Skilled Workforce
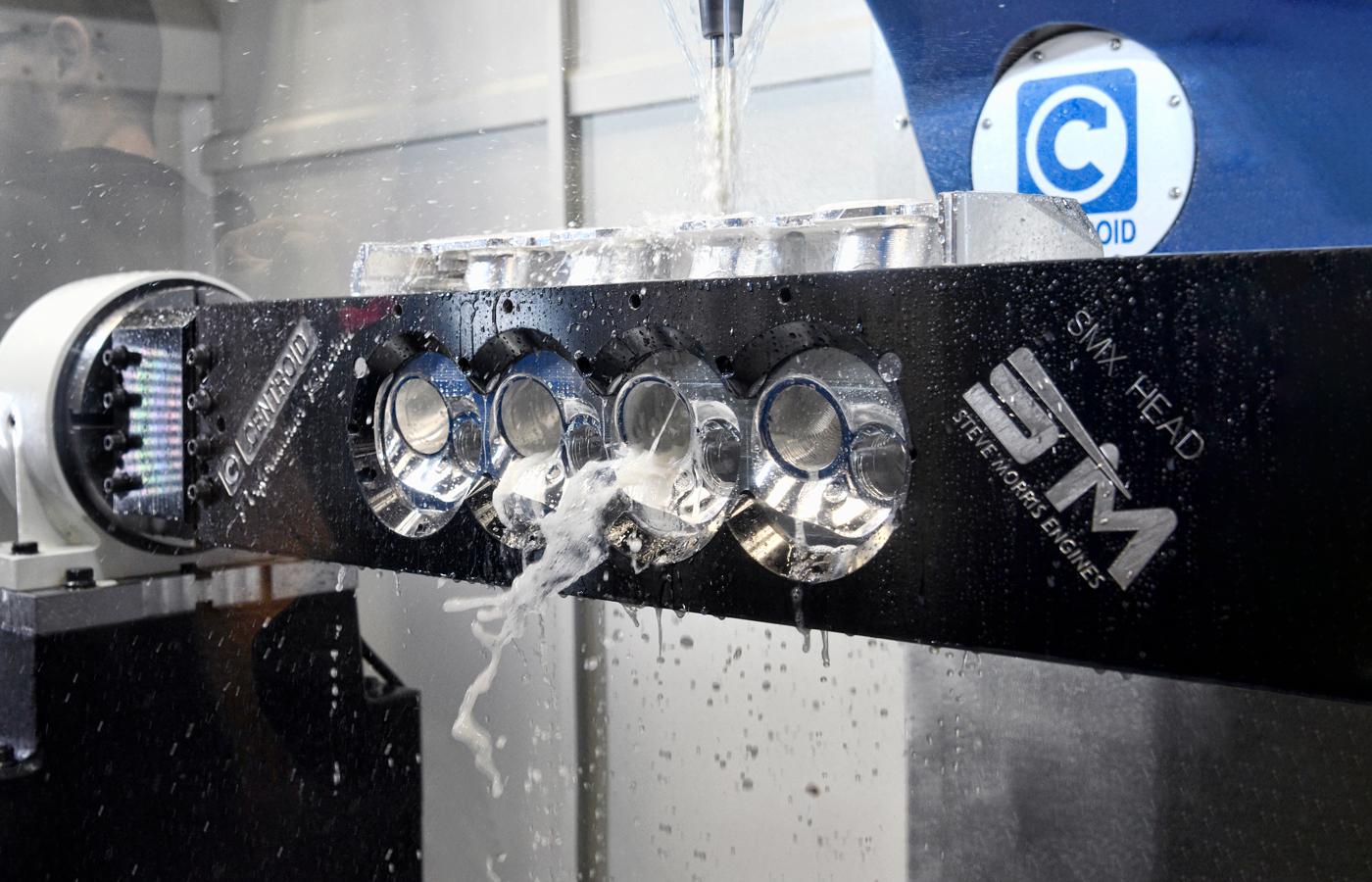
More engine shops and aftermarket manufacturers are embracing new CNC machines and their cost-saving, production-boosting features.
The speed and precision that CNC machines offer are not lost on the speed community. An early pioneer was Robert Yates, who installed a CNC machine in a secret Virginia location in the early 1990s to develop the famed C3 head for Ford’s NASCAR teams. CNC machines quickly became the winning advantage for teams and parts manufacturers who needed consistency and flexibility in their operations.
The holdouts have always had their reasons. Cost, of course, is a valid point, but crunching the numbers today is becoming more favorable due to labor issues. Another well-sounded excuse is fear of computer programing. Yet, that is another myth quickly fading.
