PRI Education: Honing Techniques For Lasting Performance
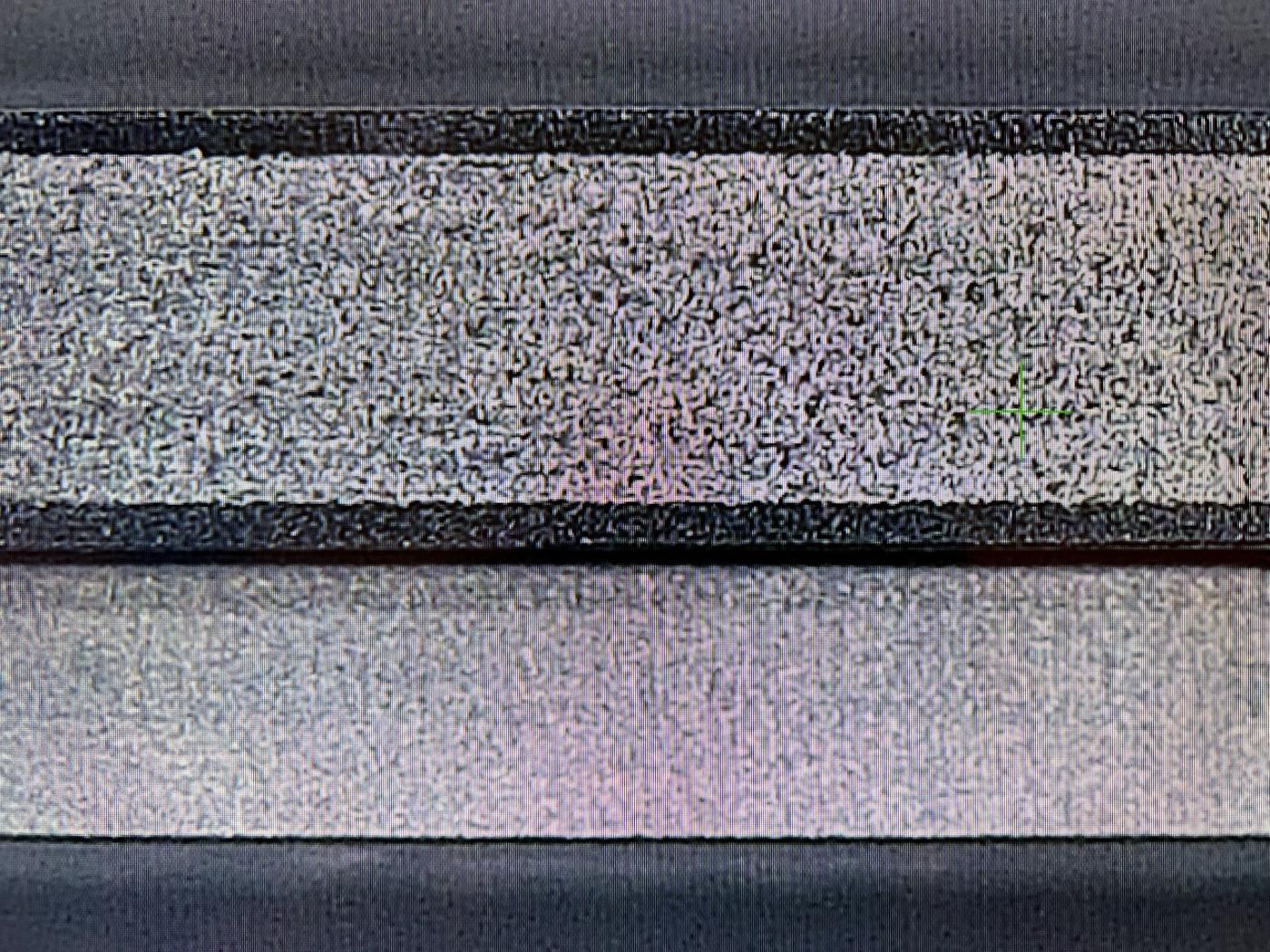
Under magnification, you can see the pores in the moly faced rings pictured at top. The lower image is a steel, PVD-coated ring, which shows no porosity.
The key to mastering piston ring seal begins with the understanding that the rings, cylinder bore, piston, and motor oil all work together.
The piston ring was invented 170 years ago. Yep, that’s right. Piston rings were invented decades before the internal combustion engine. Originally designed for steam engines, piston rings have come a long way in design, materials, and coatings since 1852.
