Printed For Speed
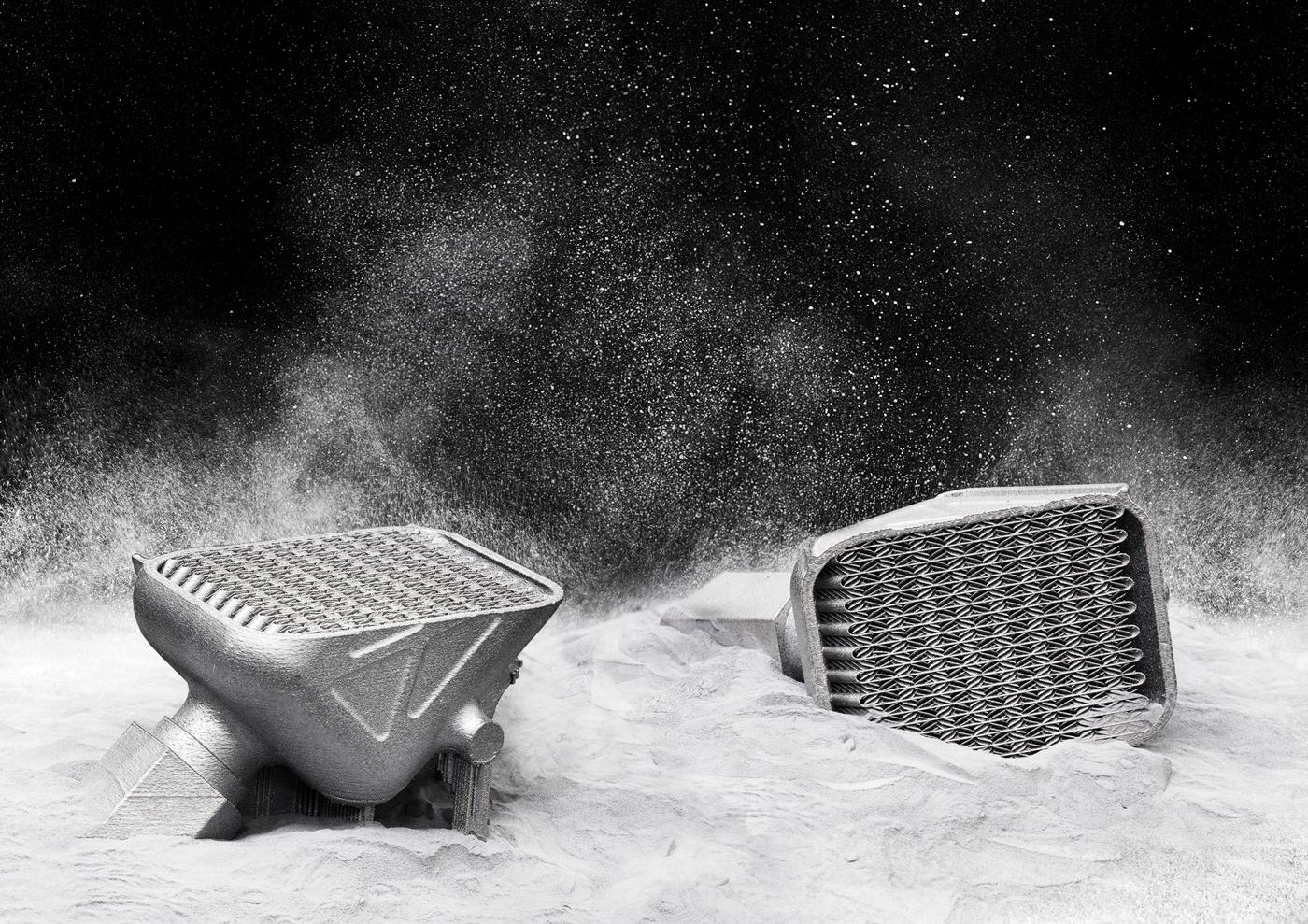
Photo courtesy of PWR
Additive manufacturing is presenting fresh, cost-efficient ways to develop and manufacture racing components.
The mid-July summer heat of 2020 was unbearable for IndyCar drivers at the Road America double-header. The new Aeroscreen protection reduced cockpit air circulation, so teams, race officials, and engineers from vehicle designer Dallara collaborated on ways to introduce a fresh-air cooling duct. Time certainly wasn’t a luxury as a pair of 250-mile races was scheduled for the following weekend in the sweltering Midwest.