Consider the call that Anthony Usher of MEC CNC in San Clemente, California, received from a Pennsylvania automotive machine shop with strong ties to a strict religious order. The employees had no cell phones or computer experience and specifically requested a manual machine.
“We delivered a CNC machine but didn’t tell them it was CNC,” recalled Usher. “Once I had it on the floor and a chance to show them, they loved it. It’s a proper CNC machine, but they didn’t realize it because it has such a simple interface.”
To be sure, there are still iron-willed disciples of the Industrial Age in automotive circles who simply prefer the meticulous art of manual machines. Give a master machinist a WWII lathe and Bridgeport and plenty of time, and they can still turn out many of the components needed in a winning race car.
However, the number of skilled machinists and those aspiring to the trade are dwindling fast in the racing market—mostly through retirement but also due to lack of interest in younger generations to take the places of experienced workers. Helping to fill that void has been CNC machines.
“We’re making these machines today very easy to learn so that anyone can operate them with minimal training,” said Usher. “Customers need CNC machines, but they want them with only two or three buttons—and so we’re developing them.”
PRI sampled seven shops that recently purchased a CNC machine. All are associated with engine building or manufacturing of performance parts. For some it was the shop’s first CNC purchase, and for others the acquisition was added to expand product offerings or increase current production.
These case-study capsules revealed real-world topics of labor, training, logistics, business-plan direction, and other industry dynamics. Looking ahead, CNC machine manufacturers are designing next-generation features to address future needs of the customer. A key factor will be integrating advanced AI or artificial intelligence.
“Researching the use of AI in optimization is already in full swing,” said John Cowher of Centroid, Howard, Pennsylvania. “The biggest benefit will be in optimizing strategies for a number of different applications. For CNC machine tools, generating better and more efficient tool-path strategies is always on the minds of the software developers producing the CAM software that is required for today’s high-speed machining.
“CNC machine tools themselves may be able to benefit from on-the-fly smoothing applications that might be able to take advantage of AI helping to improve surface finish and improving accuracy of the final part through improved motion control,” added Cowher.
Also, the future may see CNC machines incorporate additive manufacturing. “An example of an application might be to 3D print a prototype part on the CNC and machine it to the proper tolerance prior to going to production casting,” said Cowher.
Shop: Advanced Product Design
Machinery: Haas UMC-750
Although the company has earned much of its reputation for manufacturing drag racing carburetors, Advanced Product Design (APD) in Genoa, Ohio, also offers belt-driven fuel systems, cylinder heads, and other private-label products. In early 2022, APD purchased a Haas UMC-750 five-axis CNC machine from Haas Automation in Elk Grove Village, Illinois, to help expand the production of rocker arms.
“I would have to say it’s the most turnkey machine I’ve ever seen. We were making parts on day one,” said John Kyle. “The main parts and components we have run on the Haas at this point are pretty diverse. We’ve run anything from 4340 steel, cold-roll steel, 6061, and 7075 aluminum. The steel was a concern with a five-axis trunnion table, but we’ve had zero rigidity issues. We make parts in incredible time.”
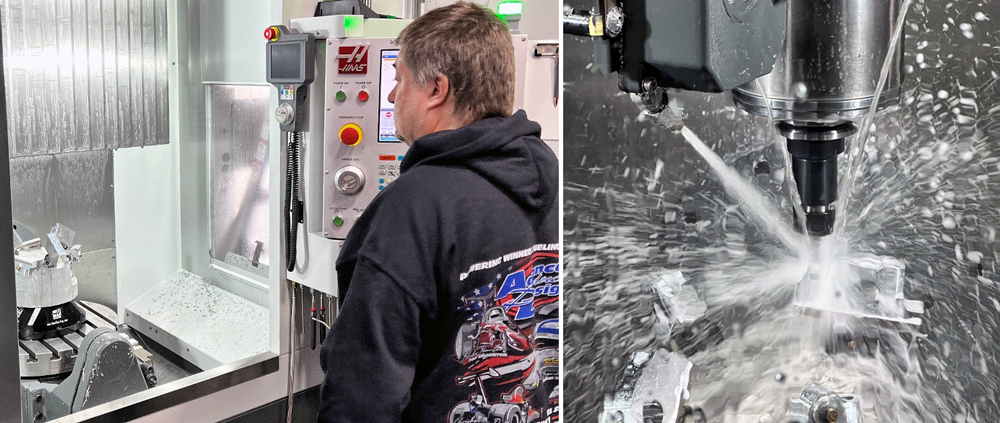
An older machining center produced a rocker arm every 18 minutes. With the Haas, that production time is now less than 10 minutes. Production times of other parts are also down, as is the transition time between jobs.
