Up To The Test
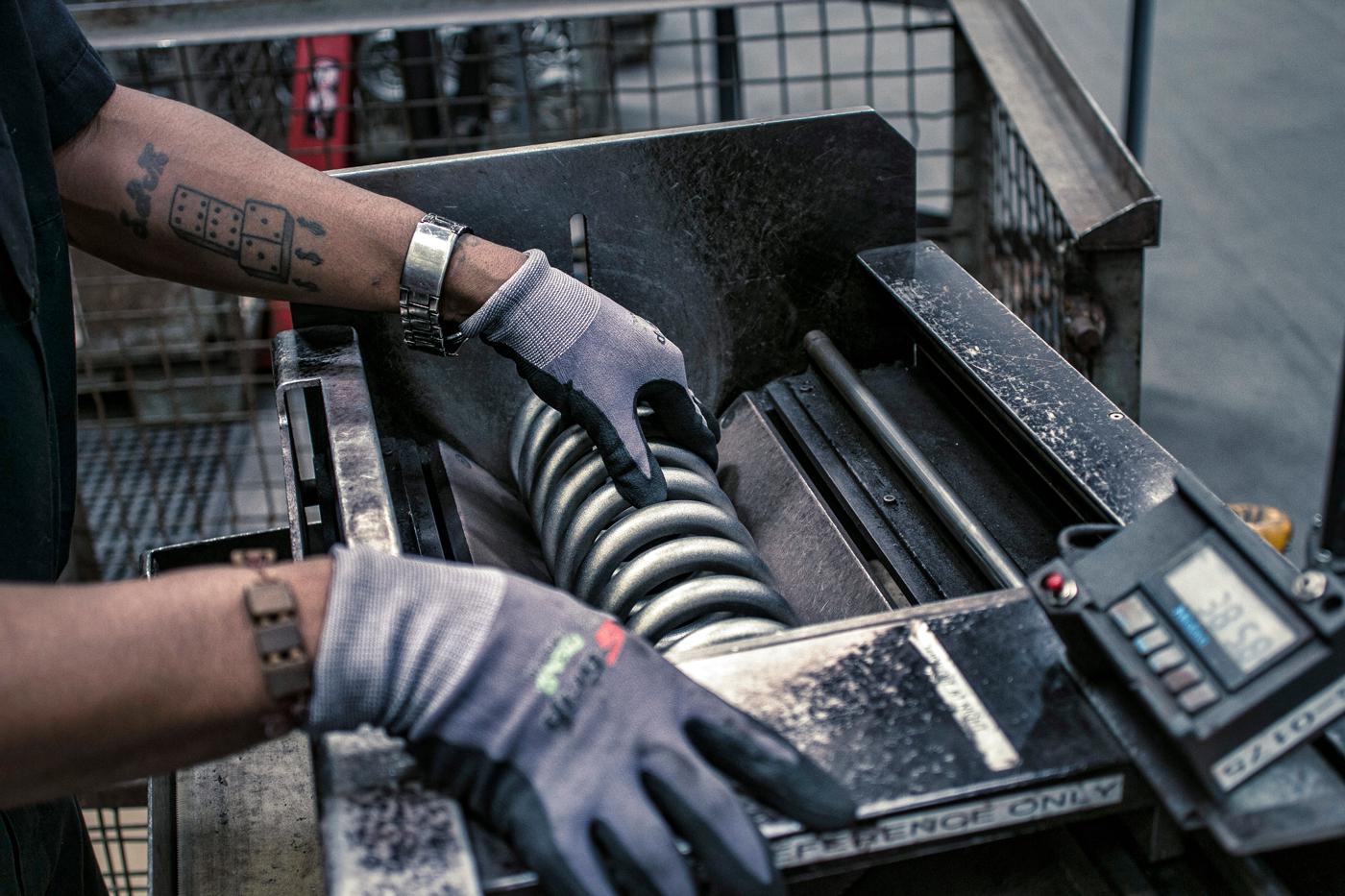
Photo courtesy of Eibach
A behind-the-scenes look at how manufacturers of suspension parts put these components through their paces before they’re released into the marketplace.
