PRI Tech: Fuel System Strategies
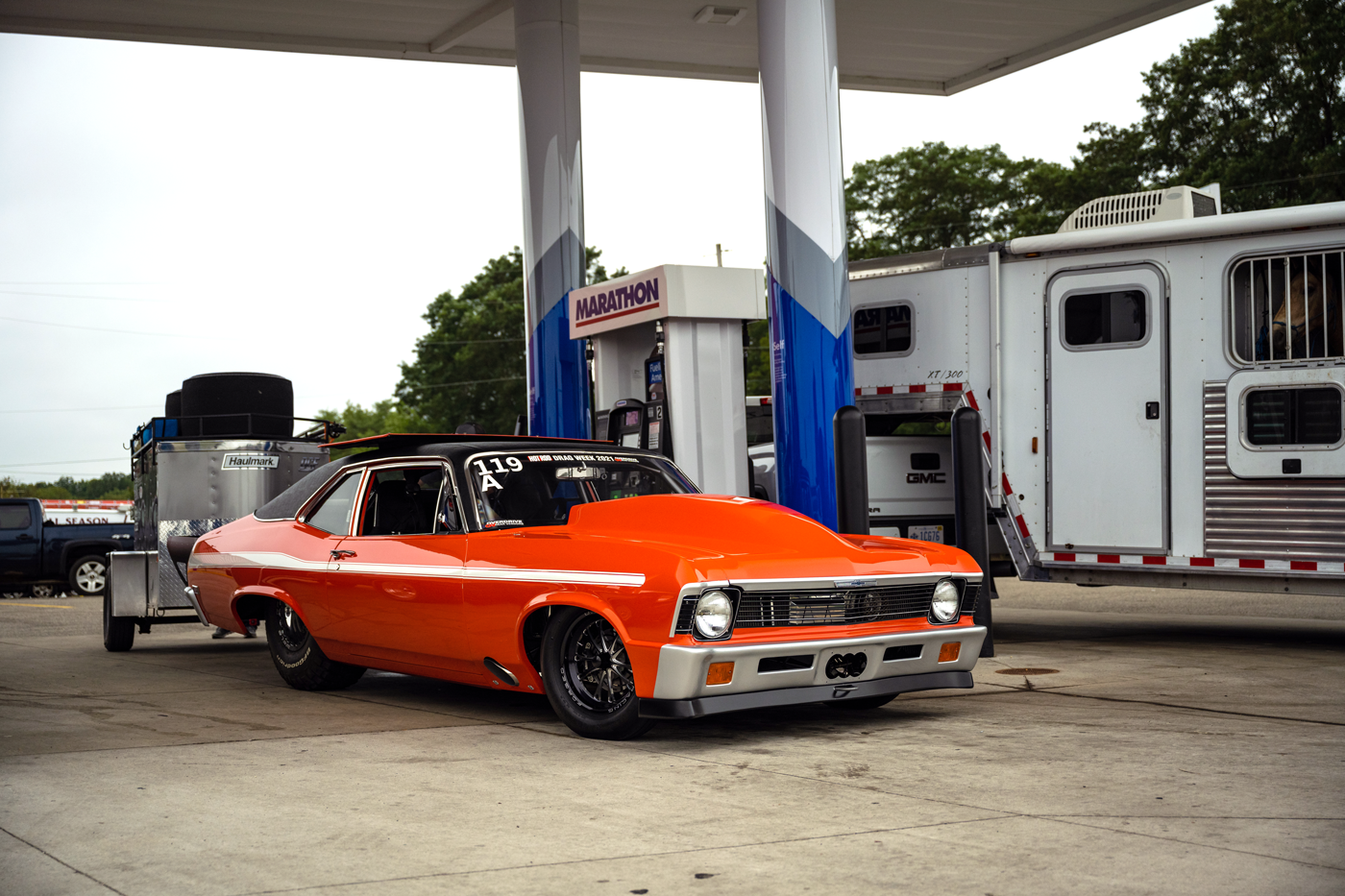
Engine builders have few restrictions in drag-and-drive events as well as no-prep and small-tire classes. This blurring of the lines between street and strip performance translates to increased power levels, which requires greater attention to the fuel system.
