Ask the Experts: Head Gaskets
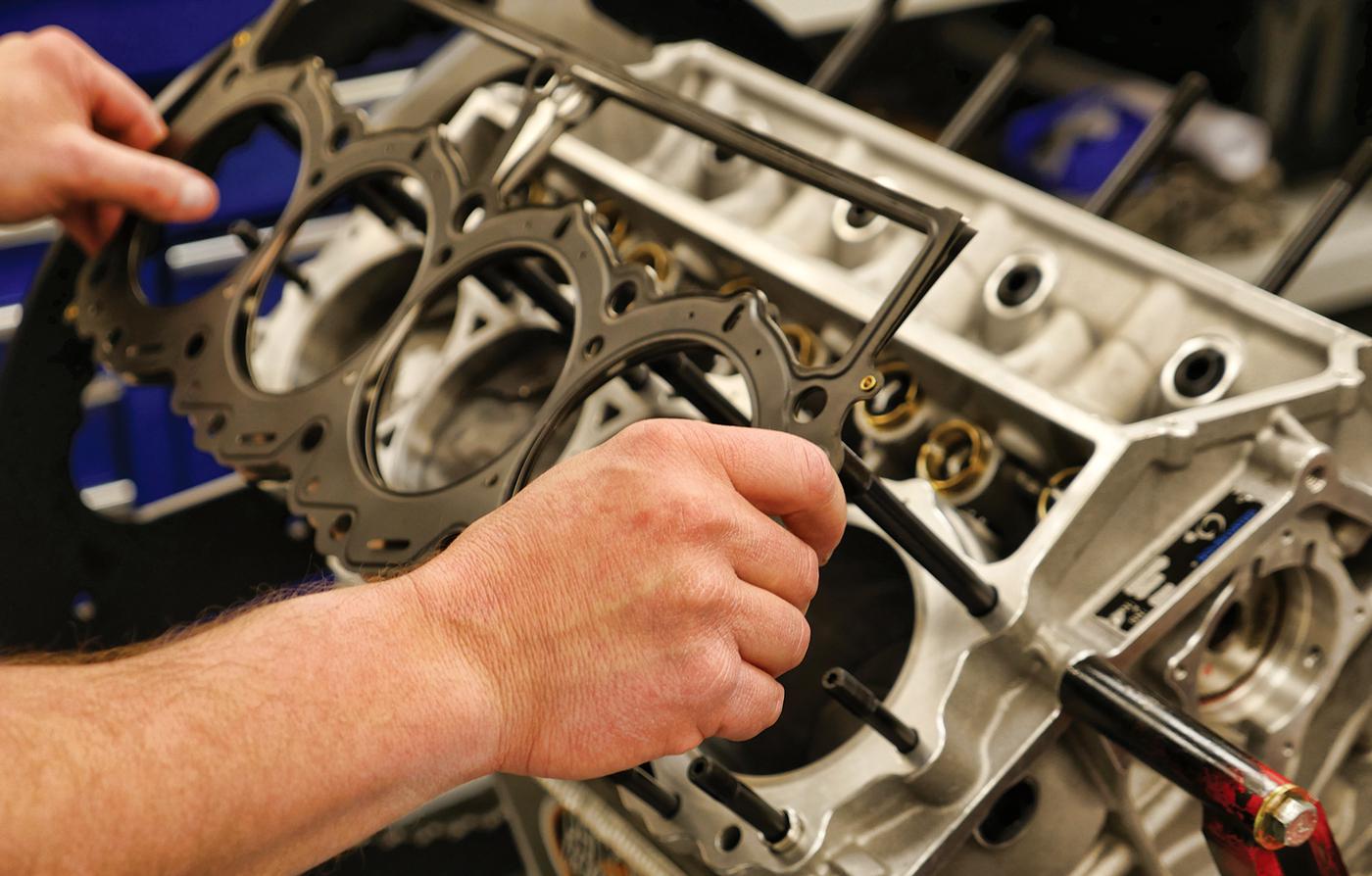
Leading gasket manufacturers remind us that leak prevention really begins at the engine assembly stage: “The first thing to do is make sure the surface finish on the block and head is correct,” said a source from Cometic Gasket. “It has to be clean, dry, and flat.”
Steer clear of power loss or, worse still, engine damage by following manufacturers’ best practices for preventing leaks and failures.
Head gaskets have to work harder than ever in these days of high-powered (and forced-induction) race engines to seal increasing amounts of cylinder pressure and also serve as a barrier to keep coolant and oil within their respective passages. Should a gasket fail, the results could vary from power loss to engine damage if the situation isn’t remedied. Even better: Prevent a leak or failure from happening in the first place.
“Once you start pushing an engine’s limits, like adding forced induction, you have to go the extra steps when building the engine to prevent leaks in the race environment,” said Sergio Duarte of Flatout Gaskets, Mundelein, Illinois.
Micky Hale of Cometic Gasket in Concord, Ohio, agreed that leak prevention begins at engine assembly. “The first thing to do is make sure the surface finish on the block and head is correct. It has to be clean, dry, and flat.”
“The roughness of the surface has to match the gasket that’s going to be used,” Duarte said. Copper gaskets can seal against a surface with an Ra (roughness average) from 40 to 80, “while an MLS (multi-layered steel) gasket has to have a roughness that’s very, very low.”
