Special Report: Supply Pain
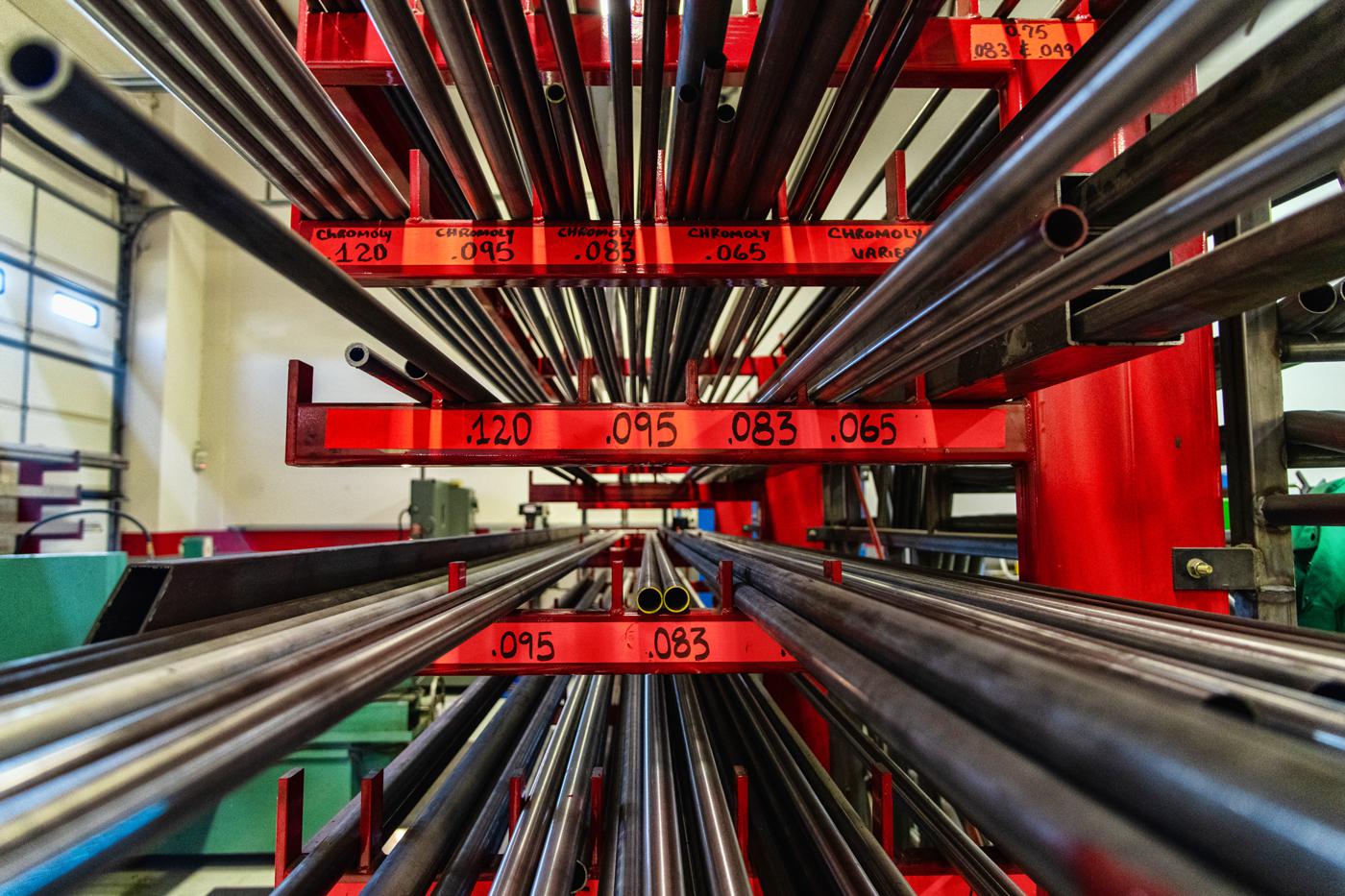
When it comes to sales forecasting for the 2022 racing season, a solid outlook is decidedly difficult to pin down.