The determining factors that are most important when putting together a fuel system.
The racing and street-performance landscapes are starting to look quite similar these days, especially when considering engine power and fuel-system setups. The same fuel pump or turbo may be used on a restomod Chevelle or an X275 doorslammer. There is a definite blurring of the lines between street and strip performance.
Among the reasons for this is the increased popularity of drag-and-drive events along with the tremendous amounts of horsepower we’re seeing in no-prep and small-tire classes at the drag strip. Few rules are holding back engine builders in these events, which means as the power levels increase, more attention must be focused on the fuel system. However, it is becoming more challenging to design a system that works both on the track and the street.
From the calls I get, at least 30–40% have a race car they want to drive on the street. Or they have a street car that they want to race at the track, and they want to run fast, real fast!
When I started with Aeromotive 22 years ago, the A1000 was the creme de la creme for an electric EFI fuel pump. There was nothing else out there that could compare. It was a 1,000-hp fuel pump. At that time, that was the dream: to own and drive a 1,000-hp street car.
Today, we’re getting to the point where if a person calls in and they’re not claiming to make 1,000 hp in a street car, it’s almost a surprise. It just seems like everyone is either making 1,000 hp now or planning to in the near future. That has changed everything when it comes to setting up fuel systems in “street cars.”
Besides gasoline as a fuel, ethanol/E85 and now even methanol have come into the picture in a big way. That’s thrown a big curve at fuel delivery for a multitude of reasons, the least of which is the solvent nature of alcohol fuels (ethanol and methanol). E85 will, in minutes, strip all the shellac from inside of a tank that’s held gasoline for years, potentially clogging the first few fuel filters on a new system. Also, the fuel lines and filters become management issues as they must be E85 compatible, and given the strong solvent nature of E85, filters require more frequent service. This is particularly important with big pumps.
Also, E85 requires more volume to make the same power. It’s going to take 30% more fuel using E85 to make the same power with gasoline. Methanol requires double the fuel volume of E85 for the same power if that’s an option for a particular customer.
New Technological Developments
Given the challenge of chemical compatibility, and the additional volume requirements to change to alcohol-based fuels, compounded with the rapid increase in the raw horsepower potential of modern-day engines, we’ve had to aggressively develop new motor and pumping mechanism technologies, along with special fuel lines and filter media to keep up.
Today, some street/strip or drag-and-drive racers want flex-fuel capability; that is, the option to run any mixture of gasoline and ethanol in the fuel tank. A couple of important points must be acknowledged. First, you need a flex-fuel sensor, and Aeromotive offers a high-flow flex-fuel sensor adapter with a built-in bypass so an OEM-style sensor can be used that would otherwise be too restrictive for the higher flow fuel pumps required to do the job.
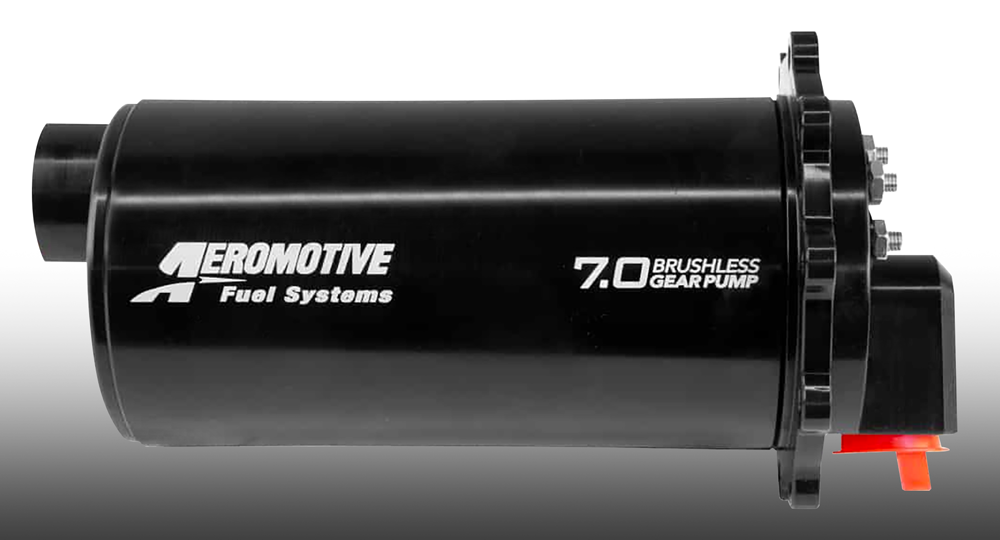
Talking about big pumps on street/strip cars, for those who decide to make a significant upgrade in power, and then change to E85 for example, Aeromotive offers inline and in-tank brushless gear pumps rated for crazy flow numbers from 3.5 and 10 GPM (1,250–3,400 flywheel hp). Further, these brushless pumps can include our TVS (True Variable Speed) Brushless Motor Controller technology for continuous duty with reduced recycling and fuel heating in the tank.
