Rock Steady
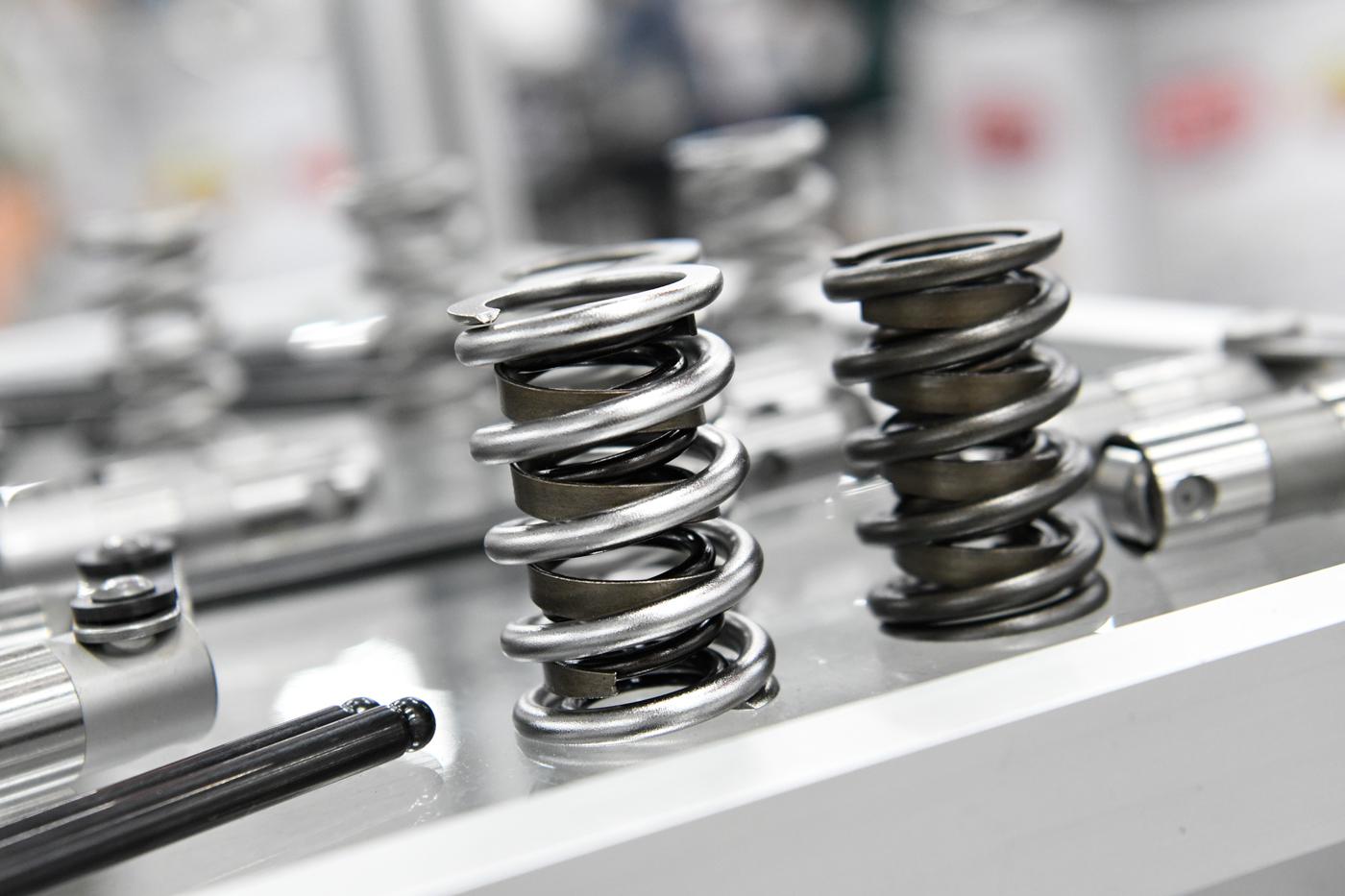
Consistency and dependability are driving today’s valvetrain development as elevated boost levels continue testing the limits of these hard-working components.
Turbos, superchargers, and copious amounts of nitrous have been creating chaos within the pushrod engine’s valvetrain for a couple of decades now—especially at the drag strip, where outlaw and small-tire classes have mushroomed in popularity under promoters who have written generous engine rules with few limits on boost.
