STOP DOING THAT…DO THIS INSTEAD: Race Car Wiring
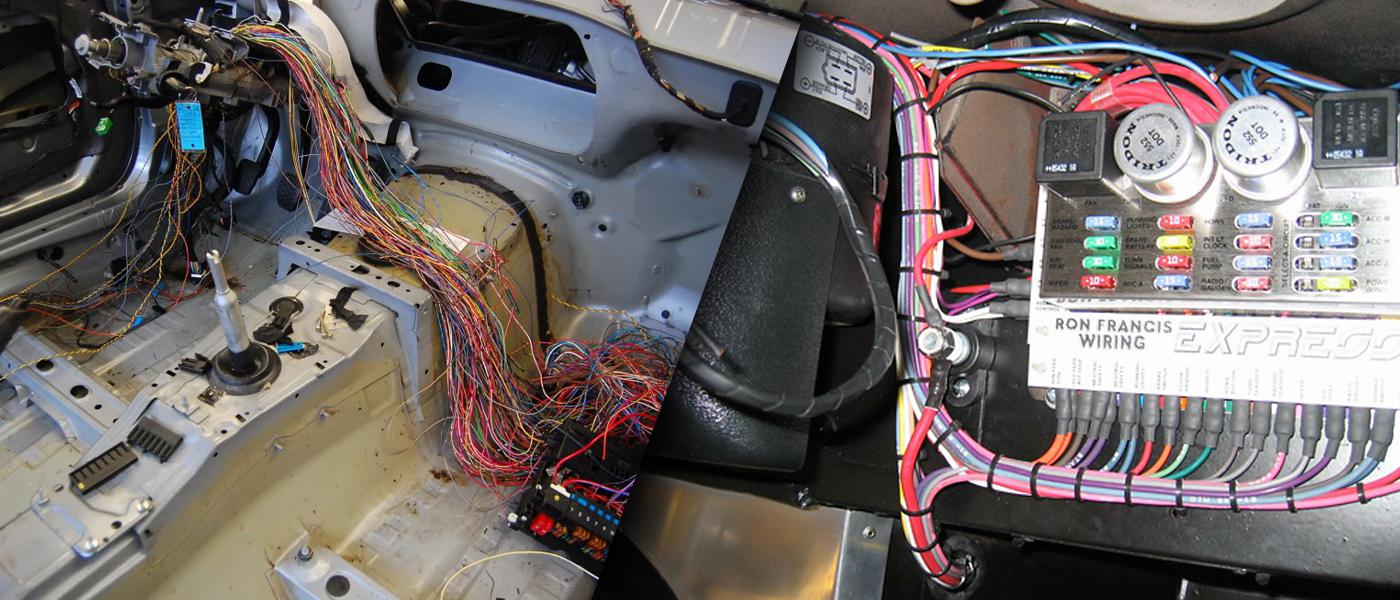
To avoid the bird’s nest, plan ahead when building or rewiring the race car, advised our source from Ron Francis Wiring, who added that going a bit bigger than necessary to start “will allow additions in the future, like nitrous, fuel pumps, and additional fans.”
Several misconceptions have infiltrated the performance spectrum, so we called on a pair of industry veterans to separate the fact from fiction.
Chasing down electrical issues can be among the most frustrating tasks on any car. The racing environment just makes things worse, as heat and vibration seem bent on attacking vulnerable components and less-than-secure connections. Plus, the hurry-up nature of in-the-pits repairs only compounds the situation.
To find out more about what racers are doing wrong with their wiring systems and what they should be doing instead, we spoke with two experts in the field: Dennis Overholser at Painless Performance Products in Fort Worth, Texas, and Scott Bowers at Ron Francis Wiring in Chester, Pennsylvania.
