CADs, CAMs & Automobiles
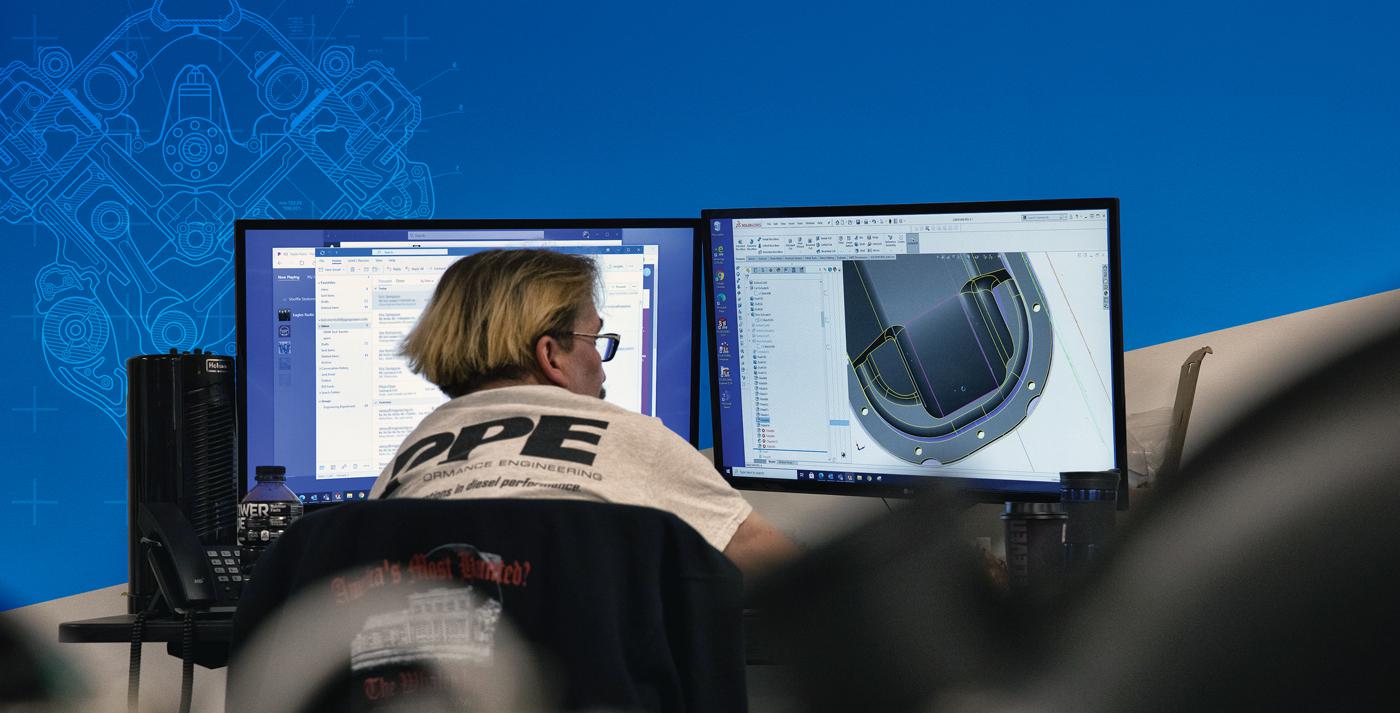
Paired with designers and programmers skilled in the latest CAD/CAM software, modern CNC machines are saving shops money and improving performance at the track.
Ask 10 race shops what technological advancement has made the most impact on performance in the past 30 years and you may get five different answers—valve springs, tires, shock absorbers, etc. One likely standout response, however, is the CNC machine.
Short for computer numerical control, a CNC machine is an automated tool that will process metal (usually aluminum in the racing industry) to the exact specification designated by coded program instructions. Alone, however, a CNC machine is quite useless unless it’s properly programmed through computer-aided machining, or CAM, software. And those precise machining instructions don’t just flow telepathically from the creator’s mind to the machine. Computer-aided design, or CAD, software is used to define the shapes and dimensions of the part before CAM can provide the usable code language that the CNC machine understands.
Before CNC machines, improvements in racing and performance shops were usually hardware-centric—teams relied on lathes, upright mills, and hand-tool skills to make changes to parts or develop new components. This work leveraged the experience and observation of racing veterans—which is a fancy way of saying trial and error drove performance development. Those changes were cycled through prototype stages, tested either on the bench or at the track, and optimized or discarded with each iteration.