Manufacturers of valvetrain components are rapidly diagnosing those problems with a great deal of success and responding with improved parts that not only survive in these high-stress environments but support engine builders who promote these high-boost strategies.
For example, the custom shop at Jesel in Lakewood, New Jersey, had a drag racing customer running a spread-port-style cylinder head on a big block Chevrolet with a pair of turbochargers.
“He wanted to improve the valvetrain stability. He was running a typical spread-port rocker system that consists of individual intake stands with aluminum rockers and individual exhaust stands with steel rockers,” explained Rob Remesi.
Jesel engineers determined that the top of the heads could be milled flat, then they designed a new one-piece rocker stand with additional mounting points that increased the overall clamping force on the stand.
“Along with the new stand, we re-engineered and optimized the valvetrain geometry by rotating the rockers slightly to take out some of the offset typically needed with the spread-port intakes,” added Remesi. “We anticipate this new setup will greatly enhance high-rpm valvetrain performance.”
This manner of problem solving and performance upgrades for boosted engines has been in play for some time.
“Many years ago, NHRA Top Fuel and Funny Car ran 11/32-inch exhaust valves for years until they simply couldn’t any longer under the demands of these nitromethane beasts,” recalled Trip Manley of Manley Performance, Lakewood, New Jersey. “Then we came out with a purpose-built, 3/8-inch stem Inconel exhaust valve that has since set the gold standard for years.”
Finding new materials, especially from within the aerospace industry, has benefited racers and manufacturers.
“Everything we’re doing right now is to get a material that can not only take the heat that these engines are putting out, especially turbo motors,” explained Ed Doyle of CHE Precision in Newbury Park, California, a manufacturer of valve seats, guides, retainers, and more. “But also making them not so much hard as tough. There’s a big difference. Everybody gets toughness and hardness misconstrued.”
Exhaust Side
In sampling a wide range of valvetrain manufacturers about developing parts for high-powered engines, the exhaust side seemed to draw the most attention. With high boost, cylinder pressures are enormous, and opening the exhaust valve can be a tense operation—and it starts with the camshaft.
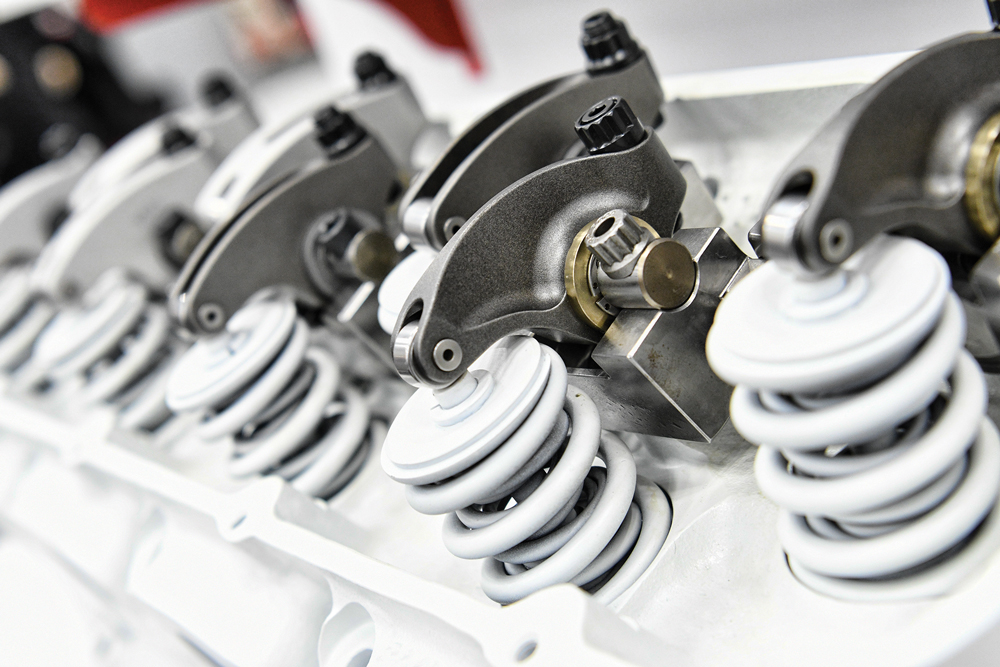
“With heavy boost or heavy nitrous, you can’t just smack that exhaust valve open,” said Lance Stillwell of Erson Cams, Louisville, Kentucky. “Really, you need less acceleration on the cam lobe. You want to creep it open to start letting the pressure out. That relieves the pressure on the rocker arm and the rest of the valvetrain.”