“I knew several lead people at Dallara, and they reached out to us while I was at the Elkhart Lake race on Sunday,” recalled Allen Kreemer of Stratasys, a manufacturer of polymer 3D printers based in Eden Prairie, Minnesota. “They said a driver cooling duct was needed. We were able to produce 24 of them in 48 hours and distribute them to all of the teams for the next race.”
Dallara had a slight head start by working on the cooling duct with a couple of teams to develop the initial CAD files, including running computer simulation tests. Initial concerns included disturbance at the top of the screen and possible buffeting that might affect a driver’s helmet. Teams were able to mount the ducts on top of the Aeroscreen using existing fastener locations.
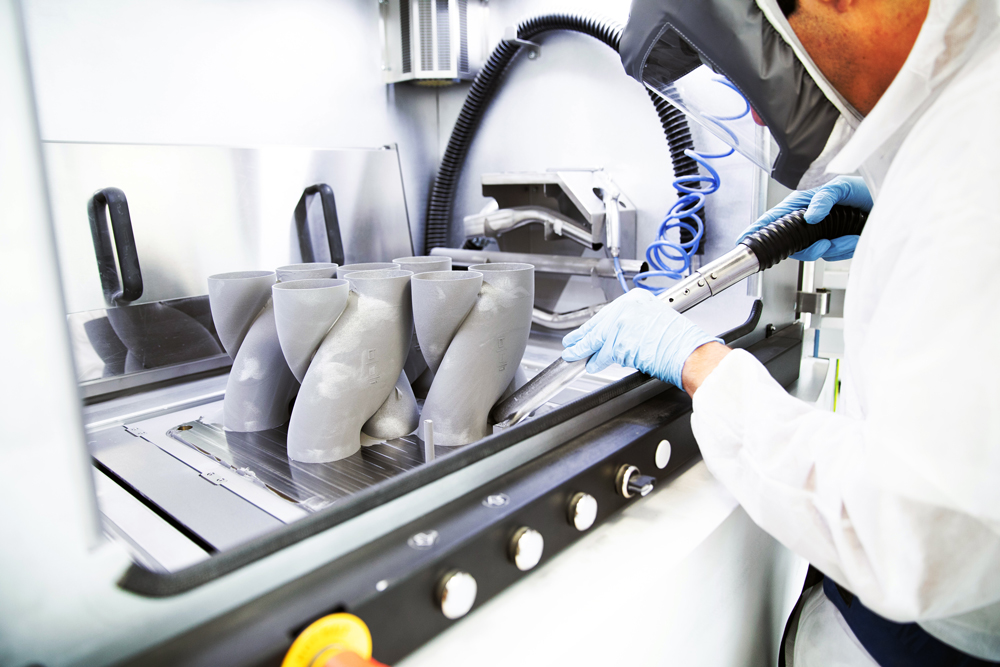
“It actually gave the teams space for a logo or advertising for the in-car camera,” noted Kreemer, who as a former IndyCar mechanic was helpful in finalizing the design in addition to managing the product’s manufacturing.
IndyCar then made additional modifications to the Aeroscreen to manage cockpit temperature before the Indy 500 that August, eliminating the need for the temporary overhead scoop. However, the quick response facilitated by 3D printing demonstrated that additive manufacturing (AM) is arguably the most important disruptive manufacturing technology in motorsports since CNC machines.
3D Printing in Action
Every major race team and aftermarket parts manufacturer relies on 3D printing in some manner for different facets of their operation. It may be used only for rapid prototyping, or with the use of advanced materials—including metals—end-use parts can be printed. Some teams even take 3D printers to the track. However, it’s not just big-budget operations that take advantage of 3D printing.
“I’m a small shop in terms of engine volume, but in terms of performance level we try to aim high,” said Ben Strader of EFI University, Lake Havasu, Arizona, which has a dyno and Spintron for unique engine-development projects. “Even at our level, we are using 3D printing for many things.”
Strader will request custom piston and rocker arm designs in plastic for mockup purposes before ordering the actual part. “We aren’t big enough to justify the expense of owning the machines, but there are plenty of companies like Jesel, MAHLE, and others who offer these services to us,” said Strader, who is working with BES Racing Engines on a 360ci LS engine with a goal of 1,100 horsepower naturally aspirated at well over 11,000 rpm. With an expected valve lift of 1.085-inch, valvetrain geometry is critical.