Now, virtual design and testing, along with reverse engineering, are at the forefront of racing development. And CAD/CAM software is itself advancing at a rate faster than many race teams can match.
“From what I’ve been told, we probably use just 15 percent of the capabilities of Mastercam,” said Tom Vigue of 3V Performance, Denver, North Carolina. Mastercam is a leading CAM software that writes the G-code programming used to operate the five-axis Centroid CNC machine in Vigue’s shop. “We use a small portion of it just for the features we use on the machine.”
While many different types of parts can be created in a CNC machine, cylinder head work seems to draw the most attention in racing circles. Vigue will design a port by hand, then his Centroid can autonomously digitize the port with the same spindle used for cutting.
“I then import into Mastercam and manipulate it to create the surfaces,” said Vigue, who added that he could do cylinder blocks in the Centroid but decided to purchase a Rottler CNC machine dedicated to blocks. “The problem is mixing cast iron and aluminum in the coolant, so I decided to get the Rottler for blocks only.”
Brad Lagman of QMP Racing Engines in Chatsworth, California, has four CNC machines, and cylinder heads are the main priority. He also shapes the ports by hand, then digitizes them to be replicated in the CNC machine.
“I’ve also designed a few oddball parts, like an oil-pan spacer for a Hemi engine,” noted Lagman, adding that he can program the machines to work on cylinder blocks. “Production-wise, it’s faster. I don’t have to stand over it like an old-style boring bar. It’s also more accurate, especially when we do custom lifter-bore locations.”
One of Lagman’s most closely guarded secrets is his cylinder honing strategy, so it may be surprising to learn that he also has a CNC honing machine. “I only let it run unattended to get close to a size,” he explained. “If I have to hone out .005-inch out of the block, I can program it to hone .004-inch, then I go in and finish by hand. It still saves me three hours of standing by a machine.”
In even larger shops, CAD/CAM work is an absolute necessity. Over the past 20 years, Don Schumacher Racing (DSR) has brought more parts development in-house, manufacturing everything from engine blocks all the way down to fasteners. The move’s two-fold objective: to save money and win more often.
“The competitive edge is always going to be there,” said Scott Cutler, manufacturing engineer at the team’s sprawling Brownsburg, Indiana, facility, where 25 CNC machines are in operation. “But the biggest thing is quality and cost. We can produce better quality parts at a lower cost. And we have more control. If we want to make a change, we’re not asking anyone. We make the change.”
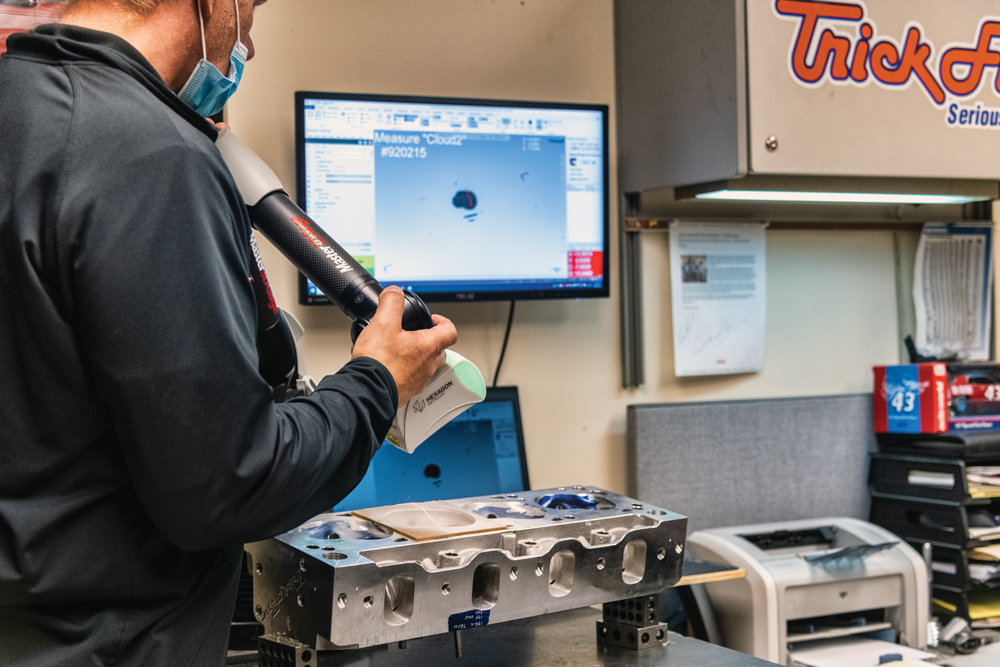
For its 11,000-horsepower nitro engines, DSR designed a new cylinder block that starts as a 750-pound chunk of billet aluminum. After it’s finished in the CNC machine, it weighs 140 pounds. Each year the shop has a goal of producing 50 blocks.