Along with the evolution of piston rings, cylinder honing has also progressed. In fact, piston ring performance (and durability for that matter) directly relates to cylinder bore surface finish, which is created by the honing techniques.
In the last 10 years alone, the understanding of the piston ring seal has greatly advanced. What was once considered a “black art” can now be easily measured and modified scientifically.
The key to mastering ring seal begins with the understanding that the piston rings, cylinder bore, piston, and the motor oil all work together to create a seal.
Just as the head gasket seals the block to the cylinder heads, the motor oil functions as the “gasket” between the piston rings and cylinder wall. This is where cylinder bore surface finish plays the critical role in ring seal.
The cylinder bore needs to hold enough oil to both function as the gasket and lubricate the rings. If the bore is too smooth, it can’t hold enough oil to properly seal and lubricate the rings, which will result in higher blow-by and reduced engine life.
In years past, the use of ductile iron rings with a plasma moly coating called for a smoother cylinder bore finish than the previous chrome-faced cast iron rings. The “old school” chrome rings needed a rougher cylinder finish (created by a coarse grit honing abrasive) to break-in. This was due to the fact that chrome was much harder than moly (upwards of 50% harder). Conversely, the softer moly-faced rings need a smoother surface to prevent excessive wear.
Today’s Steel Rings
Now enter today’s steel piston rings. The advent of steel piston rings has revolutionized engine efficiency and durability. Since more than 40% of all friction within an engine comes from the piston/ring contact with the cylinder wall, reducing piston ring thickness reduces friction, which increases horsepower and extends engine life. That’s right, thinner piston rings actually live longer than thicker piston rings. Let me explain how.
When using iron to make piston rings, the rings need to be thicker in order for the rings to have the proper strength. If they are too thin, the brittle nature of iron allows the rings to break.
However, steel provides the advantage of ductility. The greater yield strength of steel enables the creation of thinner and stronger rings.
For example, NASCAR engines used .043, .043, 3.0-mm ductile moly ring sets 20 years ago. These rings lasted about 500 miles (one race). These engines would be down 5–8 horsepower after just one race, so the engines would have to be rebuilt.
Today, NASCAR engines use .5-mm, .6-mm, 2.0-mm PVD coated steel rings, which last more than 1,500 race miles (up to three races, without any loss of power).
What does that have to do with cylinder bore surface finish? Well, the improved durability comes in part from the increased material strength of steel as well as the hardness of the PVD face coating on the rings (the same coatings used to extend drill bit and cutting tool life). But the other part of the increased performance and longevity comes from the plateau honing process, which is critical for modern steel rings.
The ductile moly rings naturally have porosity on the face of the ring, so those pores hold oil, which reduces the amount of oil needed to be held on the cylinder wall.
As such, the ductile moly rings allow for a smoother surface finish to function well. Depending on the type of fuel being used, ductile moly rings work well with a 320- or 280-grit abrasive followed by a few strokes with a 400-grit brush.
In contrast, the PVD-coated steel rings have no natural porosity, so the cylinder bore finish must hold all the oil needed to lubricate and seal. Accordingly, a more aggressive plateau honing process must be employed to create the deep “valleys” to hold oil.
Mesas and Mountain Ranges
When thinking about surface finish, it helps to think in terms of things like a mesa and a mountain range. These oil-holding “valleys” can be measured with a profilometer, which is a surface finish measuring tool. When using the profilometer, there are three key measurements: Rpk, Rk, and Rvk.
Rpk is the peak height: Think about the peaks of a mountain range. The piston rings interact with these peaks, so we don’t want rough peaks.
Rk is the core roughness: Again, you’d rather have rolling hills than jagged mountains.
Rvk is the valley depth: The deeper the valley, the more oil the cylinder will hold.