Avoid The Bird’s Nest
At races, Bowers often sees an electrical problem he calls “bird-nesting,” the tangled result of last-minute wiring additions to fix an issue. “That is a big recipe for problems,” he said. “Let’s say you’re in the staging lanes or the pits, and you have a problem that needs a solution in a hurry, and in the process a red wire turns into a blue wire through a butt splice. That kind of fix just complicates the solution, especially if there are multiple hands in the project trying to get you going again. If a fellow racer is helping, they have no idea the red wire turns into the blue wire.”
The solution is “sanitary, common-sense wiring and being smart with the wire paths and flows of circuits,” Bowers continued. “That really helps troubleshooting. Even 10 years after the build you know what you’ve got.”
Another way to avoid the bird-nesting trap is to plan ahead when building or rewiring the car, Bowers reported. “Go with a system that has plenty of room for growth in terms of capacity and fused circuits,” he explained. “The complexity will increase if there aren’t enough circuits and they have to add a piggyback or auxiliary fuse block to gain more fused circuits. Typically, it’s fairly cheap to go a bit bigger than necessary. That will allow additions in the future, like nitrous, fuel pumps, and additional fans.”
Secure Your Connections
The vibration inherent in a race car can wreak havoc on wire connections. For Overholser, the solution is to crimp, not solder, connections.
“Normally when you do a solder joint you crystalize the copper,” he explained. “The vibration will shake it enough to break it. Then you can have a real bad situation because you often can’t tell where the break is.”
Heat affects solder, too, he said. “We make our own battery cables, and we never solder them, especially the end of the cable that goes next to the starter. The headers will get the wire so hot it’ll melt the solder out of it. Then the wire will fall out, and short out. Hopefully, it won’t burn the car down.”
The “best way is to crimp the wires with a non-insulated terminal, whether it’s a splice or ring, then use heat shrink to give it some support,” Overholser added.
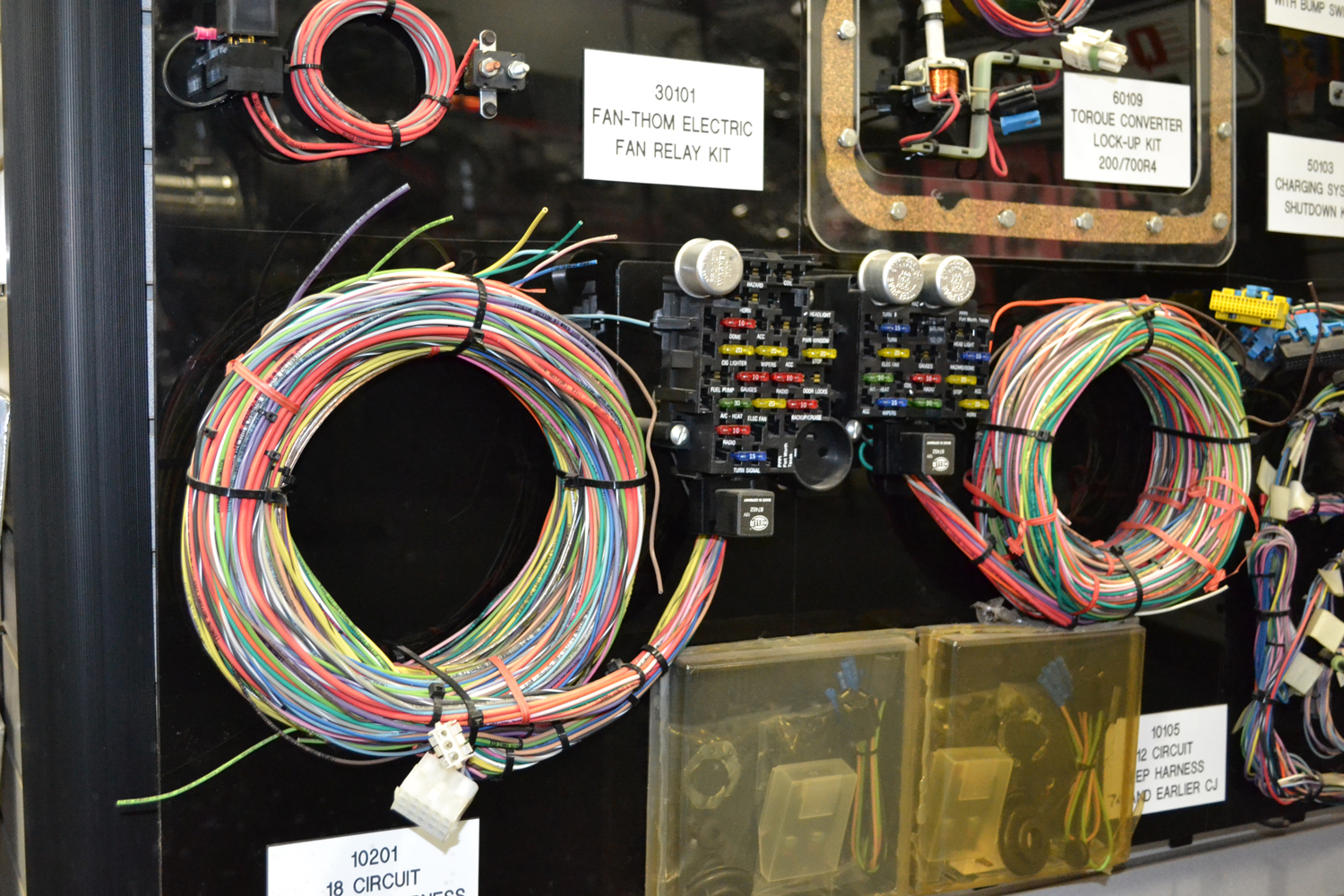