“The real valve event we are concerned about, the one that is impacted the most, is exhaust valve open (EVO),” concurred Chris Potter of Edelbrock, Olive Branch, Mississippi. “The worst offenders are nitrous and rev limiters. For the nitrous cars, especially closer to peak torque, they will run very little timing, which means max burn occurs that much further ATDC (after top dead center). They are usually softening the timing to keep that cylinder pressure from lifting head gaskets and/or trying to keep the rotating assembly alive. Softening the timing around peak torque is a way of reducing cylinder pressure to keep these parts alive.
“It’s extreme applications like this where we can see the need for a 9/16-inch pushrod,” continued Potter. “It doesn’t necessarily have to do with spring pressure but trying to keep system stiffness at peak lifter acceleration as the camshaft opens the valve and begins to normalize the pressure in the chamber.”
In the early days of hot rodding, engine builders assumed that reducing the weight of all valvetrain components would benefit the engine and increase rpm. However, as valve lifts and spring pressures increased, the pushrods were flexing enough to dramatically disrupt valve events and introduce unwanted harmonics. In fact, when some engine builders installed larger and stronger pushrods, they had to completely rethink their camshaft strategy because so much flex was taken out, and the reality of the cam design was exposed.
“We continue to see larger cubic-inch engines move to bigger diameter and heavier wall pushrods to help reduce deflection in the system,” said Mike Panetta of Race Winning Brands, which is the parent company for pushrod manufacturer Trend Performance in Warren, Michigan.
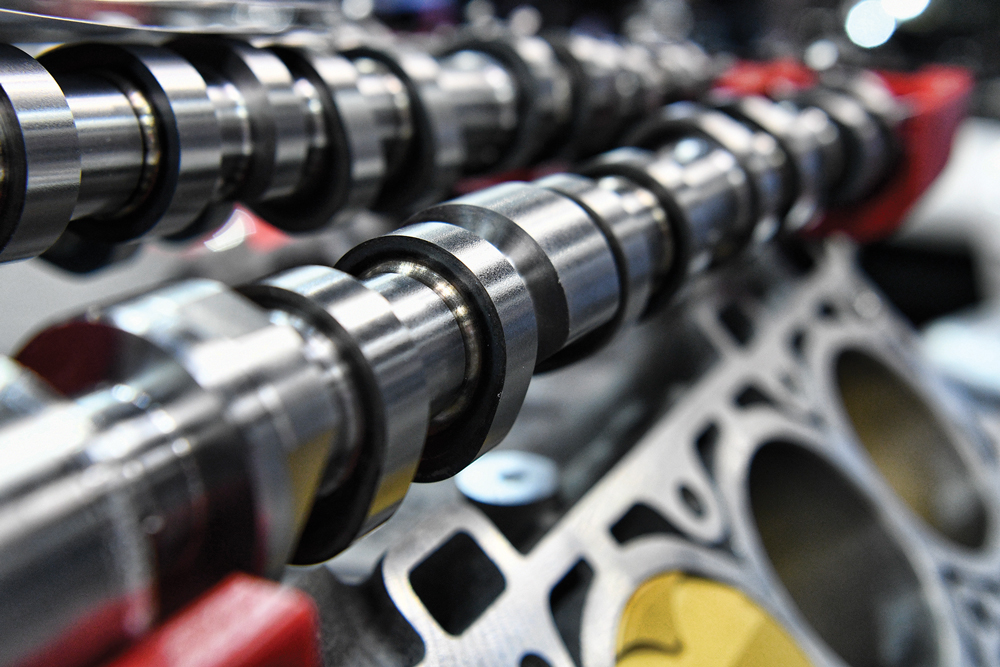
“Flex will always equate to a change in duration and overall lift. Flex is inevitable, therefore measuring it can be very important in a combination where you’re trying to get every ounce of power you can,” added Luke Brandt of Howards Cams, Oshkosh, Wisconsin. “You might find that the cam may need to be slightly bigger just to compensate for the flex. In a nutshell, flex is generally unwanted, but it’s more important to control it over trying to irradicate it completely.”
