered that porosity of the metal surface was key to lubrication.
“If the material is too hard, it can’t hold oil,” said Jamora.
Jesel acknowledges the trend toward bushed lifters but continues to promote its needle-bearing designs. “We do offer the customer a choice, but we still prefer needle-bearing over bushing,” said Remesi, who noted that failures from lower-quality needle-bearing versions on the market have alarmed engine builders, especially when pieces of the broken needles are scattered throughout the engine. “We have a custom-made needle; it’s not off-the-shelf. We can control the sizing and heat-treat.”
Jesel offers a full line of lifter designs, including keyway, tie-bar, and roller-guided cartridge.
Meantime, Crower is seeing the market expand for solid roller lifters. “People aren’t afraid to run solid rollers on the street,” said Louis Floquet of the San Diego, California-based company. “A thousand horsepower is average for the street car today. With new materials, CNC machining, and tighter tolerances, everything is more exact.”
Crower is working on a new lifter with select engine builders testing them. “This one is different in how we’re doing the oiling. It should be a pretty trick deal by the time it’s done,” Floquet added.

Meeting a lower price point is what motivated Bullet Racing Cams to develop a new needle-bearing lifter for sportsman racers. “It’s less pricey but still has pressure oiling to the wheel,” said Partridge. “The difference is about $200 per set. We’re also working on our bushing lifters. That’s an ongoing process with materials and design.”
Partridge acknowledged there are differences of opinion when considering bushed versus needle-bearing. “Top Fuel teams aren’t running bushed lifters. That tells me they have a purpose and not for all applications,” he said. “If it’s high quality and used in the right applications, there’s nothing wrong with a needle-bearing lifter.”
DEBATE OVER ROCKER ARMS
Overall, the industry appears to be leaning more in the direction of steel rocker arms versus aluminum models; and there’s also a movement to shaft rocker arms. “That’s where everything is being pushed these days,” said Floquet. “More cylinder heads are being designed for shaft rockers, and stainless-steel rocker arms don’t fatigue like aluminum. With aluminum, you had to adjust the rockers due to the heat cycles. With steel, you can set the rocker and forget about it.”
Crower recently introduced a new Legacy steel shaft-rocker design for the LS that’s available in 1.7:1 or 1.8:1 ratio. “It puts most of the offset into the stand and not the rocker,” said Floquet. “It basically straightens out everything. There’s less stress on the part. And we’re also doing a bushing tip, but a needle bearing is optional.”
Jesel is also addressing the demand for more steel rocker arms but has some words of caution. “Steel is stronger, and aluminum will eventually fatigue over time. Unless something catastrophic happens in the motor, you’re not going to break a steel rocker,” noted Remesi. “Our target when we first started the steel rockers was turbocharged, nitrous, and blower motors where there’s a lot of cylinder pressure that the rocker arm has to open into. There are a lot of applications where aluminum rockers will be fine. But a customer has the peace of mind knowing that a steel rocker won’t break.”
Steel is heavier than aluminum, so there are high-rpm applications where aluminum might be preferred. And there are some engines with unique offsets that pose difficult machining operations to produce steel rockers. Otherwise, the only real downside to steel rocker arms is price.
“They can cost 50% to 100% more than aluminum because the manufacturing process is longer and more involved,” added Remesi.
DIESEL GETS INTO THE ACT
Engine Pro in Wheat Ridge, Colorado, is adding some 275 new part numbers in its next catalog, including new valve springs and performance roller lifters.
“There are also definite opportunities in the midsize diesel market,” said Dave Sutton. “We have a drop-in valve spring to help increase rpm, and we see a strong market for our Nitro Black valve line.”
The exhaust valves in the Nitro Black line are made from Inconel and HNV-3 alloys, while the intakes are constructed from 21-4N steel. All valves are finished with a five-step liquid nitriding process.
“Ours is a proprietary process,” explained Sutton. “Everyone is pushing the envelope for products that will be more durable and last longer.”
