PRI Education: Race Sensor Choice and Care
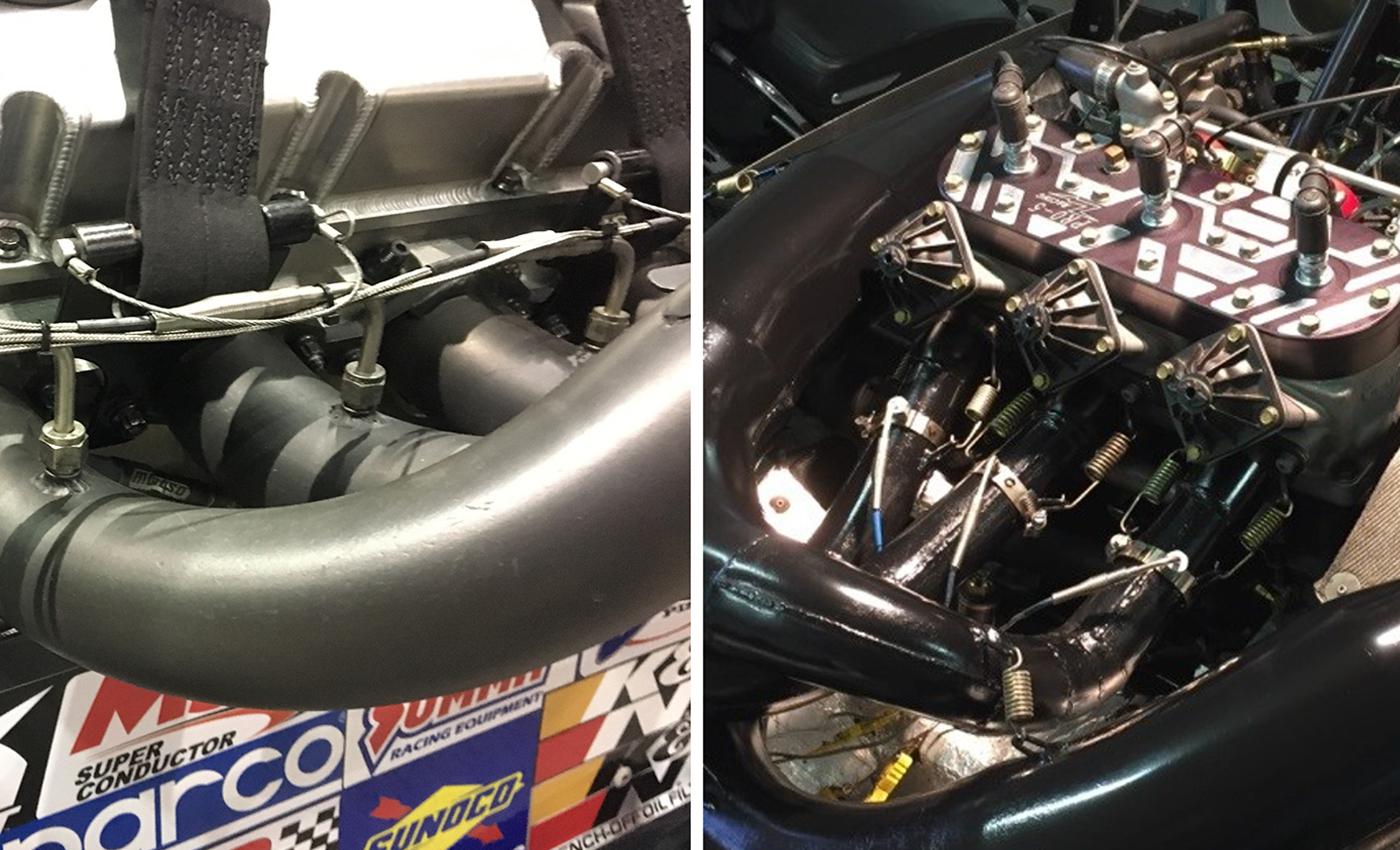
Proper sensor installation is critical to produce accurate readings. The sensors shown at far left are incorrectly installed with the exhaust flow, which results in hotter temperature readings than what is actually occurring. By contrast, the sensors at left are installed correctly. Note the sensor wire leads exiting the front or rear of the engine. This positions the sensor’s tip so it streamlines the exhaust flow (sensors should only be installed 1/4-inch into the exhaust stream).
A data system is only as good as the sensor connected to it, so choose wisely.
Choosing the proper sensor for a data system is as critical as selecting the proper camshaft for an engine. There are several considerations, beginning with the type of engine: two-stroke or four-stroke? Is a power adder, such as nitrous oxide, supercharger, or turbocharger used? Which fuel is being used, and at what rate is it being consumed? In this article, we will touch on all aspects for the race application and ensure that the crew chief or dyno shop can depend on smooth, accurate, and reliable information, because the data system is only as good as the sensor connected to it.
Sensor Sizing
In the thermocouple world, the larger the diameter of the sensor, the longer it lives. The lifespan of a 1/4-inch sensor is about four times the life of a 1/8-inch sensor. So in the harshest environments, the larger sensor is recommended for the longest lifespan. But first note that there are three sizes common in most motorsports: the 1/8-inch sensors, recommended for naturally aspirated engines that need extremely fast data like dynamometers or testing facilities; the 3/16-inch diameter sensors used in most powersports applications, such as snowmobiles, ATVs, and automobiles with lesser amounts of nitrous oxide; and the 1/4-inch sensors, which are suggested in anything that is supercharged or turbocharged, and for rotary engines since these are the harshest of environments.