Talk about a moving target.
As this is being written in early November, record numbers of container ships are loitering off the coast of California, suppliers can’t keep racing parts on the shelves, Help Wanted signs are everywhere, and things may very well get worse before they get better. Demand is surging, yet supply is locked down in a chokehold that would make a professional wrestler proud.
How does a business forecast sales for the 2022 racing season? Consult astrological charts? Read entrails, like an old-school shaman? Flip a coin?
Things may not be that dire yet, but there’s no easy way for motorsports businesses to forecast the inventory they’ll need for the upcoming racing season. With shortages happening in almost all areas of the sport, even relying on long-established business relationships with suppliers is no guarantee of getting a clear picture of parts availability.
“There is no working with suppliers to ensure anything. Because they can’t ensure anything. Nothing. It’s the most frustrating time I’ve ever had in 48 years of doing this, as far as parts go,” said Mike Johnson of JMS Racing Engines, El Monte, California. “It’s dragged on for so long now that we can’t even get estimated dates on when parts will be available. I have two high-end race engines that have completely missed the racing season because I can’t buy a block or a pair of cylinder heads. When I call, they used to say, ‘Oh, we’re looking at 90 days, we’re looking at 120 days.’ Now they say, ‘We don’t know.’”
“The forecasting is impossible. We do the best we can,” said Paul Banghart of GAT Racing, Tucson, Arizona. “It’s a little scary to get way ahead of the curve because if we get way ahead on something and have a ton of them in stock, and then all of a sudden somebody gets a bright idea and changes a rule, now we’re stuck with 150 tires that can’t be used.
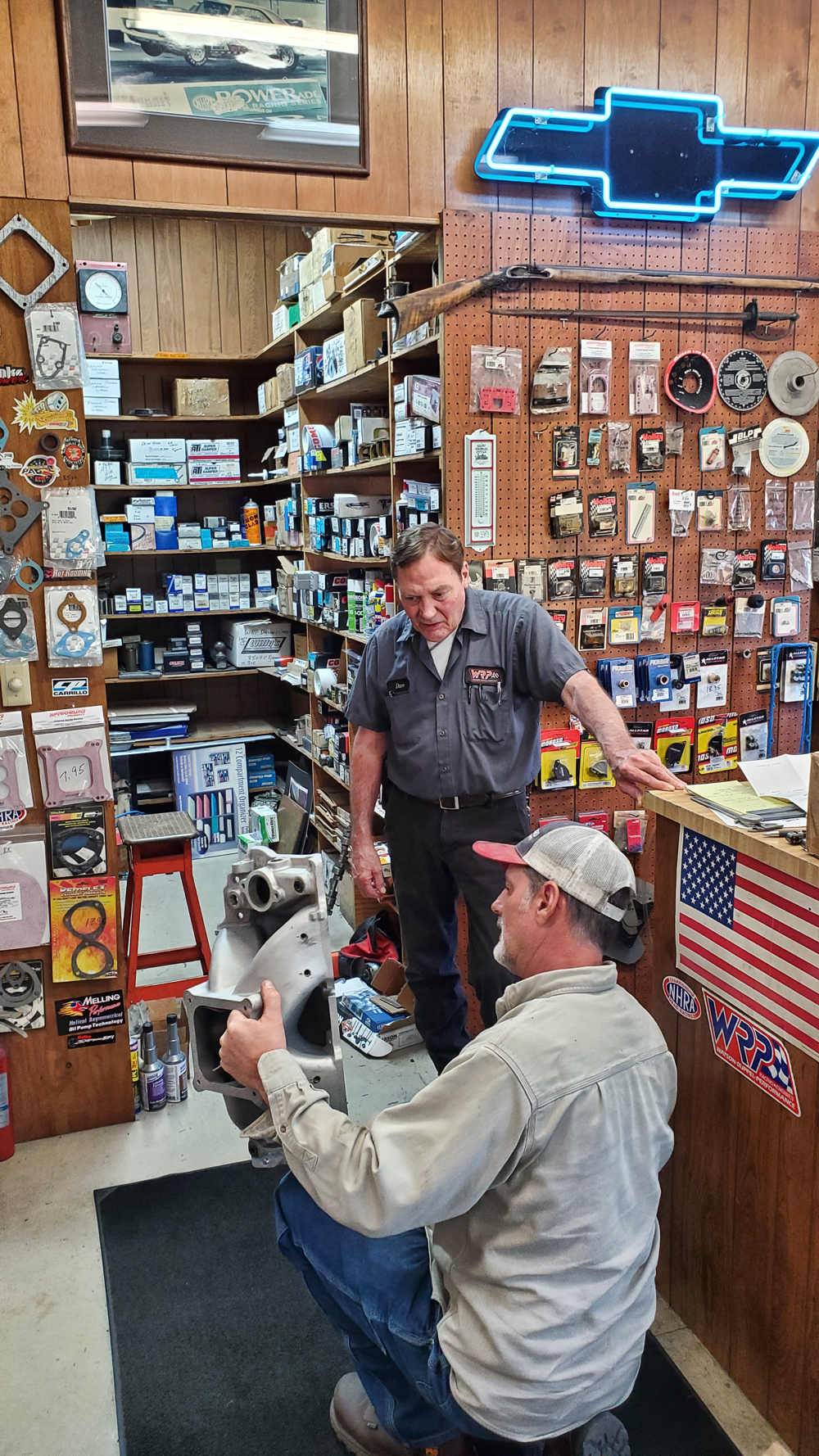
“So far, so good,” Banghart continued. “We’ve been keeping up, but it’s definitely been hard. We’ve had to say no to people this year more than ever before. ‘Nope, I don’t have it. And nope, I can’t get it.’”
Given the interconnected nature of the motorsports supply chain, a shortage in one area can send ripples through entire racing series. Boss Chassis, in Belleville, Illinois, specializes in midget and micro chassis. “There are only a few manufacturers for the rearends that we run. Same with the steering gears,” said Austin Brown. “If any of them have issues, everyone would have issues.”