There are also schools of thought that not only accept a little pushrod flex in the valvetrain but use it to an advantage.
“Unknowing flex is different than unwanted flex,” said Derek Dahl of Victory 1 Performance, Mooresville, North Carolina. “Sometimes, for longevity, a small amount of bend is needed. Beefed-up one-piece rocker stands, improved materials for stiffness in the entire valvetrain all add up hopefully to a recipe of success.”
Under the pushrod, the lifter has also gained weight and increased in size over the years to provide extra strength to the bottom side of the valvetrain.
“We advise the customer to go to the larger lifter-bore diameter. When you go from an .842-inch diameter lifter to a .937 in the same engine, you go from a .750 wheel to an .850 wheel,” said Guy Aguayo of Crower, San Diego, California. “We have a very strong American-made lifter to begin with, but going to the bigger lifter bore makes the body larger and gives you a larger pin and wheel for added strength.”
In the lifter market, bushings on the wheel axle are replacing needle bearings in many high-stress applications that use solid lifters.
“At any one time in the needle version, you’re running on three of the needles, at most,” explained Nolan Jamora of Isky Racing Cams, Gardena, California. “If you’re running a bushing lifter, you are running on the oil band, which you get about 300–400% more pressure load-bearing capability and it’s spread over a wider area.”
Jamora said many needle failures start with a crack in the outer race. “That’s because going up the ramp the race is vibrating up and down or going in and out and getting oval-shaped. The main pin will slide between the needles’ contact with the outer race and crack it.” He noted that Isky has offered a bushing style lifter for 15 years and is now on its seventh generation.
Perhaps no component in the valvetrain has received more improvements and design changes over the past couple decades than the valve spring. New materials and manufacturing tricks—along with new designs like beehive and conical—have given engine builders more options in helping stabilize the valvetrain by reducing valve float and other unwanted valve action.
Valve springs have also become much heavier in terms of load on the seat and “on the nose,” or at maximum lift. Springs can be rated at 400–500 pounds on the seat and well over 1,000 pounds at open load. They’ve also grown in size as total valve lifts are more than 1.2-inch in Pro Stock and other similar classes.
The formulas for selecting valve springs are different for boosted and nitrous engines compared to naturally aspirated. “It depends on the installed heights because we want to be in the coil-bind range,” said Jamora. “The sweet spot is .070-inch for most, or .060 to .070. Of course, we have racers that will be within .020 or .030 but, I mean, everything is going to go to coil bind. I was explaining to an engine builder, the spring just doesn’t stop at that line. It goes way past so that every spring is coil binding. What you’re setting at the coil bind is just basically the limit of where it’ll bounce off each other and not crack.”
Intake Side
The amount of boost an engine builder is planning also plays a key role in determining the valve spring package, especially on the intake side.
“With real high-boost pressures, the backside of the intake valve is really important because that’s under a constant static pressure, no matter what. So it diminishes with the seat pressure but not a lot,” said Jamora. “What we’re trying to decide is, how much does it drop or diminish under that pressure? A typical valve diameter is around two inches. That’s about three square inches of area on the back side of the valve. If you have a spring that’s 300-pound seat pressure, a good rule of thumb is to deduct 10 pounds per square inch, which will be 30 pounds at maximum load. So that means that even though you put the spring in at 300 pounds seat pressure, it’s really only 270 because of that back pressure on the inlet valve.”
