PRI Tech: Ford 9-Inch Third-Member Prep
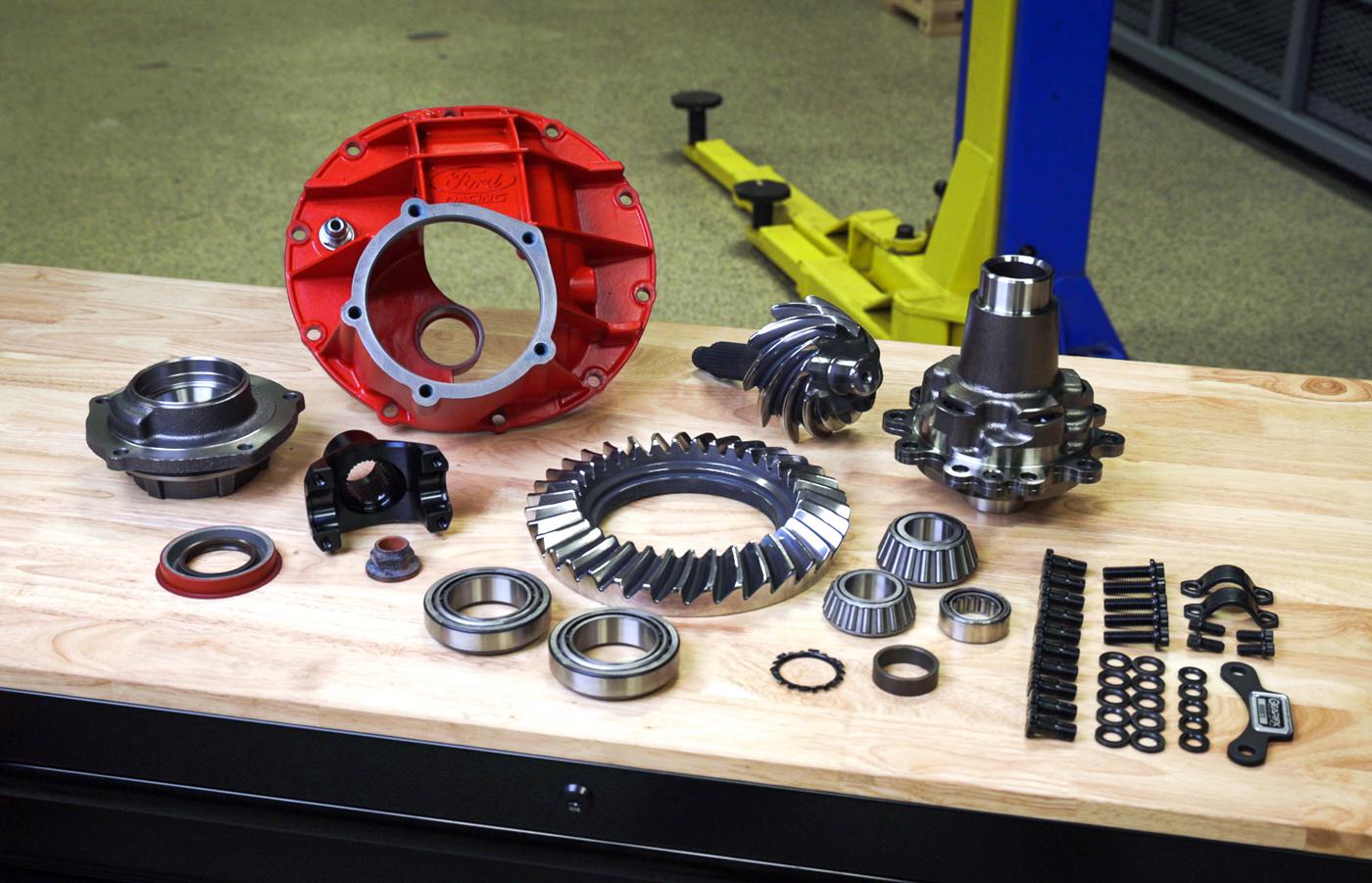
Preparing a Ford 9-inch rearend typically starts with the third member, which houses most of the rearend’s vital components, including the ring-and-pinion gears and differential. By choosing the right combination of these parts, racers can tailor their 9-inch for practically any type of motorsports segment.
With effective prep, the Ford 9-inch rearend can be used for just about any form of motorsports. Getting that ideal setup starts with its third member and using the right components for the job at hand.