Despite delays and shortages, our sources indicate that racers are still keeping the throttle wide open when it comes to ordering parts. “We haven’t seen the parts shortages discouraging a lot of folks from building engines or racing yet,” said Heath Watson at Watson Ruppel Performance, Sarahsville, Ohio. “Racers are very passionate, and most of them are going to find a way to get on the track, even if there are more challenges to do so.”
Part of that ongoing demand is undoubtedly related to people wanting to get back to “normal” life following the lockdowns of 2020. But a contributing factor could very well be that many racers are opening their wallets now because they realize inflation is running rampant, and things will only cost more in the future. If that’s the case, it’s going to be hard for manufacturers and suppliers to get back ahead of demand in the short term.
Out of Order
In this environment, businesses have no choice but to adapt as best they can. “Our parts-ordering process has definitely changed. We try to look ahead and order parts early,” said Watson. “We are also investing a lot more time in locating parts and often pay more for them when we finally find what we’re looking for. Prior to 2020, common parts were stocked at nearly every distributor we deal with. Now we often must check with all our distributors, and with several websites and do Internet searches before we might find the right part.”
Having plenty of sales data on hand always helps, but data from normal years has limited use in this economic environment. “I’m a pretty big proponent of looking at the macro sense of the economics,” said Jesse Olson of Medieval Chassis, Mayer, Minnesota. “Obviously, we have a lot of background information in our online sales, as we have our own online store. We use all the Google Analytics to see month-by-month, quarter-by-quarter, where we’ve been sitting year-over-year and try to forecast that in for our build schedules when it comes to our chassis, parts sales, things like that. With us being a manufacturer, we produce a lot of the parts that we sell in-house, a lot of the bolt-on accessories and so forth.
