Stop Doing That…Do This Instead: Wasting Excess Metal
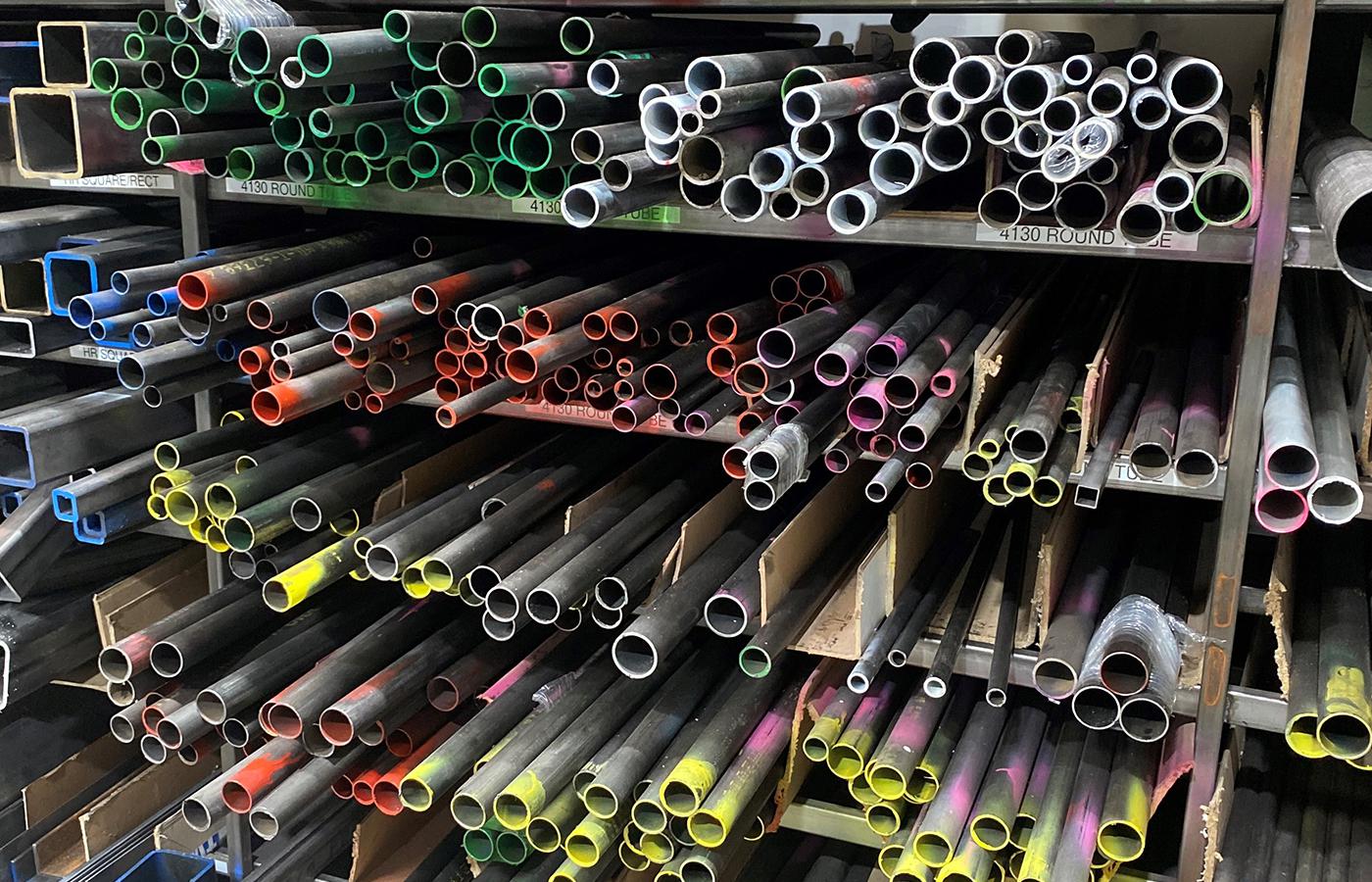
Extra material left over from custom cuts, a return, or some other reason goes into drop bins and racks at Stock Car Steel and Aluminum. “That allows walk-in customers to check out what’s available when they’re at the shop,” said Sasha Dierker, who noted these materials are usually sold at a discount.
