PRI Tech: Fuel Injector Selection
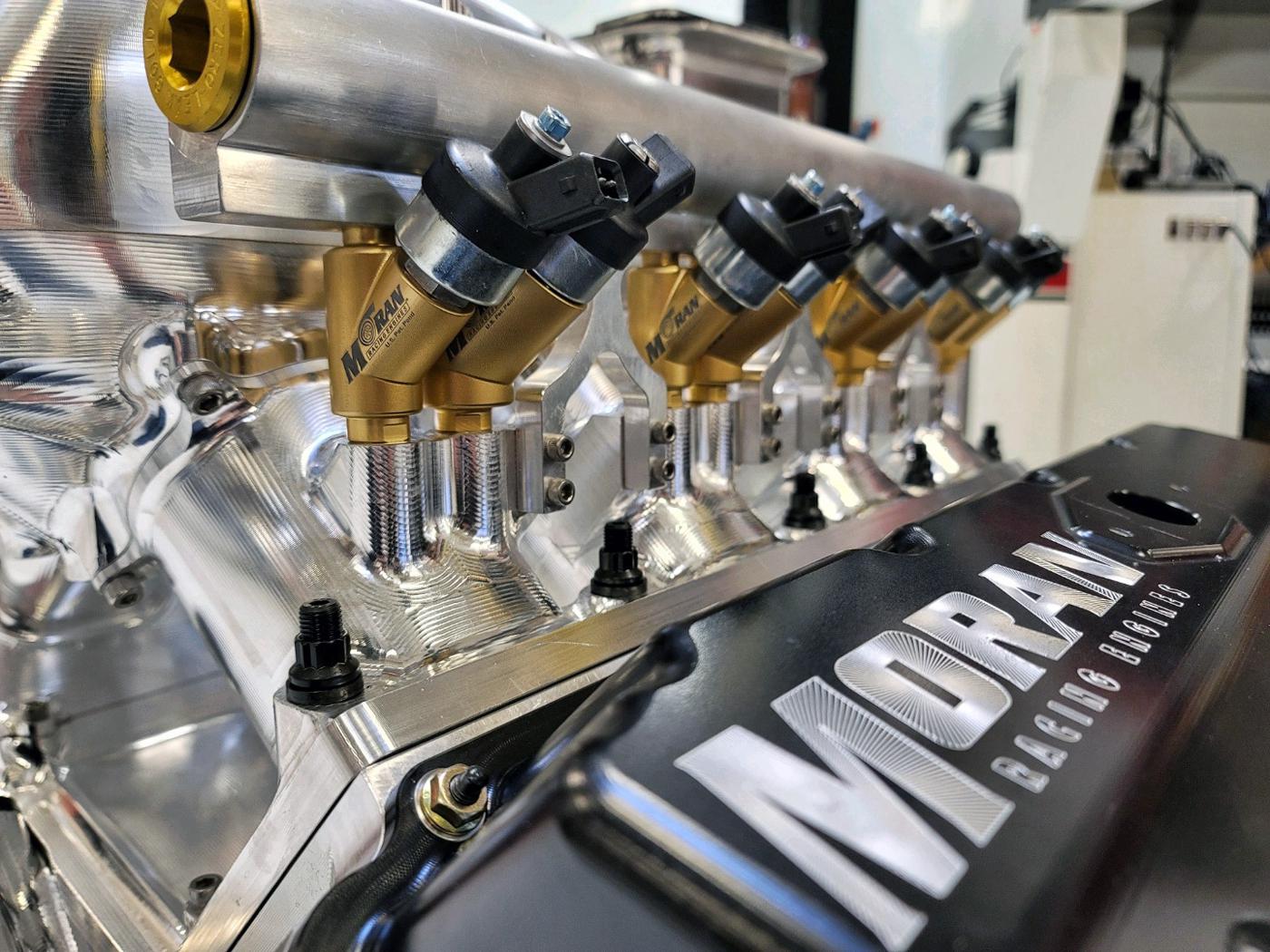
For high-horsepower engines, typically 2,500 hp and up, two fuel injectors should be used per cylinder, said Anthony Donnarumma. The primary injector operates at all times when the engine is running; the secondary turns on when the vehicle’s ECU detects that the primary injector has hit a duty-cycle threshold.
Fuel choice, power adder usage, and sizing are just some of the factors to be considered when determining the optimal fuel injectors for a race engine build.
The fuel injector in an electronic fuel injection (EFI) system plays a critical role in the performance and reliability of a modern internal combustion engine. It is the injector that allows EFI systems to attain fuel flow accuracy and efficiency that was previously not accessible with carbureted systems.
The simplest and longest-standing version—the “needle and seat” or EV1-style fuel injector—remains the injector of choice throughout much of the performance drag-racing aftermarket. This is due largely to both its reliability and design simplicity.
