Tech Update: Troubleshooting Diesel
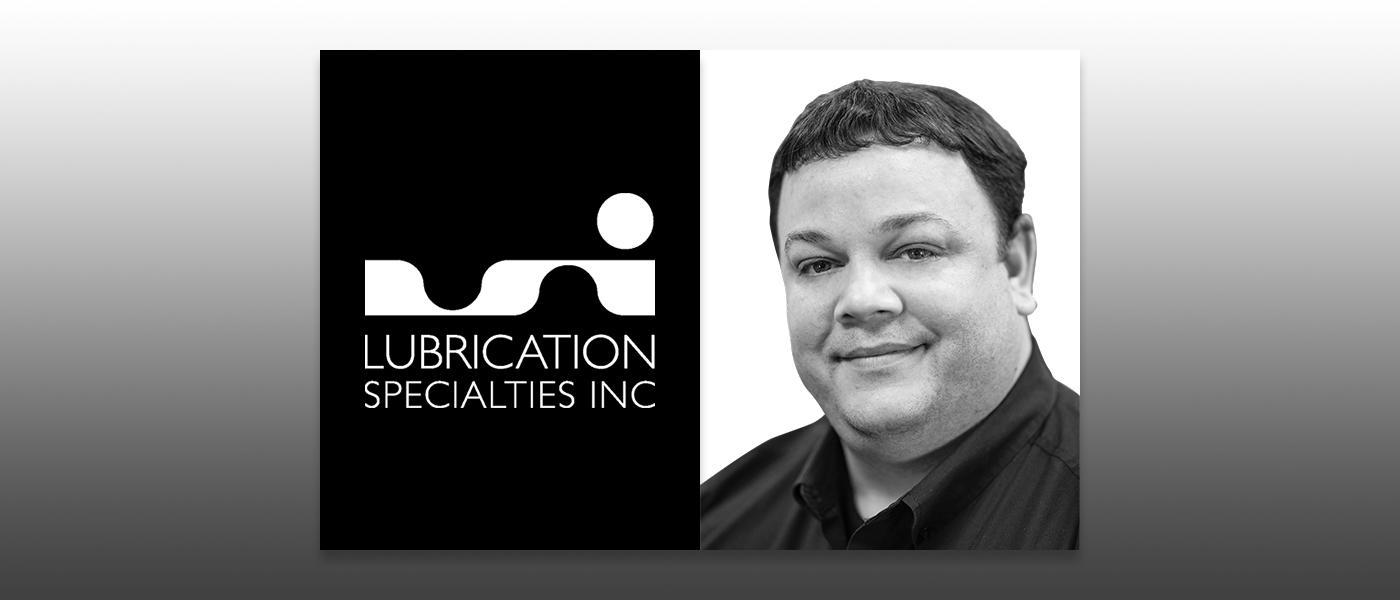
How to identify and address the top three problems associated with diesel fuel regardless of the application.
Whether we are talking about a 400-horsepower street truck or a 3,000-horsepower race truck, they each deal with similar problems associated with diesel fuel. And that holds true no matter what kind of diesel fuel they run, whether it is standard Ultra-Low Sulfur Diesel (ULSD), biodiesel, premium diesel, off-road diesel, or diesel race fuel. Sure, these diesel fuels do differ in some regard—cetane rating, sulfur content, color, etc.—but the challenges they all present are relatively uniform.
In racing, the top three problems associated with diesel, regardless of the kind of diesel used, are lubricity, deposit control, and combustion efficiency. Let’s take a closer look at all three.
Lubricity
To better understand diesel fuel lubricity and its impact, we should first consider how it is measured. There are many standardized test methods to determine diesel fuel lubricity, but the most common is the ASTM D6079 HFRR (High Frequency Reciprocating Rig) test method. The test consists of submerging a contact point between a steel ball and a flat steel disc into a sample amount of fuel. Under a controlled environment, the temperature is set to approximately 140 degrees F and the ball is placed under a light load, then it moves back and forth at a set frequency for 75 minutes. After 75 minutes, the wear scar is measured both parallel and perpendicular to the sliding direction, and the average wear scar is recorded. The results are measured in μm (microns). The larger the number, the more wear that has occurred. For reference, the ASTM D975 (Standard for US Ultra-Low Sulfur Diesel, or ULSD) specification calls for a wear scar no greater than 520μm, while the Truck and Engine Manufacturers Association (EMA) recommends a stricter 460μm wear scar maximum.