As efforts to improve sustainability proliferate throughout the automotive realm, the industry is developing solutions to help ensure that leftover material gets put to good use.
There’s an array of different processes that can produce metal waste during the journey from raw material to a finished motorsports product. Although most manufacturers are continually on the lookout for ways to improve their production efficiencies and reduce their impact on the environment, some excesses are inherent due to the nature of the industry and the specialized components that support it.
That doesn’t mean the extra material has to end up in a landfill, though. Here we’re taking a closer look at how manufacturers, metal suppliers, and brokers are helping to reduce this waste in ways that can actually bolster a business’s bottom line while benefiting the planet.
Cut to Order
Stock Car Steel and Aluminum (SCSA) in Mooresville, North Carolina, got its start back in 1996 providing metal for chassis builders in NASCAR and other series, but over the last two-and-a-half decades the company has expanded into plastics, aluminum, sheetmetal, and other materials for a range of different industries. One particularly popular service that the company offers is the ability to do custom cuts. If a customer needs a material of a particular length or some other dimension, SCSA can trim the material down to size for them.
“It’s something we’ve been doing here since the beginning, and because of that, we were able to find a use for the excess material very early on,” said Sasha Dierker. “Any extra material that we end up with because of a custom cut, a return, or some other reason ends up in our drop bins and racks, and that allows walk-in customers to check out what’s available when they’re at the shop. It’s generally materials like steel square tubing, chromoly, and welded DOM steel tubing that’s 5 feet or less in length with a 1-inch to 2-inch outside diameter. Sheet ranges from 11 gauge to 22 gauge.”
These ‘drop’ materials are typically discounted by 10–15%, depending on the type of material and size. If SCSA ever finds itself with an over-abundance of drops, the material is sent to the scrap yard for recycling.
“That hasn’t really been an issue lately,” Dierker said. “Sometimes people will buy entire bins of material. And if prices on materials keep rising, I think it’ll only become more popular over time. Cup teams can contend with the costs; the people who really benefit from this are the ones who don’t have huge budgets to work with.”
Recycling Resources
As one of the leading manufacturers of motorsports-grade crankshafts, connecting rods, and camshafts, Callies Performance Products in Fostoria, Ohio, machines and processes a vast amount of metal to produce its products. Rather than tossing out those metal shavings and chips—and in turn bearing the cost of disposal—the company has developed a storage and categorization system that makes recycling the materials a hassle-free proposition.
As Heath Norton explained, it’s part of a larger effort at Callies to operate the business in a way that’s sustainable and cognizant of potential environmental concerns. “We’re pro-racing and pro-environment,” he stated. “We recycle scrap parts, return parts, damaged parts, the chips and shavings that come off in manufacturing, cardboard waste—anywhere there’s an opportunity to do so. It’s something we’ve done since the beginning of the company, and I think anyone who wants to run their business responsibly should be making an effort. By now there’s a well-established path for this sort of thing.”