The Ford 9-inch is the most widely used rear-axle assembly for practically any form of racing in rear-wheel-drive vehicles. The reason for that is simple. These proven units have an unrivalled combination of strength, weight, and reliability that makes them effective in wildly different applications. The tremendous aftermarket support developed for the 9-inch over decades has made them even more adaptable.
At the core of the wide-ranging prep choices available for a 9-inch is the center section. Unlike many other rearend designs, the Ford 9-inch has a removable third member, which holds the ring and pinion and differential in a tidy, easy-to-remove housing. This feature not only makes the 9-inch simpler to service, it also adds to this rearend’s adaptability. By selecting different third-member housings and fitting them with the correct components, the rearend can be tailored precisely for each type of racing.
When setting up a Ford 9-inch third member for racing, cars tend to fall into one of two categories: those that turn and those that don’t. By that, we’re referring to road race or stock cars and drag cars. Each has very specific parameters for third-member preparation.
Drag Racing
Cars used for drag racing go really fast for very short bursts. The rearend needs to handle an incredible amount of shock load when the driver dumps the clutch or leaves off the trans brake from the line. But then after that, the rearend just needs to get the car to the end of the track. There isn’t much heat buildup.
That lack of heat in a drag car rearend allows for a wide range of material choices to manufacture the third-member case. Iron is still a popular choice, but aluminum cases are definitely worth considering. Granted, aluminum cases don’t hold up well in prolonged high-heat environments, but that’s not an issue in drag racing. The car is just blasting down the quarter- or eighth-mile and then loping back to the pits on the return lane. And the weight savings of aluminum is definitely an advantage.
The next component to consider is the differential. Drag racing differentials have evolved over the years due to the rise in popularity of drag-and-drive events. Traditionally, drag racers have used spools, since going straight as fast as possible is the main priority. But with the introduction of street driving in the form of drag-and-drive events, many customers have switched to a traditional locker or a helical gear-type limited slip, such as the Eaton Truetrac or Strange S-Trac differential. These helical differentials allow for docile street manners and consistent, reliable traction on the track, while still handling the extreme abuse that comes with hard launches on a prepped surface.
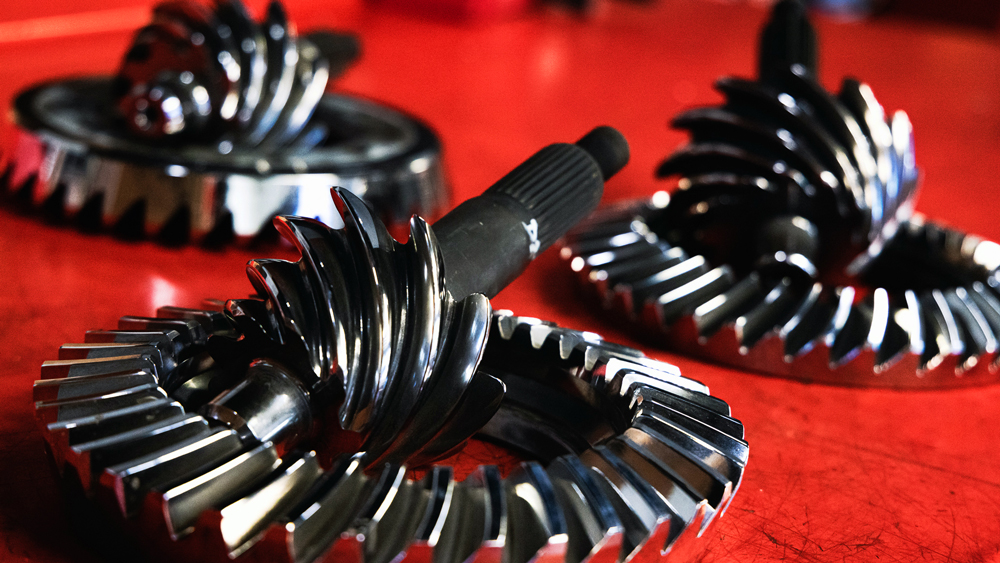
There are strength choices between differentials, and horsepower is only part of the story; tire size and transmission type also play a significant role in deciding which differential to use. We recommend the Eaton Truetrac in 31-spline up to 1,000 horsepower. If the customer plans to use a trans brake, manual transmission, or drag radials, we prefer to upgrade to 35-spline for anything over 800 horsepower. At the 1,200–1,400 horsepower mark we recommend the Strange S-Trac, again in 35-spline. If the car is strictly for track use, we typically use a spool, as there’s no need for cornering manners.
