Stop Doing That…Do This Instead: Using Incorrect Valve Spring Pressure
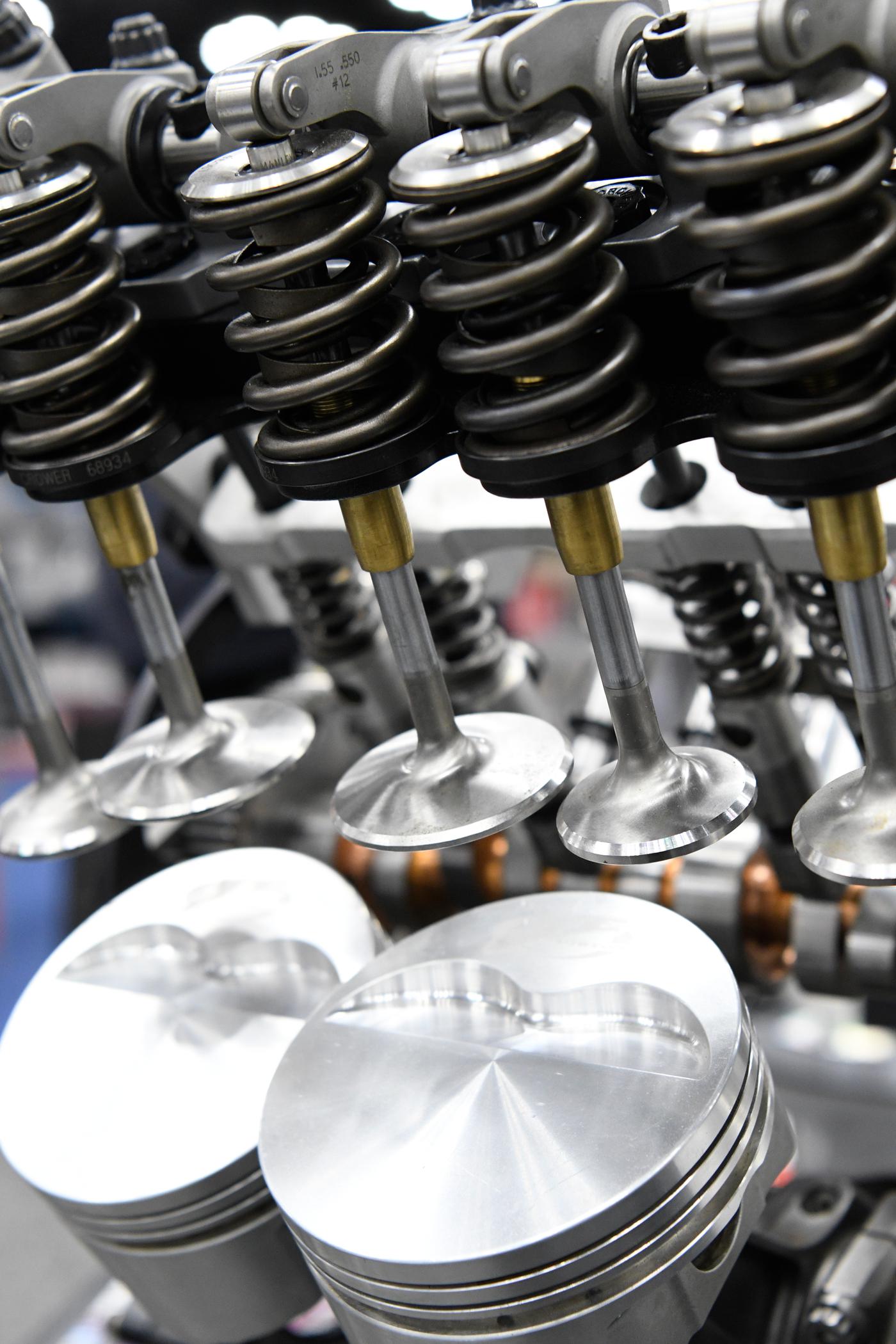
Proper valve spring pressure ensures that the valvetrain stays under control at the intended rpm ranges without causing undo stress to the system. Too much spring pressure can be harmful to parts, said a source, while too little pressure creates other kinds of problems.
