PRI Tech: Fastener Strength and Optimized Performance
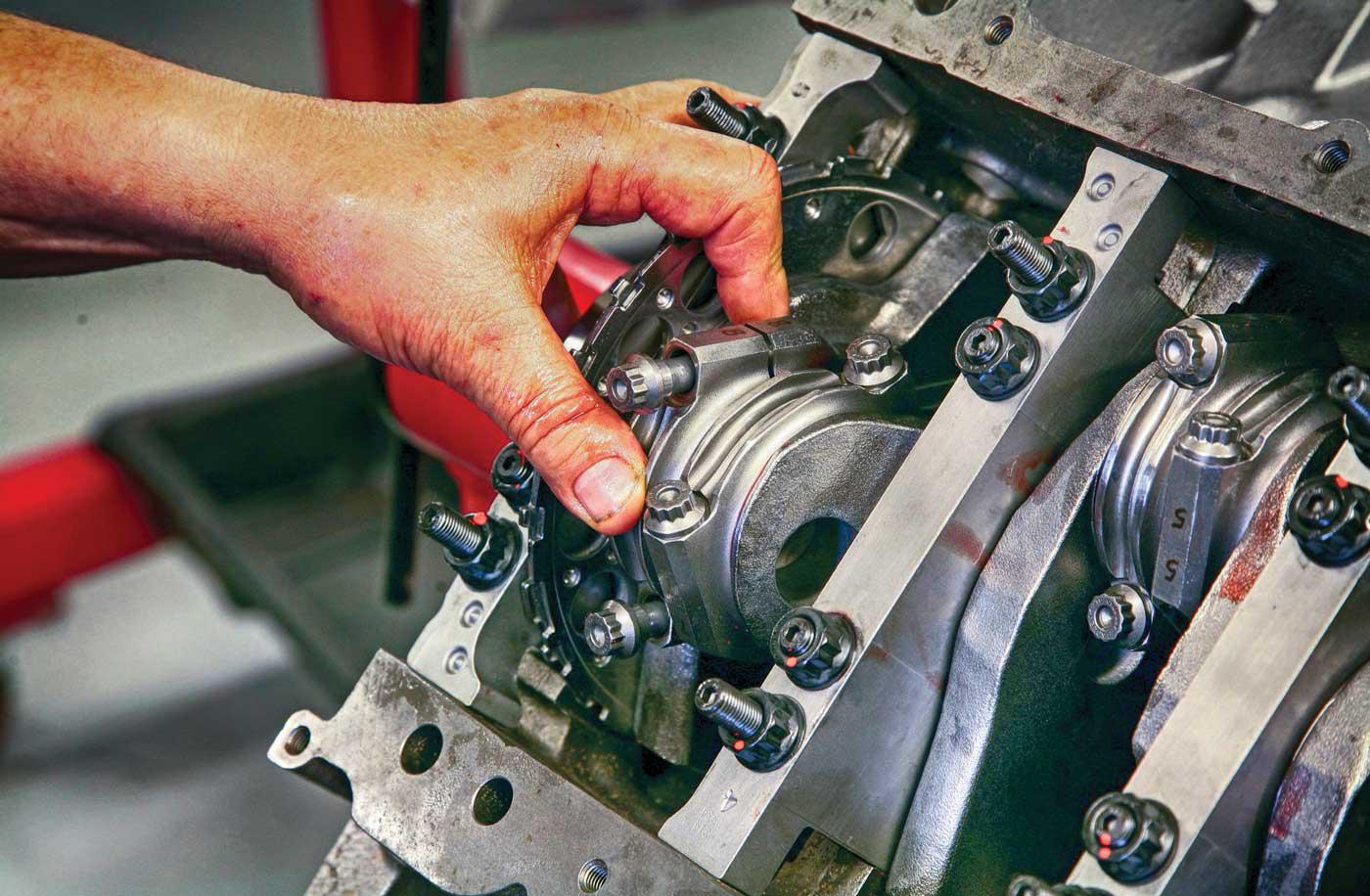
Understanding the properties of these critical components, as well as factors like preload levels and the effect of friction, are essential to the proper assembly of major systems on a high-performance vehicle.
They say you can’t tell a book by its cover, but you can certainly get a good idea of a fastener’s strength by the marking on the head of a bolt.