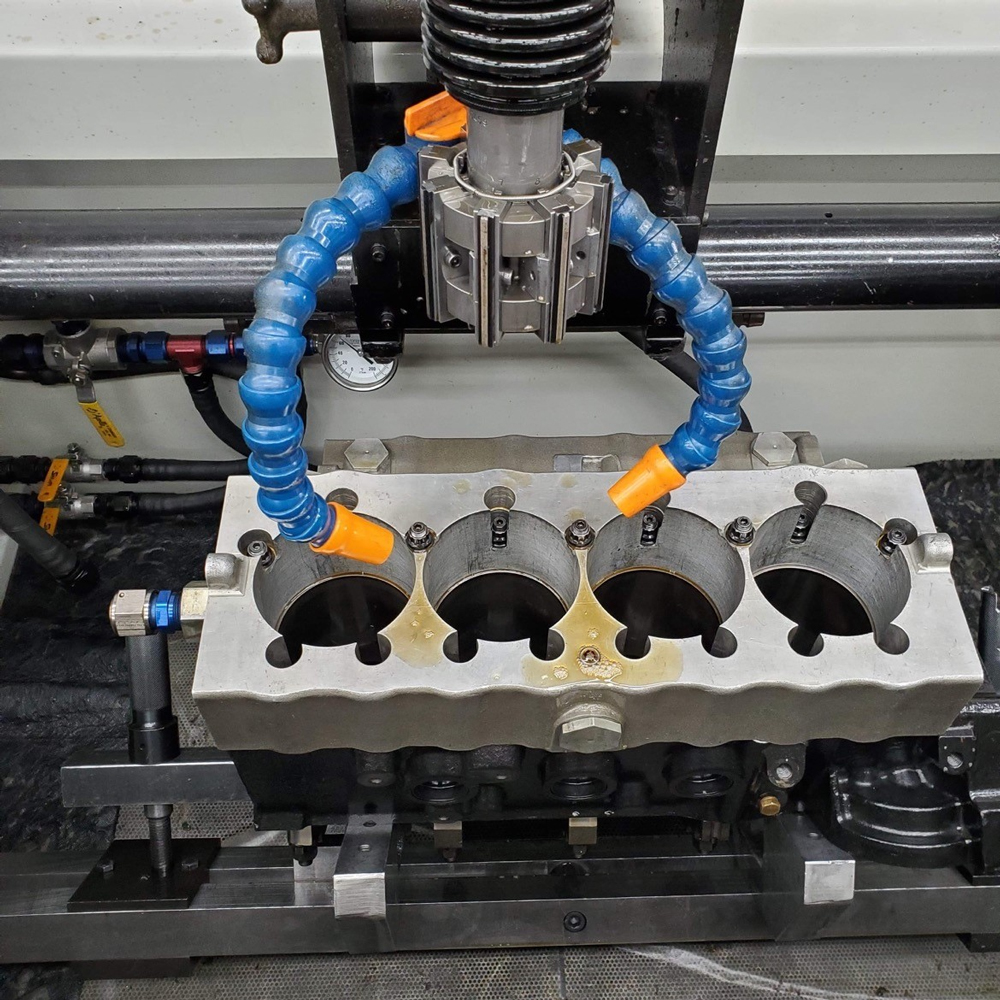
To provide some perspective, the profilometer is measuring and reporting these values in micro inches. That’s a millionth of an inch, so 100 micro inches equals .0001. A good plateau finish is about 100 micro inches from the highest peak to the lowest valley. Let that sink in for a minute.
This means the entire surface texture that can make or break your engine is .0002 when measured with a dial bore gauge (.0001 per side). This is why the modern plateau honing process requires going to finished bore size with the roughing abrasive (170–200-grit diamond) and then “plateauing” with a 600-grit CBN abrasive for 10 to 12 strokes.
That process should yield the following values:
Rpk 10–15 micro inches
Rk 40–45 micro inches
Rvk 50–55 micro inches
These surface finish measurements will work for both steel and ductile moly rings.
