Fueling Development
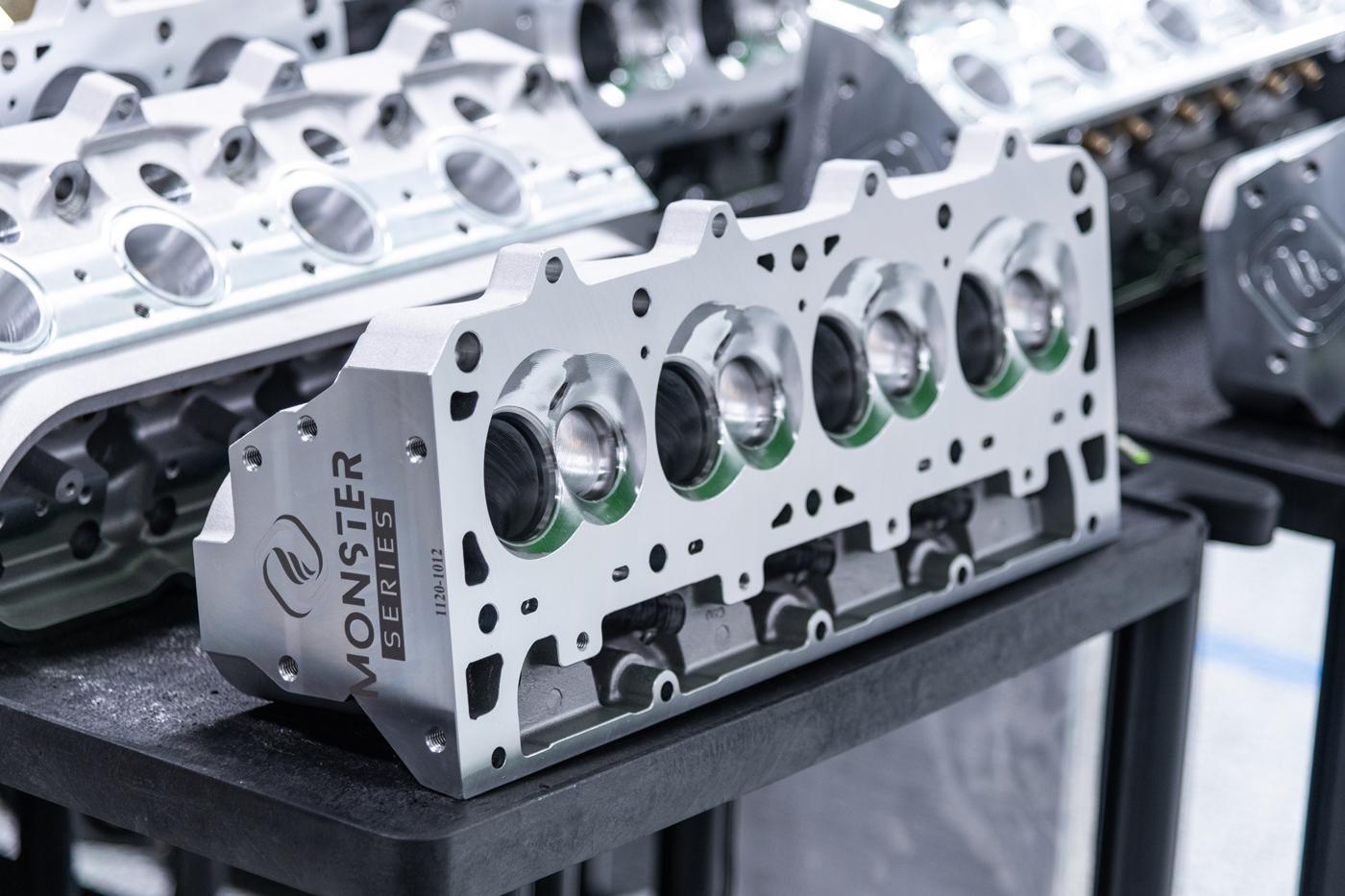
In addition to evolving performance products for the track, cylinder head manufacturers may also play an important role in the ICE vs. EV tug-of-war.
When asked about the future of cylinder head design with a sampling of aftermarket manufacturers, there were the expected replies of improving airflow with new port shapes, squeezing in bigger valves, improving valvetrain geometry, and even designing more billet heads with water jackets.
However, the topic of electric vehicles and alternative fuels came up more than once as a driving factor in cylinder head development.