That said, there’s a lot of misinformation out there. In our experience, rearend knowledge is built primarily on word-of-mouth. Many customers call in asking for a spool or old-fashioned locker for a street/strip combination. While these work, the road manners leave something to be desired. Modern helical-style limited slips are a great option for cars that run drag-and-drive events as they provide excellent drivability while still handling the extreme abuse of drag racing.
Ring-and-pinion sets are always an important consideration for drag cars, too, and they become particularly crucial over about the 1,200 horsepower level. Again, that number isn’t a rigid standard—cars that leave the line particularly hard for any number of reasons may find that cutoff to be even lower. Vehicles used purely for drag racing at these higher levels of performance typically run a Pro gear. This type of ring and pinion is made from a softer base metal—typically 9310 steel alloy—and heat-treated specifically to absorb high impact shock loads. Pro gears are less brittle, so they can absorb much higher shock loads than standard ring-and-pinion sets. The downside to Pro gears is that they don’t take prolonged loads well at all—they’ll fail relatively quickly when used for street or dual-purpose cars.
Road Racing & Stock Car
Cars that turn while racing present their own unique challenges in 9-inch third-member prep. In these applications, shock loads are far lower, which puts less strain on the ring and pinion and other components. But unlike drag cars, road race and stock cars face vastly more heat buildup, especially in long endurance events. That heat buildup becomes an important factor when choosing a third-member case. For one thing, it pretty much eliminates aluminum cases from consideration. When aluminum cases get hot, they lose their dimensional stability. This throws the very precise relationship between the ring gear, pinion, and other components totally out of whack, which typically results in the rearend eating itself.
For this reason, iron remains the best material for road racing and stock car third members. It’s not the lightest, but it can survive the punishment of even the longest endurance events. For those who do want to shed some pounds, the Ford HS case is a good option. It’s an investment-cast steel case that weighs about 8 pounds less than a typical nodular iron case, and it can handle just about anything below 1,000 horsepower—more than enough for the vast majority of road race and stock car setups.
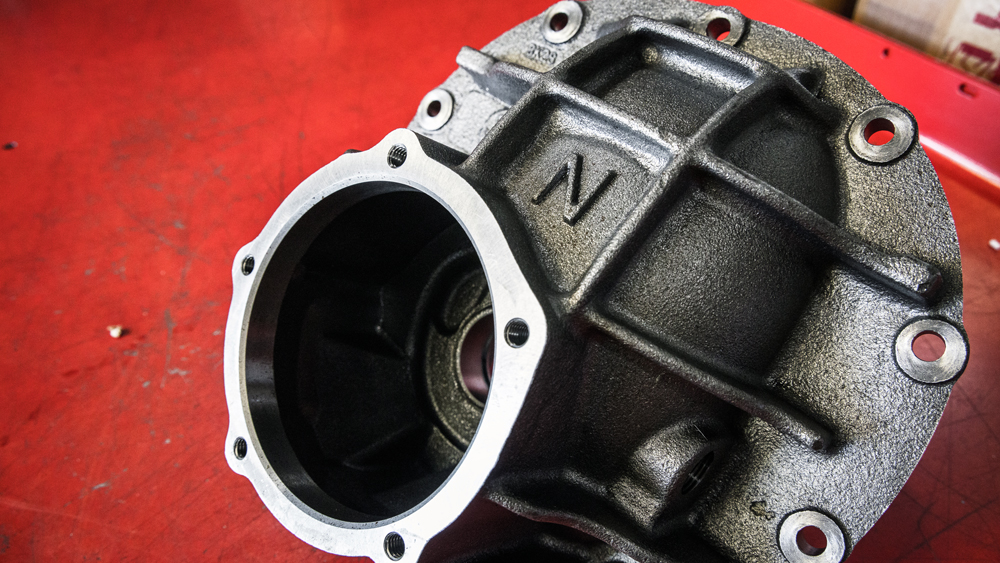
Ring and pinion choices aren’t as critical for road racers as they are for drag cars, due to the lower shock loads encountered. Of course, there’s always a megabucks alternative. For example, NASCAR teams typically use very exclusive ring-and-pinion sets that are optimized to provide minimum friction at the exact speeds they’ll be sustaining on any given track. These gears are priced accordingly—around $7,000 a set. But for normal road race or stock car teams, just about any high-quality ring-and-pinion set will work. Worth noting, however, the quality of almost all mass-produced ring-and-pinion sets has diminished drastically in the last couple of decades. But the difference is mostly in how noisy they are, rather than in their overall strength, which is what really matters on a race car.