“This machine has made short runs much easier because of its ability to set up a job quickly without having to indicate a part, having the probing system and the dynamic work offset, you’re only losing at most an hour from job to job versus typically sometimes as much as six hours,” explained Kyle, noting that the five-axis configuration also speeds up overall production time. “Once again, in the five-axis machining world, that part can be produced with one hit of the cycle start button. That part I would say in a three-axis milling application would be well over a five-hour part. In a five-axis application on this style Haas UMC, you’re looking at a 45-minute cycle time.”
For complex jobs, the Haas has features to streamline fixturing and produce completed parts much quicker. An order may call for 1,000 parts, but there are three or more different setups, then a finished part isn’t available until the last setup.
“In our business that’s a problem because that can delay weeks before a customer sees a part,” added Kyle. “We’ve really tried with five-axis machining to go every time you hit the cycle start button, you have a finished part or multiple finished parts coming off complete.”
Shop: Baldwin Racing Engines
Machinery: Rottler F69A
Jeff Baldwin already had a Rottler F65M manual block-machining center at Baldwin Racing Engines in Friedheim, Missouri, but the loss of an employee prompted the step up to the automated F69A.
“As bad as it sounds, we let a guy go for quality reasons, and it’s hard to find people right now,” explained Baldwin. “The reality of it is, this CNC machine doesn’t call in sick, doesn’t have girlfriend problems. It just shows up to work on time every day. That’s how we’ve approached it.”
Some accommodations were necessary to fit the machine in the shop to utilize the existing crane system. Marty Merz from Rottler in Kent, Washington, helped with the installation and training.
“It helped that I already had the Rottler H85AX honing machine, so I was familiar with how they approached machining,” said Baldwin. “But they’ve got it very user friendly.”
Baldwin uses the F69A for line honing, cylinder boring, surfacing the decks, and lifter bores. He can also lighten the blocks and add logos.
“We’ve got a Renishaw probe. That speeds up the process so much—just being able to measure and locate everything. Also, Rottler’s strong point is the fixturing. They either have a fixture for the job, or it’s easy to come with something that will work,” said Baldwin.
The F69A allows Baldwin to maintain the previous production level with one fewer person on staff in addition to increasing the types of machining operations not available on the previous manual machine.
“I’ve got it positioned next to my hone. I can bounce back and forth between the two machines. Today in the ’69 I’m boring the cam tunnel out for a 50-mm cam, and I’ve already done two or three blocks in the hone. Doubling up on time is where this really shines,” said Baldwin, noting that installing lifter bushings is extremely easy with the F69A. “I just hit the go button, and it’ll do all 16 bushings in one run. Before, I had to move it manually from bore to bore. What used to take five hours now takes 45 minutes on the new machine.”
Shop: Chaos Fabrication
Machinery: Centroid A560 XL
Developing its own cylinder head for diesel inline-six applications prompted Chaos Fabrication in Washington, Pennsylvania, to purchase the Centroid A560 XL CNC machine last November in order to expand the shop’s operation.
“It wasn’t efficient to try and do on our other machines,” reported Kevin Campbell, adding that the shop also developed its own billet cylinder blocks. “There really wasn’t much of a challenge in setting it up. We told Centroid what we were doing with it, and they provided all the fixtures for those applications.”
Since Campbell’s techs had previous experience with CNC machines, the training sessions went quickly, and the team was up to speed in short order. The main advantage of the A560 XL for Chaos is its size, which can accommodate Cummins and International applications.
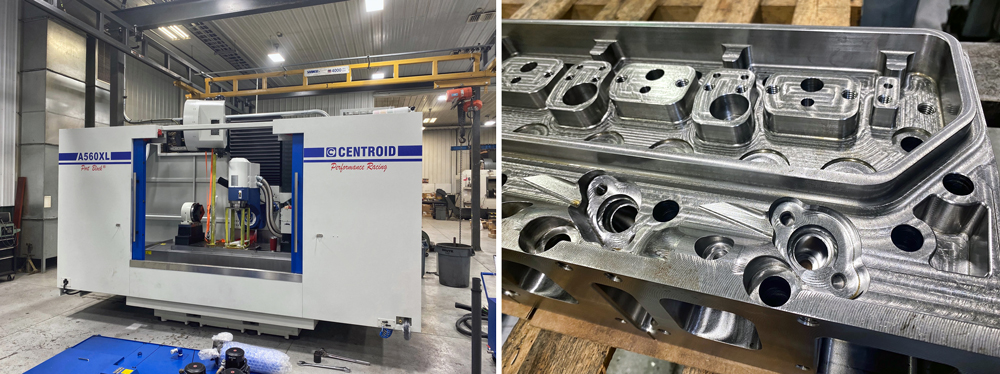
“For six-cylinder heads and blocks, they’re just so big and long. You’ve got to have a large machine to be able to work on them. It’s not like a V8 head,” said Campbell, noting that machining a head from billet steel takes up to 80 hours. “But the reason the heads take so long is because of their physical size. They’re probably the size of a couple Chevy heads end to end. We also take a lot of material out of the head to get it lighter.”