Whether it’s on dirt, an asphalt circuit for 24 hours, or at the highest levels of open wheel competition, a race car’s suspension has to perform for its intended purpose, and each component has a job to do to ensure the whole system works to its maximum potential. Each of those parts also has a story behind how and why it was developed, and each goes through a rigorous testing process to make sure it’s up to the task.
For a behind-the-scenes look at what goes into the suspension parts that are available for race cars, we talked with six of the top names in the high-performance suspension business to learn about their R&D and testing regimens.
Eibach
Eibach’s rich motorsports history dates back to the 1980s, when its springs carried DTM competitors such as BMW, Mercedes, and Audi to the top of the podium. Since then, the Corona, California, company has expanded into every corner of the racing world, offering everything from extreme long-travel springs for off-road desert racing to coils for the sophisticated inboard pushrod setups used on top open wheel cars. Today, a customer looking for the right set of springs for their race car can choose from the more than 1,500 options, including the popular ERS series of racing springs, in Eibach’s existing catalog. Sometimes the right spring package for an application doesn’t exist yet, and that’s when Eibach’s engineering and motorsports teams will get together to see what they can come up with.
In many of those cases, Eibach’s motorsports team will be presented with a challenge with certain parameters to work around—if a series changes its rulebook to allow a spring of a different length and diameter than the previous year, for example. After gathering information on what characteristics teams and drivers want from this new spring, the motorsports team then consults the R&D team to see what’s possible. Once the green light is given, engineering works on modeling a spring to make sure it can meet racers’ specific needs.
A prototype of the spring is made, then Eibach begins its in-house testing. The spring is loaded on a rate grapher, a piece of equipment that plots the spring rate through its entire range of travel, to confirm that it satisfies the racers’ specs. It’s then put on a cycle tester and run for around 500,000 cycles at various strokes for fatigue testing. If it passes that round of tests without losing any height, rate, or load characteristic, then prototypes are sent out to racers for real-world testing.
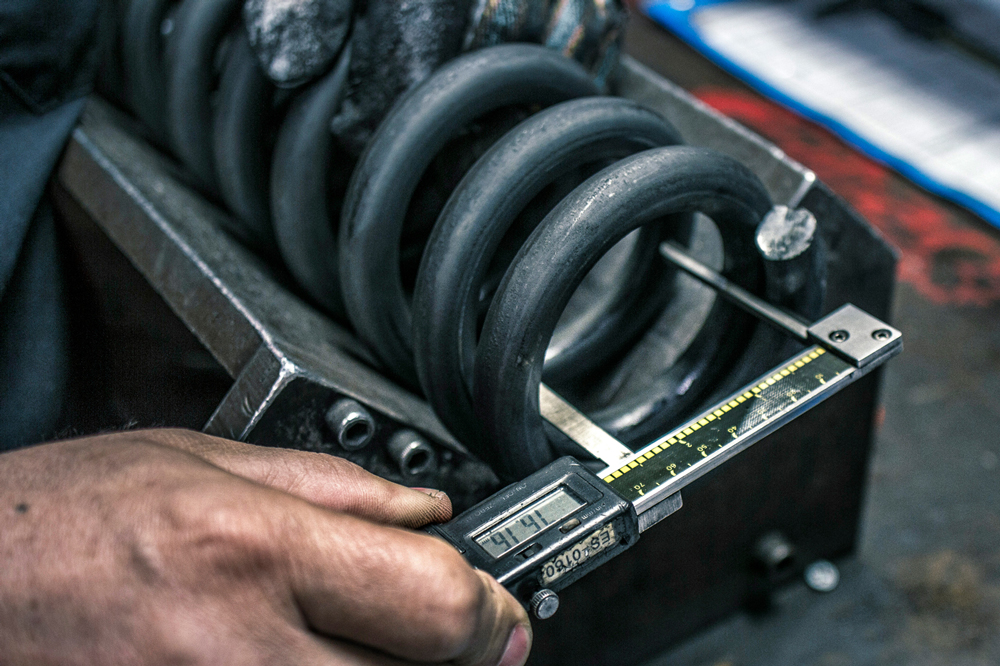
It’s at this stage where feedback from teams might lead to minor tweaks to the spring. One example came from the company’s NASCAR program, said Mark Krumme. “We were able to develop a very special spring with them for use on superspeedways to help control speed and safety of the cars and trucks. That basically came down to back and forth with engineering and saying, ‘Look, the ground effects need to be maintained this far off the ground, and we need the load to be at this point.’”