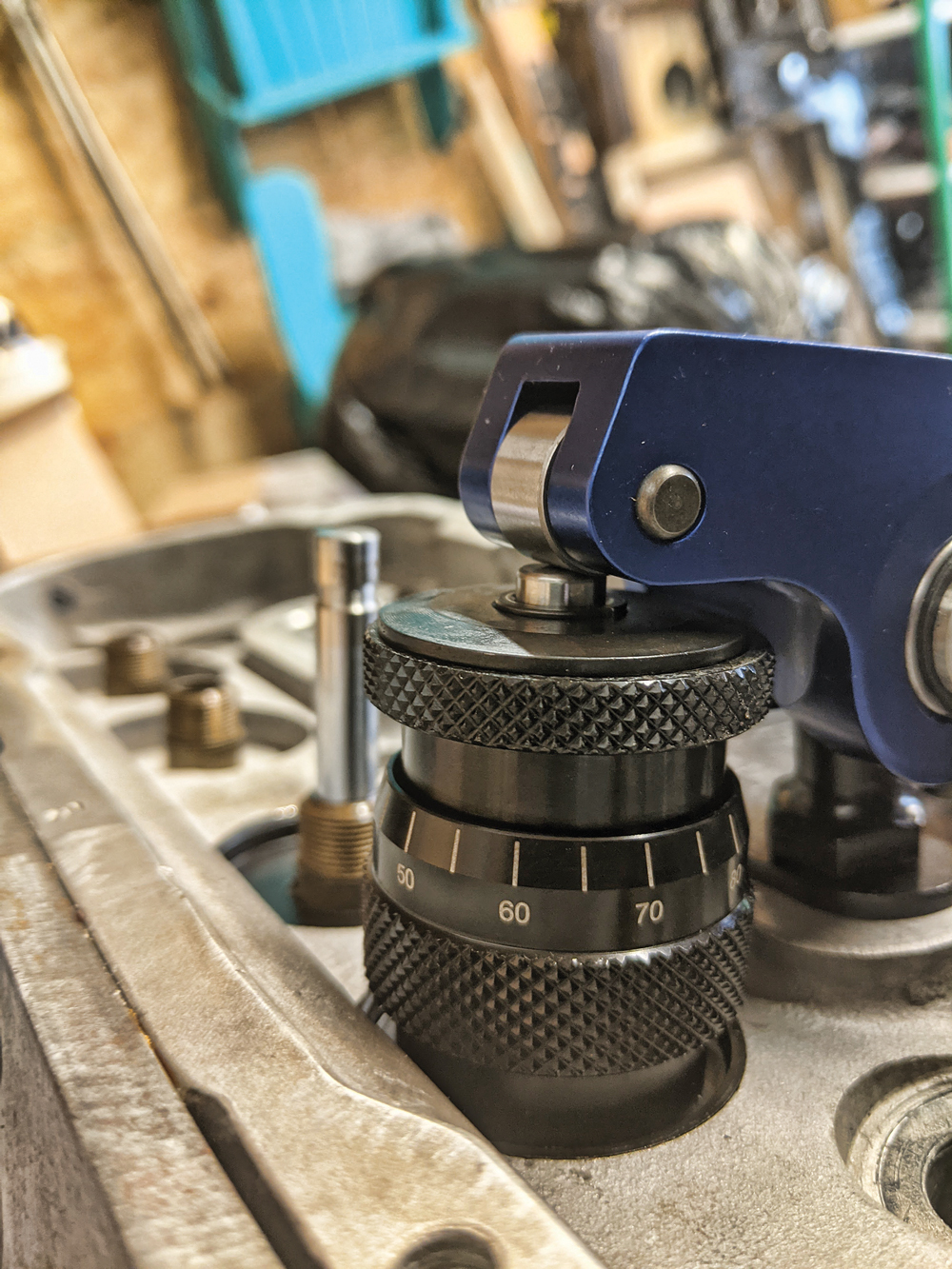
Not only can boost slightly unseat the intake valve, it makes it more difficult to close the intake valve. “A lot of guys with diesel engines, they may not have a lot of spring on the seat but they’re running these huge turbos and 90 pounds of boost,” warned Stillwell. “So it’s hard to get the valves shut. When you’re bouncing valves, you’re bending valves.”
“Added boost can also absolutely require more spring seat pressure on the intake side in order to keep the valve controlled and closed,” added Manley. ”To that end, we built some better springs for the domestic late-model markets knowing these customers would be adding turbos and superchargers.”