Closed or Exposed Tip
Closed-tip, ungrounded sensors can be used in street vehicles and diesel engines. Racers can also run open tips in these applications, but it is advised to only use them for short timeframes, as the sensor life will be greatly reduced in engines that use diesel or oils with sulfur, which can attack the exposed sensor tip and cause the wire to become brittle.
Grounded, Ungrounded, or Exposed Tip?
Never use a grounded sensor in motorsports applications, as the sensor could pick up ignition noise and feed it to the data system. If you need an enclosed-tip sensor, make sure it’s ungrounded, meaning the sensor wires internally do not touch the outer sheath. Exposed tips can work with all fuels and have an extremely fast reaction to temperature change found in a majority of motorsports applications.
Sensor Placement
Recommended sensor placement on a four-stroke engine is four inches from the center of the exhaust valve, or two inches off the side of the head. For two-stroke engines, it’s recommended to place the sensor 100 mm from the piston skirt, or what’s recommended by the pipe manufacturer. Sensor inertion depth is standard at 1/4 inch to 3/8 inch into the exhaust stream.
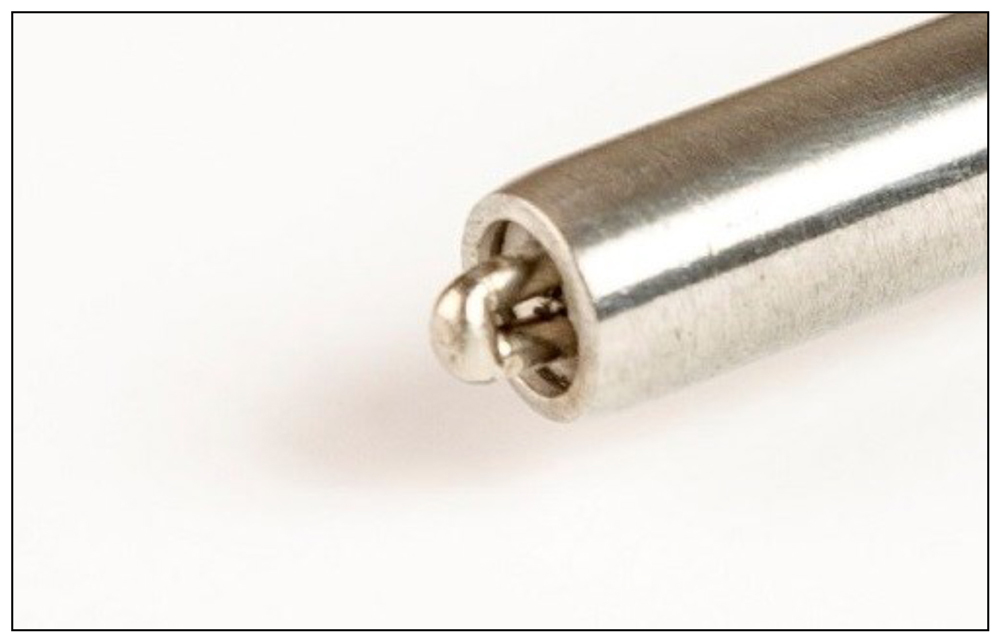
Sensor Orientation
On exposed-junction sensors, it is critical that the sensor points in the correct direction to streamline the sensor tip. Check the end of the sensors to make sure the exhaust is not flowing through the center of the sensor tip, as this will show a hotter temperature than what is really occurring.
Sensor Care
Enclosed sensors are able to avoid moisture, but exposed-tip sensors will tend to wick moisture over time. If this occurs, the moisture will start to measure the temperature that is inside the sensor sheath instead of at the sensor’s tip, called a secondary junction. While rare, this issue can be found in engines that use water injection, have excessive raw fuel down the pipe, or even get condensation from sitting in storage.
If you are unsure if there is moisture in a sensor, check the data. If that cylinder is colder by a few hundred degrees, or if there is an erratic reading, this could be the issue. Be sure to check with your engine builder first, but typically, the issue can be remedied by removing the affected sensors and putting the entire probe assembly in an oven for 24 to 48 hours at 275 degrees Fahrenheit to dry the sensor and return to like-new readings.
Tuning Tips
Tuning with exhaust temperatures is like climbing a mountain: The temperature will climb until you reach the peak, then will start to drop, like going down the other side of a mountain. When the engine starts to detonate, exhaust gas temperature will drop, while water or cylinder head temperatures will climb. So pay close attention to your data! The goal should be to tune just below peak temperatures, and to balance all cylinders within 50 degrees Fahrenheit of each other, from idle to wide open throttle. Trust us, your engine will thank you!
Rick Lawler has been the sales manager for Exhaust Gas Technologies (EGT) since 2006. Based in Chino, California, EGT specializes in high-performance thermocouples for motorsports and industrial applications. The company is world-renowned for developing the “Super X” EGT Sensor, which EGT calls the fastest and toughest sensor on the planet. In addition, Lawler is an avid drag racer and currently campaigns a 1964 Dodge Polara in Nostalgia Super Stock.