For Eibach’s Michael Seidman, that becomes a matter of fine-tuning the rate curve. Using the above methods, Eibach is able to adjust the load characteristics of a spring at any height to give it a more progressive feel, digressive feel, linear feel, or really whatever a racer wants.
And what a racer wants, of course, is very subjective. “Everyone has their own driving style, and that’s why we have spring rate ranges to fit everyone’s preference,” said Krumme.
Energy Suspension
Energy Suspension in San Clemente, California, has specialized in high-performance polyurethane bushings, mounts, and other components for 38 years. In that time, the company has produced a massive catalog of parts that continues to grow every year. Since there’s only so much time in a year to develop new products, Energy Suspension needs to carefully choose what projects it focuses on.
The decision to develop a specific part hinges on a number of different factors, but one thing Energy Suspension believes it does best is analyzing the competitive landscape and identifying gaps in the market. “Introducing similar products is not our formula for success,” said Jon Burke. “Also, a feature of good product introductions is to lead the market by introducing products that the market is not even aware that it needs yet.”
Energy Suspension’s marketing and sales teams gather data on a particular problem or market need and get together with R&D to work on a solution. Once a proposed part or kit is given the green light, the company seeks out a vehicle for measuring and test fitting.
“We can take the vehicle onto our lift to check for the match between our design information and the actual vehicle,” said Burke. “The part models are modified and adjusted as more learning about the application becomes available through our vehicle inspections.”
Once all the measurements are verified and the team has a viable prototype design, tooling for production, including master molds for the polyurethane parts, is developed, and the first prototypes are cast and assembled. These initial prototypes are measured against the original design before being test fitted. After that, the parts go through a series of grueling durability tests.
A durometer is used on all polymer parts to verify their resilience, and the parts are evaluated on a compression tester or tensile testing apparatus. A specialized load testing device vibrates parts for extended periods of time to test longevity. Oftentimes, Energy Suspension will build a special-purpose device to simulate high stress in a specific situation and get an idea of expected life under those circumstances. For the ultimate torture test, parts are subjected to a 50-ton press to see how they hold up to extreme loads and ascertain the point at which they might fail.
The other half of the testing process happens on the vehicle itself. After getting some seat time with the prototype parts installed, drivers will provide feedback on various factors, including ride and handling; noise, vibration, and harshness (NVH); and anything else they experience behind the wheel. “It’s not unusual to encounter user feedback that drives changes in a part or parts of the bushing set,” said Burke.
KW Automotive
Stroll through the pits and paddocks at any sports car race in Germany, and it’s easy to lose count of the KW logos. That reputation has scored KW some prestigious OEM contracts, with the brand supplying shocks for such potent road cars as the Porsche 911 GT3 RS and Mercedes-AMG GT four-door.
Yet racing is in KW’s DNA, so its team works with competitors both at the professional and grassroots levels to develop new products and continue evolving existing ones. The word “evolution” is key for KW, because its designs change constantly based on feedback from the track, its OEM projects, and its customers.
“Sometimes there’s a technical evolution based on something that we’re up against on a new project, and that’s where the innovation starts to happen,” said Frank Vasquez, in KW Automotive’s Clovis, California, location. “We start to think of a more creative way to approach that problem. If the solution is feasible, then we can look at applying that across the board on new products. As time goes on, those changes start to trickle down to our most common parts.
“One of the important things to point out is we don’t stock coilover kits on the shelf,” Vasquez continued. “Every kit that is ordered by a customer gets put into the production line and produced specifically for that customer. The benefit of doing it that way is it allows us to be more flexible in those design changes. We get to roll that change out into the new production right away. It guarantees that the customer gets the latest spec, say if the damping profile changed a bit or if the spring rate was updated. All those changes are live in the system, and the product will get built that way.”