“We’re constantly progressing and moving the needle forward on all designs. I think the one big thing we’ll probably see is just inevitable,” cautioned Chris Frank of Frankenstein Engine Dynamics, Weatherford, Texas. “With the competition of EVs, I think we’re going to see a lot of new fuels entering the market. We know, based on our experience, that drastically changes port design and also what the cylinder head will demand based on the new fuel requirements.”
“It’s interesting with the EV world, I think you’re going to see a lot of alternative fuels,” agreed Jason Youd of Mast Motorsports, Nacogdoches, Texas. “You’re going to see a lot of hydrogen, a lot of propane. You’re going to see a lot of alloy development in valve seats and valve materials to accommodate for hydrogen, because hydrogen is an animal in itself from the hydrogen-embrittlement standpoint.”
Youd admitted that the hydrogen future will more likely affect the industrial markets for which his company develops new cylinder heads. Frank, however, sees the possibility of more designer and synthetic fuels entering the market—which would require attention on the cylinder head much the same way the transition from carburetors to EFI did in Pro Stock a few years ago.
“There is a different demand from the cylinder head and intake manifold design than when we were running carburetors, and it’s going to be the same difference, I feel, when we’re testing and changing new fuels,” said Frank. “Fuels are going to get better, and cylinder heads are going to have to be a lot more efficient.”
Refining Current Designs
Constant improvement to maximize cylinder head efficiency is a common theme these days. The pandemic, however, presented challenges in labor, supply chain, and manufacturing to the point that some companies were forced to delay interesting development projects. Many of those are starting to come back.
“We didn’t show anything new at PRI, but we have a few projects in development,” said Mike Panetta of Dart Machinery, Warren, Michigan. “We’ll have a revised casting of our LS7 with new port designs. On the LS7, we revised the deck thickness after hearing from racers. Our head is currently .500-inch thick. With the increase in boost levels and horsepower, we’ve raised the deck thickness to .750-inch. We also made revisions to the water jackets to allow a larger port.”
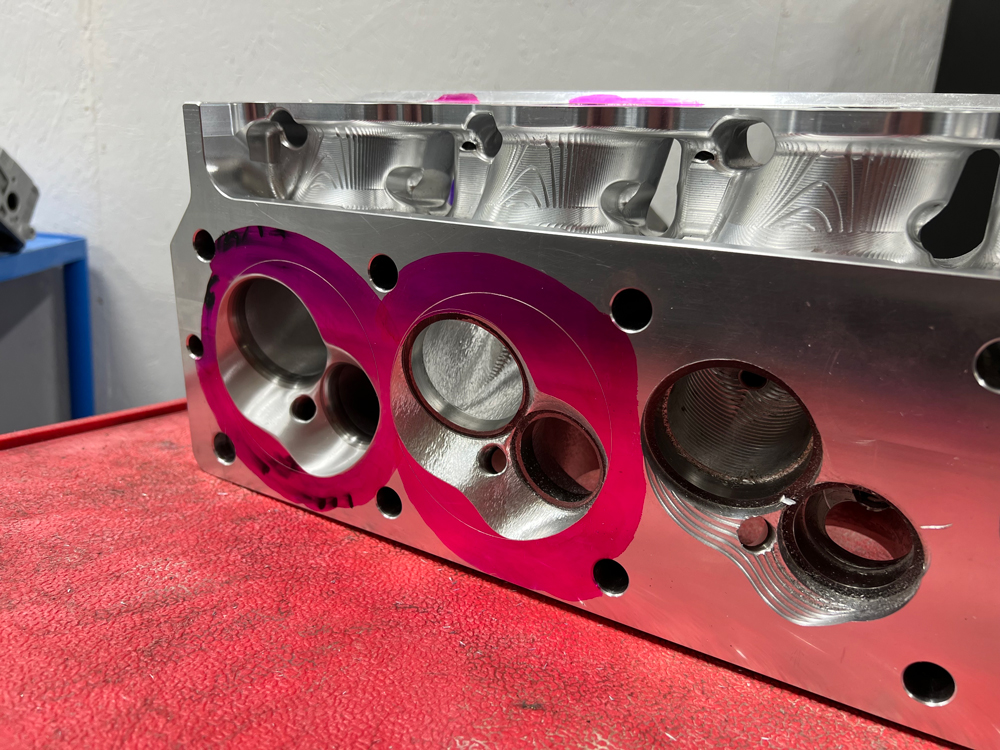
In addition, Dart Machinery is moving its as-cast LS3 Pro1 head down to the SHP line, which will bring the cost down and make it a little more user friendly. Then there will be a new CNC-machined LS3 design entering the Pro1 lineup.