There have been many evolutions of this original Bosch-designed EV1, such as slimmer EV14 or EV6 injectors with disc-style actuation. But because of its ease of construction and reliability, the EV1 remains the preferred option for drag racing engine builders.
How Injectors Function in an Electronic Fueling System
At its core, a fuel injector is a simple solenoid valve that is used to meter the amount of fuel that the engine demands at a given moment in time. This valve can be broken down into a few main components for an EV1-style injector:
• An electromagnetic coil
• An armature
• A needle
• A seat
• A housing to hold all these components together
The fuel injector actuates when an electrical signal is given from the vehicle’s ECU. This electrical signal, or current, is passed through the injector’s coil windings. This induces an electromagnetic field that in turn moves the armature. The end of this armature contains the needle that is raised off the seat, thereby allowing fuel to pass by into the intake port.
Knowing the basics of how injectors function, we can begin to understand how to select the right injector for your racing application. Amongst the many factors to consider:
Fuel Choice. The goal of a fuel injector is to maintain an optimal Air to Fuel Ratio (AFR). It is important to know what that specific ratio is for your select fuel. For example, gasoline has a stoichiometric AFR of 14.7: 1, while methanol is 6.5: 1. Thus, the size of the fuel injector that is required for methanol will be much larger than one that’s required for gasoline.
The type of fuel used determines the volume of fuel needed inside the cylinder. The volume of fuel needed in the cylinder, which is relative to the engine’s displacement, is what dictates the size of the fuel injector. Without knowing what fuel you’ll use and its AFR, you can’t properly size your injectors.
Power Adders. What about your selected induction method? For example, most engines across all displacement levels—naturally aspirated or forced induction—will use very little fuel at idle. In these instances, larger injectors are not required to keep an optimal AFR range.
However, when any of those same engines are at peak torque, they will consume much more fuel. When you add, say, 50 psi of boost at that peak torque level, you are now changing the theoretical volume of that cylinder. As a result, larger fuel injectors must be used to maintain the optimal AFR needed.
For performance applications, the primary consideration is the fuel flow needed at peak torque, where fuel demand and engine stress is highest. That demanding torque range is the basis you use to determine the requirements of your injector size.
Sizing Considerations. We’ve already noted that the goal of a properly functioning injector system is to maintain optimal AFR. If we know that adding more air requires more fuel, why not always buy the biggest and best flowing injectors? If it were only that simple....
If you decide to run an oversized injector relative to the engine’s fuel requirements, the first thing you sacrifice will be idle quality. This is because injectors have an optimal operation range. An injector that flows enough fuel to support 5,000 horsepower won’t also be able to happily idle at 800 rpm.
This is because injectors function by allowing fuel to flow into the cylinder in specific and controlled intervals. Each of these intervals is determined by a precise electromagnetic pulse. How often these pulses occur is known as the duty cycle. If an injector is at 100% duty cycle, the needle that allows the pass-through of fuel flow never closes. At that point, your injector is no more controlled than a valve on a garden hose.
You never want to max out your injector’s duty cycle either; instead, you want to keep them within their optimal dynamic ranges. This tends to be around 50% to 90% duty cycle depending on the application, so it’s important to be precise with your selection.
Multiple (Staged) Injectors Systems. Consider that the flow rate of the injector is determined by two factors: the diameter of the opening orifice and the distance the needle lifts off the seat. When your injector is too large for your fuel requirements, the injector’s electromagnetic coil will not be energized long enough to control the correct amount of fuel needed to maintain a proper idle.
How do you solve this idle issue when you need a very large injector for your application? In the case of high-horsepower engines, typically 2,500 hp and up, a single fuel injector per cylinder will not suffice; rather, two fuel injectors will be used per cylinder as a primary and secondary injector.
The primary injector, typically the smaller of the two injectors, will operate the entire time the engine is running. The secondary injector turns on when the vehicle’s ECU detects that the primary injector has hit a duty cycle threshold. This threshold is determined by the tuner based on the engine’s application and size.
A smaller primary injector is used because of its better idle characteristics compared to a larger secondary fuel injector. This way, you can get the fuel you need at peak torque without sacrificing the precise fuel control needed to maintain good idle characteristics.