“We worked with Jesel on multiple iterations of rocker arm design by installing and mocking up the rockers on the actual engine and measuring the pushrod and rocker geometry. This led to several small modifications to the rocker arm adjuster angle to get the sweeps correct near the bottom and top of the lift curve,” explained Strader.
Over at Elite Motorsports in Wynnewood, Oklahoma, 3D printing is also used for mockups. “3D printing allows us to achieve lighter weights, faster manufacturing, and cost saving for mock-up components that simply aren’t possible with standard fabricating and machining practices,” said Scott Woodruff.
“We use 3D printers to make parts for prototypes, test fitting, fixturing components, trim guides, and production retaining parts,” concurred Jason Harding of Performance Design, Auburn Hills, Michigan. “We also outsource 3D printing for things outside of our build window or different types of 3D printing, which are used in development and dyno testing.”
Race shops with 3D printers are producing a wide variety of parts that speed up operations, such as wiring or plumbing brackets, gauge housings, hood vents, brake ducts, switch panels, steering-wheel grips, and much more. In some situations, the design work is already available. The Internet offers generous sources of free standard triangle language (STL) files for brackets, spacers, tool holders, and other helpful products.
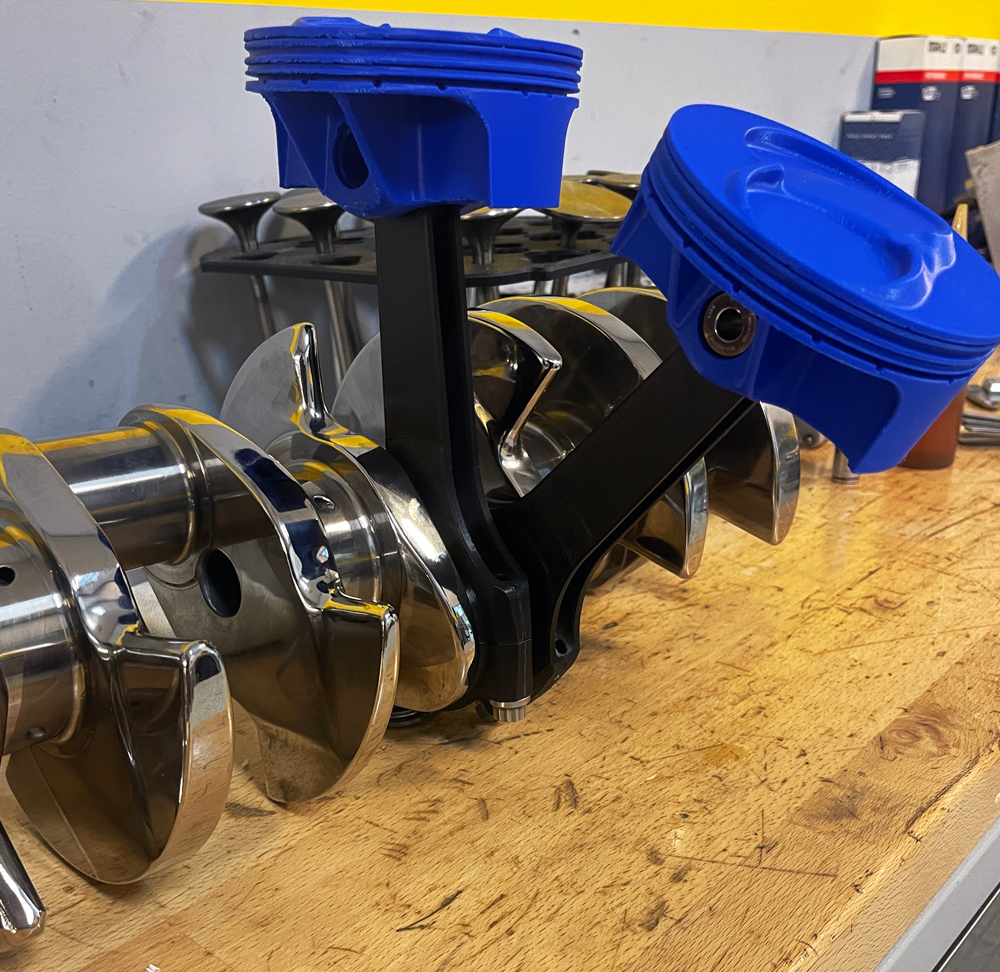
For more intense development work, there are numerous companies that will flesh out customer ideas, draw up the CAD files, and either print out prototypes in-house or source them out. HV3DWorks in Sewickley, Pennsylvania, was formed by Paul Vorbach to support a concours-level automotive restoration shop that often experienced difficulty locating rare or out-of-production parts. 3D scanning, CAD tools, and additive manufacturing allow Vorbach to reproduce many of these scarce components. Sometimes he also helps racers.