Each cylinder head starts out as a 600-pound chunk of 1018 or A36 metal, and the finished product weighs around 275–300 pounds. It is heat-treated after machining.
“The way it’s able to lay out port designs made it a better fit for what we’re doing than our other CNC machines,” added Campbell, noting that currently all the heads are machined for dry applications such as drag racing or tractor pulling.
Shop: ProTorque
Machinery: Mazak HC-5000 & Mazak QTU-350MSY
Nitro dragsters and Funny Cars go through clutch floater plates about as fast as ProTorque in Yeadon, Pennsylvania, a division of Boninfante Friction, can make them on its new Mazak HC-5000 horizontal machining center from Mazak in Florence, Kentucky.
“We make roughly 20,000 parts a year to fill the demand,” said Elliott Pickett, noting that the HC-5000 is needed for precision and consistency. “There’s a lot that we have to do as far as concentricity. The groove count and the groove quality are something that we work on very hard. For the most part, all the teams run the same style clutch, but everyone runs a different groove package, anywhere from one to eight grooves and at varying widths.”
ProTorque machinists have developed numerous macro programs based off customer needs, and the HC-5000 is a steady production machine that can turn out thousands of parts with the only variable being the grooves. A typical nitro clutch uses five floater plates and six friction discs. All five floaters are discarded after each run, while the friction discs can survive two runs. The groove package may change during a season, so the machine orders have to be flexible and react as needed.
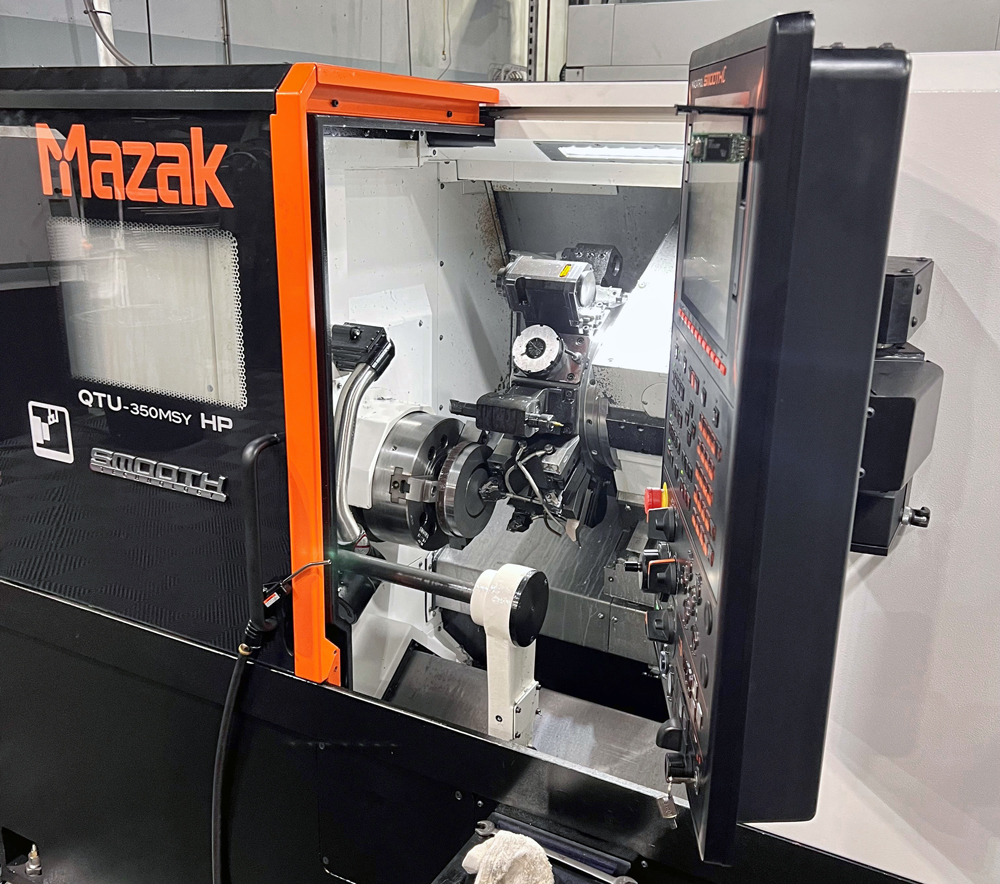
“If a disc is not wearing as much, they might put a couple extra grooves in. If it’s wearing too much, they might take a couple grooves out. A lot depends on the season and how they’re prepping the track,” said Pickett.