Over at Brodix in Mena, Arkansas, no new cylinder heads have been released recently, but there is a big block Chevrolet head under development that might be available in the spring.
“It’s a new design of an older head, so we’re not going to release anything on it yet,” said Mark Fretz. “The majority of racing that it will be used in is drag racing, mostly naturally aspirated.”
Brodix engineers have been working on the head for close to a year, but the company remains extremely busy filling regular production orders.
“Getting guys time to break away from their normal jobs to work on a special project is pretty tough,” noted Fretz, adding that the decision to initiate the BBC project was spurred internally and not by specific racer suggestions. “We have ideas we talk about, and we figure out what the market needs. This is just increasing power.”
Fretz stressed that Brodix is always “modifying, changing, and improving” existing product. With an in-house foundry and pattern shop, small or significant improvements can be made in short order, such as modifying the water jackets to increase cooling around the spark plug or adding supports for a different rocker-arm mount. He said that although the company hasn’t developed an entirely new cylinder head recently, it has produced specialty castings on a private label agreement for select clients.
Edelbrock in Olive Branch, Mississippi, is another cylinder head manufacturer with its own foundry and the ability to make speedy changes. “Edelbrock has invested heavily in state-of-the-art manufacturing processes, and in doing so we now have the ability to 3D-print sand cores,” explained Mike Sanders. “This technology not only gives us higher production throughput, it also gives us the unique advantage of eliminating core draft. We can eliminate dimensional constraints within the core package to move port locations, guide locations and improve bolt-column strength without reducing material thickness. More importantly, we now have the ability to go from design to prototype casting within weeks and service multiple custom applications for our customers.”
Addressing increased levels of boost, Edelbrock has upgraded its Big Vic 12-degree cylinder head for big block Chevrolets. “We have improved the exhaust port, added a conical chamber profile, and replaced the ductile-iron seats with Copper B1 and BX material,” said Sanders. “All of these combined improvements will not only help with forced induction applications, but they will also improve tunability in nitrous-injected applications.”
The BBC platform continues to be one of the hottest markets in cylinder head development. Weinle Motorsports in Cleves, Ohio, has a CNC upgrade program for a Pro-Filer Sniper X casting that changes the valve-seat angles and reshapes the bowl above the valve.
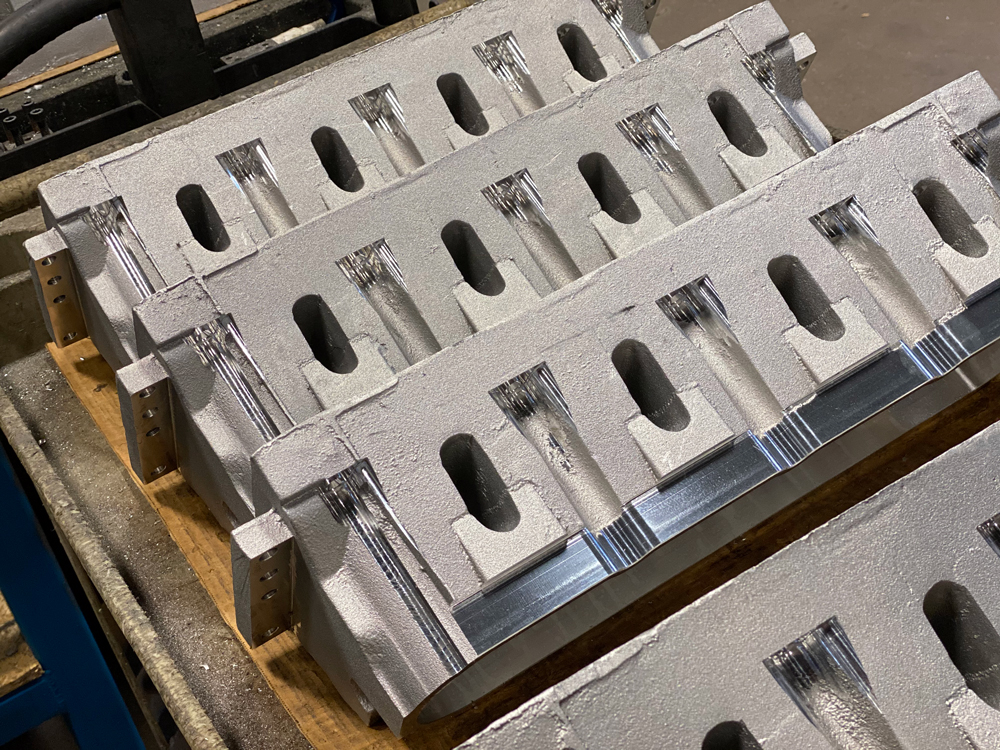
“The head is already one of the most popular out there,” said Mike Weinle. “We just made our changes, going with a 55-degree seat angle compared to 50 and made the bowl a little bigger. We picked up 10 cfm. It works best on a 600- to 632-cubic-inch engine.”