“We’re currently on our third iteration of the block, and without Mastercam there is no way we could make it into a part,” said Cutler, noting that each generation of the block is stronger, and the advanced CAD software used to design it allows for virtual testing. “We run FEA (finite element analysis) simulation on it, which gives us strength analysis. Then we are also able to simulate reciprocating motion, so we can put in the crankshaft, the connecting rods, and pistons to check clearances before we ever get to the real part. We know everything is going to fit.”
BENEFITS FOR MOTORSPORTS
Beyond engine development, the chassis also can benefit from CAD/CAM programing and CNC machining. Rocket Chassis of Shinnston, West Virginia, is a leading supplier of dirt late model chassis, and in 2015 the supplier designed its latest generation, called the XR1. Kyle Kampenga of Keyser Manufacturing in Coopersville, Michigan, worked closely with Rocket designers to develop brackets and other suspension components.
“We had just switched to SolidWorks, so that was a big help for us. Using 2D models, I could adjust rod lengths to see how the birdcage moved, and I could adjust pickup points,” said Kampenga. “Because of all the equipment we have in-house, we were able to produce prototypes very quickly. That allowed us to help get the XR1 ready for 2016 Speed Week.”
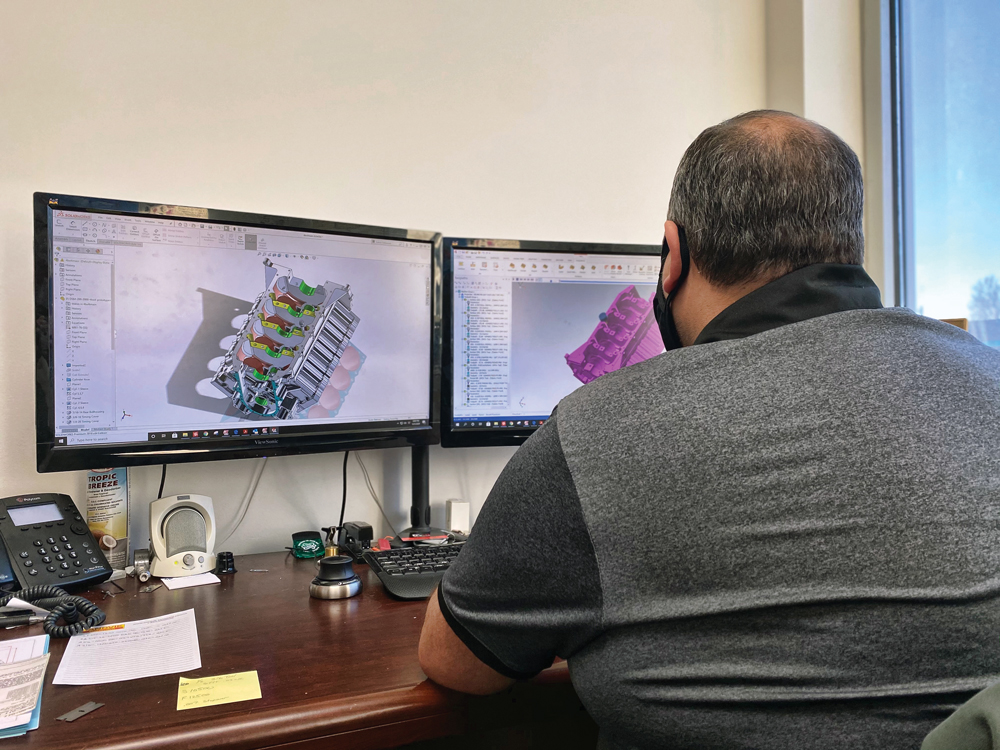
Before Keyser adopted CAD, Rocket would send parts to Keyser to determine the best production method. Keyser then produced samples and sent them back to Rocket. “It was a week of back and forth with Red Label freight,” recalled Kampenga. “This time it was much easier with SolidWorks. If they had minor changes to a specific part number, it’s easy to move a couple dimensions, update the file, spit out a blueprint, and send it to the machine. Hands down, it’s been our greatest time-saver.”