This is an often understated and important consideration, as many racing associations specify fastener strength minimums for select applications in their rulesets. Plus, most car builders place a premium on reliability “insurance” through the use of stronger fasteners.
It’s also part of a larger matrix: Understanding how fasteners are rated, how different manufacturing processes impact strength, how to avoid failures through proper installation, and factors like preload levels and the effect of friction are all essential to the proper assembly of major systems on a performance vehicle.
Identifying Bolt Head Markings
There are two entities that have established the strength standards we use today: SAE International (formerly known as the Society of Automotive Engineers, founded in 1905 by Henry Ford and others) and the ISO (International Organization for Standardization) located in Geneva, Switzerland.
The most common standards employed in high-performance automotive applications are SAE Grade 5 and Grade 8, plus ISO 8.8 and 10.9—generally employed for metric fasteners. An SAE Grade 5 bolt will have three raised “hash marks” on a hex head. It’s made from a medium carbon steel, and the minimum tensile strength is 120,000 psi. The Grade 8 bolt is made of a medium carbon alloy and rated at 150,000 psi tensile strength; it is identified by six hash marks on a hex head.
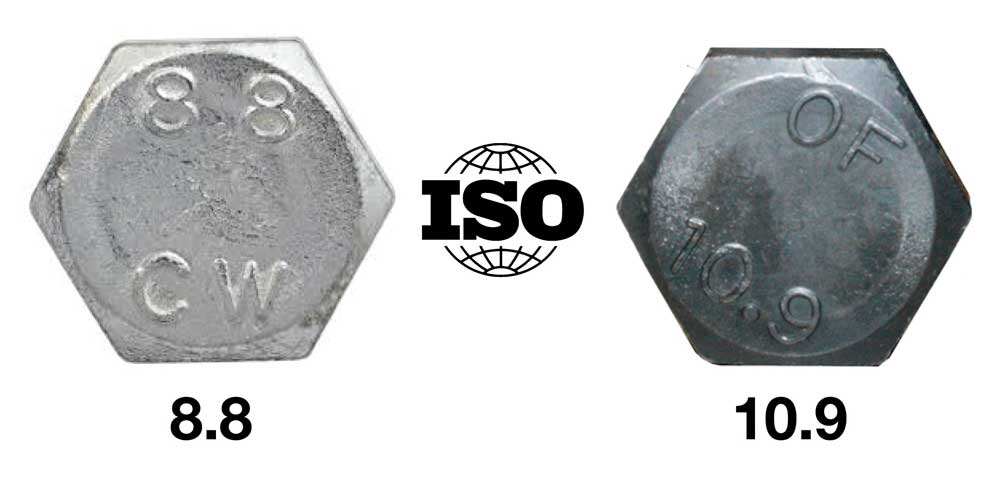
ISO class 8.8 fasteners are equal in strength to SAE Grade 5 at 120,000 psi, and class 10.9 replicate SAE Grade 8 at 150,000 psi. They will have “8.8” or “10.9” in raised digits on the bolt head.
Some suppliers may choose to exceed those standards, however. For example, ARP’s polished stainless steel and black oxide finished 8740 chromoly bolts (and studs) are nominally rated at 180,000 psi—some 20% stronger than Grade 8 or ISO 10.9 fasteners.
Tensile vs. Yield Strength
Tensile strength is the most commonly used yardstick associated with fastener mechanical property. It represents the maximum tension load that can be applied to the fastener prior to its fracture.
In addition to tensile strength there is a yield strength published for all rated fasteners. This is a measure of how much load a fastener can take before it starts to deform (typically around 0.2%). It is also the threshold at which a fastener starts to fail. For example, the yield strength of SAE Grade 5/ISO 8.8 is 90,000 psi; for Grade 8/10.9 it’s 120,000 psi.