QualCast in Nashville, Tennessee, is also targeting diesel customers with a new performance valve kit that includes valves, springs, seals, keepers, and retainers. “It gives the user one part number instead of spending time on the phone or computer looking for the parts individually,” explained Paul Hauglie. “The springs will increase the seat pressure, but you can still use the stock camshaft, and no machining is needed.”
The valves in the kit are from the company’s Black Lightning performance line. The exhaust valves have a higher nickel content to handle high heat, and the intake valves are constructed of 21-4N stainless steel. All the diesel valves have a hardened tip and a black nitride finish.
MAKING LIFE EASIER FOR THE VALVE
All valves are positioned in a guide and rest on a seat. CHE Precision in Newbury Park, California, are veterans in manufacturing those two components along with other valvetrain gear.
“We’ve had one of our best years ever,” Ed Doyle said of the past 12 months. “So, it’s been hard just to keep up with the normal work. However, we do have some new materials that I can’t talk about because they’re for certain teams.”
Doyle did tell us the new valve-seat material came from a trusted supplier, and both discussed the possibilities with the teams. “It offers a lot of heat dissipation,” explained Doyle. “I’m hoping to start introducing that material to more teams as we get more data on it. Right now it works very well in endurance racing.”
Doyle added that he’s also trying a new material with the 410 sprint car engine builders, but all seem to prefer the current beryllium copper alloy.
ENGINEERING AROUND THE SPRING
Howards Cams of Oshkosh, Wisconsin, supplies spec springs to the Racesaver series, which offers a cost-effective rules package to attract more sprint car drivers. There are very specific limits on the valvetrain, including cast-iron camshaft, .842-inch flat tappets, 3/8-inch rocker studs, specific size and weight valves, and valve springs with specific seat and open pressures. There’s also a maximum valve lift .510 inch on the intake and .535 inch on the exhaust. To help racers find a little power with those limitations, engineers at Howards are developing cam lobes to work with those specific springs.
A company spokesperson said Howards Racing Cams has developed a new family of lobes, noting the ramp rates were tuned to control harmonics with the Racesaver spring.
This effort truly confirms a delicate balance between all valvetrain components, yet there is a synergistic cooperation between them. Spintron testing can confirm how little changes have a huge effect on one or more other components. Sophisticated engine simulation programs are also helping engine builders find the right combinations.
“Eventually, we learn what to stay away from and what we can live with,” concluded Bullet Racing Cams’ Partridge.
SOURCES
–
Bullet Racing Cams
bulletcams.com
CHE Precision
cheprecision.com
COMP Cams
compcams.com
Crower Cams
crower.com
EFI University
efi101.com
Engine Pro
enginepro.com
Erson Cams
pbm-erson.com
Howards Cams
howardscams.com
Hylift Johnson
toplineauto.com
Isky Racing Cams
iskycams.com
Jesel
jesel.com
QualCast
qualcast.com
Trend Performance
trendperform.com
SIDE BAR
PARTS FAILURE OR CLUMSY INSTALLATION?
Over the past few years, valvetrain failures have led to vast improvements in quality and design. However, Jack McInnis of Erson Cams in Louisville, Kentucky, believes manufacturers and suppliers shouldn’t shoulder all the blame.
“Many times, a valvetrain failure may result from inattention to detail rather than the component itself,” McInnis said. “One of the problem areas we’ve heard questions about concerns top-end oiling issues when running a solid roller cam. It’s important to check for proper clearance between the lifters and lifter bores. Also, pre-assemble to make sure the oil feed on the lifter is lining up with the oil galley in the block.
“Proper clearances are critical because the lifters’ oil feed is not in constant contact with the oil galley. Pre-assembly checking can reveal potential problems when the lifter oil feed is out of alignment with the galley,” he continued. “This can happen with reduced-base-circle cams causing the lifter to ride lower in the bore, or conversely, when larger cam journals are employed causing the lifter to ride higher in the bore. It may be necessary to use lifters designed for these applications and/or bushed lifter bores to correct the alignment and ensure adequate oiling.” —Mike Magda