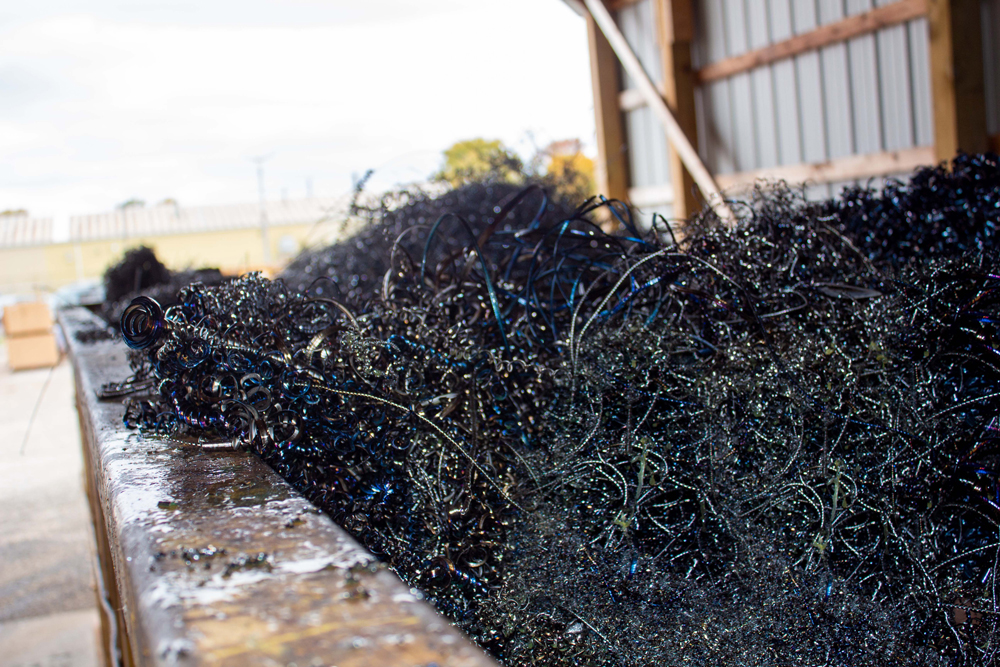
To help reduce metal waste, Callies Performance Products divides up chips and shavings by material type and stores them in an enclosed area outside the facility to prevent any potential groundwater contamination from rain. “Everything we do at Callies is ferrous-based, so we can recycle all of that material,” Norton noted. “Selling that material to recyclers allows us to turn something that would otherwise be an expense for us into something that brings money back in. Throwing stuff away is expensive, so anything we can do to avoid adding to landfills is going to be advantageous.”
Cash for Scrap
Scrap metal processor J. Solotken & Co. in Indianapolis, Indiana, buys excess materials from factories and demolition companies as well as machine shops and other motorsports-related businesses. As Bob Schneider explained, the company’s close proximity to Indianapolis Motor Speedway has given it a direct connection to auto racing and has provided greater awareness of the services it offers in turn.
“This is the ‘racing capital of the world,’ so of course a lot of race teams have facilities here,” said Schneider. “As these teams machine materials on a mill, lathe, or whatever else they might be using, they produce turnings from that process. They also have a lot of end pieces and material that’s had sections cut out from sheet, bar stock, plate stock, and so on. I think that because of concerns about things like global warming and other environmental factors, folks are becoming more aware of the need to keep this stuff out of the dump. At the same time, they’re also realizing that the material has value. Every now and then I’ll talk to someone who tells me, ‘Oh, we’re just throwing that stuff away.’ And I’m like, ‘Don’t do that—I’ll pay you for it!’”
As Schneider noted, trashing this material rather than selling it to a broker tends to move a business’s money in the wrong direction. “Trash services will charge you to dispose of it, so what we’re offering is income rather than an expense,” he added. “It’s good for the environment, and it’s also good for the overall perception of the business.”
J. Solotken & Co. also works directly with companies to advise them on how to collect and sort materials, along with ways to minimize material contamination when using different types of metals on the same piece of equipment. “Let’s say they’re working with a steel part and then they’re going to switch over to an aluminum part,” explained Schneider. “If they don’t clean the machine out properly, they’ll end up with steel in their aluminum turnings, and that can turn something with value into something with little or no value.”
He noted that virtually all metal material can be recycled, and that the recycling process has actually been an essential part of metal production for decades. “Generally speaking, about 40% of the material that goes into making new metal comes from scrap,” he added. “Depending on how the metal is going to be used, sometimes recycled material can be preferable to new raw material because of potential differences in things like hardness and resistance to heat. It really all comes down to the application.”
Sources
Callies Performance Products
callies.com
J. Solotken & Co.
jsolotken.com
Stock Car Steel and Aluminum
stockcarsteel.com