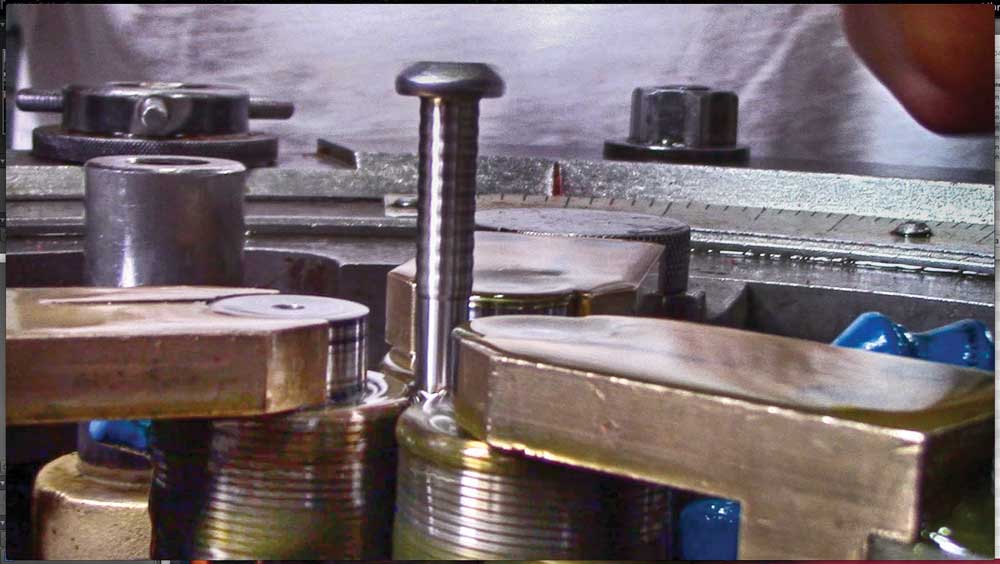
This is an important factor because almost all modern engines are primarily assembled using TTY (torque to yield) fasteners—often installed robotically. While this process is certainly adequate for OEM applications, placing additional stress on these fasteners through engine modifications can lead to serious consequences. Moreover, since the fastener has been yielded by design, it should never be re-used.
Manufacturing’s Impact on Strength
There are also several elements of fastener manufacturing that, while invisible to the naked eye, absolutely do impact a fastener’s durability and service life. This includes the quality of heat-treating process and how the threads are formed as a result.
Generally speaking, there are two primary heat-treatment methods: case hardening and through-hardening. Case hardening is a relatively inexpensive process that affects the surface layer of the component while leaving the core softer than it was before treatment. Through-hardening, by contrast, increases the hardness of the entire component with uniform properties throughout. It is a far more expensive and time-consuming method that requires specialized equipment and multiple steps.
The threads on inexpensive fasteners are cut or rolled on a bolt-making machine prior to heat-treating, when the material is softer and easier to work with. As you might imagine, the threads on better-made fasteners are constructed differently. For example, ARP rolls the threads (versus cutting) after the material has been heat-treated. This results in a fastener fatigue life some 10 times better than you’d get using other procedures.
Critical Bolts and Avoiding Failures
Connecting rod bolts are by far the most critical fastener employed in an engine. A failure here can lead to massive carnage—often damaging the crankshaft, pistons, block, and more. It’s here where more exotic materials are employed to withstand the increased loads brought on by power-adders and racing fuels.
On cap screws manufactured by ARP for aftermarket connecting rods, the actual alloy is stamped on the head (in addition to the company ID). These alloys include:
• 8740 (190,000 psi)
• ARP2000 (220,000 psi)
• L19 (260,000 psi)
• CA 625 (Custom Age 625+ at 280,000 psi)
• ARP 3.5 (280,000 psi)
Upgraded head studs (or bolts) are also a significant factor in engine performance and reliability. When combustion pressures increase, it is necessary to compensate with stronger fasteners and corresponding clamping force.