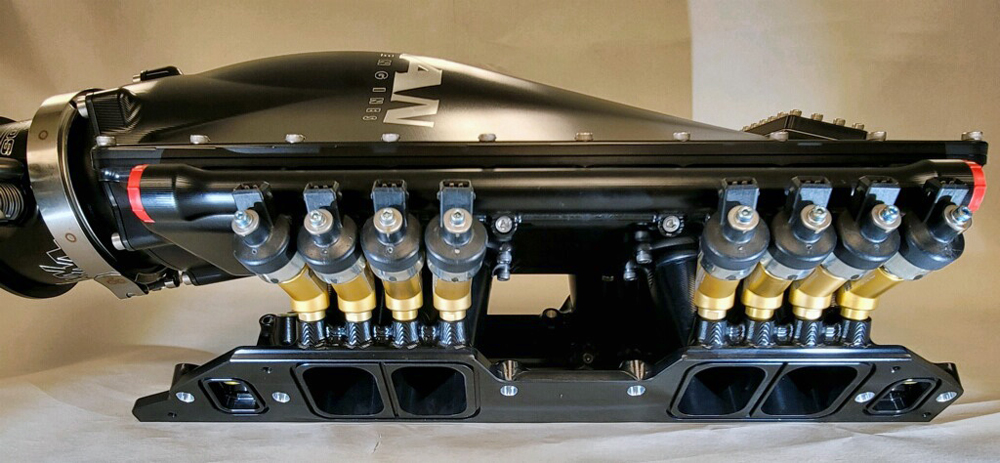
Incorrectly Sizing Injectors Has Consequences
When it comes to performance injectors, it’s always better to have more fuel flow than less. Remember, the goal of a proper injection system is to maintain optimal AFR. If your injector can’t provide the fuel the engine needs at peak torque, this can cause it to run lean when you need fuel the most.
An unbalanced AFR at peak stress levels can lead to a detonation event. That is something you want to avoid at all costs. For that reason, it’s generally safer to overbuild your fueling system than to do the opposite.
A good tuner will be able to work out the kinks for your setup and make good power while maintaining proper idle with a bigger injector than needed. However, if the injector is too small and peak torque fuel flow isn’t cutting it, they may choose not to tune the engine altogether, knowing the possibility of a critical failure in the system.
Don’t make your tuner’s life harder than it needs to be. If you don’t know what’s best for your setup, ask questions.
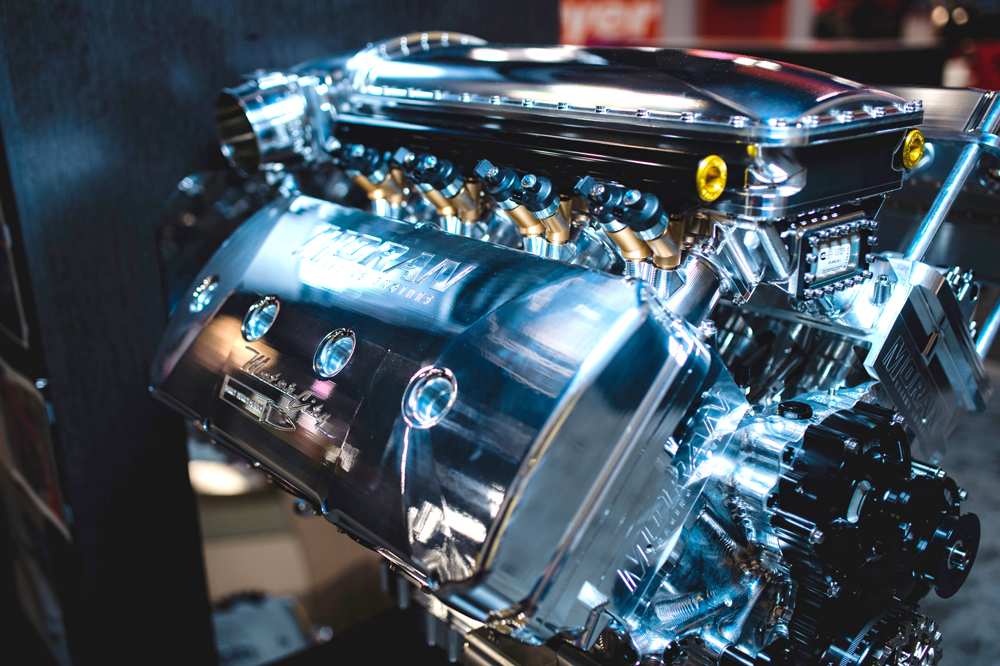
System Optimization
Now that you have considered the key factors that go into choosing the right fuel injector for your application, it is just as important to pick the rest of your fuel system components with the same level of research.
Many injector manufacturers will give their customers recommendations on what fuel pump flow and system filtration will be required to match an injector setup. If you are unsure of what size and system is right for your engine build, consult your injector supplier. Every drop of fuel counts! P
Anthony Donnarumma has eight years of professional experience in the automotive racing industry. He currently works as a Design Engineer and Engine Builder for Moran Motorsports. Prior to this position, he worked for Fiat Chrysler Automobiles in the SRT Motorsports group as an engineer to help develop the 2021 Dodge Challenger Drag Pak. He has a BS in Engineering Design from Western Michigan University.