Missing the mark in either direction can reduce horsepower and component longevity, so getting this element dialed in is well worth the effort.
Motorsports applications demand much from valve springs, and spring pressure plays a crucial role in the overall performance of the valvetrain because it provides the force needed to control valve motion. While the camshaft profile dictates when the valves open and how much, proper spring pressure ensures that the system stays under control at the intended rpm ranges without causing undo stress to the system.
“One of the oldest misconceptions in the valvetrain realm is that it’s fine to just use too much spring, and if you run into a problem, putting more spring on it will help. That’s just not the case,” said Joe Hornick of Joe Hornick Enterprises, Mooresville, North Carolina. “Stress is something that we do not want, and as you increase spring pressure, you increase stress. You’re trying to open the valvetrain against this big spring, so you’re winding up all the parts. You’re making the pushrod bend more, and you’re making the rocker arm bend more. When those parts are bent like that, the valve is going to hit the seat too fast when it comes back. So not only are you fighting the inefficiency of excess weight, because the spring and retainer are heavier than they need to be, you’re also potentially losing some performance due to the additional bending load on the parts.”
Inadequate spring pressure, meanwhile, can cause serious issues of its own. “Generally, you’ll lose limit speed,” Hornick explained. “If you need to run at 9,000 rpm, but you don’t have enough valve spring, maybe at 8,400 rpm things start going out of control. It has become harder to identify than it used to be because of improvements over the last decade or so in spring materials and how they’re processed. Today’s springs can handle a lot more instability. Regardless, that instability is causing horsepower loss at the very least.”
That means an accurate assessment of valve spring pressures is necessary to extract all of the potential out of a given engine combination. “There are a number of good gauges out there, both manual and automated, that will allow you to check valve spring loads versus spring height,” noted Chris Potter of Edelbrock Group, Olive Branch, Mississippi. “The manual ones will have some sort of load measuring device and a dial indicator to measure the actual spring height. The automated ones from Performance Trends and Larson will take all the data for you. However, these only show static load. The best way to measure load is with a load cell under the valve spring on something like a Spintron, or another type of motoring dyno. A load cell allows you to measure the running load between the bottom coil and the cylinder head.”
Potter also told us that because both static load requirement and frequency play important roles in valve spring performance, teams need to work with both the camshaft company and the valve spring supplier in order to properly match both components for a given application.
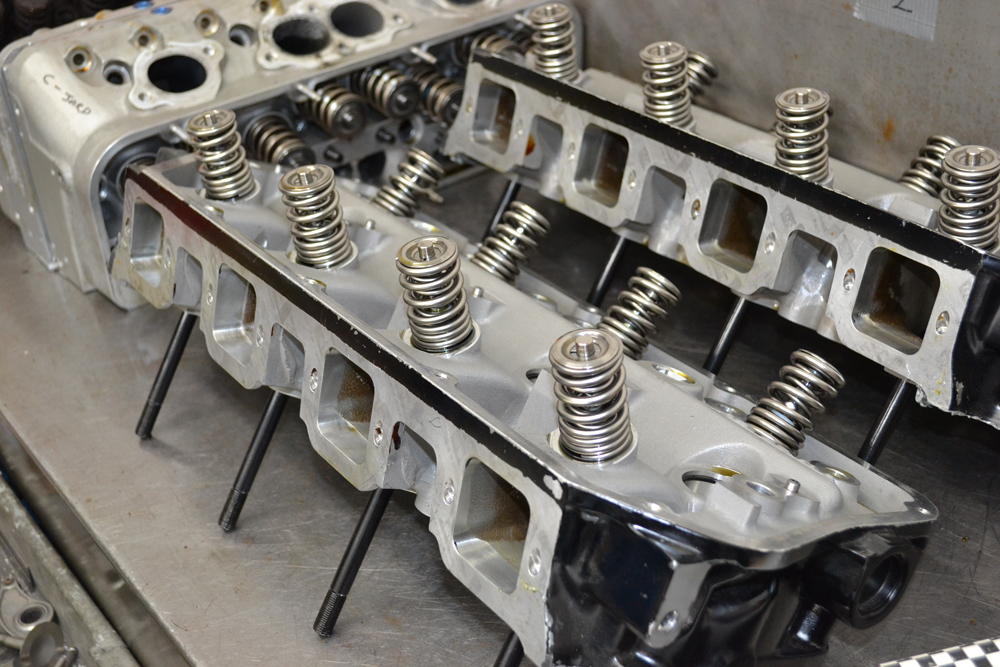
“In this situation frequency, mass, and load are all working together,” Potter explained. “The camshaft profile is going to input specific frequencies that the spring must be able to withstand, then that profile is going to ‘write a check’ for a certain dynamic load that’s required from the spring to keep everything under control. The pushrod and rocker stiffness are going to alter that check through deflection and stored energy from those components. So a good valvetrain must be built as a system.”