If you use a diesel tow rig, you should take note that today’s ULSD does not contain the lubricity needed to fully protect our vehicles. Consider: The Bosch CP4 fuel pump has an unusually high failure rate in the US, upwards of 7%, when compared to a 1% failure rate in Europe. The European EN-590 Diesel has a 490μm wear scar specification, while in the US the base is 520-micron in ASTM US D-975. Therefore, the failure is caused by the lack of lubricity in ultra-low sulfur fuel in the US.
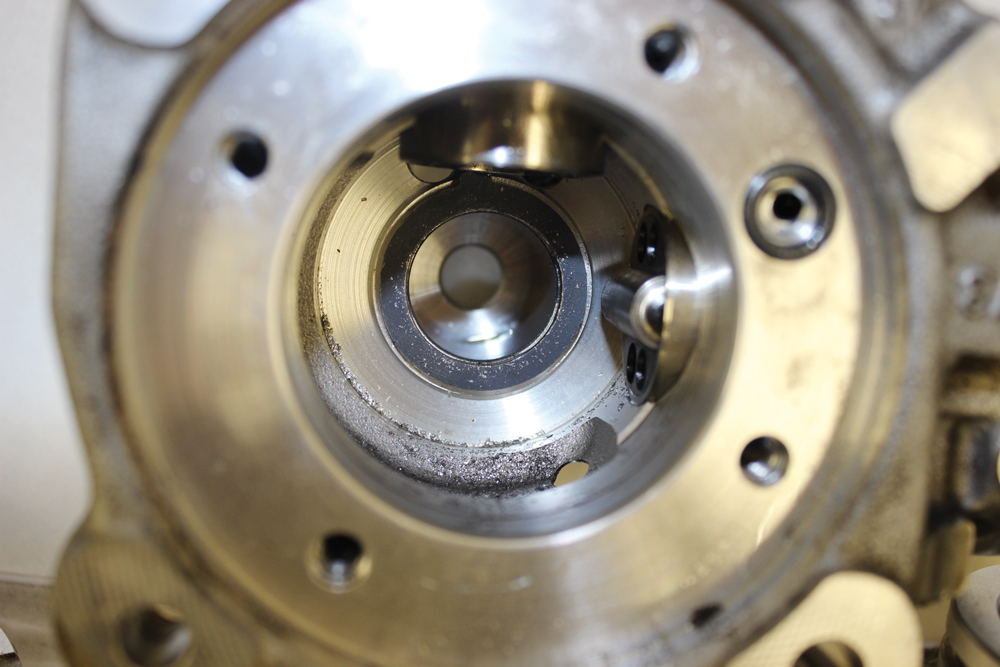
Lubricity is so critical because of its role in controlling fuel-pump and injector wear. This is even more the case when talking about high-horsepower, high-torque diesel applications with aftermarket performance upgrades.
At Hot Shot’s Secret, we recently tested an industry-leading diesel race fuel in the HFRR test method, and it came back well below the recommended level of lubricity, recording a wear scar of 590.5μm. Drivers beware, because this lack of lubricity can lead to very expensive mechanical failures. Fortunately, we were able to treat this diesel race fuel with an additive and lower the wear scar to 461.5μm—a much safer level of lubricity. We recommend doing a fuel analysis that measures lubricity if you consistently use the same diesel race fuel and ensure you are getting enough protection for your hard parts.
Deposit Control
Another common problem with diesel fuels is their ability to control injector deposits. Coking deposits forming on injector tips have been an issue for years. These deposits form both in, on, and around the injector nozzle holes, which can cause spray pattern issues. A relatively new problem with high-pressure common rail fuel injectors is the formation of internal diesel injector deposits (IDIDs). Unlike traditional coking deposits, these deposits form on the internal components of the injectors.
Diesel fuel contains something called carboxylic salts (waxy, sticky deposits). These deposits used to be soluble in older, high-sulfur diesel fuel, but are not in today’s ultra-low sulfur diesel. The salts make their way past the fuel filter and into the fuel injectors, depositing on the internal surfaces. Today’s high-pressure common rail injectors have a very tight tolerance of 1–3 microns, so even the slightest deposit formation can cause serious problems, including sticking injectors, power loss, and fuel flow issues.