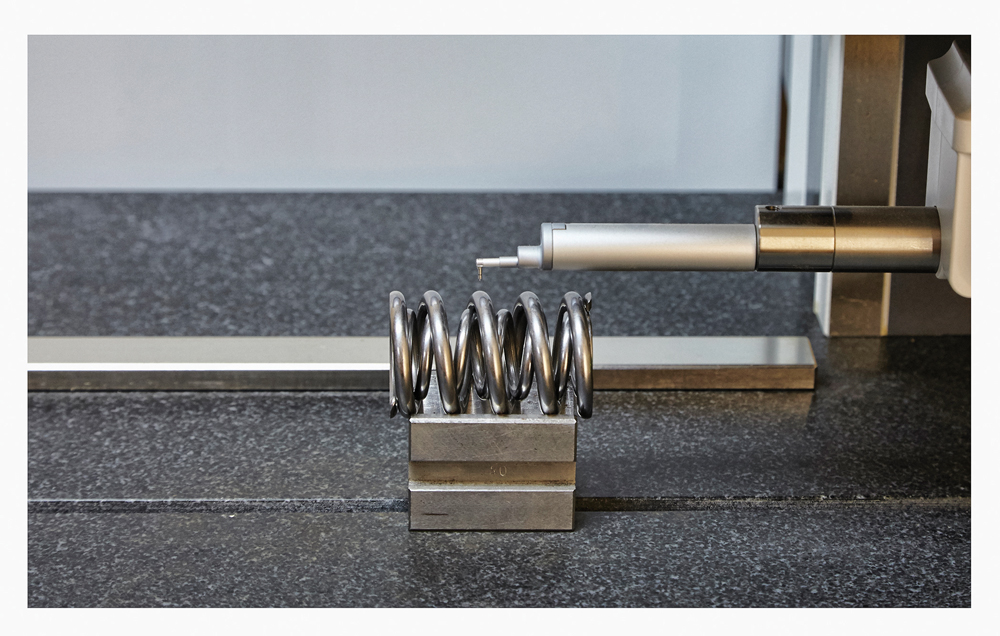
Package Deal
Still, much of the concern when designing a valvetrain package is focused on the exhaust side, again because of the increased cylinder pressure. An unlikely culprit could be traction control. One method of reducing wheel spin is pulling timing to reduce cylinder pressure, as opposed to closing the throttle.
“Late timing is like creating work or power and not taking advantage of it,” explained Potter. “Obviously, we can’t take advantage of that power, otherwise we wouldn’t need the traction control. Either way, the delayed timing creates a later burn that EVO must fight. In these cases, not only is EVO fighting opening, but in some cases, it also must fight a significant buildup of pressure in the exhaust, such as a backfire when unburnt fuel ignites. This is where a two-step rev limiter will make many valvetrain designers cringe. That explosion outside of the combustion chamber can force the exhaust valve open, creating separation between the valve, rocker, pushrod, lifter, and cam lobe. The crash when these come back together can be incredibly detrimental. We’ve definitely had to step up and design components that can handle this abuse.”
Because of the high cylinder pressures in boosted engines, many builders have already switched from aluminum to steel rockers on the exhaust side—and some use steel across the board. Again, valve size is critical to overcoming those pressures.
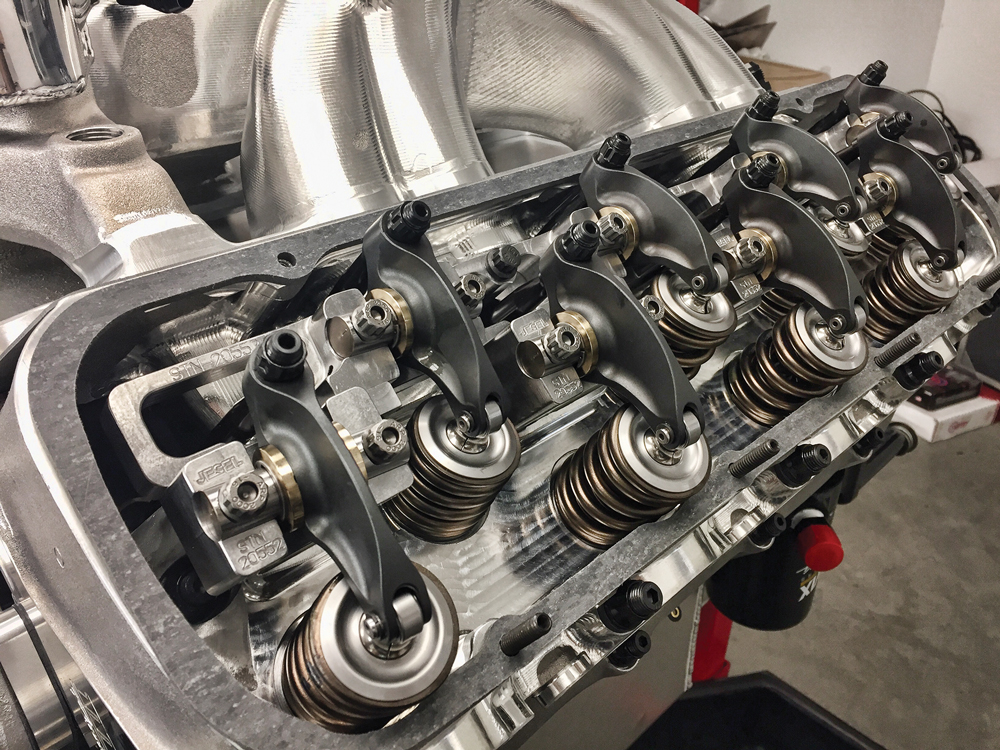
“Steel rocker arms obviously contribute to the biggest gains in valvetrain stiffness,” observed Remesi. “If you have a turbo engine that develops 1,500 psi of cylinder pressure and you are using a 1.800-inch diameter exhaust valve with a surface area of 2.54 sq./in., it would take about 3,800 pounds of force to start to open the exhaust valve. That is why steel rockers are so important on the exhaust side of turbo/nitrous builds. Our Pro Steel BBC 1.650-inch pivot rocker is approximately 20% stiffer than its Pro Aluminum solid-body equivalent.”
Increased spring pressures compel other equipment manufacturers to respond by improving their products, such as spring retainers and rocker-arm trunnions.
“We’ve made everything a little bit beefier, still trying to keep the weight the same, which is next to impossible. With minimal weight change, we’ve tried to make everything stronger. Our trunnions are proprietary material specifically for the LS,” said Doyle, adding that little race tricks like 55-degree valve-seat angles can wreak havoc on valve seats. “We’ve especially worked on materials. When you start increasing valve angles, the unit pressure goes through the moon. Take your 1,000-pound over-the-nose spring and bounce on a 55-degree angle, and the unit pressure is astronomical. So, we worked on materials that could handle that kind of abuse.”