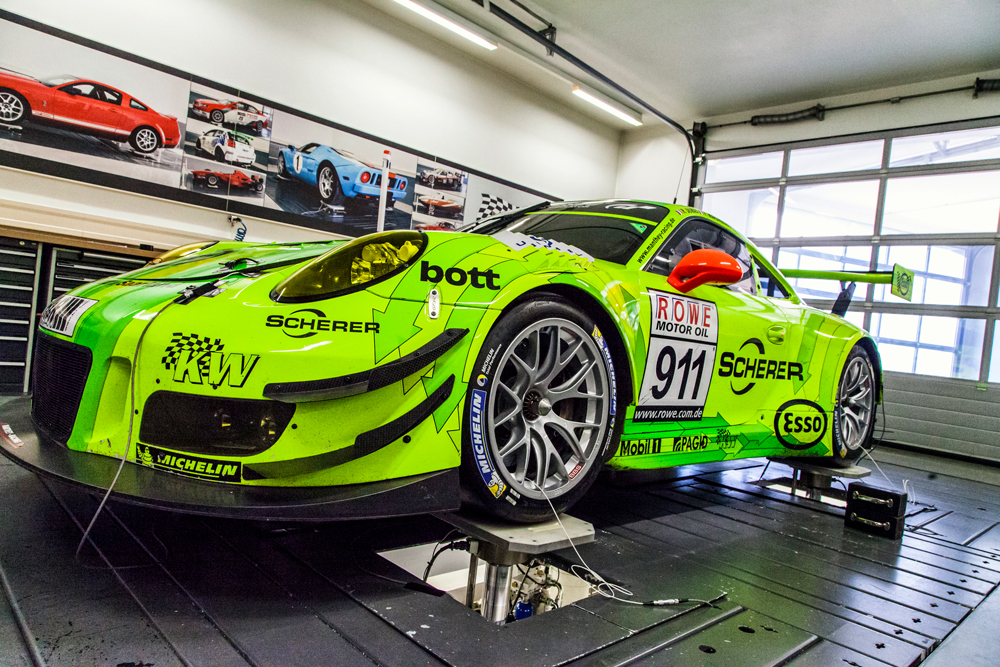
Given KW’s extensive involvement in endurance racing, its dampers go through a great deal of durability testing to prove they can perform over the course of a 6-, 12-, or even 24-hour race.
“When it comes to endurance racing, it’s a matter of longevity, service life, and consistency throughout that,” said Vasquez. “The teams are looking for parts that are going to work and provide a consistent output from the dampers throughout the extent of that race.”
KW has many different stress tests to simulate hard usage over extended periods of time. “That helps us down to a component level evaluate how the product wears or behaves, the changes that the shock may see over time, temperature changes, that sort of thing,” said Vasquez. “A lot of it comes with experience as well. If we’ve been using a certain type of shock technology for a while for an endurance championship, we know what to expect. If we do discover any shortcomings, we can start polishing or improving for the next iteration of that product.”
Penske Racing Shocks
As a longtime supplier and partner of teams in Formula 1, IndyCar, and other top-tier series, Penske Racing Shocks of Reading, Pennsylvania, has earned a reputation for its professional racing suspension. But it also offers shocks for drag racing, dirt late model racing, motocross, and much more. The company has developed shocks for many different applications; and while all of its development draws from its experiences at the top levels of competition, the door also swings both ways.
“Formula 1 is probably at the tip of the spear on everything,” said Aaron Lambert. “But from a philosophy standpoint, we try to take all of our technology, whether it’s from Formula 1, or sprint cars, or ATVs, and when we’re designing, we try to cross-pollinate with other markets. That’s where we see a lot of our success. Even though the markets may be drastically different, part of our philosophy is that a lot of our parts all fit together. We might be doing some development for one market, but we’re always trying to see how that might relate to another market and give us an advantage there.”
Penske also develops shocks for endurance racing. Currently, it’s working with teams running cars in the new LMDh prototype class for the 2022 FIA World Endurance Championship and IMSA SportsCar Championship seasons. When developing shocks for those teams, once again Penske relies heavily on its experience in F1.