Weinle has a similar program that starts with a Brodix BB-3 CNC porter’s casting. He then machines his own port design to work with a 2.375- or 2.400-inch intake valve. The exhaust is reworked for a 1.850-inch valve.
“The valves are in the standard location, so you don’t have to buy special pistons and rocker arms,” noted Weinle. “Again, these heads are great for 600- to 632-cubic-inch engines. They’re economically priced and still flow over 480 on the intake. It’s a conventional style head, which we will sell three-to-one over, say, a Big Chief style head.”
Weinle said a conventional head is still a strong performer when drag racing on eighth-mile tracks. “Everybody went to a Big Chief style, then they started going back the other way,” recalled Weinle. “In the eighth mile, if you put on a strong enough conventional head, it’s only a couple hundredths different in ET. So, a lot of people don’t bother spending the extra money. If you have 75 or 100 more horsepower, you don’t really see that power until the second half of the track. It might be a couple hundredths in the eighth mile, but in the quarter mile it would be more. Today, most tracks run only eighth mile.”
Cost considerations will drive development when companies strive to offer CNC-ported performance in an as-cast head. Mast Motorsports focuses on LS, LT, and Godzilla applications. The company’s Black Label line is CNC-ported and may run $3,000 to $4,000 for a set of heads. By digitizing the ports on its LS7 head and tweaking those numbers in CAD, Mast developed an as-cast head with a strong port design.
“I’m working from the top down,” explained Youd. “Our Black Label flows 400 cfm at .600-inch lift. The as-cast Factory Mast head flows about 10 to 15 cfm less at half the price.”
Mast also offers a Mozez line of heads for extreme performance. “It’s a specialty market,” described Youd. “We really haven’t done too much development there. We did launch a second-generation Mozez line this time last year, and that’s done really well. We haven’t done any more development on that line. From a development standpoint, we are taking on a lot of private-label projects. We have various customers that are asking us to do the CAD, design work, and CFD, and then produce those cylinder heads for them under their name.”
One of the strong points for Mast in both development and manufacturing is a strong partnership with its foundry, especially in light of so many foundries experiencing difficulties in supply chain and labor. When Youd assumed control of the company in 2020, he formed a technical partnership with a foundry.
“We saw what was coming,” said Youd. “We retooled our entire product line in the last 14 months with the new foundry. Every single LS that we do is out of one casting at this point, because the permanent mold is almost $250,000.”
Developing News
As noted, creating a new cylinder head from a clean sheet of paper can take 18 months or longer, depending on the application. Having the versatility to produce different versions from a single mold—even if those different versions are for different-sized blocks—can be enough of a cost advantage to save a program.
For 1 Way Technologies in Washington, Indiana, a unique development story started with General Motors releasing the SB2 head for NASCAR racing in the mid-1990s, and later coming out with the SB2.2 version. Chris Grace worked for Weld Tech then, which had CNC-porting contracts with GM. Grace later purchased the company and merged with a customer to form 1 Way. When GM developed a new NASCAR block with 4.500-inch bore spacing—compared to the standard 4.400-inch—the ROX head followed, which was basically a wide-bore SB2.2. Other companies then started producing SB2.2 and ROX heads but soon discontinued their programs.