We also have mechanical fuel pumps that can deliver from 2–120 GPM, used in almost all forms of motorsports from nitro-burning drag cars to offshore marine, from Indy cars to NASCAR, and everything in between.
But there’s more to setting up a complete fuel system than just stepping up to a more powerful pump. The biggest mistake we see people make when upgrading a fuel system for a big increase in power is that they’ll change the pump but fail to upgrade the rest of the fuel system to match. That is, they don’t understand they’ll need bigger fuel lines, bigger filters with more surface area (higher flow capacity and appropriate service life), and a fuel pressure regulator that can handle the big jump in flow volume while keeping pressure under control.
Aeromotive is an engineering company, with a “pump-centric” approach to fuel system design. This means we seek a flow problem to solve, then engineer, design, and test a fuel pump to do the job. That done, we then engineer the ancillary components needed to support that pump, everything from port fittings to fuel filters, fuel lines and hose ends, pressure regulators, and fuel rails or fuel logs. From that we generate the appropriate system diagrams for each pump, showing the correct fuel line sizes, supporting components, and plumbing diagrams, depending on the application. This is a tremendous resource available to anyone on our website, aeromotiveinc.com.
Now, there is a risk of building a fuel system that’s too big for an application, so some caution is advised. For example, someone making 1,500 hp on methanol today requires a little more than 7 GPM into the engine. Say sometime in the future the plan is for a new engine combination making 3,000 hp, which would take double that, or 14 GPM. Can you put a 20-gallon-per-minute pump on it now, knowing it will be a year or two before going to a bigger engine? Unfortunately, the answer is no, because it will just run the regulator over trying to bypass the extra 13 GPM the engine isn’t able to use today at the lower power level. As a rule, we try to limit the bypass fuel to 7–8 GPM max to install the biggest possible pump for the future but avoid false high fuel pressure under load down-track today.
Excess fuel bypass is also a problem for those who are spending time on the street with a big engine that needs a lot of fuel at WOT, which can easily overheat the fuel in the tank when the engine is at low load on a longer drive. You really have to deal with just how much extra fuel will be recycled and how hot the fuel is going to get in the tank over time.
Here’s an example: If there’s a 15-gallon tank in a car with a 5.0-GPM pump at full speed, every three minutes all the fuel in the tank goes through the chassis and the engine bay if the tank is full. If the tank is down to half full, every minute-and-a-half all that fuel goes through the chassis and the engine bay. The less fuel in the tank, the higher the frequency of recycle, and the faster the fuel in the tank gains temperature.