“I did some injector stacks for a BMW engine,” he said. “We took the owner’s stock one, modified the design to make them longer, and then printed them. In that case, they were printed out of a nylon plastic.”
Vorbach doesn’t own the printers used to produce the parts he designs “because of all the different disciplines, and the machines are so darn expensive to do one-off parts,” he explained. “But if you work with somebody who knows the various different disciplines, metals, and materials, you can do the design work and then print the parts. The advantage is you can print one, 10, or 20 parts and not lose your shirt.”
Vorbach has seen the cost of metal printing come down in recent years, and there are more opportunities with metal printing—including titanium, stainless steel, and other alloys.
“I would say the metal AM is where we’re seeing the biggest increases in technology. There’s a lot in composites, too, of course,” said Vorbach. “The real opportunity is in making parts lighter and cheaper. You can design to take advantage of honeycomb structures and things like that. Think of holes. In a CNC machine, putting in holes costs money. Once you design something with holes, in additive manufacturing you’re not putting in any material, and it costs you less.”
There are dramatic examples of high-end race teams and automotive companies that are 3D printing end-use metal parts. The $2 million Czinger 21C hypercar is mostly built with parts that were designed with AI software and produced at Divergent Technologies on huge 3D printers.
Critical engine parts such as pistons are also 3D printed. As long ago as 2017, Ferrari publicly discussed printing steel pistons for its F1 team. The alloy may be heavier than aluminum, but design changes can reduce the amount of metal needed. Porsche recently disclosed it was 3D printing pistons for a 911 GT2 RS engine. Not only did the company reduce the weight 10%, but it added cooling ducts that allows oil squirted from below to draw heat away from the crown. Such a feature would have been impossible with traditional forging and machining.
About 10 years ago, Pankl Racing Systems in Austria recognized the potential of AM and invested heavily in 3D metal printing. “We have 10 machines in different sizes, and we try to keep the machines printing the same metals,” explained Christoph Wachmann. “When switching from titanium to steel or aluminum, you have to clean the machine thoroughly to avoid contamination. It’s better to have more machines with separate materials. We have our own HIP [hot isostatic pressing] chamber to reduce porosity. And we have four or five choices of heat-treatment options.”
On a recent project, Pankl helped a race team reduce engine weight by 3D printing a thin-wall aluminum oil tank that is attached directly to the cylinder block, a set of titanium fuel rails, and coolant fixtures. Pankl also 3D printed Inconel header flanges and exit tips for the exhaust system.
“We can do crankcases, it just depends on how big the engine is,” said Wachmann. “We are also doing turbocharger housings that could be titanium, aluminum, or Inconel.”
And remember those Aeroscreens for Indy cars mentioned in the beginning? Pankl 3D printed those from a titanium alloy. Five separate pieces are printed, then welded together.
Technology Advancements
The potential to expand metal 3D printing involves a number of technology advancements, including the metals themselves. New alloys are being tested, and the feedstock powder itself is being produced with more consistency to improve the resolution of the finished product. The machines will get bigger with more lasers used to speed up the process, and the software will continue to improve. Finally, testing will validate material properties to satisfy structural demands.
“[Printed materials] are consistent and can be used in FEA,” said Wachmann, noting that early iterations of the previously mentioned lightweight oil tank developed a crack from vibration. “This crack happened three or four times in exactly the same spot. The root cause was stress from vibrations that we didn’t know about up front in the design stage. But the crack was always in the same spot, which for me is an example that the metal is consistent. Then we made a design iteration, and it stopped cracking.”
Another motorsports supplier moving forward with 3D metal printing is PWR, which is based in Australia and has a plant in Indianapolis, Indiana. The company designed a heat exchanger concept and tried it on 20 different printers before choosing one from Velo3D.