Other Mazaks on the floor are the QTU-350 and QTU-350MSY. The former is for machining nitro input shafts out of a proprietary steel that can handle the 12,000 lbs.-ft. of torque fuel engines are estimated to produce. The other QTU machine can be set up for torque converter stators and other parts.
“Our main guy on the floor had no programming experience, and he was able to go through the training when we first introduced the QTU,” said Pickett. “Within a couple of days he had parts coming off. That’s a testament to the people that Mazak has in training.”
Shop: Ross Automotive Machine
Machinery: MEC Robins SG8-XL & MEC Robins RubiSurf 1.9
A full-service engine machine shop that includes dyno services, Ross Automotive in Lapeer, Michigan, stepped up to CNC machines as business was outpacing the aging manual machines in use. One of the upgrades was a MEC RubiSurf CNC surfacing center used for cylinder heads.
“We went from 45 minutes on and off with the head to about 10 minutes with the RubiSurf,” said Brendan McInerney, noting that the RubiSurf can also be used for exhaust and intake manifolds. “It’s a huge time saver for us. When you click start, we let it run, and walk away until you come back to put on the next head.”
McInerney admitted that there was apprehension among the employees with the arrival of two CNC machines. But he had previous CNC training on a Haas that is used to make custom parts like pulleys. McInerney also handles the design work using Fusion 360 software.
“Some of the older guys were a little uneasy, but they actually like it now,” said McInerney.
The SG8-XL handles valve guides, seats, rocker studs, and other head-related chores. It will perform valve jobs, from one- to three- to five-angle options.
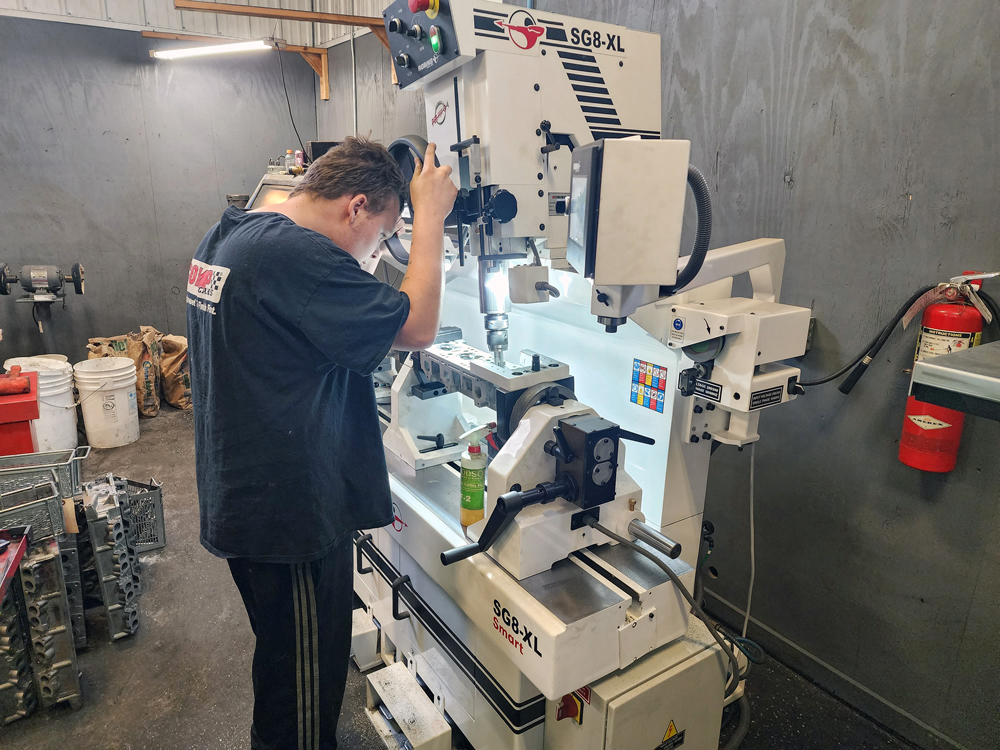
“We just got this machine, so we’re designing some of our own cutters for custom port jobs,” said McInerney. “For the moment, however, we’re using the supplied cutters.”
The shop previously had the equipment to surface heads and offer valve jobs, but the new machines have improved efficiency.
“It’s pretty much to save time and money for us. I’d say we’re 60% faster than we were before,” said McInerney. “Maintenance is super easy.”