To Bowers, soldering is fine “unless vibration is of a concern. Then a connector system would be a better solution. The trick with soldering is that it must be done right. It’s one of those areas where more is not better. It does create a rigid area in the wire, but as long as you don’t go overboard with the amount of solder you wick into that joint, in my opinion it’s far superior to a butt splice.”
Another way to fight the effects of vibration is to “make sure there’s some type of support to keep everything rigid so it won’t move around,” Overholser said. Plastic zip ties, Adel clamps, “or any kind of clamp, you can’t use too many of them.” Tying the wires to a drag car’s tube chassis, for example, “helps eliminate the wire from vibrating. It will vibrate with the chassis, but it won’t flop.”
Rely On Relays
“I am a firm believer in fan relays,” Overholser said. “A hot wire run from the fuse block to the toggle switch and then out to the fan will never be efficient. The only thing that will do is overload the switch or the wire, and something’s going to melt. If they’re using a toggle switch not capable of carrying the amperage required, the fan won’t run at maximum speed, and it won’t cool the engine.”
“The switches on the market may or may not be able to handle the load that the controlled item is drawing,” said Bowers. “Relays allow the load to be carried through the relay, and the switch is simply controlling the relay. That is going to improve the life of the switch and create more trouble-free experiences when using those relays.”
Consider Alternator Capacity
“It’s always good to think ahead in terms of alternator capacity, especially if the car is running fans and fuel pumps,” Bowers said. “An alternator only puts out a portion of its rated amperage or current at idle. A 100-amp alternator may only be charging 20 to 30 amps at idle. Racers can get more capacity at idle by playing with the pulley sizes—smaller on the alternator or larger on the crank.”
Another consideration: An alternator “will only put out what it needs to charge to keep the voltage up to where it is expected to be,” Bowers said. Even a 100-amp alternator will be putting out “just the amperage it needs to keep up to the 14.5 or 14.7 volts to keep the system healthy.”
Here is one more alternator tip: Never demand more than 80% of an alternator’s rating for a continuous amount of time, Bowers said.
SOURCES
–
Painless Performance Products
painlessperformance.com
Ron Francis Wiring
ronfrancis.com