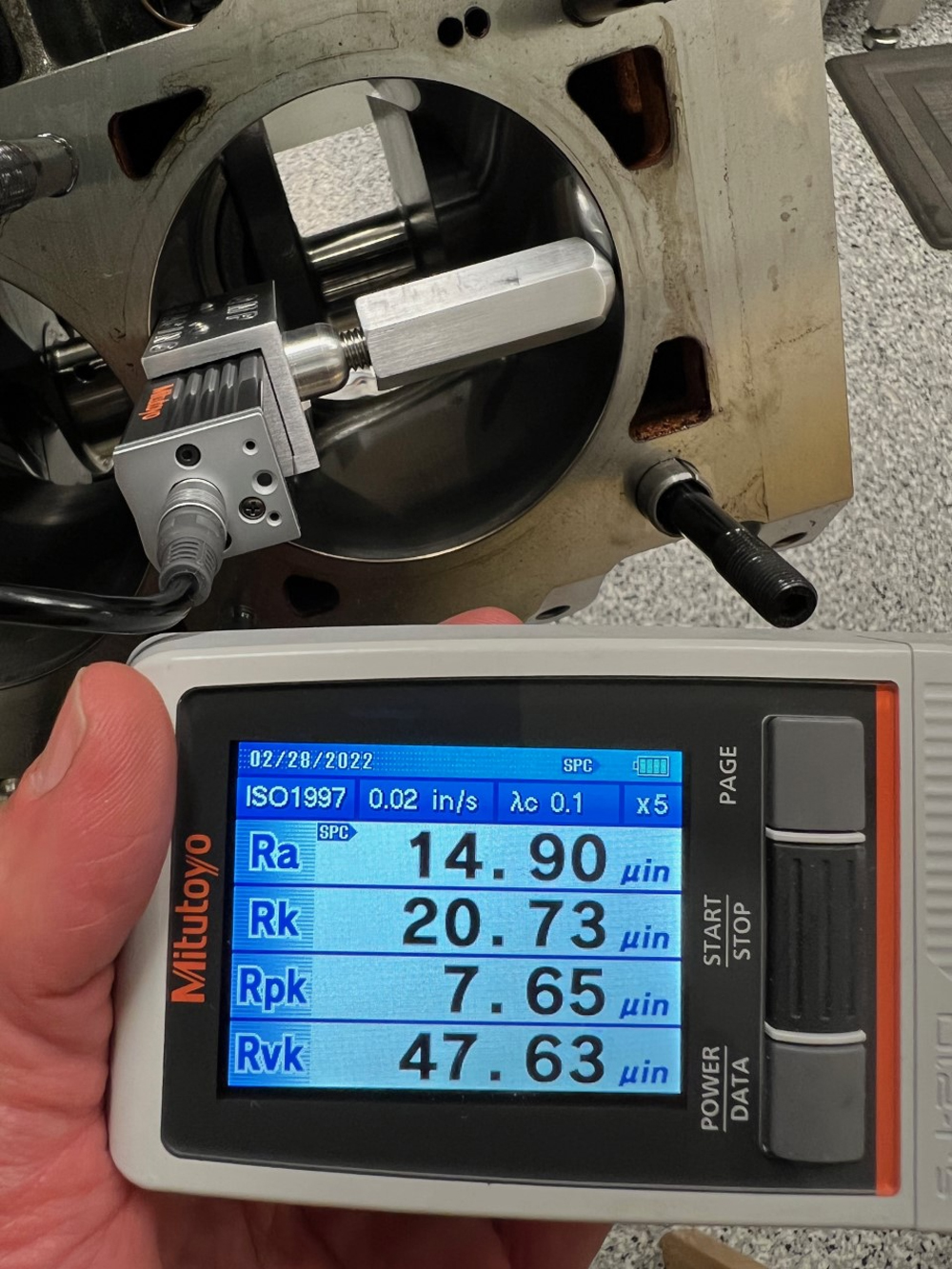
When using steel rings with methanol or E85, increase the Rvk to 60–70 micro inches. That extra valley depth will hold additional oil to offset the higher volume of fuel that goes into the cylinder because of the richer air-to-fuel ratios of these fuels compared to gasoline. Essentially, the more fuel that goes in the cylinder, the deeper the Rvk needs to be. This rule applies to boosted engines as well—the more boost you run, the more fuel will be going into the cylinder, so the Rvk needs to increase to retain more oil, which is the key to increasing ring seal and extending cylinder bore/piston ring life.
Without enough oil to properly lubricate and seal the rings and cylinder bores, the performance and durability of the engine will be compromised.
Fortunately, we don’t have to guess or rely on “tricks” to get the right surface finish. Today, we have the profilometer and proven surface finish values that allow us to achieve precise surface finishes with the same level of precision as we do with other parts of our engines.
Lake Speed Jr. is the son of Lake Speed Sr., who raced professionally in NASCAR and International Karting Foundation before retiring in the late 1990s. After graduating from the University of Tennessee, Speed Jr. moved to Charlotte, North Carolina, to work for Melling Racing, which fielded Bill Elliott’s No. 9 NASCAR from 1982 to 1991. There, Speed Jr. helped develop an engineering department to test programs and improve performance. After joining Joe Gibbs Racing in 2004, Speed Jr. studied lubrication fundamentals and chemistry as part of a development relationship with Lubrizol. He later joined Driven Racing Oil as the director of research and development. In 2019, Speed Jr. joined Total Seal to advance the tribology of piston rings.