Workflow focuses on all employees trained to run all the machines. “Everything here is custom. When we do a set of heads, we like to keep one guy doing that set of heads. Then there are three or four other guys behind him. Everybody can use the machine, so its fluid, not just one guy trying to keep up with everyone else’s workload,” explained McInerney.
Shop: Scorpion Racing Products
Machinery: Star SR-32
The manufacturing center for Scorpion Racing Products in Ocala, Florida, could be a showroom for Star CNC Machine Tool in North Olmsted, Ohio.
“We have two SB-16s, three SR-20s, and one SR-32,” said Zac Collins, noting that the oldest is a 2005 model and the newest arrived in 2022. “In our line of work—rocker arm and valvetrain manufacturing—we use the Stars for all of the steel sub-assembly components. They make everything from our Polylocks and lock nuts to our pedestals for the Ford and LS rockers. Also pushrods, seat inserts, pins, rollers, fulcrums or trunnions for the rocker assemblies. Basically, anything steel goes through those machines to supply all of the steel components for our rocker assemblies.”
Scorpion was running three shifts, six days a week, and still found the need for additional machinery due to increasing private-label orders.
“Basically, we looked at the numbers and said there just weren’t enough hours in the day, even at three shifts,” recalled Collins. “That’s when we justified purchasing another machine. The Stars are so consistent, they hold tolerance very well, even when we cut several different materials on them. They’re holding plus or minus half a thousandth of an inch.”
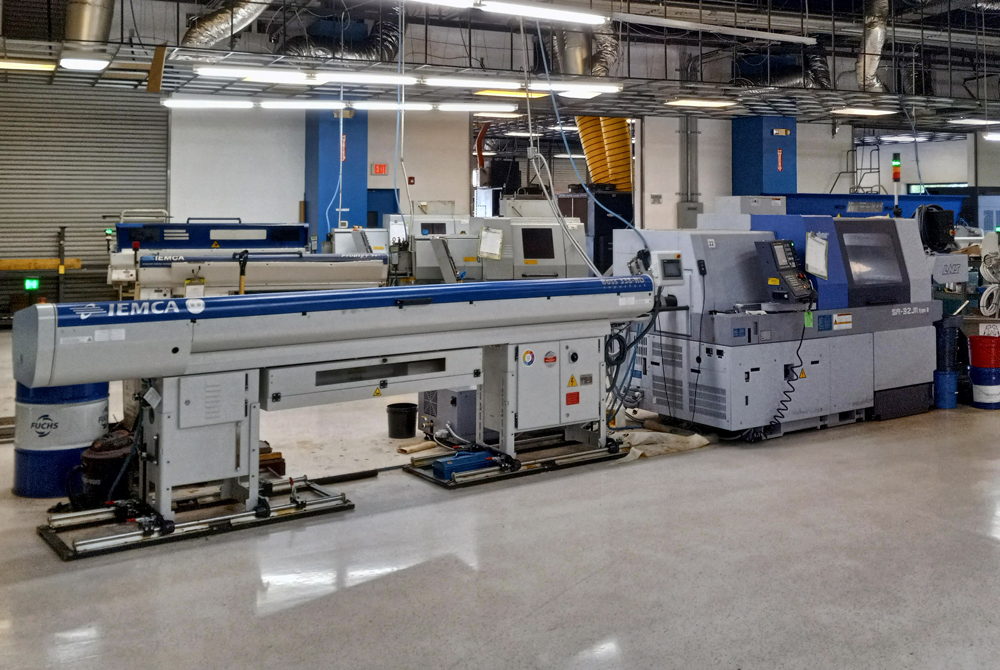
Scorpion has one operator to run all six of the Star machines in addition to a pair of twin-turret lathes.
“Once you get them running, you don’t have any issues with feeds, or speeds, or any of the programming,” added Collins. “They run as long as you feed them with material.”
Collins said transitioning to the newer machines was easy, as many of the fixtures and programming carried over. In-process inspections are routinely held to check critical measurements, but otherwise the machines run without operators.
“The main benefit is not to rely on an operator,” continued Collins. “You put a 12-foot bar on it and walk away. And you can get a bar feeder that will hold eight or 10 bars and you’re loaded up for hours.”
One feature Collins would like to see in the future is offsite communication where if a machine goes out of tolerance or there’s an alarm on the machine, company officials are immediately notified and can return to the shop to address the problem.
“It would be great to go fully lights out and still have visibility on the machine,” he said.
Shop: Unlimited Diesel Performance
Machinery: RMC V50
Nate Bailor was rather new to CNC machines when he started training his staff at Unlimited Diesel Performance in Bremen, Ohio, on a V50 block machining center he purchased in March 2021 from RMC Engine Rebuilding Equipment in Saginaw, Michigan.