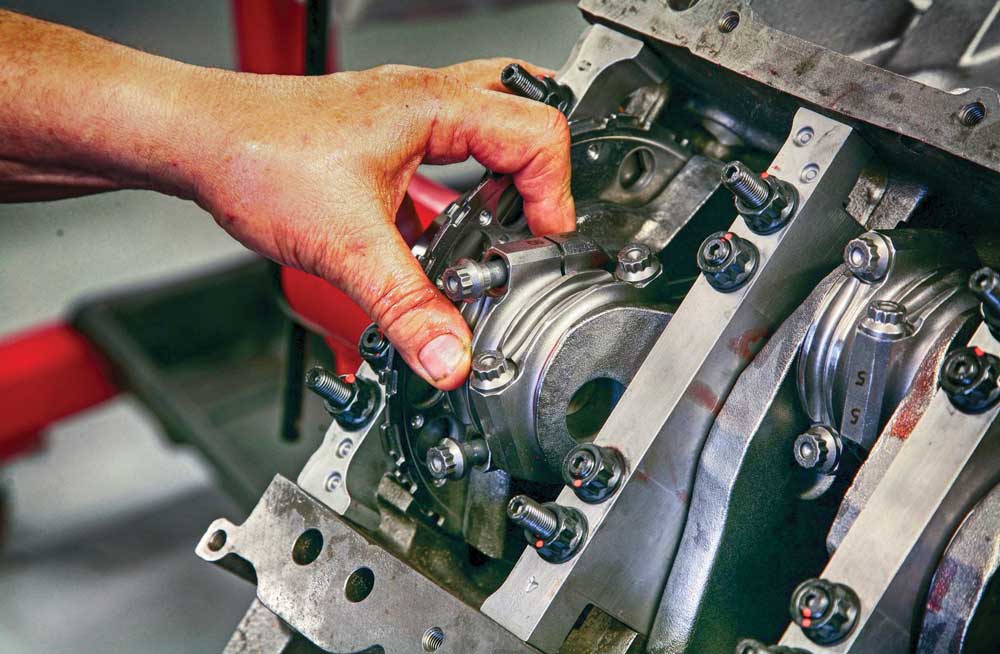
Standard 8740 chromoly studs and bolts are sufficient to handle most normally aspirated engines, while stronger fasteners should be employed for supercharged, turbocharged, and nitrous oxide-boosted engines. ARP, for example, uses an alloy strength range similar to the range for its rod bolts. Likewise, increases in combustion pressure (and engine power output) exert more force on the crankshaft and require upgrading main cap fasteners.
Proper Installation Procedures
No matter how good a fastener is, it can’t do its job unless it is properly installed. A fastener acts much like a spring, as it must be stretched to achieve a rebounding force. For example, a typical 3/8-inch rod bolt will stretch between 0.060–0.065 inches to achieve a 10,000-psi clamping load. When installing rod bolts, it’s highly recommended to employ a rod bolt stretch gauge. This will ensure the fastener is accurately preloaded.
The most common causes of rod bolt failures are either too much or insufficient preload. Too much torque on a bolt will stretch it to the point of yield; conversely, not enough clamping force will ultimately lead to rod cap movement in each cycle and imminent failure.

Most fasteners, though, are installed in “blind” holes. So it’s imperative to properly apply the required torque loads. ARP maintains a database of instruction sheets on its website (arp-bolts.com), so finding the proper specs is easily accessible.
Since torque wrenches are delicate instruments, it’s wise to have them tested periodically for accuracy. There are calibration services available nationwide, including by ARP—for free—at NHRA national events.
Preload Levels and the ‘Friction Factor’ Effect
It’s important to note that when a torque wrench goes “click” at its preset value, that does not mean all of the required torque is used to stretch the fastener. A large portion of the energy is usurped by friction, both in the thread and the underside of the bolt (or nut) and the lubricant. This led ARP To develop a lubricant that is superior to oil, moly, EPL, etc., and delivers 95–100% of the desired preload on the first (and all subsequent) pull of the torque wrench.
Note, too, that most OEM automotive engines are built—often with robotic equipment—using the “torque angle” method. This method calculates the specific amount of fastener rotation required, which then is used to determine the ultimate clamp load required. For hand assembly, a minimal torque reading—say 10 ft.-lbs.— is the starting point, and the fastener is then rotated “X” degrees to its final preload.
In conclusion, it’s a good rule of thumb to be wary of any fastener that does not have a marking on it, or that has markings you are unfamiliar with. Using properly rated fasteners, and understanding how to optimize their capabilities, is critical when assembling the engine, driveline, chassis, and suspension of any race car or high-performance vehicle.
Bill Holland has been involved with ARP’s marketing for 25-plus years. His competition background includes drag racing, off-road, and oval track. He currently races vintage sports cars. Holland has authored technical articles for numerous enthusiast magazines and websites. He also has built an AMBR Contender street rod.