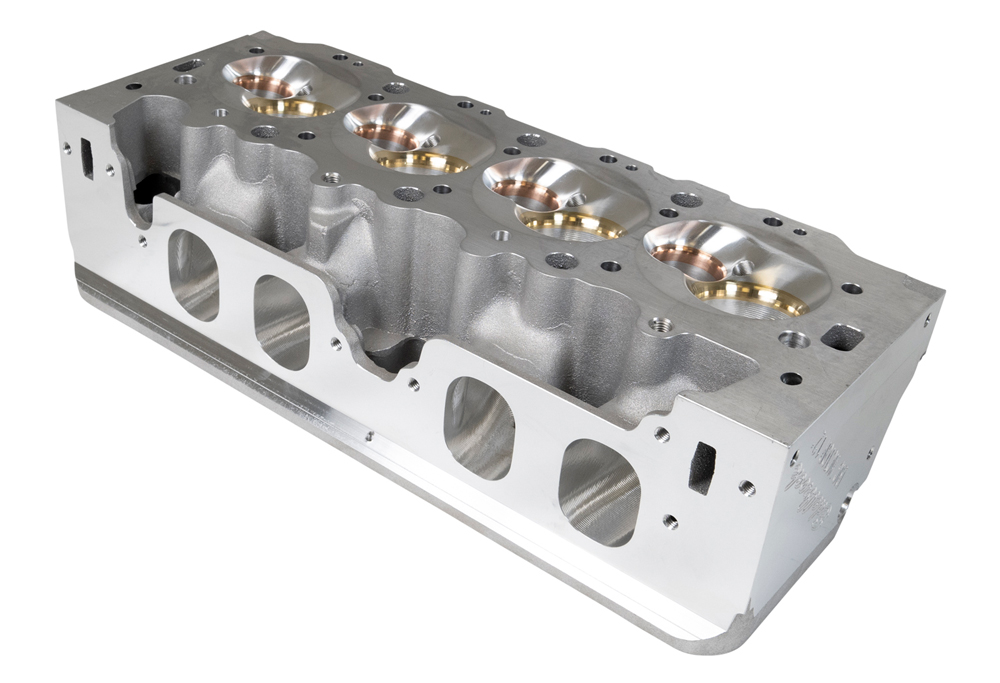
“There was a void in the industry, so I came up with the concept of making a single casting that I can machine an SB2 for the 4.400 block or a wide-bore ROX for 4.500 out of one mold,” said Grace. “The development process was, we had to overlay the head-bolt locations and put enough thickness there for all the head bolts. Also, make sure the valve-cover perimeter and everything would fit the port overlays. With the water jackets, we made sure that there was enough material for both shapes of intake and exhaust ports. In essence, there is less water in our casting, but I can use one mold and just have one casting poured for two different styles of cylinder head.”
Obviously, a choice has to be made between the SB2 or ROX design when the casting is released—the finished head won’t fit both blocks. But 1 Way does have some options in machining the head.
“We can stand the valve up and we can rotate the valves in the cylinder. Having more material in the casting allows us to be able to rotate the valves around as the engine builder requests,” added Grace. “We make sure there’s enough spring-pad material and guide-boss material down inside the port.”
Blueprint data were entered into a CAD model on the computer where all the design decisions were made. At times, the engineers wanted more material in certain places, but the foundry cautioned that they were already at a critical limit in those areas.
“That is one constraint we have with the head, but it hasn’t been harmful in any way,” noted Grace, adding that the casting is one of the most popular in the dirt late model market where the 4.500 ROX version is preferred. “But we’re also getting more calls from engine builders with the old SB2 Cup engines where their heads are getting too old.”
Grace said plans are in the works for another 1 Way head targeting the small block Chevy family but won’t get specific or mention the racing genre. He’s also been approached about doing a Ford head based off the D3 NASCAR design.
That is an application that Frankenstein is pursuing. “We are coming out with a canted-valve race head for small block Fords,” confirmed Frank, adding that a billet version is possible. “It would be like a hybrid. It’s not going to have the same architecture as the D3 or the [Edelbrock] SC1, but it will be in that category. It will be a full-race cylinder head, something that could be used from road racing all the way up to professional drag racing.”
Frankenstein also plans a traditional inline SBF head with raised runners. Both heads will have compatible intake manifolds. Also on the list is a LS canted-valve race head and a new 16-degree BBC. Again, dedicated intake manifolds are in the plan.
“One thing that we always take into consideration is that we like to design the entire induction package from start to finish,” continued Frank. “Just because the cylinder head is only one part of the air pump, and you really need to have an intake manifold designed specifically for the cylinder head it is being used on. We design ours to be very specific.”
Design Tools
Frankenstein has an in-house dyno and Spintron and has been utilizing CFD more in its design operations.
“One of the latest challenges in the CFD testing was optimizing spark-plug location with the chamber shape and valve locations on a new race head,” said Frank. “The valve locations were pretty aggressive, and it became slightly difficult to make sure the spark plug would be optimized. A lot of the changes were made to the intake port shape and valve job to guide the fuel charge in a different direction, to get optimal atomization and keep that plug happy.”
Computer tools are being used more often in the industry. Air Flow Research (AFR) in Valencia, California, is updating its CAD files with older products.