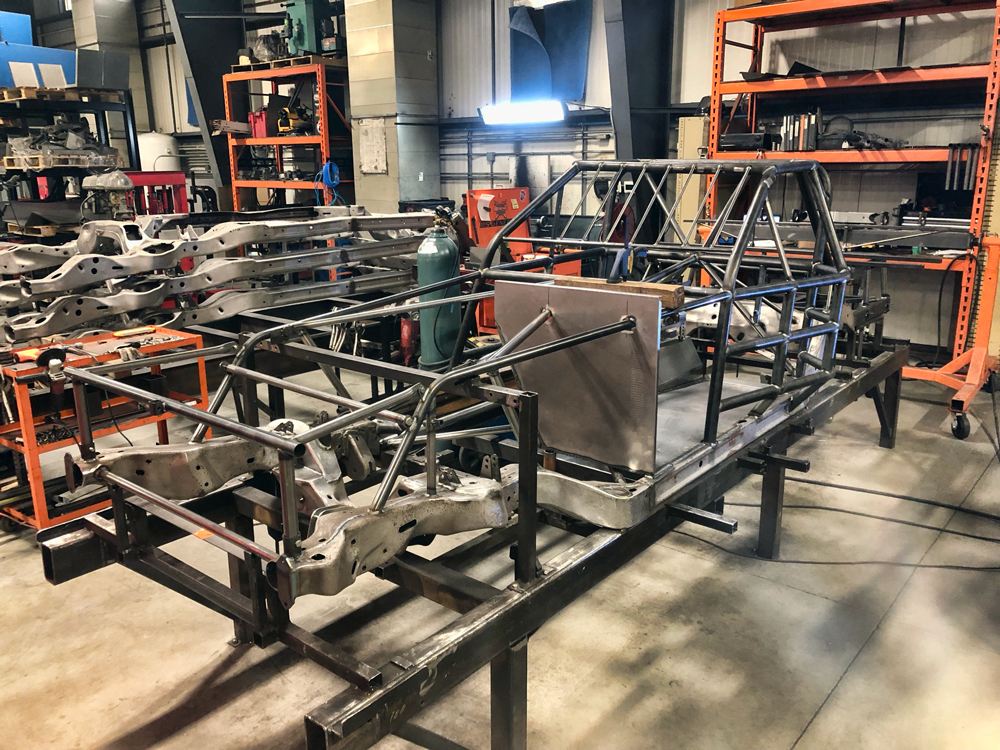
“From the macro sense, we’re just watching what’s going to happen after the beginning of the year,” Olson reported at the close of 2021. “I don’t think anything is going to change. We’re on the up right now. People basically want to get out and work on their cars and get going for next year already. Usually we see a lull of about a month between the last week in October to about the first week in December. Guys have harvesting and will be in the field, or deer hunting, and so forth. This year we have not seen that at all. Every week it’s just more and more and more.”
Although parts of all sorts are in short supply, certain items kept being mentioned by our sources. “Our biggest challenge right now is with a certain few products like tires, which is a huge one,” said Banghart. “Sheets of aluminum are huge problems for us right now. Assuming that things are going to be held up, assuming what normally comes in a week or week-and-a-half will be four to five weeks, we’re just trying to forecast that. It’s obviously really hard. We’re calling the suppliers every so often to ask if they have any information. Sometimes you get a good answer, sometimes they don’t have a clue.”
“What I’m hearing from the manufacturers is that a lot of the time they can’t get the material,” said Johnson. “It’s widespread, through pistons, connecting rods, cranks, heads, blocks. There’s a shortage of valve springs. It’s crazy.”