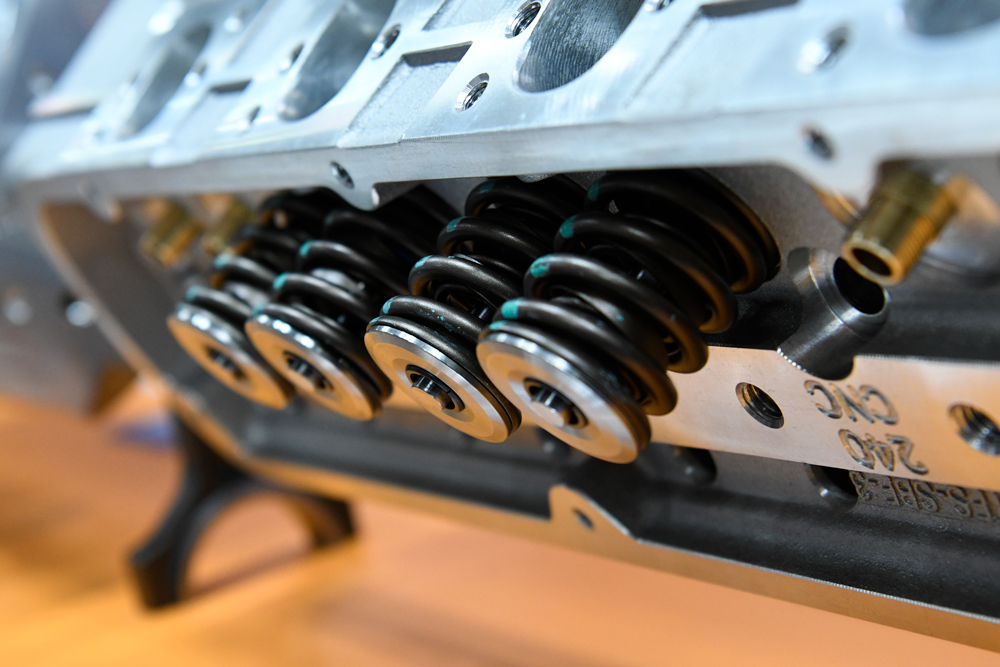
As Hornick pointed out, the considerations often extend beyond horsepower targets and rpm ranges. “You’re not going to use the same type of spring for endurance racing and drag racing, for example. The static numbers that are generated by our design software will tell us we have this much stress at wide open, this much stress at the seat, and this much of a variation in stress as it’s opening and closing. When you’re looking at a spring that’s going to be used for drag racing, and we compare it to the number that we believe the wire can take, we’re going to use maybe 90% of that stress number and the spring is not going to break.”
While that can provide enough headroom for a situation where the engine is on boil for a few seconds at a time, Hornick said that racing formats that subject the engine to extended periods of time at or near wide open throttle generally require a more conservative approach in order to ensure durability. “That means that the number we would use in an endurance application would be a lot lower relative to what the max stress would be.”
SOURCES
Edelbrock Group
edelbrockgroup.com
Joe Hornick Enterprises
jheinc.com