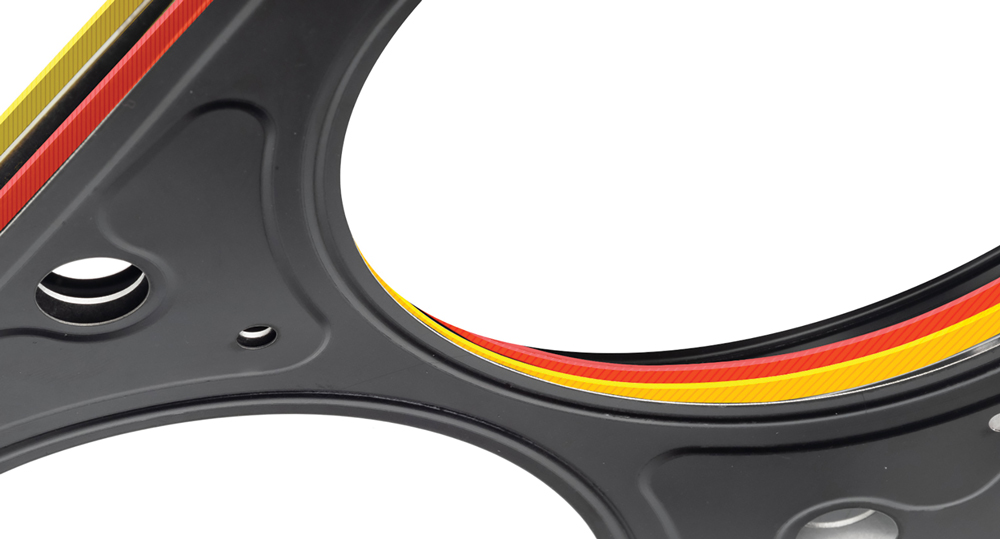
Hale put the Ra target for MLS gaskets at “50 or better. That’s a smooth finish, with no mill marks or pattern in it. If a pattern that looks like a fingerprint is visible—those are lines from the cut—that’s too coarse. That gasket will tend to seep. It doesn’t necessarily have to be a mirror finish, but it has to have a smooth finish.”
Hale said “any modern machinist should be equipped for that. Over the last 10–15 years, everyone’s upped their game there. They know what to do to use MLS gaskets.”
Special machining is also needed for an engine using copper gaskets, Duarte said, “to O-ring the heads and install fire rings properly to prevent a leak.”
Is copper a better choice for a race engine? “It depends on how the engine is prepared,” Duarte said. “A lot of people are making 2,000–3,000 horsepower with MLS gaskets, and they’re perfectly okay. Most of the MLS gaskets are made with an O-ring around the combustion chambers, so they seal very well even in some race applications. The embossing in the MLS has memory, so when the head is moving up and down with heat cycles, the MLS gasket springs back and keeps the engine sealed.”
But, he added, “for an engine that’s going to push more and more, in an all-out racing application, copper gaskets with the right fire rings are the way to go.”
Whether the choice is MLS or copper, both Duarte and Hale said that proper head fastening is important to prevent gasket leaks.
“Torque specs are critical for the gasket to work,” Duarte said. “Always keep the load on the gasket steady.”
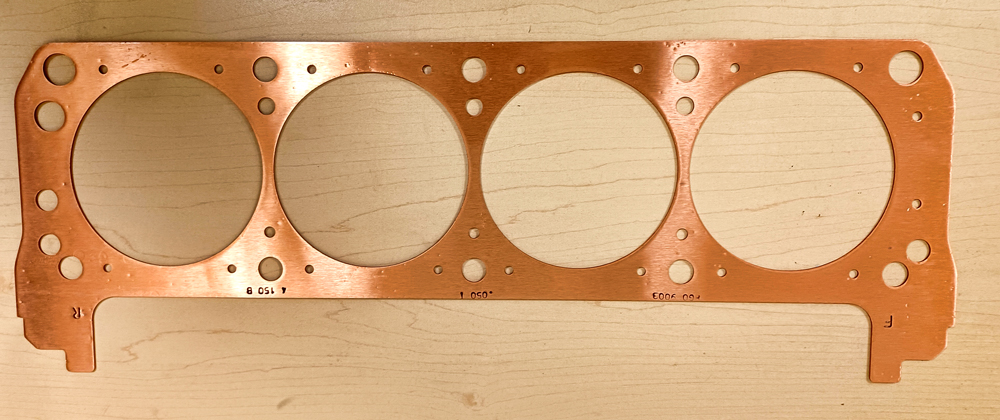
“Use a good torque wrench, something that’s been calibrated recently and is accurate,” Hale added. Good fasteners are also “a must. Having a quality fastener will improve the clamp load needed to compress the gasket.”
Because of the stainless-steel material Cometic uses in its MLS gaskets, “it takes a bit to compress it,” Hale said. “If they are seeping or leaking, typically they’re not compressed fully. If somebody calls me and has a leaky gasket, I tell them to try a retorque. If the block and heads have a good finish to start with, that will typically take it away.”
As for adding sealant to the gaskets, Hale said “no sealers whatsoever” should be put on the Cometic MLS gaskets. “Our material already has a coating on it, so any additional sealers or coating typically work against it.”
Duarte said the silicone coating applied to Flatout’s copper gaskets “has been tested by hundreds of people in different forms of racing, from dirt track, Pro Mods, you name it. It’s a very good silicone coating.” Some builders, he said, also use RTV sealant around the gasket’s coolant ports. “It’s a matter of choice. Every engine builder has their own preference as to what to use for sealing.”
Keeping head gaskets leak-free is “pretty straightforward,” said Hale. “It’s not rocket science, but it is a science to make everything work together perfectly.”
Sources
Cometic Gasket
cometic.com
Flatout Gaskets
flatoutgroup.com