As noted earlier, users don’t always capitalize on the full potential of the software.
“There is a motion simulation option, but I haven’t used it to its fullest extent,” said Kampenga. “I would especially like to work more with the rear four-link setup to see how everything moves.”
SolidWorks and Mastercam are arguably the leading CAD and CAM programs, respectively, but one shop is also working with Fusion 360 in the event that company starts to develop groundbreaking features.
“I felt if we got in on the ground level and they got stronger, possibly offering something better in the future, we’d be a part of it and it will speed up the learning curve,” explained James Nunn of Machine Nunn, Statesville, North Carolina, a shop with four CNC machines that helps produce threaded weld-in bungs and suspension components for race shops and aftermarket suppliers.
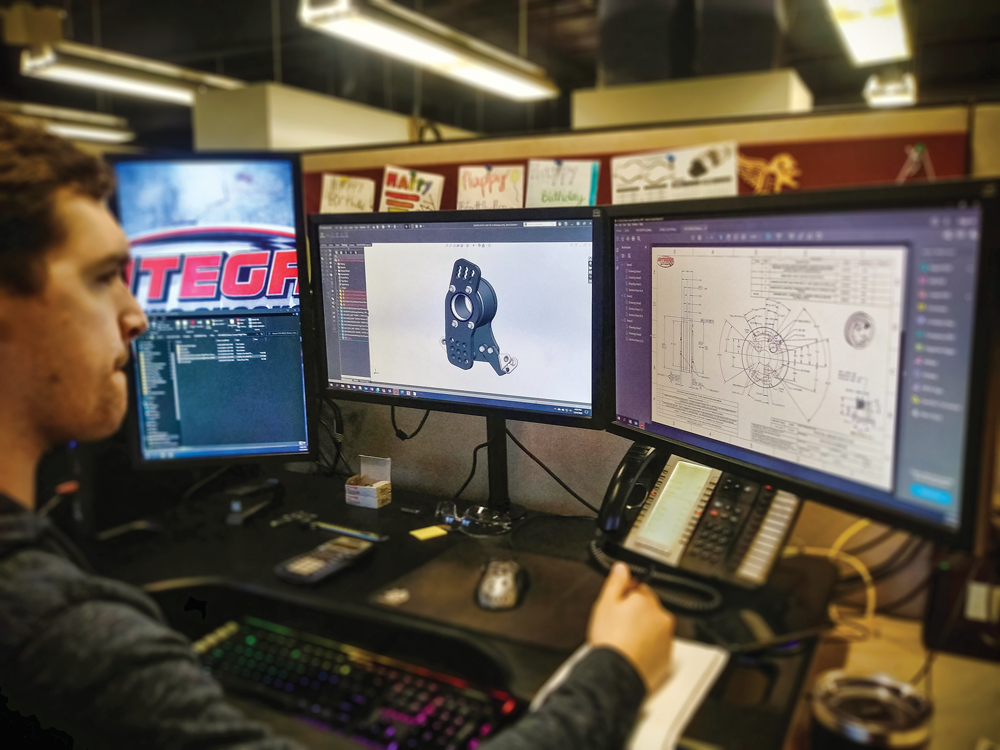
Regardless of the program, the objectives are the same: improve performance both at the track and in the shop.
“It is a parallel that we actually make with the motorsports industry quite a bit because there are a number of things that we do in the CAD/CAM world or the machining world that folks in the motorsports world do as well,” said Ben Mund of Tolland, Connecticut-based Mastercam. “Similar to what happens in motorsports, where potentially you have thousands of data points coming in real time to help the team make adjustments and refine what they are doing, CAD/CAM is similar in that aspect. As technology improves, there is a constant inflow of more information that can be used to streamline and optimize those toolpaths and cutter paths to make the machining process faster.”
By understanding the precise needs of its motorsports clientele, Mastercam can tailor features to help improve on-track performance.
“There are things that are done in CAD/CAM that are very specific to motorsports. In Mastercam, we have an add-on called Port Expert. It is used for other things, but its sole design purpose was to design, machine, replicate, and improve porting,” explained Mund. “As I am sure you know, that is an art that people perfected over decades. The repeatability and the slight adjustments were always something that folks in motorsports want to make sure they could get in. The Mastercam Port Expert is designed to do exactly that.”
Reverse engineering is a buzzword heard often when discussing CAD/CAM opportunities. As noted, it’s used in cylinder-head development after a specialist hand-designs a port; then that port shape is 3D-scanned or digitized before being manipulated further in CAD/CAM software.