“We’re transitioning to have everything in CAD,” said Chris Sperling. “That’s more for internal benefit to give us flexibility with casting design.”
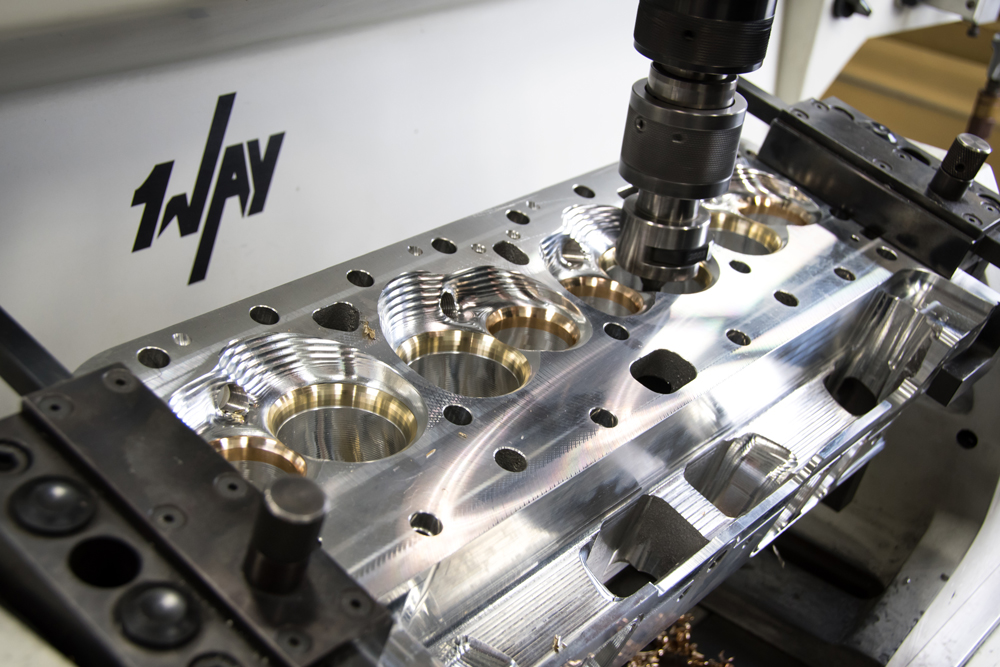
AFR’s latest cylinder head designed for the Mopar Gen III Hemi is now starting to hit the shelves. There was an early challenge in its development due to COVID-19, which forced engineers to work from home and hampered intense collaboration efforts. Once the team received more input from various parties and customers, changes were made in the combustion chamber size to reduce concerns from customers doing swaps where a smaller chamber might not allow the use of pump gas for street use.
“I’d say the major difference on this cylinder head from the past, we started to heavily utilize FEA and CFD throughout the development process on the ports, the water jacket, and the casting itself,” said Sperling. “A lot of what we have designed has been designed around proven methodologies that we’ve had, such as three-quarter-inch deck, our valve-job theories with different angles, and lengths of the valve job. We were able to take some of those theories, put them into CFD and FEA, prove out and/or improve upon what we’ve already developed.”
Lab testing has validated many of the computer simulations. The head will be offered in different versions to suit street and high-powered race situations. But it’s also getting harder to improve upon factory performance engines. In the past, a head and cam swap could easily pick up 50 to 70 at the rear wheels.
“In modern-day engines, the as-cast offering from the factory is very competitive,” Sperling said. “We’ve also been able to improve our casting technologies here at Air Flow Research. For a street-strip, entry-level, replacement-style head, most of our products are being transitioned to an as-cast cylinder head. The performance is just as good as our CNC-ported cylinder heads but at a lower cost. It allows more people to get into Air Flow Research products.”
For the Mopar Hemi head, AFR targeted an as-cast version with 186cc runner as a factory replacement. That same casting can also be CNC ported for larger versions. One CNC version has 2.125-inch diameter intake valves and 212cc runner, which flows about 40 cfm over the OEM head and is expected to perform well on the 6.4-liter engines. There’s also a CNC head with a 2.165-inch intake valve and 224cc runner that flows around 400 cfm at .700-inch lift.
Overcoming Obstacles
Cylinder-head development is not cheap, nor is there a quick turnaround when looking to create a new casting, especially if there’s some chaos in the supply chain. The pandemic forced the closure of some foundries, which limited options for World Products in Louisville, Kentucky, to develop new cast-iron heads for its catalog.