It’s not just the parts that are delayed. “Even the powder coaters are so backed up that they can’t give you a date, and they don’t have employees so they can only do one certain thing,” said Brown. “It’s just about everything we deal with. It’s hard to even give a customer a date if it can’t all be done in-house.”
“A lot of stuff that we do is not necessarily cookie-cutter stuff. So we’re trying to find a balance of what we think we’re going to need,” said Trevor Hutter of Hutter Performance, Chardon, Ohio. “In some instances, when we use a part off the shelf, I can reorder it immediately, knowing that it can take sometimes 12, 14 or more weeks for stuff. If we’re using something that I’m pretty confident we’re going to use again, I’ll just reorder it right away. But, man, the stuff that we need to custom order, we have to warn people ahead of time. We used to be able to pay for expedited stuff. Some people aren’t even doing expedited at all because everybody wants everything expedited.”
These shortages are reminiscent of the first few months of the pandemic, when grocery shoppers encountered empty shelves. “What’s happened in the industry, I want to call it the Toilet Paper Syndrome,” said Johnson. “It just creates more of a shortage because of the hoarding. And I’m guilty of it too! It’s like, ‘Oh, no main bearings for big block Chevy. Oh, there’s four sets.’ I buy them all. It’s just so amazing to me that the manufacturers are so far behind and can’t get caught up.”
Domestic vs. Import
There’s another conversation that industries both large and small will have after the supply chain cyclone stops wreaking havoc and some semblance of predictable sales forecasting returns. That conversation revolves around the accepted economic wisdom of just-in-time delivery models reliant on the unhindered flow of global trade. That model has enriched many, but it’s a model that relies on nothing ever going wrong.
It’s inevitable that people will talk about sourcing more American-made parts and forming domestic supply chains that are less vulnerable. Some of the businesses we spoke with pointed out that partnering with more domestic suppliers has relieved some of the parts availability pressure and helped with sales forecasting.
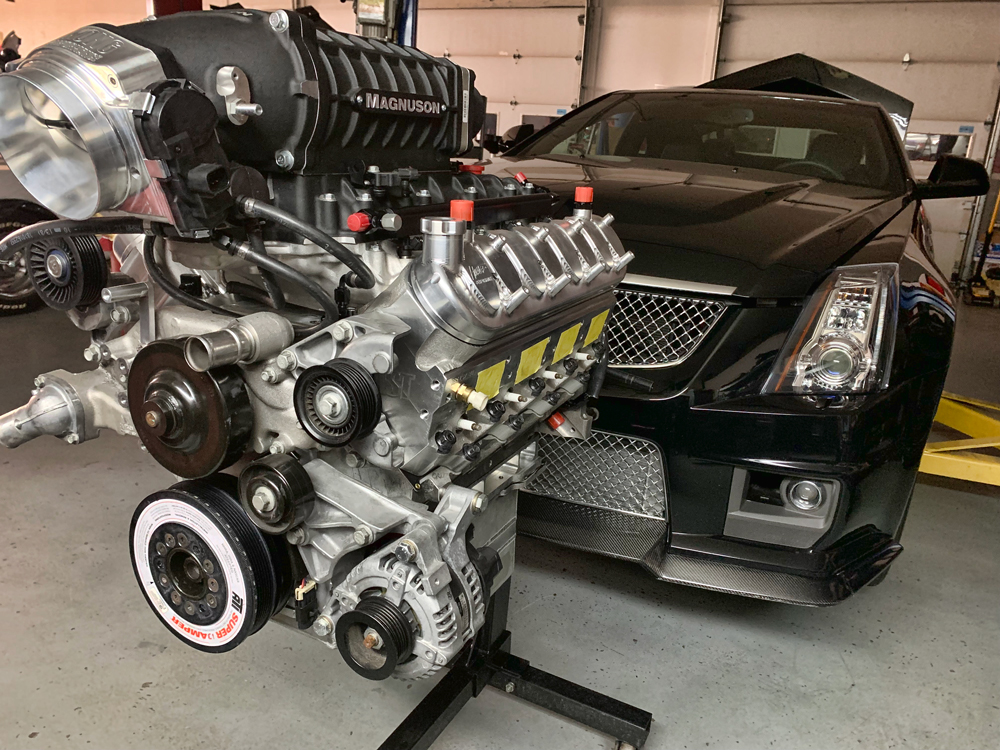
“I’ve always been a very big proponent of buying domestic, and it seems like the domestic items are available,” said Medieval Chassis’ Olson. “They’re not the cheapest, and racers don’t always like that. But the domestic sources are typically available. Aside from a couple of larger items—hub assemblies, things like that that we can’t control—everything else we source domestically.”