“We were doing block work with older equipment,” explained Bailor. “It would take us an entire day to bore and resurface a block. When we bought the V50, I can bore eight cylinders in about eight minutes. The longest part of the job is the setup. The entire job is done in two hours. It definitely has increased our productivity.”
Bailor has yet to run the V50 himself but has one machinist fully trained. “I can tell you, the guys from RMC have a great software package,” he said. “When we trained with them, it was very easy to learn. They do it in such a way that they can take someone who has never run a CNC machine, and by the time you leave their facility, you’re really confident in what you’re doing with it.”
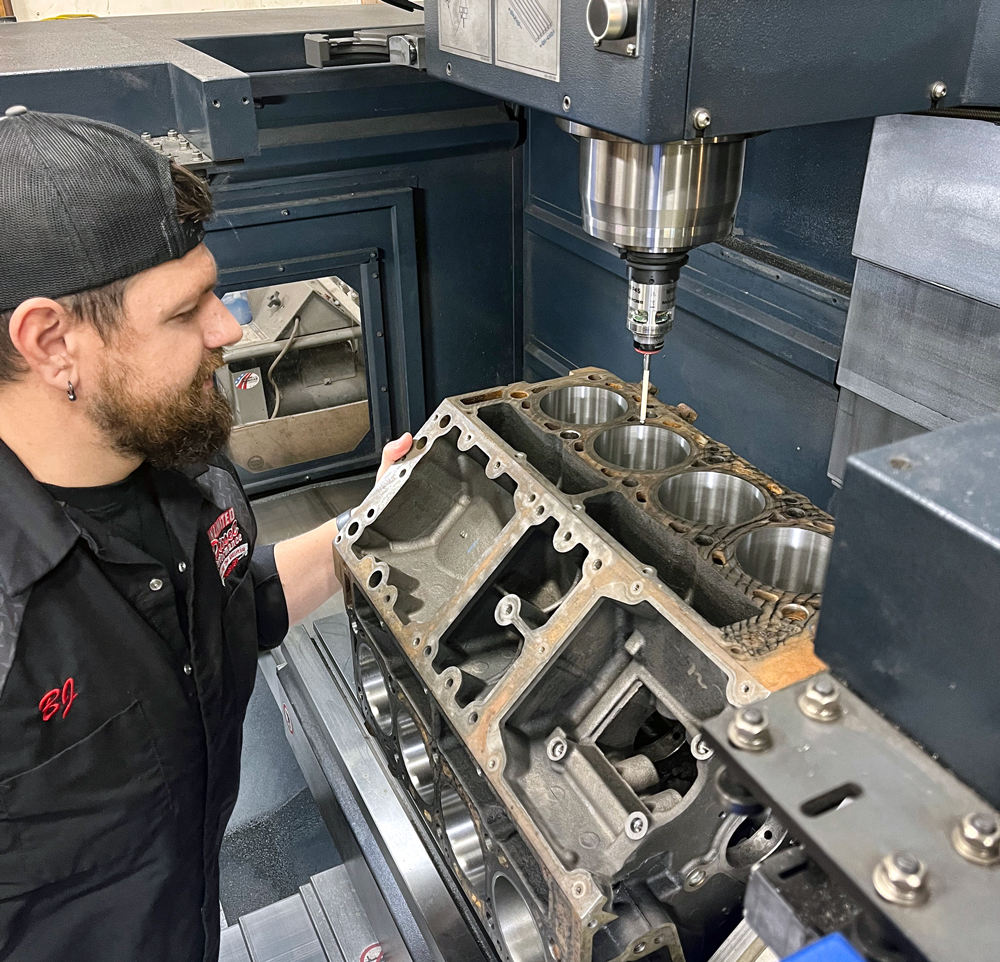
Bailor said the operating system has plenty of safeguards built in to avoid costly mistakes, and the customer service is always helpful when there is a new application or a new procedure they want to try.
“As for the setup, it does take a large footprint for sure,” said Bailor. “But with all the extra work we’ve taken on, it feels like it’s taking up even more room. Actually, we had to take one of the lifts out of the shop to locate this machine. We went from a three-bay shop to a two-bay, but it was definitely worth it in the long run.”