When it comes to differentials, road racing and stock cars are completely different from drag cars. Once again, consistent traction is the name of the game. A spool isn’t optimal, as it will always resist direction changes. Alternatively, an open differential will allow direction changes but won’t transfer power reliably when one corner loses traction. Most, if not all stock cars use a traditional locker differential. Lockers are great for consistent traction when needed, yet they still allow the differential to unlock when turning sharp corners.
In road race applications, many racers prefer a clutch-type limited slip or helical limited slip. Two common differentials in road racing are the OS Giken SuperLock and Eaton Truetrac. The OS Giken is a tunable clutch-type limited slip that allows the user to tailor the differential to course conditions and driving style. The downside is that with repeated racing, the clutches will wear and need to be replaced over time. The Eaton Truetrac is a common choice for weekend warriors; it provides reliable grip when traction is inconsistent but remains budget friendly as there are no clutches to replace.
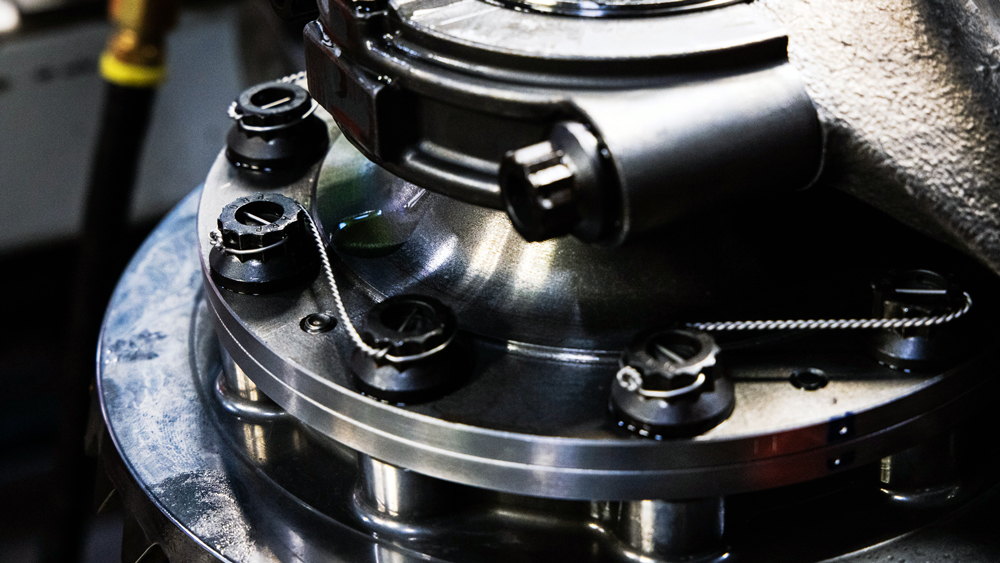
Choosing the wrong differential can cause inconsistent cornering characteristics and result in slower lap times. In extreme situations, incorrect differential choice can result in internal damage or even an accident. A perfect example would be in a dedicated road-course situation with a differential that can’t handle wheel hop or sudden shifts in chassis loading, such as when the car hits the rumble strips in a fast corner. These situations unsettle the suspension and can cause the inside tire to lose traction. If the driver doesn’t lift, this rapid loss and regaining of traction under power can damage the differential. This is where a locker or clutch-type differential can benefit the dedicated racer.
By following these recommendations, Ford 9-inch rearends can be as at home on a drag strip as they are on punishing laps of endurance racing. The key is in proper setup. This tremendously adaptable rearend design can do it all if the right components are used for each application. When prepped effectively in this way, these robust units are more than up to the job race after race, season after season.
Lucas Hardin is the drivetrain technical specialist at Detroit Speed & Engineering, a division of Holley Performance Products. In his role at Detroit Speed, Hardin works with a team of master technicians to help racers in all forms of motorsports select and set up drivetrain components. To learn more about Detroit Speed rear axle assemblies, visit the company’s website at DetroitSpeed.com.