According to Olson, the difference between locking in domestic sources versus foreign suppliers isn’t just an improvement at the margins. “It’s dramatic,” he said. “Something as simple as, say, rearend snouts. In the past, what everybody did was source them overseas to get the cheapest price possible to make the biggest margin. Well, as things have stopped as far as the imports go, the domestic sources have opened up, and they’re on the shelf. We have changed some suppliers on that front, knowing what was coming. With some items, we are taking it upon ourselves to create a domestic source so that option is out there for the racing industry.”
GAT Racing’s Banghart also reported that buying domestic has helped ease some of the supply pressure. “There are probably three or four companies we deal with that manufacture onsite and ship straight out. Honestly, I would have to say, they’re pretty good,” he said. “Those three or four companies that build stuff and ship it, where it doesn’t go to a warehouse first, their fill rate is probably better than something that I buy from overseas.”
The search for domestic sources can often drive businesses to take another look at their local industrial scene. “On my end, I haven’t had an issue with getting metals, aluminum and tubing,” said Boss Chassis’ Brown. “We have a big supplier in St. Louis that’s maybe 20 or 30 minutes from us, so I don’t have to have it shipped in, I can just drive there and get it myself. Obviously, the prices have increased, and they try and let us know, but it’s just so unknown.”
2022 Season
As for what racers should expect for the 2022 season, the outlook is still murky. But there are a few things safe to predict. For one, it’s going to be more expensive.
“I’m telling them to expect price increases on everything, which we are absolutely seeing, and increased lead times on everything,” said Banghart.
“Any time there’s a shortage, prices are doubling and tripling,” said Johnson. “There’s another problem that all of us are dealing with. We all have a parameter of a quote in our heads. We’ve been doing this long enough so if a guy says, ‘What do you think it’ll run?’ we have an idea.
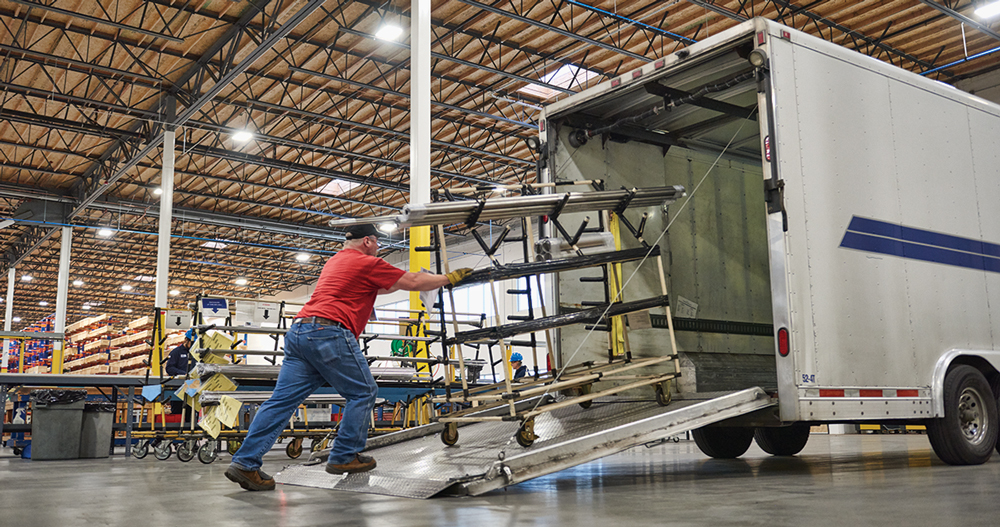
“Right now, a crankshaft has gone up 30%. But they’ve done it three times this year,” Johnson continued. “Typically, in this industry, we would get a price raise on parts around February every year, 3%, maybe 4%. We got price raises in February of 4%. I got another price raise in June of another 6%, and I just got letters that parts are going up again. And every one of them is saying ‘due to the cost of materials.’ It makes it really hard to be able to even quote anything right now.”