Value of After-sales Service
Convincing a race shop, engine builder, or manufacturer to purchase a CNC machine may be the easy part. Keeping that operation as a customer requires a cmmitment to service all the parts and repair needs. Following are thoughts on this topic from a few of this story’s sources:
“It’s not just the machine with Haas. It’s everything from the financing. Financing was way easier than I ever did with a bank. We’ve only had one problem with the machine. There was a filter that was causing a pump to cavitate a little bit. Another amazing thing about Haas is its huge online portal where you can see other people’s problems. Within minutes we figured out that stone filter has the ability to clog up. We just removed that filter and fixed the problem. One phone call. The ability to get parts is a huge, huge plus on the machine. —John Kyle, Advanced Product Design
“We’ve been in contact with Anthony [MEC sales rep Anthony Usher], and he’s always been responsive. He’s sent us care packages with parts that came out after the sale. We had a couple of issues, and he’s come up with new fixtures to solve those problems. Now we can cover a wider range of cylinder heads, and we can run two big block Chevy heads at the same time. —Brendan McInerney, Ross Automotive Machine
“The Rottler F69A uses the main journals and the cam tunnel for location, and we had ordered the basic pucks to locate everything. After I got the machine and started going through it, I found things I needed or extras I wanted. You call them and they’re very good about getting the parts out right away. I also purchased their R-Cam software that can be used to machine logos. Ryan Thompson (of Rottler) came down and trained with me, but it’s something I don’t use every day. Literally almost a year went by before I wanted to put logos on valve covers again, so I was at a loss. I called Ryan, and he logged in with his computer on the machine and he was able to walk me back through. I was putting logos on within an hour. It’s amazing to work over the Internet. They can literally run my machine from Washington. If that would have been just a conversation over the phone, that would have been very hard to navigate.” —Jeff Baldwin, Baldwin Racing Engines
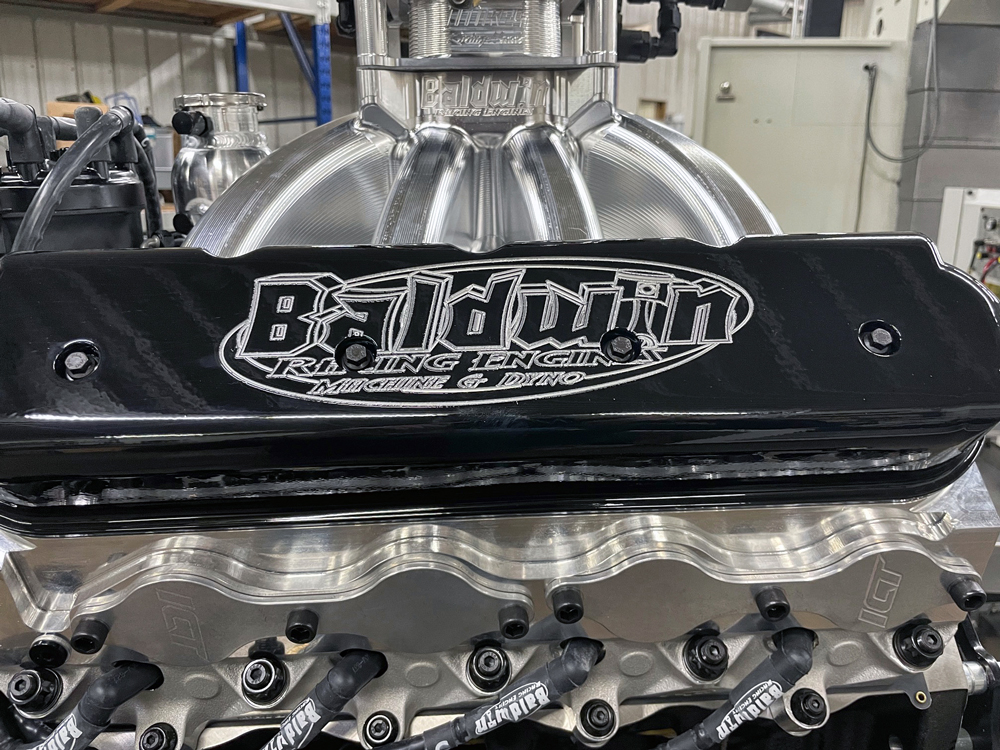
Sources
Advanced Product Design
apdracing.com
Baldwin Racing Engines
baldwinengines.com
Centroid
centroidcnc.com
Chaos Fabrication
chaosfabrication.com
Haas Automation
haascnc.com
Mazak
mazakusa.com
MEC CNC
meccnc.com
ProTorque/Boninfante Friction
protorque.com
RMC Engine Rebuilding Equipment
rmcengine.com
Ross Automotive Machine
rossautomotivemachine.com
Rottler Manufacturing
rottlermfg.com
Scorpion Racing Products
scorpionracingproducts.com
Star CNC Machine Tool
starcnc.com
Unlimited Diesel Performance
unlimiteddiesel.com