Ask the Experts: Chassis Dyno Maintenance
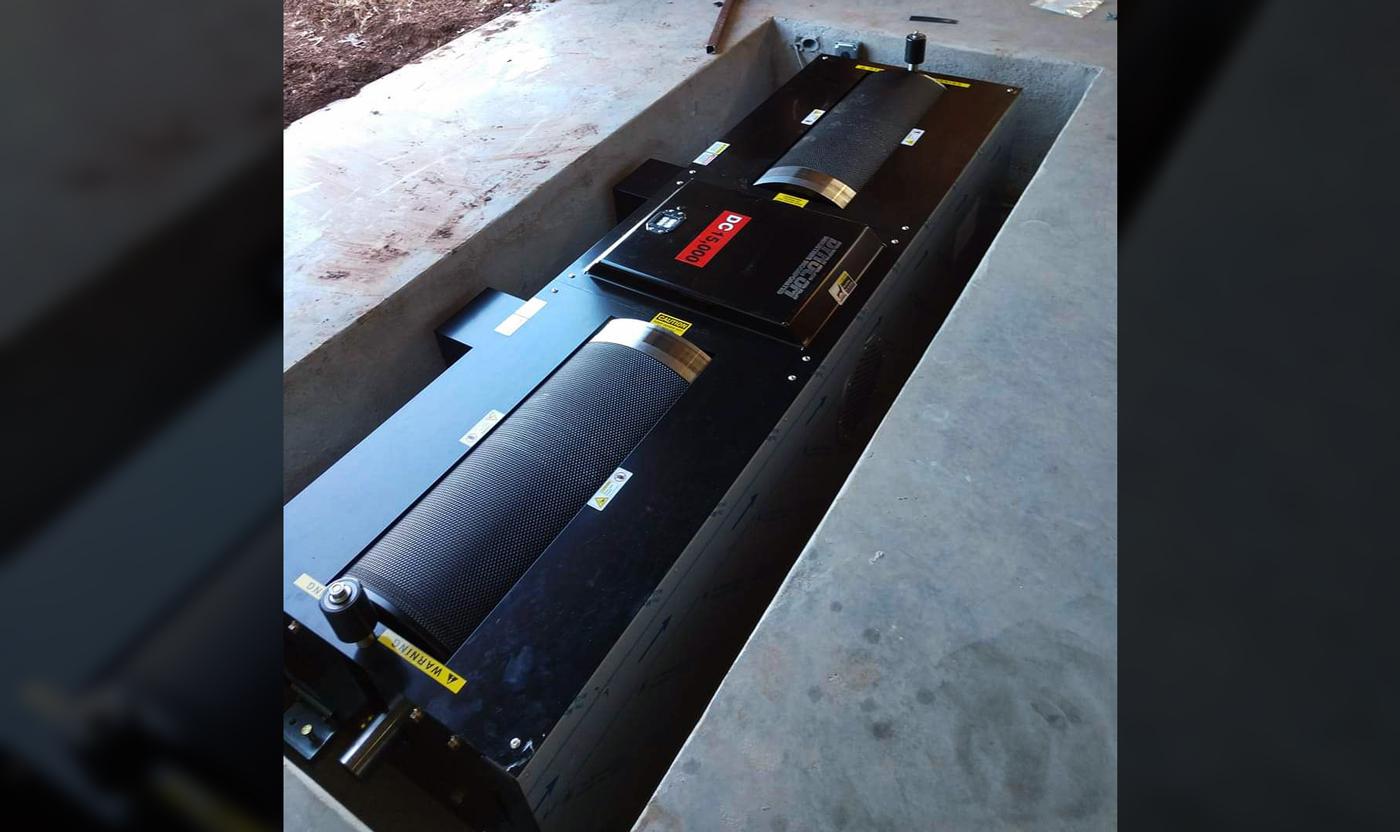
With a pit installation, it’s important to pull the plates off and clean down in the pit to get rid of paper or other debris. Dynocom’s Allison Blackstein had a customer who found rats in the pit chewed through the wires. “Rats love the insulation,” she said, “so you really have to stay on top of that.”
These tips can help prevent downtime as well as the potential need for costly repairs down the road.
Like any sophisticated mechanical device, chassis dynos require routine care to ensure consistent and accurate performance. But while some of this maintenance should be performed in scheduled intervals, Michael Caldwell of Mustang Dynamometers in Twinsburg, Ohio, said that maintaining some good habits on a day-to-day basis can help address some common problems before they develop.
“It’s important to have a very organized dyno room. You want to know where everything is because things can get into the dyno and cause problems, and if the room is disorganized, that might go unnoticed,” he explained. “If it’s in a pit, you want to make sure you pull the plates off and use a shop vac to get pieces of paper, tools, and other debris out of there. It’s really just a good idea to clean your dynamometer and dynamometer area on a regular basis.”
Allison Blackstein of Dynocom Industries in Fort Worth, Texas, also noted that cleaning the dynamometer and surrounding area on a regular basis is important for another reason that should definitely be on the radar of dyno operators with pit installations.