“On steel, we’ve seen about a 10% cost increase in total, which for us is a lot,” said Olson. “Most other manufacturers, I’m guessing, are probably seeing a 30% to 40% cost increase. Again, just because of the volume that we run through here, our costs are pretty limited as far as increases.
“Aluminum is going to be the big one,” he continued. “We’re seeing 10% month-over-month here since March. That is not going to stop until probably March of 2022. A sheet of aluminum is going to be close to $200 here by the time all is said and done. That’s going to get pretty hard for modified guys, and dash kits, things like that, on other cars. The other side of it are the labor costs and all the indirect costs—powder coating has gone up, consumables have gone up, welding gasses have gone up.”
On a more positive note, it’s likely racers can look forward to rules stability from the sanctioning bodies, as any abrupt changes to the rulebook could run into the reality of parts that comply simply aren’t available. “I’ve seen a little bit of easing up on allowing a different tire for an event or two,” said Banghart. “IMCA now allows grooving of tires because of the tire shortage. They figure people get more life out of them.”
So what can racers do to prepare for the 2022 season? For one, start planning sooner. Don’t wait until three weeks before the season starts to begin work on the race car.
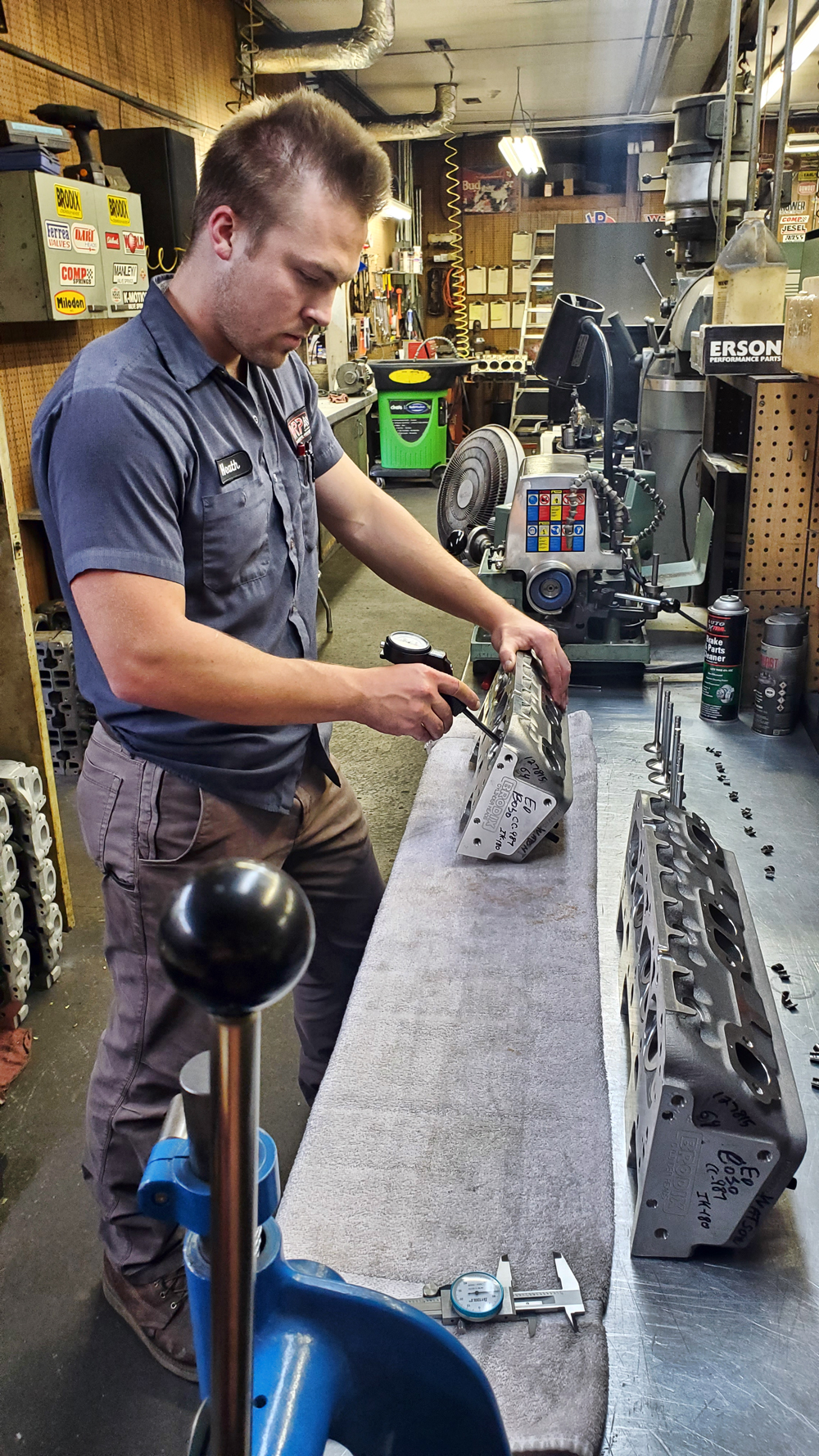
“We have seen several acting sooner to get their engines pulled and begin the rebuild process earlier in the offseason than in previous years,” said Watson. “That will be helpful in getting things back to them in plenty of time for next season. We often don’t know what parts will be needed until we tear down and inspect the engine. The sooner we do that, the quicker we will be able to order the parts that may be backordered or hard to find.