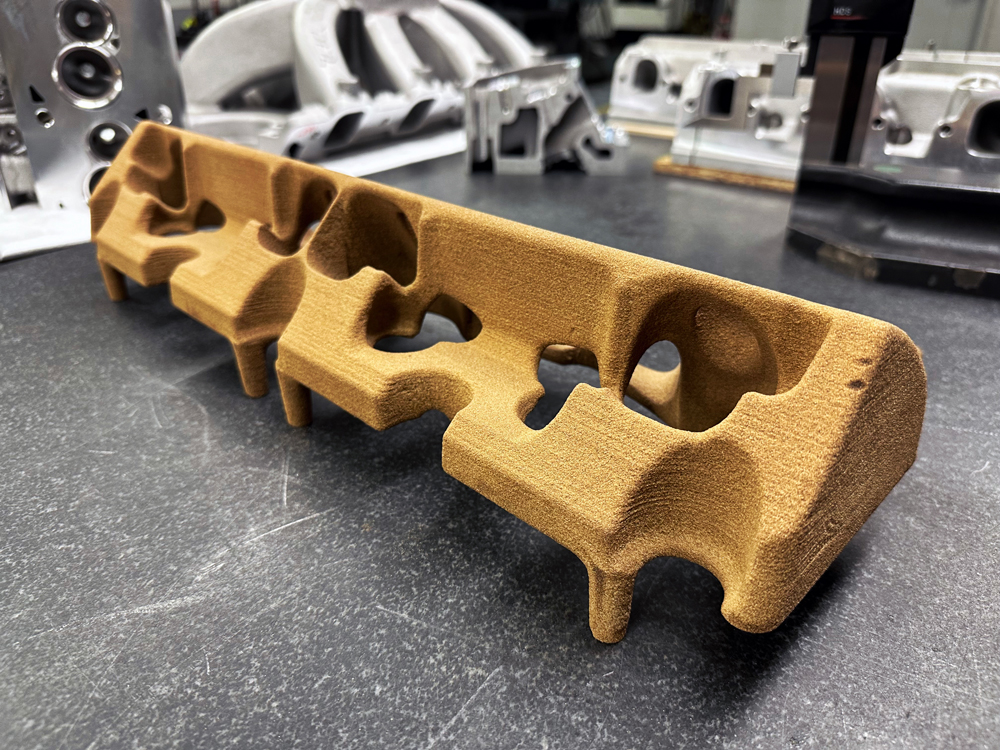
“For us, machine capability with additive wasn’t about just producing the fastest nor the cheapest part,” explained Matthew Bryson. “Obviously, you’ve got to be cost-competitive with everything you do. But for us, it was about exploring the maximum potential of the technology to try to produce components that others couldn’t.”
One of the current strategies at PWR is to integrate 3D-printed pieces with existing conventionally manufactured components. “If you want to propose additive as a solution, it’s not good enough to be, in and of itself, interesting or look cool. It genuinely needs to compete with traditional technologies,” added Toby Maconachie. “While additive has advantages for thermal applications and the capability for internal complex geometries, it’s also limited, such as the minimum feature size.”
Key performance factors possessed by traditional thermal products include fine features, such as very thin tubes and tight tolerances. While current 3D printers can achieve mathematically complex surfaces, the resolution doesn’t always meet the engineers’ requirements.
“We can take both the high-performing cores that are traditionally manufactured and combine with fluid distribution systems that take advantage of complex geometries achieved through additive manufacturing,” said Maconachie.
That means that complex housings can be designed to fit the lines of bodywork or wrap around a rollbar, then the different heat-exchanger cores can be integrated with welding or brazing.
“Heat exchangers are being redefined at the moment with hybrid and EV technology,” added Bryson. “The increased power density of electronics and batteries now mean more power in smaller spaces. More complex cooling solutions are required to deal with those thermal challenges, and additive manufacturing gives us the ability to produce some quite intricate and freeform geometries to be able to solve some of those challenges.”
On the other side of the industry, Stratasys focuses on polymer printing to meet the needs of racers. Often the printed part is used as a sacrificial core to manufacture the end-use piece.
“We can 3D print the inside shape of a brake duct out of a high-temperature soluble material, then wrap it with carbon fiber,” said Kreemer. “You cure it in an autoclave, trim the ends, and finish as needed. Then you toss it in a support removal tank that comes with every FDM [fused deposition modeling] printer. That washes away the printed material in a matter of a few hours. That leaves a seamless, very durable, very complex shaped carbon-fiber duct.”