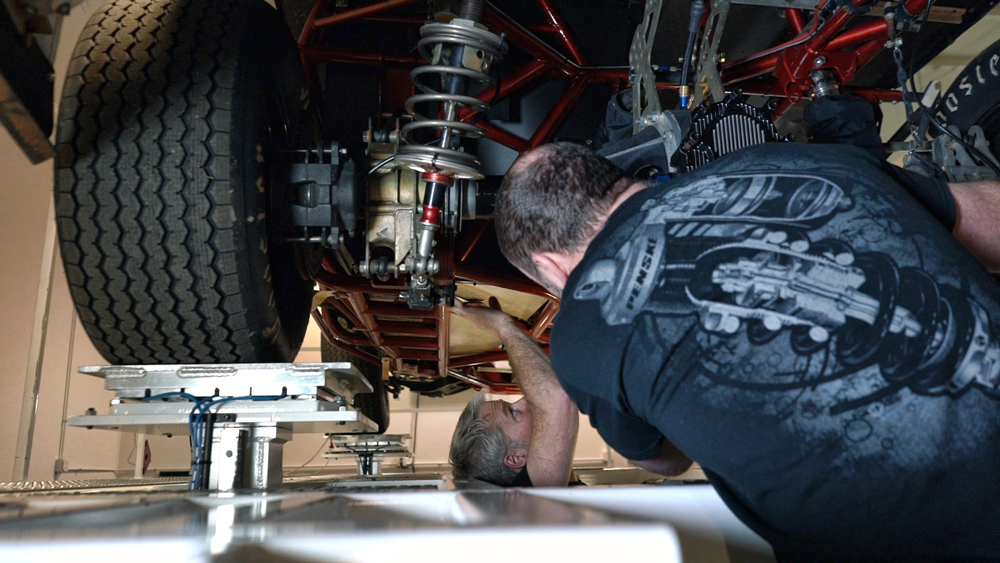
“From a performance standpoint, we know what types of loads a lot of these new sports cars will be experiencing,” said Lambert. “So we can bring in some of our F1 experience, and when they get to testing these cars, hopefully their initial testing is a lot closer to where they want to be.”
One big difference between F1 and endurance racing is the level of durability needed for all the parts on a race car that’s going to run for a dozen or more hours at a time.
“There’s a lot of testing that goes on, not only just from the standpoint of the damper performing but also the environment it’s going to live in,” said Lambert. “As aero gets more efficient and teams look for savings there, the temperatures get a lot hotter underneath the car, so that means the shocks are getting a lot hotter now. In Formula 1 the car might run for two hours at a certain temperature, whereas in endurance racing the car runs 12 hours, 24 hours in the same conditions.”
Constantly pushing 100% for 12 hours or more “really puts all the hardware through the toughest conditions possible,” he continued. “We can run simulations and other things here in the shop. We have a lot of different tools to run the shocks for a certain period of time, run them at that temperature, look at the fade, look at what’s going to fail on them before it fails on the car, and then replace those parts or design them differently. We just constantly test and evolve to where, hopefully, our part’s not the weak link.”
QA1
QA1 in Lakeville, Minnesota, makes all kinds of suspension parts for all kinds of vehicles. A remarkable amount of development goes into each part, due to the fact that the company employs what’s called a phase gate product development process for every part it makes.
The phase gate process isn’t too dissimilar from other product development methods, except that at each phase a decision is made to either kill a project or allow it to proceed to the next phase, hence the “gates.” In many cases, customers and racers come to QA1 with a problem, and if the engineering team thinks it can come up with a good solution, then it moves into the six-step phase gate process. Eventually, some concepts are explored, one stands out as a plausible solution, and the process moves forward.
“After a concept approval we move into a design stage, and that’s where it gets really serious,” said Chuck Olson. “We have a general idea of what we want the product to look like, but in the design stage we’re modeling everything accurately in CAD, and we’re getting a lot of data off the vehicles that our product would attach to, so there’d be a lot of measurements taken. We do a lot of laser scanning of chassis and test fittings of products at this stage.”