“We are talking with our customers about parts availability issues, but most of them already know about it to some extent from their own research or talking with other racers and gearheads,” Watson added. “Shortages are happening in every industry, so I don’t think it is a surprise to many people anymore. Most people are understanding of that.”
“The more pre-planning you can do, the better off everyone is going to be with how long it takes to get stuff,” said Hutter. “People call up and say, ‘Oh, we don’t need it for a month.’ Well, okay, that’s about a quarter of the time it’s going to take to get the parts you need.”
With shortages likely continuing for the foreseeable future, racers may need to dust off or relearn some old skills. “The racer will need to be prepared as much as they can, as far as getting their spares and whatnot together,” said Brown of Boss Chassis. “They may have to go back to not being able to just purchase products right off the shelf. It would be neat to see racers build their own parts again.” There was a time when racers, out of necessity or simple ingenuity, took a more hands-on approach to making parts themselves, he said. “We may see more teams start doing that.”
In the meantime, racers and suppliers both will have to grin and bear it. Johnson of JMS Racing gave us the forecast for the winter: “The frustration level is everywhere. I have frustrated customers, which frustrates me. I call the manufacturers. I’m frustrated so I get on one of them. They’re frustrated from getting bitched at all the time. It’s just a frustration chain now.”
SOURCES
—
GAT Racing
gatracing.com
Hutter Performance
hutterperformance.com
JMS Racing Engines
jmsracingengines.com
Medieval Chassis
medievalchassis.com
Watson Ruppel Performance
wrpengines.com