“We’re upgrading and retooling some products, possibly offering larger valves and updating the port design,” said Jack McInnis. “I don’t see us adding another engine family, it’s too prohibitive cost-wise. There has to be a market for iron heads that would support it. We still get requests from some loyal contingent of an engine family, but it’s not large enough to support the development.”
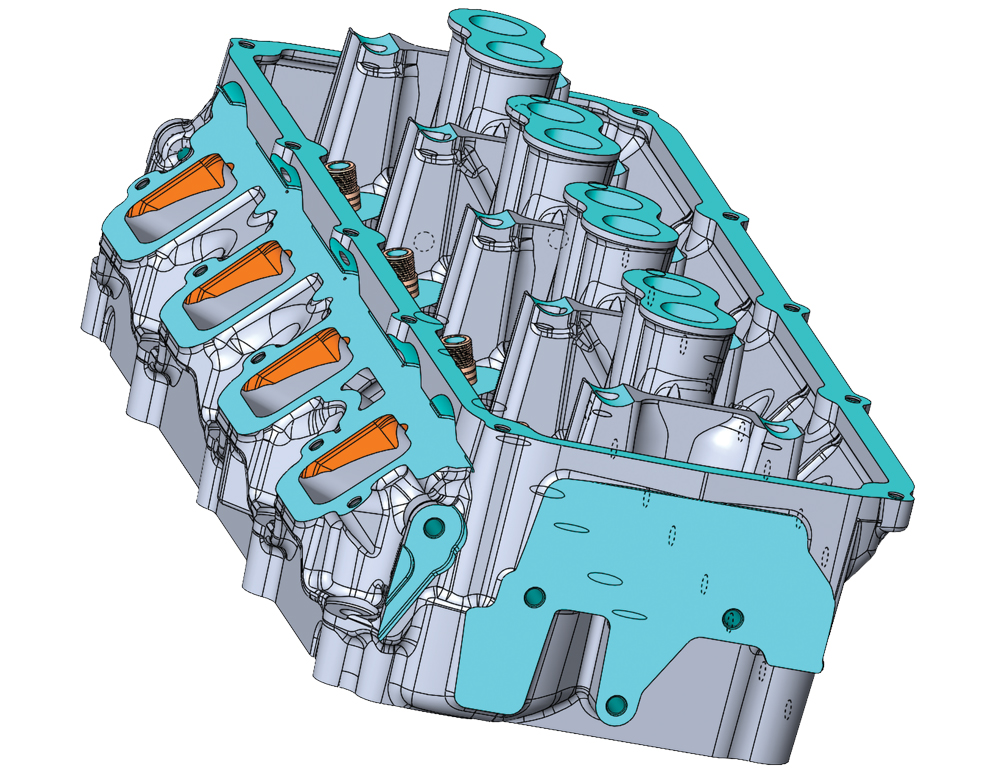
All Pro Cylinder Heads in Johnstown, Ohio, is well known for developing special projects for race teams, including factory-sponsored programs.
“It actually takes a lot of money and a lot of time,” confirmed Robert Williams. “Most people think that you can just make a cylinder head for $10,000 to $15,000. You’re going to spend $50,000 to $60,000 to maybe get the first part poured, and then that’s not going to guarantee that it’s going to pour correctly.
“I’ve given some serious thought to the new Godzilla engine, but I don’t think there’s enough market out there for it,” continued Williams. “Again, we’re going back to the cost of money to develop a cylinder head. You have to sell an awful lot of them to make it back.”
Technology that might speed up the process isn’t cheap, either. 3D-printed cores require engineers fluent in CAD design.
“It’s a big deal. It’s not something that an individual can do unless they’ve got a lot of money that they can put out there,” noted Williams.
Another factor driving development is the different uses for each cylinder head. All Pro has a 4.500-inch wide-bore head that dominates the dirt late model scene, but it isn’t useful in drag racing unless changes are made.
“To use that in a drag-race application, you would have to make some major changes to it to make the big horsepower numbers needed,” said Williams, adding that sanctioning bodies will also stifle new head development. “We’ve been bitten before by coming out with something new, and then somebody with a five-cent pencil said we won’t allow this. We’ve been doing this since 1983, so we’re not new to the marketplace. We’ve been stung on several good ideas.”