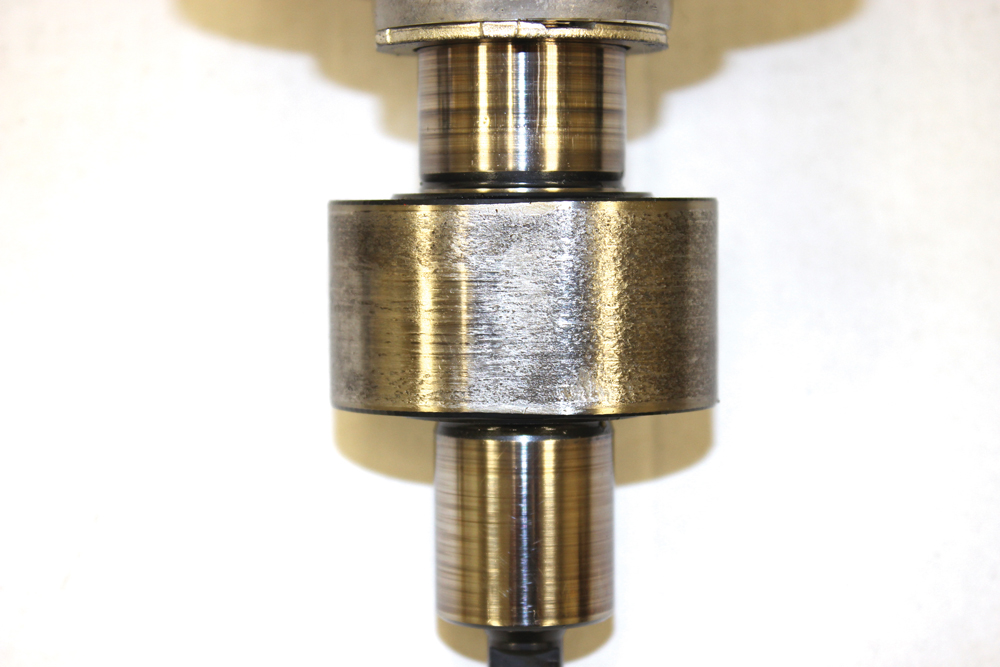
Unfortunately, not all additives and detergents are able to remove IDIDs; they are much tougher to eliminate than traditional coking deposits. To remove IDIDs and prevent them from inhibiting performance, you must use an injector cleaner that is specifically formulated to combat IDIDs.
Combustion Efficiency
Combustion efficiency issues may not be as prevalent with diesel race fuel, but they can still be problematic at times. Cetane is a liquid hydrocarbon that, when available in higher volume in diesel fuel, improves the ignition of the fuel, resulting in improved performance and fuel economy, and decreased emissions.
Diesel fuel cetane rating can vary greatly from station to station, and from state to state. A 40 cetane is the minimum rating for diesel fuel sold in the US, but some states have stricter requirements. California, for example, has its own cetane minimum of 53. This is because, generally, a higher cetane rating means the fuel will burn cleaner and produce less emissions. This is good news for the environment, but it also produces greater horsepower and torque numbers. Diesel motorsports applications generally seek greater cetane numbers for that reason—more power.
While most over-the-road diesel engines run best on fuel with a cetane rating of 47+, it is not always available. Running fuel with a poor cetane rating often results in rough operation, knocking, less power, and lower fuel economy. The challenging part is that you often do not know the cetane rating of the fuel you’re running. This is where additives come in. Whether you want better fuel combustion for on-road or off-road diesel applications, a cetane improver may be the answer. The industry standard to improve diesel fuel cetane is 2-ethyl hexyl nitrate. Keep this in mind as you do your research—be smart about what you add to your diesel engines and rely on a supplier’s track record and reputation to give you the facts.
Kyle Fischer is the director of branding and promotions for Lubrication Specialties Inc., manufacturer of Hot Shot’s Secret. Fischer is a self-professed “gear head” with a passion for anything car-related. When he is not managing Hot Shot’s Secret’s busy event schedule, race sponsorships, and trade show marketing, you can find him testing new products on the dyno or track, or attending drag racing and car club events for fun.