More permanent carbon-fiber molds can be printed and used to lay up the composite materials many times. “You can literally bake and cure the carbon fiber in an oven, and the plastic tool does not deform whatsoever,” said Kreemer, noting that Stratasys offers five different printer technologies using both thermoset and thermoplastic materials to serve a wide variety of customer needs. “The reason we have a diverse product line is there are some applications, some users that need a very high detail, smooth finish part for a concept model. Those same materials would not work as parts on race cars.”
Race Winning Brands in Mentor, Ohio, the parent company of such race suppliers as JE Pistons, Dart Machinery, and Manley Performance, uses 3D plastic printing during the R&D phase of product development, including test-fitting applications.
“It is part of our day-to-day business with almost every brand in our portfolio,” said Nick DiBlasi. “It saves us time, money, and allows us to visualize parts at our facilities that do not have manufacturing cells onsite. The best-use case is when making custom pistons or rods, and we need to get the largest skirt or beam width. It’s very important to 3D print and test fit them in the engine and cycle them for clearance. That solves issues where a customer can’t 3D model their block that has been modified, yet they need a part to fit perfectly. We also send them parts where they can grind and fit the part, then send it back and we model the clearance built in. This happens a lot with big beams on rods needed to clear blocks, or pistons with oil squirters.”
Modeling With Sand
While 3D-printed prototype parts are useful in most mock-ups, some parts can’t be tested in plastic, or a race shop wants to see how a cast-metal part will fit and perform. Hoosier Pattern in Decatur, Indiana, can 3D print sand cores for a foundry to cast the part. If changes are needed, an updated sand core is printed, and another test casting is made.
“We had a customer testing exhaust manifolds, so we printed up a couple of molds,” recalled Todd Yoder. “They ran their samples and found out that the external geometry was what they wanted but wanted to tweak the internal geometry. We printed a couple more molds, and then they had their final parts for the race day. That was pretty easy to do with 3D-printed sand because there were no major changes to a core box. All we had to do is print the model based on what they needed.”
Instead of making traditional hard tooling for casting, Hoosier can print molds in sand directly from a 3D CAD file. The process is quicker and less expensive while retaining the freedom to make changes.

“We can combine cores. So, if you have a complex internal assembly, many times we can print all the cores as one piece,” added Yoder. “You’re going to have higher accuracy. You don’t have to worry about making all the individual pieces, filing them, and then assembling and gluing them together, then risking stacking up the tolerances.”
Trick Flow Specialties in Tallmadge, Ohio, utilizes 3D-printed sand cores to produce prototype cylinder heads and intake manifolds for testing. “When designing a cylinder head or an intake manifold from scratch, the CAD modeling and flow simulation only gets you so far,” said Josh Cook. “At some point early on, you need work with real metal parts.”
Once testing and validation are complete, Trick Flow will use conventional tooling for production. Even though 3D printing the sand cores offers additional flexibility in the design, Trick Flow hasn’t had a problem translating any printed designs into standard tooling.
“Our products are designed to be moldable or castable from the beginning of the design process. Our design engineers work with our pattern makers to think about draft angles, and can we make a tool effectively where our parting lines are going to be clean,” continued Cook. “They’re going to be in a location on that part that is either aesthetically pleasing or isn’t going to affect the performance.”
With regards to 3D metal printing, the team at Trick Flow is looking forward to having that option. “I see great potential in that technology. There are still question marks that I have about the strength of 3D-printed materials. Strength is extremely critical in our application. So, the cost-effectiveness of that manufacturing process and the material properties are something that we would really need to dig into and understand,” said Cook. “We haven’t been convinced that the technology is ready for scale volume production—at least to be cost competitive with more traditional methods.
“The exciting thing is pushing those boundaries, and over time that technology becomes cost effective, and it can trickle down,” Cook explained. “I believe that it will reach a point where it becomes more cost effective in mass production applications, and more consumers are going to be running 3D-printed product on their grassroots race cars.”
Sources
EFI University
efi101.com
Elite Motorsports
elitemotorsportsllc.com
Hoosier Pattern
hoosierpattern.com
HV3D Works
hv3dworks.com
Pankl
pankl.com
Performance Design
performancedesign.com
PWR
pwr.com.au
Race Winning Brands
racewinningbrands.com
Stratasys
stratasys.com
Trick Flow Specialties
trickflow.com
Velo3D
velo3d.com