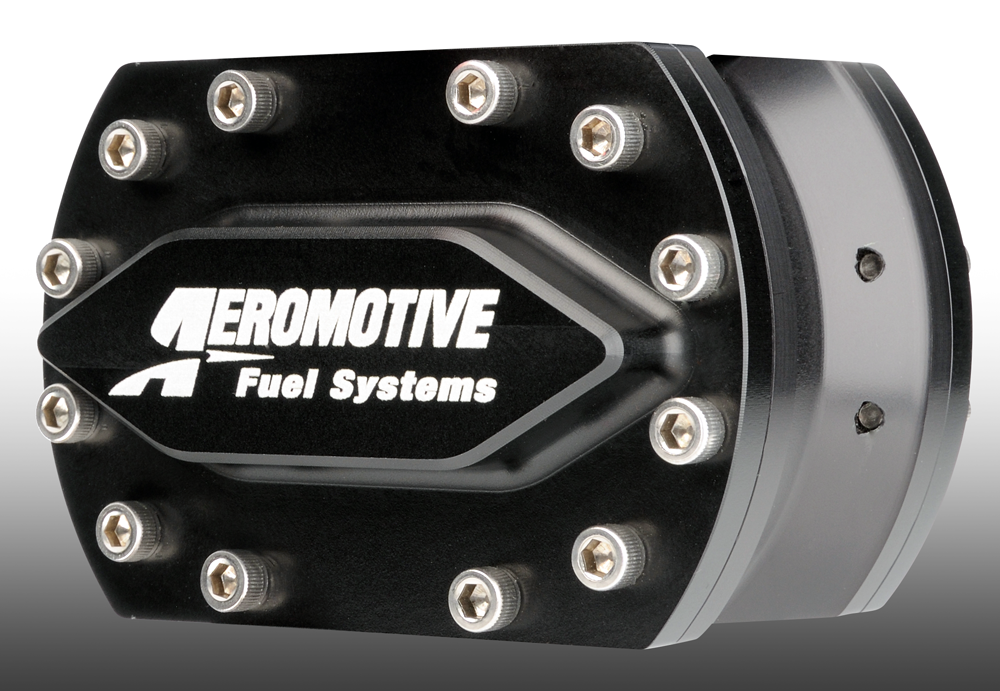
Depending on altitude and time of year, the maximum fuel temperature in the tank varies before cavitation and vapor-lock can start. This generally falls between 130 and 145 degrees F. When you cross that threshold, you can easily see hot fuel handling problems occur, including poor drivability and vapor-lock.
The key to avoiding such problems when using large, high-flow pumps is to vary pump speed with engine demand in order to minimize excessive recycling. Aeromotive offers a fuel pump speed controller suitable for use with all of our standard, brush-style fuel pumps, and we offer all of our brushless fuel pumps with an optional TVS, or True Variable Speed controller. This gives the user the flexibility to run a bigger pump for higher horsepower combinations and avoid creating a hot fuel problem.
Our standard pump speed controller uses engine RPM as a reference, whereas our brushless TVS controllers use an analog voltage reference between 0- and 5-volt DC. Typically, a reference off the TPS (throttle-position sensor) is a simple, intuitive way to control pump speed. The input range is technically from .5 to 3.8 volts, so as you move the throttle, the pump speeds up or slows down automatically. Full speed is typically achieved by roughly three-quarter throttle opening.
Some engine builders and tuners prefer to control the pump on a load-based strategy. Here we can take a 2- or 3-bar MAP sensor and dedicate that to the fuel pump, and then the pump speed is controlled by manifold pressure.
Another big benefit of using an Aeromotive brushless fuel pump with TVS control is less amperage draw on the electrical system at lower pump speed. As an example, a 10-GPM pump at full speed and 60 psi is drawing 48 to 50 amps. Using a TVS controller, at full slow the current draw drops to 13 amps, while the regulator adapts to the reduced flow, and fuel pressure is unaffected, remaining at 60 psi.
If you’re in the pits warming the engine up, or you’re driving it in the pits to warm up the driveline, you don’t need that pump running at 10 gallons a minute and drawing 50 amps. You’re just draining the battery or heating the tank up.
Using our True Variable Speed brushless pumps provides all the flow needed at WOT while being able to reduce the recycle rate and reduce the current draw at idle and low load.
A lifelong hot rodder, Brett Clow has been the Director of Technology at Aeromotive for more than 20 years. He’s been tuning fuel injection systems for more than 27 years, and he heads up all of Aeromotive’s technical training programs and workshops.