DezignWorks, based in Mooresville, North Carolina, previously used SolidWorks and now has developed its own software just for reverse engineering. In a rather ambitious project, the company is taking a well-known German engine and adding cylinders to develop a marine version.
“We scanned the block and heads to have 3D models because no one is going to give you prints for them,” said Jim Watson. “They’re going to add a cylinder, and the first prototype will be all billet. They were going to increase the displacement, make it stronger, and put twin superchargers on it. The engine is designed for 2,500 horsepower.”
Working with numerous race teams over the years, Watson maintained a front-row seat in watching the evolution of CAD/CAM in the industry. “It has really changed everything, even with helmets,” he observed. “If you would see how helmets are fitted on people, it is crude. They actually just pull the foam out and they cut it and see how it fits. In one company we were working with, we put the fire mask on the driver and scan the head. Now you can CNC machine the plug to fit the person’s head exactly.”
Watson noted that this strategy is used on helmets designed for professional bull riders. The inserts can be changed as younger riders, or even racers, mature. If there’s a broken helmet, the current head scan will facilitate the new helmet much quicker.
In addition to creating its own design software, one company has expanded into designing and building machines to help shops improve their manufacturing processes.
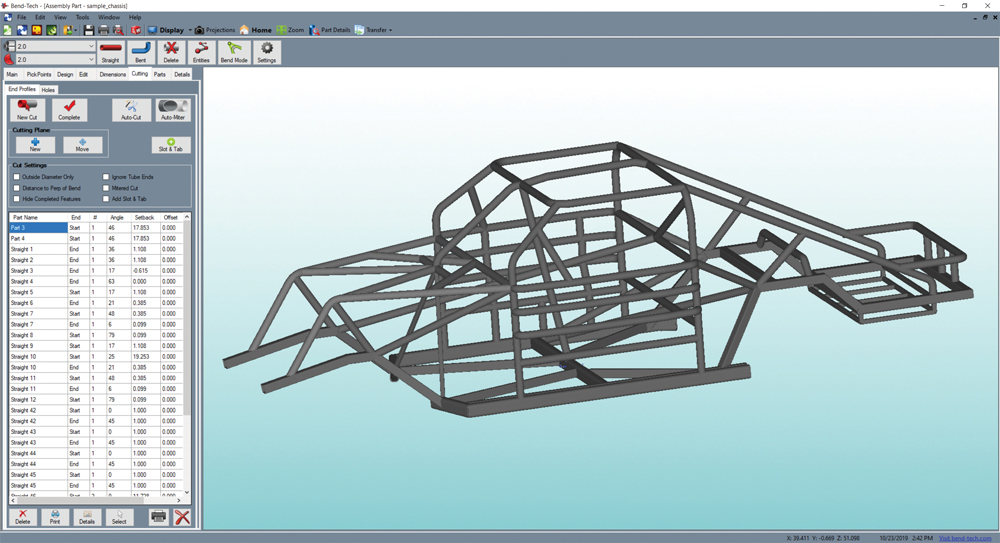
Bend-Tech in Osceola, Wisconsin, is best known for its tube-centric software that’s used primarily to design chassis, roll cages, and bumpers—almost any product where round or square tubing is used. Now Bend-Tech has developed automatic plasma cutters to process long lengths of tubing.
“They will not bend the tubes, but [instead] will mark the bending information calibrated to a bender on the tube,” explained Ron Dabill. “The operator can then take the tube over to their bender and line up the marks. It takes all that guesswork out. Of course, in the motorsports world that was huge. For guys who were building a chassis that took 50 man-hours, we were cutting that time in half by just taking care of all the cutting and the bending information.”
Plus, Bend-Tech’s software is improving, with new add-on features being developed to handle specific tasks more quickly. “There’s a template module with about 150 simple sheet-metal parts. A lot of our customers have plasma tables that aren’t really user-friendly, and a lot of these guys aren’t into CAD—they’re fabricators,” said Dabill. “So they want to be able to cut out a tab, a bracket, a beadlock—you know some of these simpler parts. Well, we give them a shape of what they want, and they put in their dimensions. They then save that off as a DXF file and bring it over to their CAM software for the plasma table.”
FUTURE NEEDS
Looking ahead, expect to see more partnerships between CAD/CAM developers and the machines they serve. Software will be better integrated to speed up the parts design and manufacturing process. As CNC machines and tooling bits become more sophisticated, software companies will move forward to ensure that users can get the most out of the operation. Even AI, or artificial intelligence, will be integrated into the software to create “smart toolpaths” that actually learn from previous jobs.