Looking Ahead
Looking to the future, valvetrain manufacturers will be watching for problems and reassessing component strategy for the different racing disciplines.
“Honestly, it depends on the market. There really isn’t a one-shoe-fits-all answer for this question,” said Manley. “For instance, I would say that the domestic late-model market has seen high demand for twin turbos as a way to achieve big power. On the other hand, there are plenty of classes, from Pro Stock to dirt late model, that do not allow power adders. Engine builders putting together naturally aspirated motors must figure out creative ways to eke out more power without the benefits of a turbo, blower, or nitrous kit.”
“To state it plainly, turn up the boost,” said Brandt. “Combinations these days are going ridiculously faster with half of the cam. Rpm always makes power, but when you’re confined to a budget, like most guys are, making power to the point that rpm falls just above peak torque on the shift is really all you need. Boosted combos don’t need large valve lift. It’s not uncommon to see very fast, boosted combinations running low .600 or less lift, and durations in the high 220s to low 240s at .050-inch lift. This has made it easier to get combinations to live, and in some situations, requires far less spring pressure.”
One trend that is welcomed in the boost industry is that engines are being purpose-built from the ground up with turbos, nitrous, or superchargers in mind.
“Recently the term ‘power adder’ is used less and less as people are realizing it’s difficult to add power to a combination and get the performance they need with the parts they have,” said Dahl. “What most builders have now is a stable base that is consistent and trackable. If they start from the same point every time, it’s easier to pinpoint the problems and find solutions. Every part has its frequency, and the difference between motor carnage and winning is how far you’re allowing the part to move versus how far it needs to move.”
“We want horsepower,” concluded Potter. “The easiest way to get us there will win.”
SOURCES
Callies Performance Products
callies.com
CHE Precision
cheprecision.com
COMP Cams
compcams.com
Crower
crower.com
Erson Cams
pbm-erson.com
Howards Cams
howardscams.com
Isky Racing Cams
iskycams.com
Jesel
jesel.com
Manley Performance
manleyperformance.com
Race Winning Brands
racewinningbrands.com
Trend Performance
trendperform.com
Victory 1 Performance
titaniumvalve.com