Before a physical prototype is built, a virtual part is put through Finite Element Analysis (FEA) testing. QA1 uses a program called Solidworks, which can run a variety of tests on a part to assess strength, flexibility, or whatever else designers and engineers would want to know about. Immediately after running these tests, the team can make changes on the fly.
Yet the product can’t be tested only virtually, according to Olson. Instead, it must be backed up with physical testing to confirm the FEA is correct.
“We have many systems at QA1 that we can use for durability testing,” he said. “We have a servo electric test stand that we call the TUV that’s our main durability system. It’s based on a linear electric actuator that, if cooled properly, can run essentially forever. That’s frequently what we’ll use. We purchased it for extremely high loads. One of its primary uses is for shock durability, but we found that by specifying the system correctly, we can use it for sway bars, control arms, components for control arms, cross shafts, you name it. It works great in many applications. We just design some custom fixturing for it. If we want to test a control arm with thousands of pounds of load continuously over two weeks, we have the ability to do it.”
Shortly after these prototypes go through physical testing, they’re sent out to racers to see how they perform in the real world. “Ideally, we’re going to get a lot of miles on them,” said Olson. “And in many cases, they’re racing them. Trying them on the drag strip, trying them on autocross, and road course events, and testing. That’s also a big part of the feedback that we get. It’s all necessary to really have a well-thought-out product prior to release.”
At this stage in the process, it’s rare for QA1 to get feedback that requires a major design change. Some of the most useful feedback they do get deals with installation—whether a part was easy to install or the instructions were clear enough.
RE Suspension
Since RE Suspension’s founding in 2003, the Mooresville, North Carolina-based company has been a champion for grassroots racers. After hearing about the lack of suspension support his friends were getting at their local tracks, co-founder Jason Enders made it his mission to offer top-level suspension knowledge to everyone, whether a particular race car was born in a garage or in the boardroom of one of the top teams in the industry.
One key advantage RE Suspension was able to offer was shock testing, and that’s in large part thanks to Enders’ partner, Kurt Roehrig of Roehrig Engineering, which builds shock dynamometers. Currently, RE Suspension has five Roehrig dynos, including two 5-horsepower crank dynos, two 10-horsepower dynos, and one EMA (Electro Magnetic Actuation) dyno that can reproduce any waveform, download track data from a data logger, and simulate the exact conditions of a race track.
In addition to setting up race cars and fine-tuning suspension systems, RE Suspension manufactures a line of its own parts. Since the company is also a dealer of many of the biggest suspension brands, including Penske Racing Shocks, it tries not to overlap with any existing products when developing parts of its own. “We create products that don’t exist, or people don’t know they need yet,” said Enders. One niche where RE Suspension has thrived is in the performance bump stop market.
When a rule change in the NASCAR Cup series gave teams greater flexibility with their bump stops, Enders saw an opportunity to develop a purpose-built part for the job. He began looking at different materials, like polyurethane foam and solid polyurethane. At the same time, Roehrig had introduced a new top-of-the-line valve spring rater. Together, they beefed up that machine so it could test and measure larger springs, among other compressible parts like bump stops, with impressive accuracy.
“For a good two years I lived on that advanced spring rater trying to get stops that were more linear, because we figured out that, in the world of bump stops, tires love linearity,” he continued. “All the bump stops we had at the time were made out of foam and they were very progressive, so we started trying different shapes and using different materials that were more linear than what we had.”
This cycle of researching, designing, and building prototypes, testing those pieces and then ultimately going back to the drawing board would continue for some time, but eventually RE Suspension’s hard work paid off.
“We microscoped this thing until there wasn’t much left to learn,” said Enders. “We figured out where we needed to be and then expanded upon that. It was a lot of R&D, a lot of making stuff and throwing it away and trying different materials and different suppliers for materials until we found something that was good all the way around.”
Sources
Aldan American
aldanamerican.com
Calvert Racing
calvertracing.com
Eibach
eibach.com
Energy Suspension
energysuspension.com
KW Automotive
kwsuspensions.com
Penske Racing Shocks
penskeshocks.com
QA1 Motorsports
qa1.net
RE Suspension
resuspension.com
Summit Racing Equipment
summitracing.com
TTS Top Tier Suspensions
toptiersuspensions.com