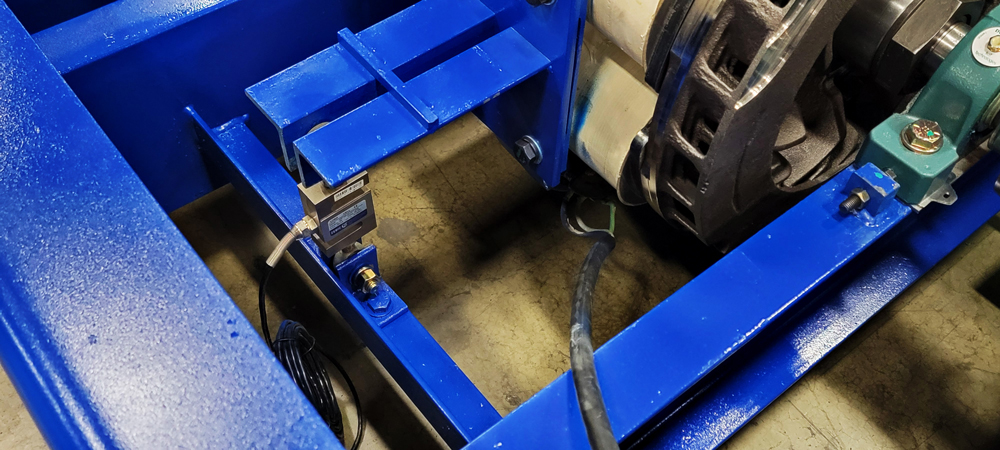
“We visited a customer of ours in Oklahoma recently who was having some unusual problems with his system,” she said. “We took the car off, took the pit cover off, and got down in the pit, and we discovered that rats had chewed through a bunch of the wires. Rats love the insulation on the wiring, so you really have to stay on top of that.”
Regular cleaning also provides opportunities to lubricate the bearings and eddy current brakes. “Make sure to use the lubricant that’s recommended by the dyno manufacturer and follow the recommended lubrication schedule,” Caldwell said. Owners should keep in mind that those schedules can vary widely depending on a dynamometer’s design.
“Our dynos, for example, use Dodge bearings, and these bearings aren’t really meant to be greased. They’re designed to essentially run 24 hours a day, seven days a week for 20 years in industrial applications,” said Blackstein. “They have Zerk fittings because people tend to get a bit anxious about not being able to grease the bearings if you sell them without those fittings. But there’s not necessarily a need for it with this type of bearing, and you can definitely over-fill a bearing. Over-filling can cause grease to come out of the seals, which can create issues rather than resolving them.”
Caldwell said that the electrical system that the chassis dyno is connected to can affect component longevity as well. “You should definitely be using a dedicated circuit. Most eddy current dynamometers have a separate circuit for the eddy current brake that runs off of a 240V single-phase circuit. You should have your electrician run a dedicated circuit for that, and you should switch that off at the breaker when you’re not using it. That’s going to minimize the chance for some kind of electrical damage from storms, which is the most common issue that we see.” He also recommends using surge protection for all of the dyno’s associated electronics, much like you would with sensitive electrical equipment at home.
Beyond the Dyno
Consistent performance also requires proper leveling, Blackstein said. “A lot of people say, ‘My concrete is perfectly flat,’ but there’s no such thing as perfectly flat concrete. You have to make sure that it’s not deflecting, so we provide shims with every chassis dyno, and they should be used wherever you can tap them in with a mallet.”
S-beam load cell calibration should also be done on a routine basis, Caldwell told us. Operators should also be aware that, due to the forces that they’re subjected to when used, these load cells typically need to be replaced every eight to 10 years in often-used dynamometers so that the dyno can continue to provide accurate results.
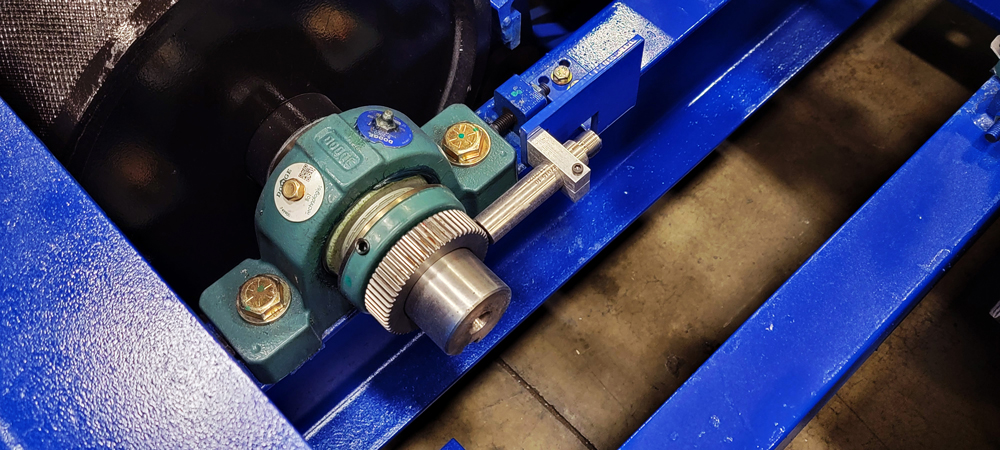
“There are folks out there who have been using the same load cell for decades,” he said. “Bad idea. It may still seem to work, but the chances of it operating to as-new specifications are zero. You’re putting tons of force on it over and over again, and that means it’s not going to stay linear because the shape of it actually gets warped over time. It may seem to be working because it calibrates, but it’s not linear anymore.”
Blackstein recommends having a spare speed sensor on hand at all times. “Even a little flake of dirt on the reluctor wheel will cause issues.”
Newer versions of these sensors are typically sealed, but dirt can find a way in anyway—especially on mobile chassis dynamometers. “This is the most important sensor on virtually any dyno,” she added. “If you don’t have the speed sensor, you don’t have anything. So it’s good to always have a backup available, just in case.”
Sources
Dynocom Industries
dynocom.net
Mustang Dynamometers
mustangdyne.com