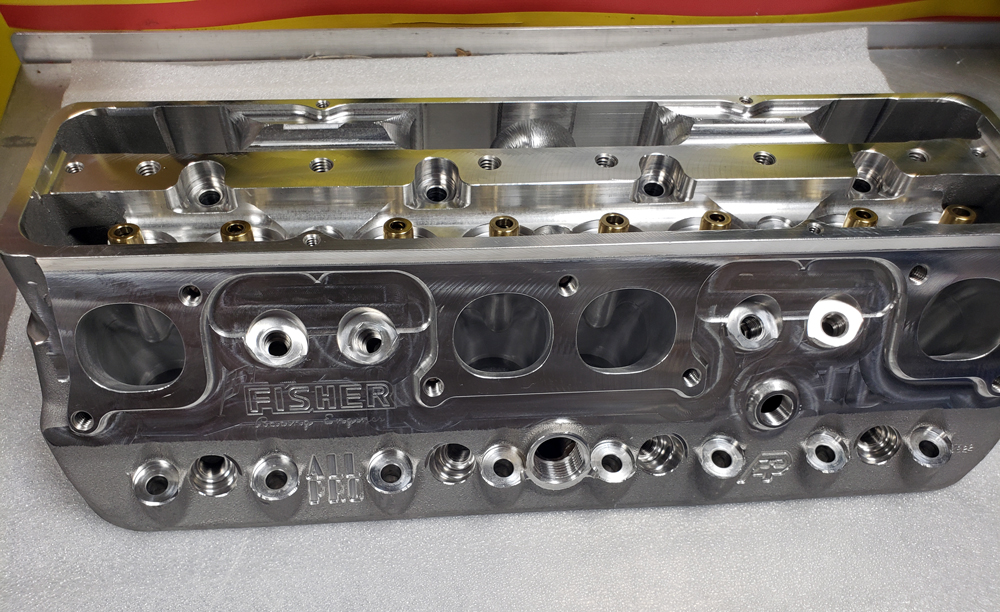
Williams said he didn’t get the written confirmation he wanted at first for the wide-bore head and postponed development. Meanwhile, GM was working on a 4.500-inch bore-space platform for NASCAR, and other cylinder head companies responded. It wasn’t until racers came to him with a request to build a competitive head.
“Because we’re not a mass producer, I feel we can make a better head. So, we built one, and it took off really well with engine builders,” said Williams.
What to Expect
As for the future, cylinder head development will follow the trends that are backed by the money. Boosted applications are certainly driving the features in today’s new products. The romance of developing naturally aspirated power is losing much of its passion because, quite frankly, engine builders have become so good at it.
“There’s always going to be improvements,” said Williams. “I think the improvements now are more subtle than they used to be. I think we are advanced far enough now that it takes a lot of changes to make 10 horsepower. Some of the builders, especially in the circle track market, are not inclined to go a new route simply because they have so many piston-rod combinations, crank combinations, and so forth on the shelf. For 10 horsepower, they’re not going to change it all.”
Williams shared the example that his 13-degree sprint car head is popular, even with global racers. He also offers an 11- and 10-degree head that can be worth an additional 10 horsepower. But on dirt, it may not be noticeable for a driver the same way a drag racer could see the improved ET.
“If anything, it might slow you down because you’re going to spin your tires more in the dirt,” he explained. “The good drivers who are going to hook a car up are going to go a little faster, but are 10 horsepower out of 950 worth it?”
LS head technology could also provide measurable improvement in the sprint car world, but so many other changes would have to be made to the engine that the cost effectiveness of such a swap is not worth the trouble to many teams. They’d have to change headers, intake manifolds, pistons, and other components that they’re comfortable with.
“Teams would like to see an engine with a better cylinder head that fits their package,” said Grace. “So, we’re limited with that working space.”
“The development of cylinder heads will never stop,” added Sanders. “It’s a moving target year over year as engine technology and markets change. There is still power to be found through extensive research and development.”
“In development, it’s all about how big the market is,” added Panetta. “I could have one person come in and want us to do a single set of heads, with every trick in the book, and we could do that. But it’s not cost effective. So we have to look at the larger picture. How many units can we sell? How big of a market reach do we get from that? And that’s kind of how we redirect those new projects.”
Sources
1 Way Technologies
1way-tech.com
Air Flow Research (AFR)
airflowresearch.com
All Pro Cylinder Heads
allproheads.com
Brodix
brodix.com
Dart Machinery
dartheads.com
Edelbrock
edelbrockgroup.com
Frankenstein Engine Dynamics
frankensteined.net
Mast Motorsports
mastmotorsports.com
Weinle Motorsports
weinlemotorsports.com
World Products
pbm-erson.com