“It’s really such a wide-open field that anything could happen as we go forward,” claimed Mund.
Despite the unbridled optimism brought forth by CAD/CAM and CNC machining, many racers who rely on this technology nonetheless share a gloomy outlook due to difficulties finding qualified help to learn and program the software.
“There’s a gap between the engineer and the actual guy entering the toolpath,” said Nunn, who works with a local community college in hopes of getting more students into machining. “There just aren’t enough programmers.”
“In today’s age it is extremely tough—we’re constantly looking at new ways to train young people and get them interested in manufacturing and CNC machining,” said Cutler, adding that the DSR shop is also a full-service contract manufacturer to keep the machines running when racing needs slow down. “We have good equipment, which helps keep people around. We are always innovating, but finding good help is getting, without a doubt, harder and harder every day.”
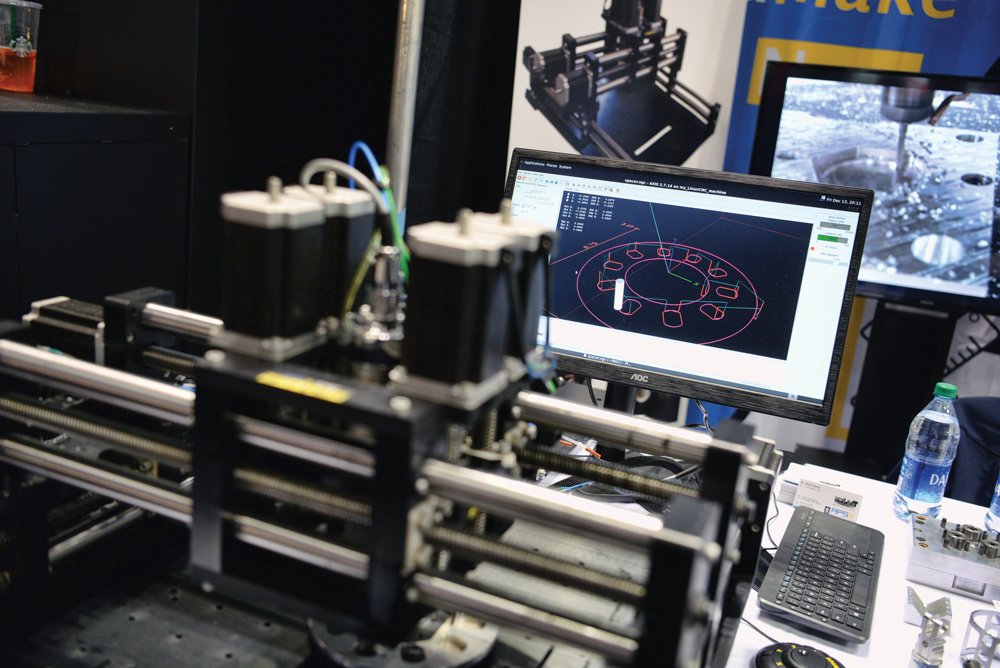
Vigue agreed, noting, “Manpower is a problem we’ve struggled with over the past year.”
While the line at this particular complaint window stretches around the block, some schools are in fact making an effort to bring students into the trade. And it should be easy, given the obvious widespread demand—i.e., the auto industry is also competing with petroleum, aerospace, and medicine for these same skilled workers.
“Ninety-seven percent of our students are hired before they graduate,” claimed Jud Massingill of the School of Automotive Machinists and Technology (SAM Tech), Houston, Texas. “We have an entire CNC course that includes programming.”
One of the stumbling blocks to entry, however, is that all students must pass a mechanical aptitude test to be accepted into SAM Tech. Then, a second math-based test is required for the CNC programming class.
“Some who fail the second test will take courses at the community college to improve their math skills,” said Massingill. “The future holds that more shops will upgrade to CNC machines and take on high-volume workloads. If you’re educated in CNC work and can put chips on the ground, you’ll get a job.”
SOURCES
–
3V Performance
3vperformance.com
Bend-Tech
bend-tech.com
DezignWorks
dezignworks.com
Don Schumacher Racing
shoeracing.com
Keyser Manufacturing
keysermanufacturing.com
Machine Nunn
machinenunn.com
Mastercam
mastercam.com
QMP Racing Engines
qmpracing.com
Rocket Chassis
rocketchassis.com
SAM Tech
samtech.edu